Hands-Free and High-Speed Post Process Surface Finishing of 3D Parts with Centrifugal Iso-Finishing
- David A. Davidson
- Aug 1, 2018
- 4 min read

This is a guest column by Mike Klein, Chief Technical Officer at Isofinishing, Inc. Centrifugal Iso-Finishing specialists and contract finishing services contractors.
Additive components rarely meet surface standards without post processing. Post processing for additive parts is an important step in the manufacturing process. It's the final stage where parts receive a market ready finish. Post processing improves the quality of parts and enhances the surface characteristics, geometric accuracy, and mechanical properties.
Centrifugal Isotropic Finishing has been shown to be useful in reducing the rough surfaces common to 3D printed parts. Below is an example of surface finishes that can be achieved with the method.
Centrifugal isotropic finishing (CIF) is a high-energy finishing method, which has come into widespread acceptance in recent years. and a long list of important CIF applications for precision machined and additive parts have been developed in the last few years.
Similar in some respects to barrel finishing, in that a drum-type container is partially filled with media and set in motion to create a sliding action of the contents, CBF is different from other finishing methods in some significant ways. Among these are the high pressures developed in terms of media contact with parts, the unique sliding action induced by rotational and centrifugal forces, and accelerated abrading or finishing action. As is true with other high energy processes, because time cycles are much abbreviated, surface finishes can be developed in minutes, which might tie up conventional equipment for many hours.
Centrifugal Barrel Finishing principles – high-intensity finishing is performed with barrels mounted on the periphery of a turret. The turret rotates providing the bulk of the centrifugal action, the barrels counter-rotate to provide the sliding abrasive action on parts.
The principle behind CIF is relatively straightforward. Opposing barrels or drums are positioned circumferentially on a turret. (Most systems have either two or four barrels mounted on the turret; some manufacturers favor a vertical and others a horizontal orientation for the turret.) As the turret rotates at high speed, the barrels are counter rotated, creating very high G-forces or pressures, as well as considerable media sliding action within the drums. Pressures as high as 50 Gs have been claimed for some equipment. The more standard equipment types range in size from 1 ft3 (30 L) to 10 ft3, although much larger equipment has been built for some applications.
For information on our (free) sample part processing program go here: https://dryfinish.wordpress.com/2018/06/15/high-energy-centrifugal-iso-finishing-contract-services-for-deburring-and-super-iso-finishing-information-and-sample-finishing-request-form/

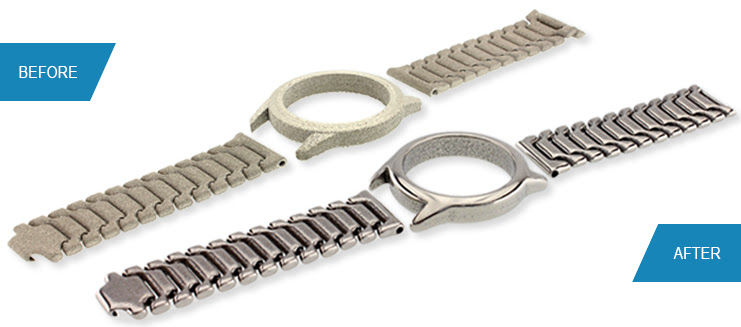
____________________________________________________________
CONTACT: Dave Davidson, Deburring/Finishing Technologist Phone: 509.230.6821 | dryfinish@gmail.com | https://about.me/dave.davidson

If you have parts that need edge or surface finishing improvement and would like to have FREE sample part processing and a quotation developed for finishing the parts contact Dave Davidson at dryfinish@gmail.com I can also be reached at 509.230.6821. Information about equipment for bringing Centrifugal Iso-Finishing capability to your facility is also available…
________________________________________________

_______________________________________________
3D Printing, Layered Manufacturing, Rapid Prototyping, Additive Fabrication
ISO Finishing provides complete finishing services for all major and additive manufacturing markets including aerospace/aviation, automotive/performance motorsports, defense/military, dental, firearms, hydraulic, medical, OEM, pharmaceutical, and plastic industries. We have developed documented processes designed to ensure each finished part exceeds the most demanding requirements.
In order to achieve the necessary specifications or improve properties such as surface quality, geometrical accuracy and mechanical properties, it is often necessary to post-process and finish components produced with additive manufacturing techniques for materials such as ceramics, metals, and polymers.
The reach of additive manufacturing is rapidly expanding. While its current uses and applications are already diverse, experts across industries agree additive manufacturing is more than a trend. AM has been revolutionary for the industries that use it most, and researchers continue to develop new applications to solve problems across countless other fields of expertise.
Below are slides of other Centrifugal Iso-Finishing part projects...
Below are some examples of Centrifugal Isofinishing Equipment used to produce these edge and surface finishes...
Post Processing Finishing Services for Additive Manufacturing
Centrifugal Barrel Finishing Barrel tumblers work well for jobs requiring heavy burr removal. Centrifugal barrel finishing machines are also good for burnishing, rapid radiusing of edges, and heavy deburring. Removing excess material or polishing additive parts, remove burrs, improve surface appearance, polish and clean are all possible using centrifugal barrel finishing equipment.
Deburring In the manufacturing world, deburring refers various methods used to remove burrs, the residual rough edges or protrusions left behind after a part is produced. Burrs can affect the surface quality of additive parts produced where performance, safety, and appearance of a part is concerned.
Deflashing Deflashing is the process of removing residual rubber, titanium, stainless or plastic material used in the injection molding process. During 3D printing, the deposition of small bits of residual material called “flashing” may appear each part. The particles can be removed using a centrifugal barrel machine for a fast and cost-effective method of removing any residual particles.
Radiusing Radiusing is a type of deburring which entails the removal or rounding of sharp part edges formed during the additive manufacturing process. Parts with sharp edges can be radiused to pre-defined specifications using centrifugal barrels, vibratory bowls and centrifugal disc machines.

Support Structure Removal Support materials are structures that are 3D printed along with the actual product to provide support to fragile, thin or overhanging areas. These support materials are temporary and can be removed using mass finishing techniques. Achieving the necessary specifications or improve the overall surface quality, additive manufactured products often need post-process and finishing. There is usual surface roughness left on parts after the support structural material is removed. Most physical characteristics can be enhanced by adding well developed and documented surface finishing processes at the end of the AM process. Depending on a part’s material, geometry, and purpose, our parameters may include vibratory deburring/polishing, centrifugal barrel polishing, ultrasonic cleaning, passivation, anodizing or other coating services.
Comments