*NEW* Post-Process Surface Finishing of Additive Manufactured Parts with Dry Electro-Polishing
- David A. Davidson
- Apr 30, 2018
- 2 min read
by Contributing Editor: David A. Davidson
Contact me at dryfinish@gmail.com | 509.230.6821
about sample finishing for your parts...
See also: https://dryfinish.wixsite.com/iso-finish
_________________________________________________

Metal Additive Manufactured parts offer a substantial finishing challenge for 3D printed parts for many industries. This is especially true of parts with complex geometries and intricate designs that have a need to improve the surface finish on more interior areas of part shapes. Some parts also have a requirement that the edge geometries of the part be maintained.,which can be problematical for many mechanical based abrasive finishing and polishing systems.
This dry electro-polishing method is much simpler in concept than conventional electro-polishing most finishers are familiar with. With the new method, there is no liquid electrolyte required, and specialized conformal tooling for different part shapes are not utilized.
Above are a variety of parts with before and after comparisons of surfaces prior to dry electro-polishing and as shown after processing. The method makes use of dry bead-like or granular materials that are finely divided and that can access intricate part areas and acts as a transfer medium for the electrolytic processing.
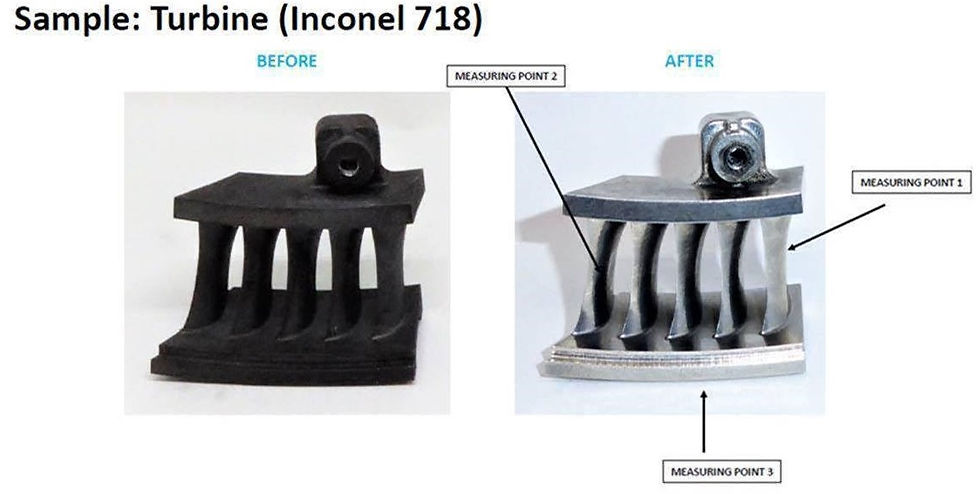

Above are pictorial and graphic measurement comparisons of the process results on aerospace parts made from Inconel.718.

This polishing method is non-abrasive in character. surface polishing results from ion transfer and the effect is concentrated on surface peaks. Little or no edge radius is developed and edge definition is preserved as is the overall geometric shape and dimensional integrity.
The Process Benefits and Advantages are:
(1) Smoothing and polishing operations are performed in a single step.
(2) Simpler and accelerated part throughput
(3) Complex parts can be processed without disassembly
(4) Non-conductive materials are unaffected
(5) Part geometry is maintained
(6) Minimal material or stock removal
(7) Extensive expertise or training is not required
(8) Low maintenance and consumable materials cost
(9) Environmentally friendly
For information on sample finishing and processing contact: Dave Davidson - dryfinish@gmail.com
or 509-230.6821
Comments