Avoiding Part-on-Part Contact in High Energy Surface Finishing Systems
- by David A. Davidson
- May 24, 2018
- 3 min read

Above: A Model HZ-85 Centrifugal Iso-Finishing Machine with divider inserts processes parts in separate compartments to prevent surface impingement of parts being processed in high-energy rapid processes.
Contributing Editor: Dave Davidson, Deburring/Finishing Technologist | 509.230.6821 | dryfinish@gmail.com | https://about.me/dave.davidson
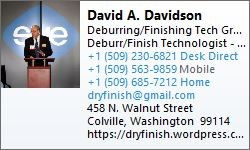
If you have parts that need edge or surface finishing improvement and would like to have FREE sample part processing and a quotation developed for finishing the parts please contact Dave Davidson at dryfinish@gmail.com I can also be reached at 509.230.6821 Information about equipment for bringing Centrifugal Iso-Finishing Equipment to your facility is also available...
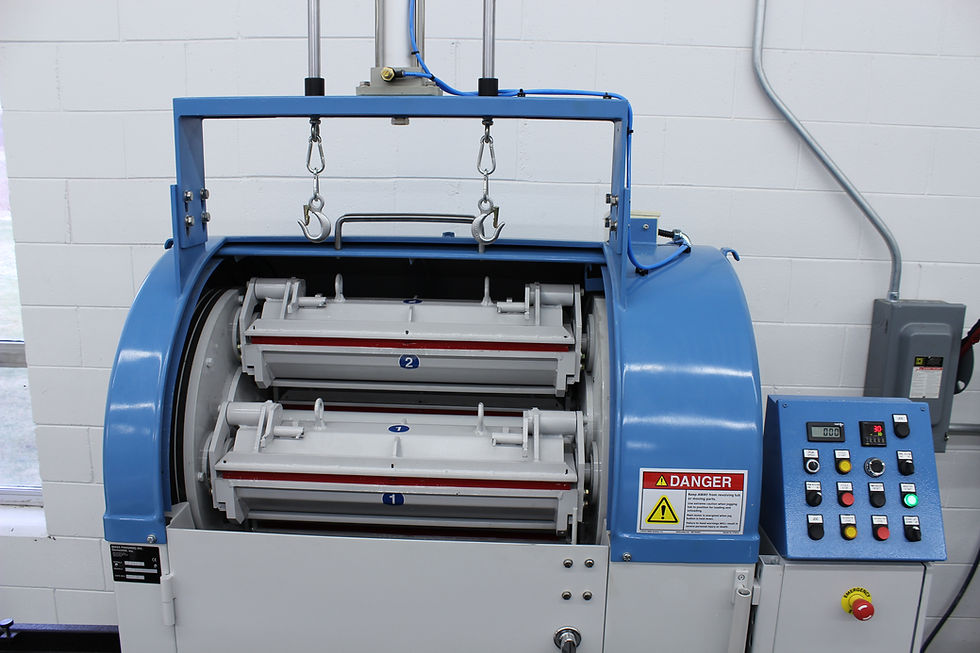
Above: Model HZ-60 machine with long barrels that can accomodate divider inserts so that the barrels can be subvidivided into smaller processing compartments. To see detailed information on this machine model see also the product brochure at this link:
Avoiding Part-on-Part Contact...
Centrifugal Iso-Finishing is an accelerated mass finishing process that utilizes high force to perform deburring, smoothing and polishing rapidly on part edges and surfaces. The high-force of the interaction of abrasive or polishing materials on parts surfaces comes from the 10 G's (or more) of force that is developed by the centrifugal forces developed by the machine for processing. This force makes it possible to develop edge and surface finish conditions up to ten times more rapidly than traditional mass finishing equipment that is limited to 1 G of media pressure or force against parts or components being finished.
PROBLEM: In small part finishing this centrifugal pressure does not seem to pose much of a problem for the process. Large numbers of parts in jewelry, dental, medical, screw machine and many other industries have been successfully deburred, smoothed and polished for many years with out a problem, when the finishing media and the parts are correctly loaded into the processing chamber of the machine. In recent years there has been an increasing demand for the fine-finishing and even super-finishing and polishing that this type of process can produce on ever larger parts. (Some finishes as low as 1 micro-inch and lower have been achieved on certain of these parts). Many of the parts that require this type of fine finish have critical surfaces. Surface impingement arising from part-on-part collision within the process chamber MUST BE AVOIDED.
SOLUTION. In recent years, some manufacturers have come up with centrifugal iso-finishing machines that are capable of processing large numbers of larger parts that would have posed a problem had the parts been run together in the same processing compartment. This is accomplished by arranging divider inserts to break up the larger processing compartment into sub-compartments so that these critical parts can now be centrifugally finished in its own segregated compartment. Some equipment designs have been modified so that hexagonal processing chambers are longer and now able to accommodate much larger numbers to meet higher production targets.
EXAMPLES: See below a video showing the process on some larger aluminum parts, which are first smoothed in a wet abrasive process and then dry polished for final finish treatment. (This same type of sequential processing is accomplished on ferrous alloys and other harder metals with a three step sequence. In many cases the process cycle times involved for each step are thirty minutes or under)
See the videos below:
Below see some photos of some of the equipment and the type of parts that make good candidates for this type of high speed centrifugal processing:
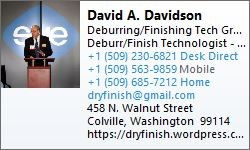
About Dave Davidson: I am a deburring and surface finishing specialist, consultant and advisor to SME's [Society of Manufacturing Engineers] Technical Community Network. The focus of my activity is assisting manufacturers and machine shops with reducing their dependence on hand or manual deburring and finishing methods. We also help them to upgrade the edge and surface finish quality of their parts. I currently work from Colville, WA but I assist clients nation-wide. I can arrange for free sample processing and process development for your challenging deburring and finishing problems and can provide you with either contract finishing services or the in-house capability to produce improved hands-free finishes on precision parts. I can be contacted at 509.230.6821 or dryfinish@gmail.com


Comments