Some Case Study and Application Examples for Centrifugal Iso-Finishing Processes
- Dave Davidson
- Jul 6, 2022
- 4 min read
For additional information CONTACT: Dave Davidson | Deburring/Finishing Technologist
Mobile: (509)-563-9859 | ddavidson@deburring-tech-group.com | https://dryfinish.wixsite.com/iso-finish
Ask about the FREE sample part processing program Finishing Technology for Metals, Plastics, Ceramics and Composites
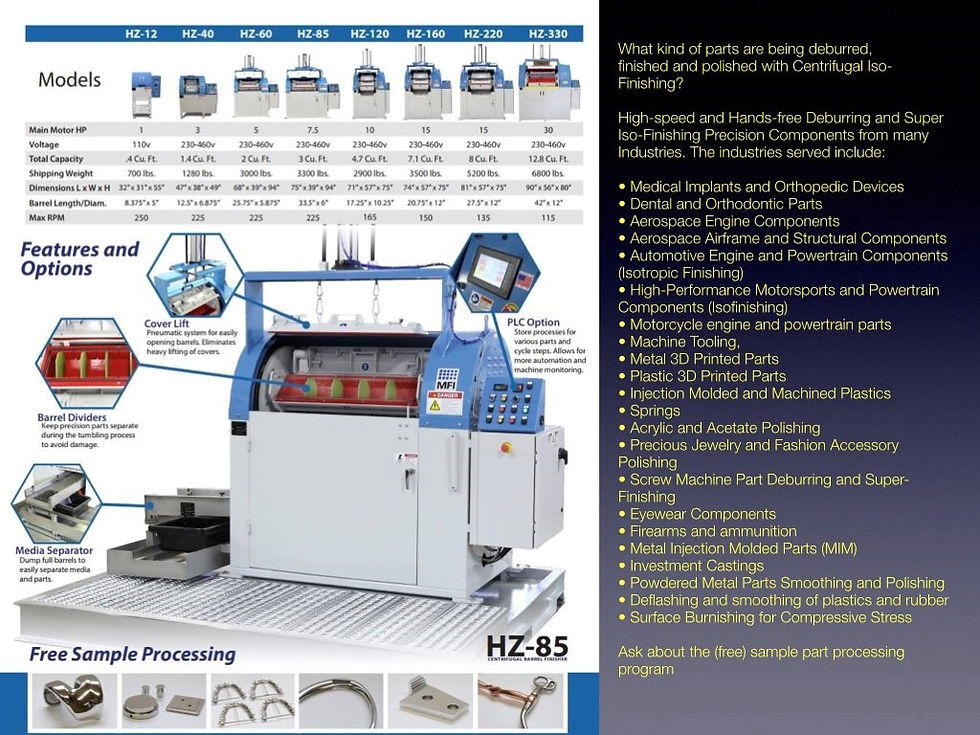

Large numbers of parts can be uniformly edge and surface finished in centrifugal mass finishing equipment. Process development in recent years has facilitated the creation of very refined surface and edge effects by processing parts in a series of successively finer processes in high-energy centrifugal equipment
Nearly all manufactured and fabricated components require some edge and surface finish preparation prior to final assembly. Although many parts today are still individually handled and processed with hand tools or hand-held power tools, it has become almost universally accepted that utilization of mass finishing techniques is far to be preferred on both their economic and technical merits, whenever possible. Utilizing energy developed from motion imparted to the containers or vessels in mass finishing equipment, loose abrasive or polishing media can produce a wide range of desirable edge and surface effects.
The information below discusses a variety of important applications for Centrifugal iso-Finishing. Contact me at ddavidson@deburring-tech-group.com for help in making arrangements for sample part finishing your parts.




SLIDE PRESENTATION, Centrifugal Iso-Finishing Equipment, Processes, Media and Before and After Part Finishing Examples




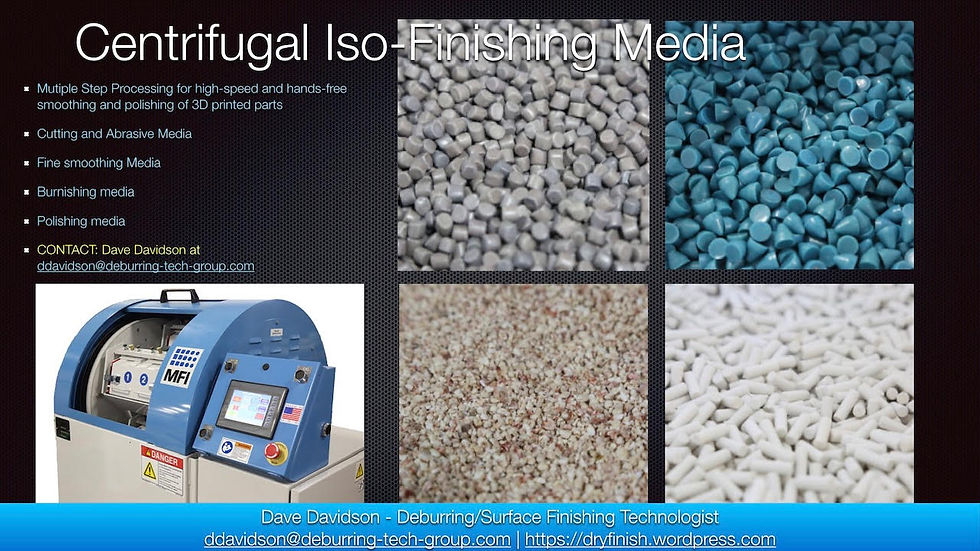
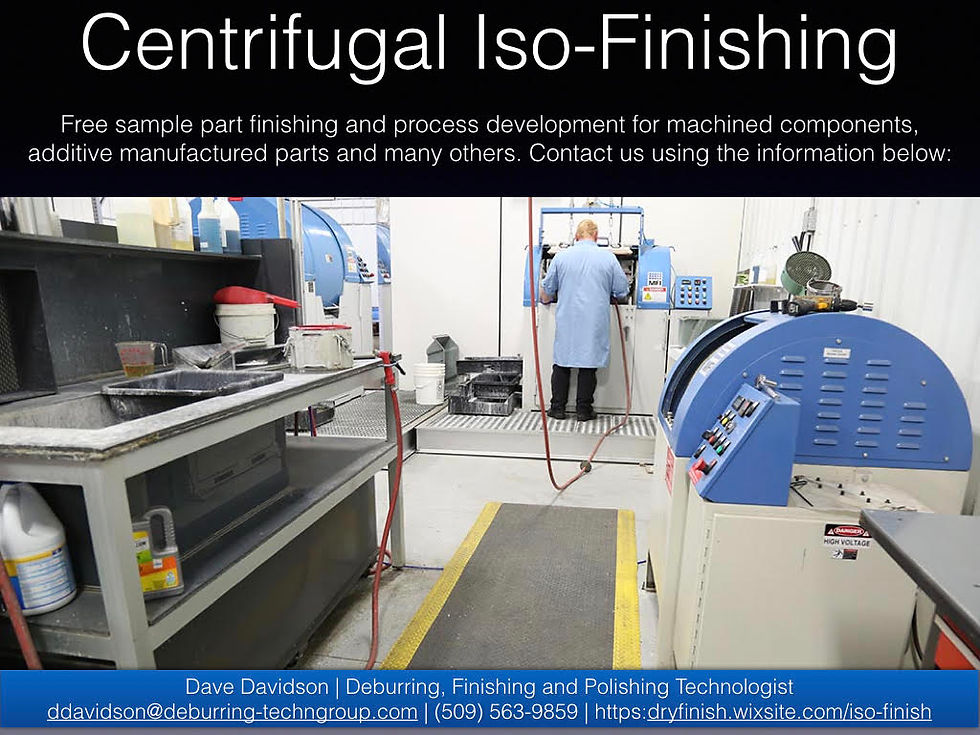





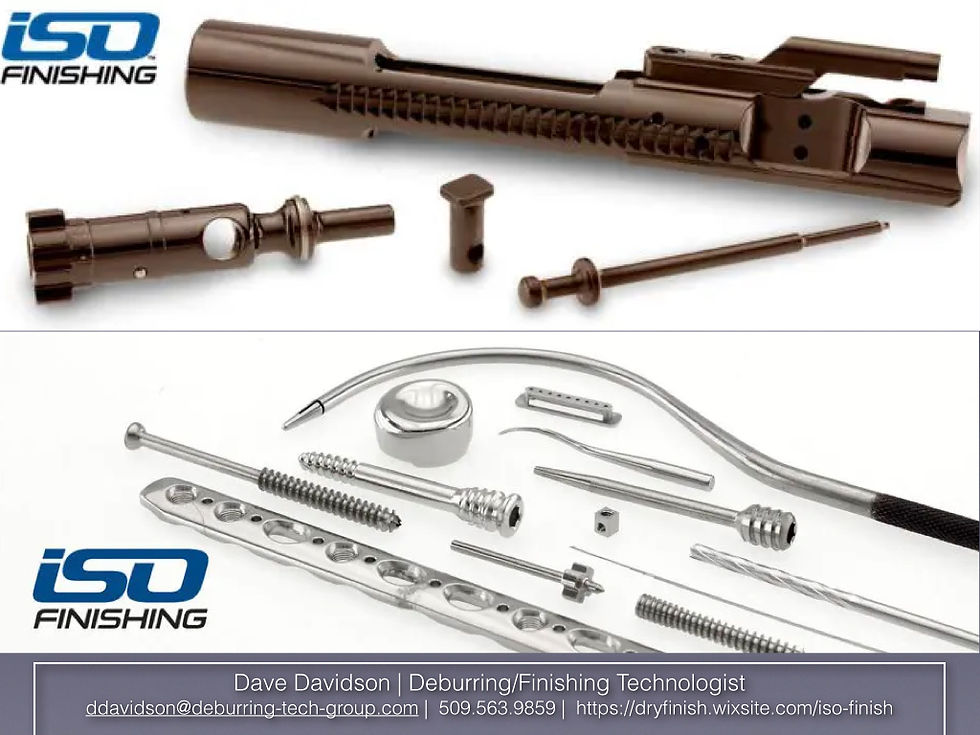

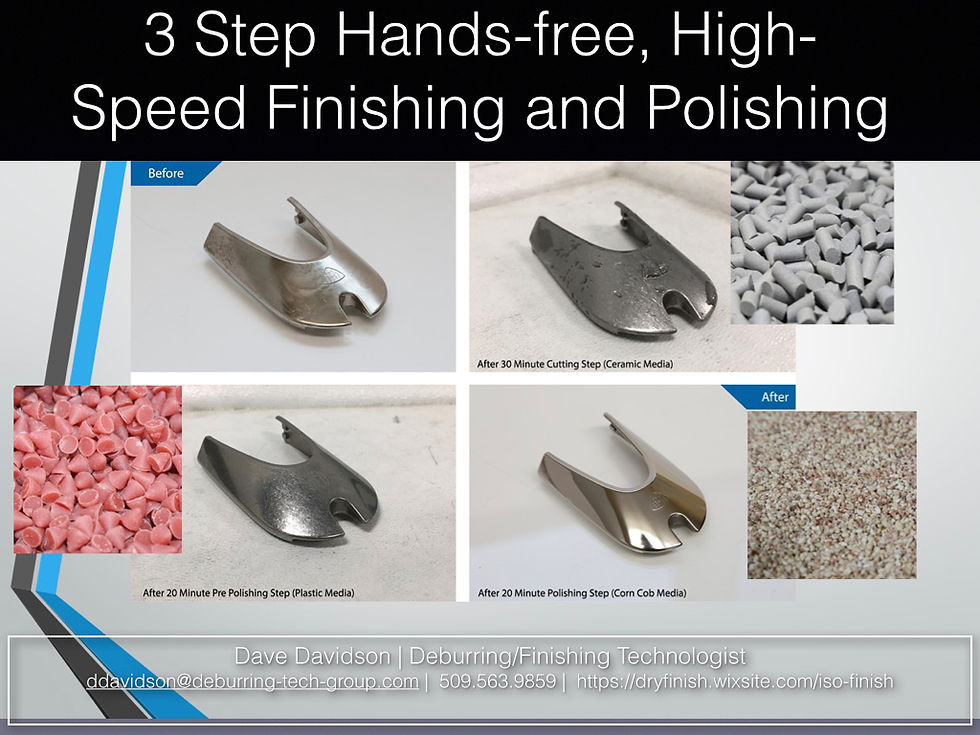

Centrifugal Iso-Finishing Machine and Application Videos.
See the comparative chart below which illustrates the various models of Centrifugal Finishing machines.that are among the machines shown in the videos below. Equipment overall dimensions as well as that of the hexagonal work chambers are also given below. Parts can be processed in bulk or processed in individual compartments. See the illustration of the Model HZ-85 showing how dividers are used in a barrel to facilitate separate part processing.
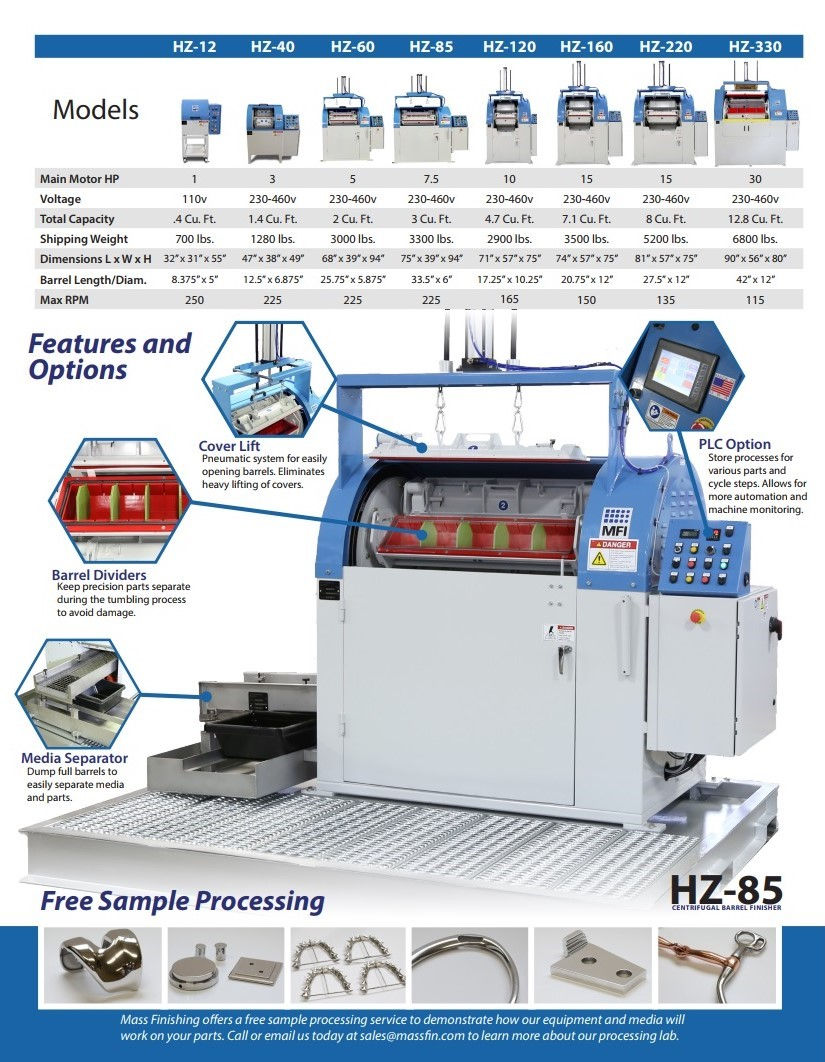
SAMPLE PART PROCESSING PROGRAM. An essential step in determining the right equipment for your part is running samples in our process laboratory. Once we have your parts in-house, we’ll determine what type of media and processing times it will take to get your desired finish and return the parts to you for you evaluation. FEEDBACK IS IMPORTANT. You need to get back to us with information about the part finish results so we can make modifications to the process if necessary. Dave Davidson at ddavidson@deburring-tech-group.com
Leader in High Energy Centrifugal Barrel Finishing Machines As an industry leader in the production of finishing and polishing equipment, MFI is capable of assisting you every step of the way. This includes helping you develop your finishing process goals along with your production and profit objectives.
Mass Finishing, Inc. (MFI) is a manufacturer of deburring and polishing equipment. Clientele includes medical device manufacturers, the aerospace industry, automakers, gun manufacturers and many more. The high-energy Centrifugal Iso-Finishing machines we specialize in can produce unmatched isotropic surface finishes and also handle part finishing problems related to deburring, radiusing, cleaning, heat treat scale removal, surface finish improvement, service life extension and metal fatigue failure resistance.
Discussion on MFI. History, process development, manufacturing operations and process development capabilities.
Mass Finishing, Inc's Technology director, Tommy Mathisen gives a demonstration of a three-step process in an HZ-60 Centrifugal Barrel Finishing machine Three step processing is used to develop highly polished finishes similar to what you would expect from jewelry. (1) Deburring and soothing (2) Fine smoothing and (3) Final Polishing.
This Model HZ-40 machine is popular among manufacturers of small arts in the jewelry, dental, medical and other small part industries. In this video barrels with plastic barrel liners is shown. This is useful for applications where there is a need to avoid part-on-part contact during the processing.
In this video an HZ-40 machine is used in a two-step process to first deburr and smooth and then burnish (brighten) parts. The burnishing process can be used in many part applications to strengthen parts against premature metal fatigue failure with centrifugally induced compressive stress.
This Model HZ-85 is being used to run a 3 step finishing process on machined orthopedic medical bone plate parts to first deburr, then smooth and highly polish these medical implant parts. Often times machines like this Model HZ-85 are used with barrel dividers to keep parts separate from each other during the process. In this particular process, the parts are being run in bulk.
In this video, an HZ-85 Model machine is being used in a single step to deburr and deflash clear plastic dental aligners. prior to the adoption of this centrifugal finishing procedure that type of edge finishing was being performed by hand in a tedious manual oeration.
Factory floor video. Katie MacKay ay Mackay Mfg in Spokane, WA explains how they use a Model HZ-120 machine for deburring, smoothing and polishing of machined parts in Spokane, Washington
This Centrifugal Barrel Finishing machine is typical of larger diameter machines. The largest machine available is an MFI HZ-330 machine with hexagonal processing barrels that are 12 inches in diameter and are 42 inches in length. Contact me at ddavidson@deburring-tech-group.com for additional information on free sample part processing for your parts.
Contract Finishing option. Need to have some of your parts processed with Centrifugal Iso-Finishing but not ready for an equipment purchase. Contact us at ddavidson@deburring-tech-group.com to make arrangements for sample part processing along with a job shop quote for your parts.

Comments