Centrifugal Super Finishing and Polishing of Conventional and Additive Manufactured Parts
- by Dave Davidson
- Jun 14, 2019
- 2 min read
Updated: Apr 28, 2021
CONTACT: Dave Davidson, Deburring/Finishing Technologist, +1.509.563.9859
There is an increasing demand within industry for developing low micro-inch finishes on precision parts. For years this type of finishing required a certain amount of hand deburring and hand polishing. Much of this manual component is being now being replaced with multi-step processing in Centrifugal Iso-Finishing Equipment. In the illustration shown below is an example of multi-step processing, show the progression of the surface finish on the part as it comes out of each step. Similar results are developed on dental and orthodontic parts, medical and orthopedic implants and implements, high-performance racing engine components, aerospace engine parts, aero-structural parts, firearm parts, precision CNC components and many others.

ABOVE: The photo illustrates the use of 3 step Centrifugal Iso-Finishing processes in order to develop highly refined and polished surfaces (often with single digit microinch surface profile readings.) While the processes vary with alloy, shape, weight and initial surface roughness of the part, they generally are processed in three different steps. The parts in the photo show a progression of surface finishes (1) Before processing (2) Following surface finishing with heavy bulk-density abrasive preformed shapes. (3) Processing with lighter weight resin-bonded preformed media. (4) After processing with dry organic granules that have been treated with proprietary micro-fine polishing materials.
An example of this three step processing can be seen in the video shown below. In this example, aluminum CNC parts are being deburred, smoothed and polished in the same machine but with differing media combinations in sequence. A similar sequence of media operations would work on almost all softer alloys. For ferrous and exotic alloys, the combination would be altered and would make use of harder, heavier and more abrasive processing material in the first step.
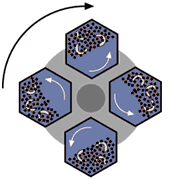
HOW IT WORKS: Centrifugal Iso-Finishing Technology operation is similar to the operation of a "Ferris Wheel" but this Ferris wheel operates at high rotational speed with the turret swinging the barrels around its periphery while the barrels counter-rotate at high speed. This motion imparts high centrifugal force to the parts and media in the processing chambers and finishing and polishing work is performed 10 times faster than conventional low-energy finishing equipment. On many parts, single digit micro-inch Ra surface finishes can be achieved.
BELOW: A photo allery of other part types processed with the Centrifugal Iso-Finishing method can be seen below:
BELOW: Slide-show of various models of centrifugal iso-finishing equipment
For additional information or assistance with having your parts sample finished contact me at ddavidson@deburring-tech-group.com or +1.509.563.9859
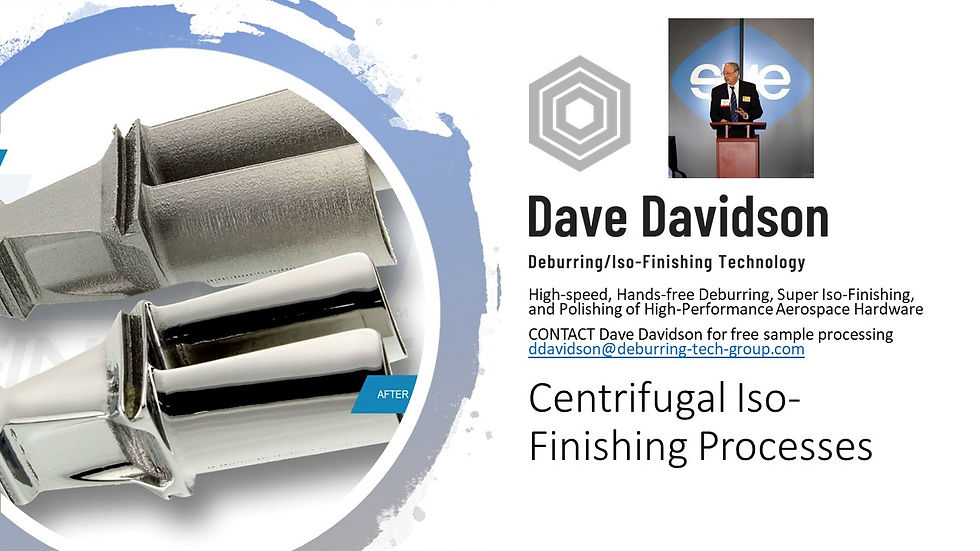
Below: Part photos of Centrifugal Iso-Finished parts that have been processed with (1) "Wet (grinding and smoothing) processes and the final polished with dry process polishing media.


For additional information or assistance with having your parts sample finished contact me at ddavidson@deburring-tech-group.com or +1.509.563.9859
Comments