The Role of Surface Finish in Improving Part Performance
- by David A. Davidson
- May 21, 2019
- 6 min read


For additional information contact Dave Davidson at ddavidson@deburring-tech-group.com or +1.509.563.9859
The mechanism that allows for improved “functionality” for all surfaces is basic to surface performance —to accept the loads imposed and resist wear. Traditional processes that generate form and control fit do not necessarily dictate how that part or assembly will function over time. In recent years, it has been realized that there is another contributor to long term part performance—surface finish. If a manufacturer does not account for surface finish characteristics like lube retention, micro burr removal, identification of torn and folded material, directionality, and load-bearing capability, the performance of components in the system cannot be predicted. (See below: Parts and components with Centrifugal Iso-Finished Surfaces)
ABOVE: Watch operation of a Model HZ-120 Centrifugal Iso-Finishing Machine
High-energy finishing processes can contribute to more predictable and extended service life by developing useful and uniform compressive stress equilibrium in parts as a hedge against premature fatigue failure. Through progressive process development, evolving measures, and a mature understanding of the “function” of surfaces, manufacturers can design parts that become assemblies that are in systems performing over predictable, extended lives. This is the key to reduced warranty costs, reduced scrap, higher quality, lower production costs, and satisfied customers and end-users. Centrifugal Iso-Finishing processes can be used to improve part performance and service life, and these processes can be tailored or modified to amplify this effect. Although the ability of these processes to drive down deburring and surface finishing costs when compared to manual procedures is well known and documented, their ability to dramatically effect part performance and extend service life is not nearly as well understood by the manufacturing engineering community.
Why Centrifugal Iso-Finishing?
Centrifugal Iso-Finishing is a high-speed and high-intensity mass finishing method in which abrasive or polishing materials are caused to interact with part edges and surfaces with ten times the surface pressure (10 G’s) found in low energy finishing methods. What this means, in practical terms, is that it is possible to produce very refined surface finishes in abbreviated process cycle times that can obviate the need for over-lengthy processing that previously were the source of production bottle-necks. It also means that parts with complex and detailed geometries can be deburred with a minimum of manual intervention. This is because the higher surface pressures generated in the equipment makes it possible to utilize much smaller dimensioned media effectively. The smaller dimensions of these preformed media shapes make it possible to access areas that cannot be reached with more conventional sized media commonly used in lower energy positive displacement or kinetic surface finishing methods. (See examples of various models of Centrifugal Iso-Finishing Equipment shown in the slides below)
Challenges from Part Complexity and Surface Finish Requirements. The increased complexity and precision requirements of machined mechanical products have reinforced the need for more accurately producing and controlling the surface finish of manufactured parts. Variations in part surface texture can influence a variety of performance characteristics. The surface finish can affect the ability of the part to resist wear and fatigue; to assist or destroy effective lubrication; to increase or decrease friction and/or abrasion with cooperating parts; and to resist corrosion. As these characteristics become critical under certain operating conditions, the surface finish can dictate the performance, integrity and service life of the manufactured parts.
Sequential Processing (See an example of centrifugal sequential processing in the video shown above.)
To meet more demanding surface finish requirements, one trait that many of today’s more sophisticated mass finishing operations share is a reliance on multiple-step sequential processing. In this type of processing, very rough surfaces can be brought to a highly polished or micro finished state. This is done by initially processing the parts with coarse abrasive material, and then following up with a sequence of steps using finer abrasives. Each of the subsequent steps uses an abrasive material that has been calculated to clear and blend-in the abrasive pattern left on the surface by the preceding step. To use a common everyday analogy, almost everyone understands that to produce fine finishes in woodworking applications, it is necessary to use sanding operations with successively finer abrasive grits to produce cabinet or furniture quality surfaces. The same principle holds true when mass finishing metal and some plastic parts, when very smooth or polished micro-finished surfaces are required.
One time-honored method for producing very refined surfaces on softer metal alloys and some plastics is sequential step dry barrel processing. This technology was originally developed and heavily utilized in the northeastern United States as early as the 1930’s; similar methods were developed concurrently in Europe.
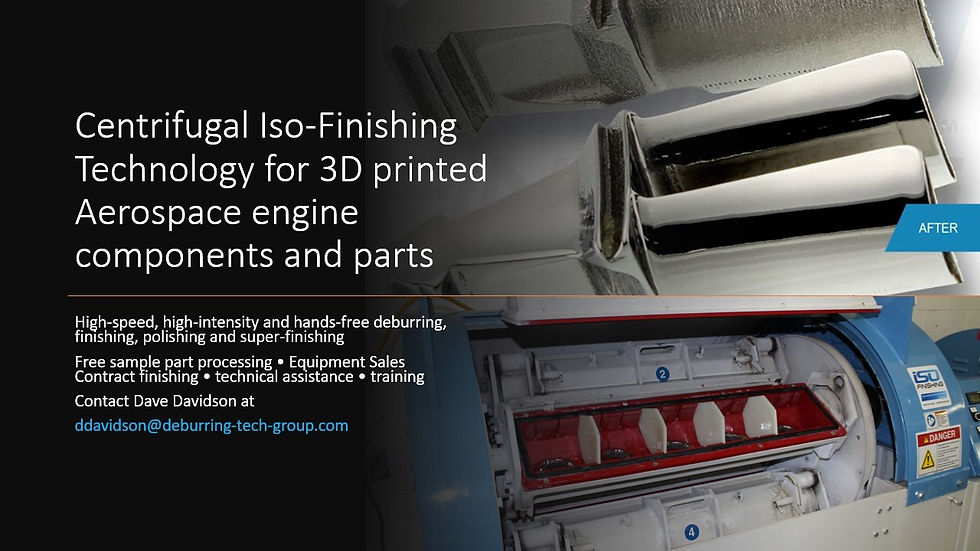
The method was developed primarily to mitigate the high labor costs associated with hand-buffing large numbers of consumer-oriented articles such as eyewear and jewelry. This technique was widely accepted as a standard method for producing very refined consumer acceptable product finishes that had previously been the sole province of hand buffing methods and it is still utilized for these types of applications to this day. This sequential processing principle has been adapted for use in other types of equipment for other part finishing applications. Where reflective or very level surfaces are desired on parts being finished, it is not unusual now to see secondary processes with non-abrasive burnishing media or dry process polishing media develop these more refined surfaces.
Flexible Processing
Many processes have been developed for centrifugal barrel finishing where two or even three steps are utilized to bring part surfaces to very low micro-inch surface profiles, or to develop very reflective surfaces for cosmetic or aesthetic reasons. With other mass finishing processes, it is not unusual to see dedicated equipment assigned to handle each of these processing steps. Centrifugal Iso-Finishing processes typically can process these several steps in the same equipment as the equipment is typically furnished with four processing compartments that run simultaneously, and relatively quick change-outs of processing media are possible. In a factory floor video interview produced by the SME Deburring/Finishing Technical Group and the SME chapter 248 in Spokane WA, Katie MacKay, VP of Mackay Manufacturing elaborated on their transition to centrifugal iso-finishing. The company was struggling with a very complex aluminum part that had numerous drilled holes and edges and planes. Although the company had vibratory finishing equipment at their disposal, this part still required eight hours of hand deburring following the vibratory processing. After transitioning to centrifugal processing, the hand deburring was reduced to less than an hour and justified the purchase of the equipment by itself.
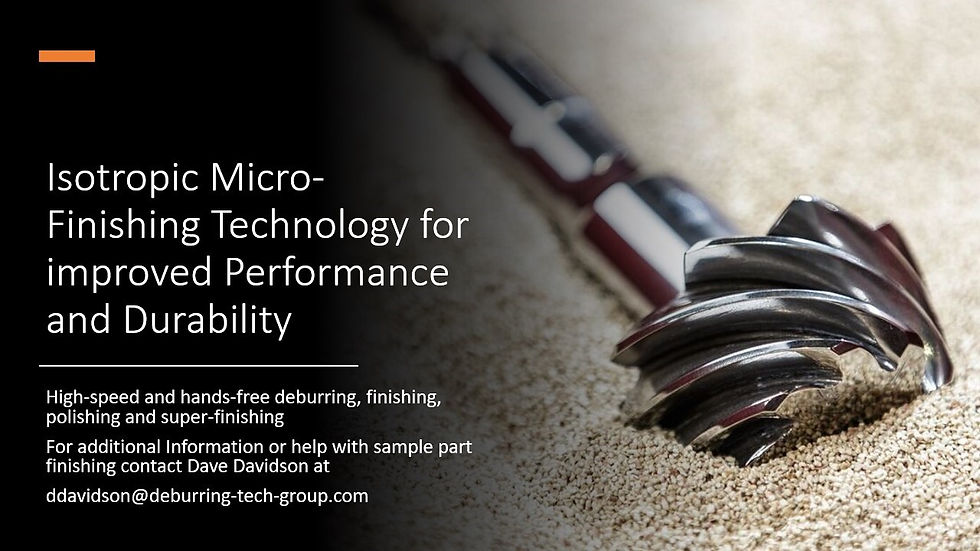
Since then, centrifugal processing has become the standard finishing method for the company. Without the machine the company would need an additional three employees on its deburring staff. Since the installation, the company has developed processing for more than fifty additional part numbers made from titanium, steel, stainless steel, aluminum and plastic. Over two dozen different finishing “recipes” are used to process the different parts to specification. In some cases, parts are finished to highly polished surfaces with low micro-inch surface values. Almost all the deburring and finishing needs of this 135-employee contract machining company with 50,000 square feet of manufacturing space is serviced by this one machine.
(Watch the video of Centrifugal Iso-Finish processing at MacKay Manufacturing shown below:)
If you have parts that need edge or surface finishing improvement and would like to have FREE sample part processing and a quotation developed for finishing the parts please contact Dave Davidson at ddavidson@deburring-tech-group.com I can also be reached at 509.563.9859 Information about equipment for bringing Centrifugal Iso-Finishing Equipment to your facility is also available...
I am a deburring and surface finishing specialist, consultant and advisor to SME's [Society of Manufacturing Engineers] Technical Community Network. The focus of my activity is assisting manufacturers and machine shops with reducing their dependence on hand or manual deburring and finishing methods. We also help them to upgrade the edge and surface finish quality of their parts. I currently work from Norwich, NY but I assist clients nation-wide. I can arrange for free sample processing and process development for your challenging deburring and finishing problems and can provide you with either contract finishing services or the in-house capability to produce improved hands-free finishes on precision parts. I can be contacted at 509.563.9859 or ddavidson@deburring-tech-group.com Let me know if I can be helpful.
These links will provide additional information:
This is a portfolio of some recent part finishing applications: https://dryfinish.wixsite.com/iso-finish




Comments