Mass Finishing Fundamentals
- by David A. Davidson
- Feb 8, 2018
- 3 min read
For more information and sample processing assistance contact:
Contributing Editor: Dave Davidson | Deburring/Finishing Technologist | Deburring/Finishing Technical Group
Mass Finishing Processes and Mechanical Surface Preparation
What is Mass Finishing?
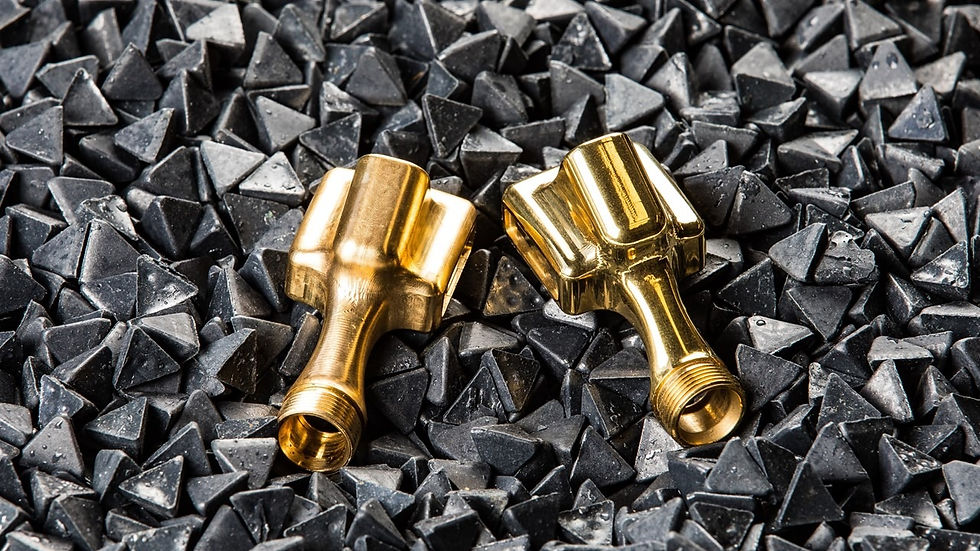
Mass finishing is a term used to describe a group of abrasive industrial processes by which large lots of parts or components made from metal or other materials can be economically processed in bulk to achieve one or several of a variety of surface effects. These include deburring, descaling, surface smoothing, edge-break, radius formation, removal of surface contaminants from heat treat and other processes, pre-plate and pre-paint or coating surface preparation, blending in surface irregularities from machining or fabricating operations, producing reflective surfaces with nonabrasive burnishing media, refining surfaces, and developing super-finish or micro-finish equivalent surface profiles.
All mass finishing processes utilize a loose or free abrasive material referred to as media within a container or chamber of some sort. Energy is imparted to the abrasive media mass by a variety of means to impart motion to it and to cause it to rub or wear away at part surfaces. Although by definition, the term mass finishing is used generally to describe processes in which parts move in a random manner throughout the abrasive media mass. Equipment and processes that utilize loose abrasive media to process parts that are fixtured come under this heading also.
Above are shown various parts and components have have been deburred, finished and/or polished with various mass finishing processes such as barrel finishing, vibratory finishing, centrifugal barrel and centrifugal disc finishing.
Why mass finishing? Nearly all manufactured parts or components require some measure of surface refinement prior to final assembly, or the final finish or coating required to make the parts acceptable to the consumer or end-user. Most manufacturing companies who employ mass finishing techniques do so because of the economic advantages to be obtained, especially when compared with manual deburring and surface finishing techniques. Mass finishing processes often reduce or eliminate many procedures that are labor intensive and require extensive part handling. This is especially important in meeting increasingly stringent quality control standards, as most mass finishing processes generate surface effects with part-to-part and lot-to-lot uniformity that cannot be replicated with processes in which parts are individually handled. It has become a manufacturing engineering axiom that part reject and rework rates will plummet if a mass finishing approach can be implemented to meet surface finish objectives.
Although each of the mass finishing process types carries with it a unique set of process strengths and weaknesses, all of them are sufficiently versatile to be able to process a wide variety of part types successfully. A plethora of abrasive media types, sizes, and shapes makes it possible, in many cases, to achieve very different results within the same equipment, ranging from heavy grinding and radiusing to final finishing. Components from almost every conceivable type of material have been surface conditioned using mass finishing techniques including ferrous and nonferrous metals, plastics, composition materials, ceramics, and even wood.
Above are shown various types of vibratory finishing and centrifugal finishing machines.
Above is shown operation of a vibratory bowl fishing machine deburring parts.
Above is shown operation of a multi-step centrifugal barrel finishing process to develop very fine finishes and polished surfaces on parts.
I am a deburring and surface finishing specialist, consultant and advisor to SME's [Society of Manufacturing Engineers] Technical Community Network. The focus of my activity is assisting manufacturers and machine shops with reducing their dependence on hand or manual deburring and finishing methods as well as helping them to upgrade the edge and surface finish quality of their parts. I currently work from Norwich, NY but I assist clients nation-wide. I can arrange for free sample processing and process development for your challenging deburring and finishing needs and can provide you with either contract finishing services or the in-house capability to produce improved hands-free finishes on precision parts. I can be contacted at my cell: 509.563.9859 or ddavidson@deburring-tech-group.com. Let me know if I can be helpful. http://dryfinish.wordpress.com https://partsfinished.wordpress.com https://dryfinish.wixsite.com/iso-finish

Comments