EXTREME SURFACE FINISHING with Centrifugal Iso-Finishing
- by David A. Davidson
- Jul 18, 2018
- 2 min read
Contributing Editor: Contact: Dave Davidson, Deburring/Finishing Technologist | 509.230.6821

Above: Flame-cut foundry steel castings, with as-cast and flame-cut surfaces . Demonstration experiment to validate surface profile reduction on extremely rough surfaces. In this case a two-step centrifugal method was used with an abrasive media operation followed up with a burnishing media process using non-abrasive media. Other applications that could make use of this high-speed, hands-free centrifugal processing would include: investment castings, metal additive manufacturing and 3D printed parts, forgings and others.
The Method: Centrifugal Isotropic Finishing
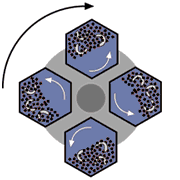
This is a high-intensity edge surface finishing method that is useful for producing very refined surface finishes and functionally useful isotropic surfaces.
The method makes use of high G forces generated centrifugally to multiply the surface interaction of abrasive or polishing material with part surfaces. It is not uncommon for edge and surface effects to be developed in cycle times less than 1/10th of more conventional methods
The Parts: Flame-cut foundry steel castings, with as-cast and flame-cut surfaces . Demonstration experiment to validate surface profile reduction on extremely rough surfaces
Processing Notes: Parts were processed with a two-step method, the first involving high-intensity centrifugal finishing with heavily abrasive ceramic preformed media. A secondary non-abrasive operation was then performed utilizing a very heavy bulk-density burnishing material comprised of specially prepared sintered bauxite material. In this two step processing initial part surface was reduced from surfaces that were in the 250 - 300 micro-inch Ra range to level burnished surfaces in the 10 - 20 micro-inch Ra range.
Above: Examples of extreme surface reduction achieved with centrifugal iso-finishing processes that utilize both wet process smoothing with follow up processing that makes use of dry process polishing materials on stainless steel investment castings
Above are examples of surface reduction,smoothing and polishing of metal additive manufactured parts
_______________________________________________________________
Below are some process video footage demonstrations of high-speed centrifugal isotropic finishing. These automated edge and surface finishing methods are capable of producing very refined low micro-inch surfaces that can improve functional part performance and service life.
More about Dave Davidson…

I am a deburring and surface finishing specialist, consultant and advisor to SME’s [Society of Manufacturing Engineers] Technical Community Network. The focus of my activity is assisting manufacturers and machine shops with reducing their dependence on hand or manual deburring and finishing methods, and helping them to upgrade the edge and surface finish quality of their parts. I currently work from Norwich, NY but I assist clients nation-wide. I can arrange for free sample processing and process development for your challenging deburring and finishing needs and can provide you with either contract finishing services or the in-house capability to produce improved hands-free finishes on precision parts. I can be contacted at 509.563.9859 or dryfinish@gmail.com. Let me know if I can be helpful.
Comments