Mass Finishing Problems and Their Effect on the Future
- John Kittrege, CMfgE
- Jul 17, 2019
- 33 min read
Updated: Dec 6, 2020
Revised and edited by Contributing Editor: David A. Davidson, Deburring/Finishing Technologist,
Email: ddavidson@deburring-tech-group.com | Web-site: https://dryfinish.wixsite.com/iso-finish
[Editor's note: This technical paper was written by John Kittredge as his career was drawing to a close. He wanted to write a brief summary about some of the problems he had observed with mass finishing processes in his work as a technical director of an equipment manufacturer and as an independent consultant. John was a founder of the Mass Finishing Job Shops Association, He lectured extensively for the Society of Manufacturing Engineers on Mass Finishing subjects and wrote extensively for periodicals such as PRODUCTS FINISHING magazine. He also was a friend, a colleague and a mentor, and I knew and worked with him from the start of my career in the 1980s.].]

TITLE: Mass Finishing Problems and Their Effect on the Future.
AUTHOR: John B. Kittredge, CMfgE
TECHNICAL PAPER NUMBER: MR91-118
INDEX TERMS: Finishing, Vibratory Finishing, Deburring, Corrosion Prevention, Barrel Finishing, Cleaning, Training
ABSTRACT: Problems can become challenges, rather than just agony and turmoil. Challenges can make the solutions to problems beneficial, rather than stop-gaps which just let us get through another day. This paper deals with problems that have occurred in the field of mass finishing and the effect they are having. It includes problems related to mass finishing equipment, media, compound and water and people. Some will seem humorous by today’s standards while others are much more serious. Many form the basis of an excellent learning process and may easily withstand the scrutiny of time.
The purpose of this paper is to reflect on a few of the problems encountered during the past 25+ years in the mass finishing business and to see what has been learned from them. Some were quite dramatic and therefore have been quite important over the years. They teach a lot about the processes we call “mass finishing” and of the people serving this industry and others. They may be helpful to others as well.
INTRODUCTION
First of all, what is mass finishing’? We define it as a mass of parts dispersed in a mass of media with a compound and water solution, contained in a piece of equipment which generates a desirable, differential action between the media and parts. Media is the tool that does the cutting or polishing. It keeps parts separated and prevents excessive contact of one with one another during the process.
Equipment includes the now-elderly rotary barrel, sometimes incorrectly referred to as a “tumbling barrel”. This is because parts do not normally “tumble” in a properly run barrel. They usually slide with the media - sometimes gently, and sometimes with considerable vigor.
The equipment also includes both the more-popular tub and round vibrators and the higher energy centrifugal disk, centrifugal barrel and spindle machines. Compound and water solutions are critical to cleaning media and parts, preventing corrosion, controlling, cut-rate of media and lots more. The “solution” is the key because 99% of it is water and water varies tremendously all across the country. It is as important as the compound. The media is kept clean and free to cut and it and the parts are cleaned and kept rust-free by proper use of the compound aad water solution.

Above: [Editor's note] Photo shows the vibratory induced roll and flow action of media in a round bowl vibratory machine. These machines are heavily utilized throughout industry and are especially useful because of the internal automated parts/media separation that are available on many models which is a major materials handling and labor-savings advantage. The machine shown above is a Model BV-5DR manufactured by BV Products located in Melbourne, Australia.
The differential action referred to in our definition is the result of machine design. The parts and media should slide by each other with some pressure so that scrubbing and cutting will occur, but without the excessive impact that might cause damage to the surfaces of the parts. With abrasive media, this scrubbing cuts metal. With non-abrasive media, it causes brightening to occur. More complete descriptions of mass finishing can be found in the references cited at the end of this report.
MEDIA PROBLEMS
1. A company out West was running zinc die castings in a large vibratory finishing machine. The company owner was complaining about the poor cut rate of the media. Cycle times were too long. A look at the machine, made the trouble apparent. The vibrator was full of parts, but only about 10% of the bottom of the machine contained media. There just wasn't enough in the machine to do much good. It was suggested that a “fix” for the problem was quite easy: fill up the machine. He didn’t want to because of the increased cost of operation. And this was compared with his former buffing operations.
Conclusion: What is the price to pay for saving money? Is there an end to “cost-saving”?

[Editor's note] Above: Shown are some typical media types used in vibratory and other) mass finishing processes.
From left to right: (1) Plastic (brown) cone media. Used for finishing softer alloys, and also for preparing surfaces for plating operations. It is also used as a second step to further refine surfaces on harder alloys subsequent to ceramic media finishing to prepare surfaces or super-finishing and polishing operations.
(2) Porcelain white cylinders. This media is used in conjunction with special aqueous compounds for burnishing operations. This is a non-abrasive procedure that follows prior abrasive operations. The burnishing levels surfaces by compression rather than by abrasion. Surface peaks and asperities are "compressed" rather than abrasively removed. Similar materials are also use with acidic accelearants to develop super-finishing on gears and other cooperating parts for the high-performance motor-sports, automotive and aerospace industries.
(3) Ceramic (gray) triangle media. This media is used primarily for deburring and smoothing rough surfaces on harder alloys.
(4) Blue Plastic media cones. Similar in function to the brown cones previously described. Media manufacturers use color coding to differentiate different plastic media levels of abrasive grit content. This is especially useful for plants or shops who may be using different grades of media in the deburring/finishing operations. Photo courtesy of Jim Riley, BV Products, Melbourne, Australia
2. Did you ever see a grown man cry - almost ? A large mass finishing job shop out East had a problem. A l0+ cubic foot vibratory finishing machine was filled with small D-shaped parts, every one of which had 4 pieces of media stuck in it! That same load of media had been used for that part, and only for that part, since the day that job shop got that business, and finally it wore down to just the wrong size.
Conclusion: Even the experts can be fooled by lodging and many other of the major variables in mass finishing. But, they’re not fooled often or they don’t stay in business.
3. A big manufacturing company was proud of their relatively new vibratory finishing systems. They had replaced a room full of men and women who hand deflashed their die castings. However, they had a room full of men and women band-picking media out of their parts. Just as big a room as before, but they were happy because the part quality was so much better. What did they do with the media they picked out of their castings? Yes, they put it all back into their vibrators “to save money” (and to get lodged in the next load of parts.) It was suggested that they use it elsewhere or sell it to someone who could use it, but this would have meant another “change” and they wouldn’t do it.
Conclusion: What is the price you must pay to save money and improve quality? It may require thought as well as the investment in capital.
4. Two 50 cubic foot (1400 liter) capacity vibratory steel ball burnishing machines were sold by brand “X”. In their infinite wisdom, they filled the machines with a cheap grade of steel media. Everyone was happy until the media began to crack and break in two. It fractured disastrously. Why? Improper heat-treatment.
Conclusion: An expensive lesson: cheap is not always better.
5. Not long after leaving the media manufacturing business (it had been sold to a third party), we joined a company that was the biggest corporate user of that media. After several months ‘of things going smoothly, trouble. A new load of media was put into a new machine in a new customer’s plant and it wouldn’t cut. After some serious questions and numerous futile calls to the third party, a mild abrasive was added to help promote cut. It did for a few minutes, then stopped again. A brand new load of new media was then put it into the machine. Everything went as advertised. The cut was good, results super. The customer was finally happy. Now, back to the third party. They would not take back their bad media, claiming it had been “contaminated with abrasive.” We agreed, but suggested that the product was not of first-class quality (even though the price was!) Within 6 months. all media purchases to the third party bad been switched to another supplier. That defective load of media probably cost several hundred dollars. The lost business amounted to many thousands of dollars.
Conclusion: With poor supplier support, there is no justification for continued business A big part of what you buy is service - not just taking back defective material - but technical, product and process support, as well.
Above: BV Products Model BV5-DR Round Bowl Vibratory Finishing machine. Direct-drive motion vibratory motion generator is used in this design for more efficient energy transfer. Automated internal parts/media separation sequence is also shown. Video courtesy of Jim Riley at BV Products.
6. There once was a customer who was having terrible media problems. it stopped cutting not too long after he bought it and, after sending the first load back to the manufacturer, but another load that was doing the same thing. With much gnashing of teeth, a few well-placed invectives and more, the customer greeted us with the “Why?“s and “How Come?? that characterize such encounters. After an inspection of his media and the rest of his mass finishing system, it became apparent that it was not a media problem. This leads us to the next section. , .
COMPOUND and WATER “SOLUTION” PROBLEMS
. . . to continue . . . No, it was not a media problem. The customer had a poor-to-terrible solution system - most probably a compound that was not designed for his bard water. Because of this, the compound concentrate reacted with the water producing insoluble calcium and magnesium soaps, depositing them on the media and the lining of the vibrator. The result? The media was polished almost like jewelry. It fairly gleamed. With continued deposits of insoluble material, the media could not continue to cut. The incredible thing here is that even the media supplier didn’t know what was happening. He probably took back the second load of media, too. The customer probably used another supplier and the same thing probably happened. We say “probably” because we don’t really know what happened in detail. He didn’t believe us because his product purchases stopped.
Conclusion: Because he was not given the result he wanted, the customer took his business elsewhere. Was this unfortunate? Not to his supplier. He saved them money by buying from them. It often pays to listen to your suppliers.
7. A die caster in Missouri had been sampled with a new liquid compound. A follow-up was made with him for this and other reasons. Oops! He was not using the new pride and joy. He was using a really cheap powdered material that his machine operator had to premix in a bucket with water “whenever it was necessary.” The bucket was slimy with undissolved powdered material. It was a mess. He admitted that the new mixture did clog up the compound metering pump and that the operator had to take it apart and clean it every day or so. He added that, no, this was not bad. The operator had “plenty of time to do it.” It took at least 30 minutes to clean up the metering pump each time. l/2 hour times 5 days a week times 50 weeks a year meant 125 hours a year (3 whole weeks!) spent cleaning the pump. At only $5.00 an hour (rhea) this amounted to $625.00 per year. Now, how cheap was this powdered compound? He began to use the new liquid right away.
Conclusion: Cost per pound is not the only criteria for saving money. Think it through completely before making such decisions.
[Editor's Note] Above: Chemically Accelerated Super-Finishing is demonstrated in this short video. This type of processing is very popular among automotive, motor-sports, wind-energy and aerospace manufacturers for improving gears, powertrains and other cooperating parts to develop high-performance levels and extend service life. Video courtesy of Jim Riley, BV Products.
8. It’s really awesome when a major manufacturing company is shut down “because of an [expletive deleted] compound. It happened. It seemed that the abrasive compound “no longer cut.” Rotary barrel cycles that had been fine for finishing and radiussing Swedish steel stampings had been doing yeoman's work for years. All of a sudden, zip. Nothing. A complete analysis of existing and prior (sample retain) batches of the product was made with no apparent discrepancies being noted. Still nothing. Tempers flared. Finally, a worker in the plant “no one would listen to” explained the problem. It seems that the coffee machine vendor servicing the plant bad changedfrom 8 ounce (235 ml.) coffee cups to 6 ounce (175 ml.) cups and bed failed fo notify the finishing department. Because the finishing department bad based all of their compound “metering” on (coffee) “cups” of the compound, they were putting in only three-quarters of the required amount.
Conclusion: It pays to use standard measures for everything. If more convenient, use “bandy” measuring devices, such as “cups” and “scoops”. But, be quite sure you know what their real capacity is ... just in case. it could save a lot of time and anguish in the long run.
9. A vibratory finishing machine was quite literally straggling with a process that got longer and longer for the user. The process was to deburr and finish small parts in a very small size of fused aluminum oxide. The machine could barely roll and feed the media mass because the entire machine was filled up with compound and water solution. The drains were clogged. The excess solution could not drain out and it was stopping the action in the machine. The drains were cleaned. The process immediately got better - for a short time. Then the drains were changed to a different design. They allowed much more solution to drain out, but were a bit less effective in retaining the very small media. They saved the process.
Conclusion: Solution going into a vibratory finishing machine must also get out or the process efficiency suffers. Drain design is critical to success in a great many processes.
CLEANING:
10. The barrel is a positive displacement device in that when the barrel rotates, the media-parts mass is elevated, and when elevated sufficiently, it must slide down the hill. Vibratory machines are not positive in their displacement. Here the mechanical action in induced directly into the walls of the chamber and the mass of media and parts inside are asked to respond by a smooth rotary-vibratory action. The mass does not have to do this unless conditions are ‘proper. But it’s supposed to. High lubricity compounds make a very slippery system. The traction between the wall of the vibrator and the media-parts mass and between the media pieces themselves drops, much like a car tire on ice. It skids. No roll. Nothing happens.
One of the early applications for a steel media machine was a big one to clean and deburr cast iron castings. threaded parts. bronze gears, welded sub-assemblies, and lots more. Everything in the plant was togo through the 50 cubic foot (1400 liter) round bowl vibratory machine. Because the parts were threaded. stamped, made outside as well as in house, there were a total of 12-14 different kinds of oily soils on them. The best cleaner then available was having problems with a number of them. The potential for trouble was there.
Several trial compound systems were evaluated. One product made the mass slide around the chamber with absolutely no roll-over. Another trial product made the mass roll-over like crazy, but there was no forward feed. The first “successful” compound was a 50-50 blend of the two. It gave a pretty good roll and feed with most of the oils. The customer.later was able to eliminate 3 or 4 of the most troublesome oils. He was helped over the years by the gradual improvement in his overall system.
Conclusion: Work with your suppliers. They have reason to help you. Meet them half-way if you possibly can. It saves both of you considerable expense and frustration and strengthens the cooperative bonds between you. Cooperative customers are the first to benefit from new products, new process developments and new technology. Cooperation pays.
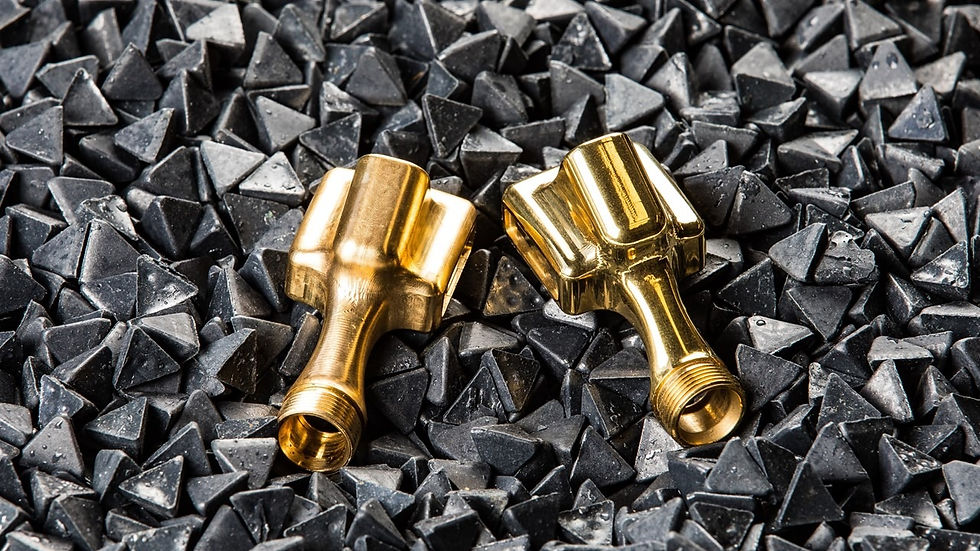
Above: [Editor's note] Shown above are before and after examples of softer alloy parts that have been smoothed and polished. Developing finishes such as this are highly dependent on correct specification of liquid compound used in the processing. Photo courtesy of Jim Riley at BV Products, Melbourne, Australia
11. A watch manufacturer was having residue problems in the zinc die-cast bezels he manufactured. In the recesses of the bezel where the media could not scrub the surface, a deposit was forming. After six hours in small plastic media, these deposits were quite heavy and had to be removed. Tests with another compound verified that this was a compound problem - that a change to another could suspend the solid soils and prevent their deposition in the recesses of the parts.
Conclusion: If the product you are now using does not do your job, work with your supplier to change it. If that doesn’t work, look for another supplier. Caution applies here as we will see later on.
12. A new vibratory finishing system was installed in a toy company plant to deburr and clean steel stampings prior to paint. A mildly acidic compound was being used with the steel media in a very large vibrator. Parts were clean and well deburred, meeting every customer requirement and more. However, after installation of the system, severe problems were encountered with paint adhesion on the parts. This was highly unexpected in that this kind of system had performed so well in a great number of other applications. It just didn’t seem possible that the cause could be with the new process. Immediately following the mass finishing process, an alkaline cleaner was used before painting. By-passing this alkaline cleaner solved the problem. Enough mildly acidic material remained on the parts to react with the alkaline bath depositing a semi-release film on the parts. After skipping the alkaline bath, paint adhesion was excellent.
Conclusion: Oftentimes when a new process is installed, some minor changes may be needed in existing up-or down-stream processes in order to take full advantage of and obtain full benefit from the new one. This is not at all unusual.

Above: [Editor's note] This illustration shows the configuration of a round bowl vibratory finishing machine that has an integral parts/media separation deck. When the machine is deburring and finishing the media mass flows in a counter-clockwise direction. To separate parts from media this direction is reversed, and the offloading ramp is lowered, and parts and media march across the deck with the media dropping back to the media mass until eventually only parts will drop into the tote pan placed at the end of the deck. Photo courtesy of Jim Riley, BV Products.
13. Parts cleaning in vibratory machines with case-hardened, steel media is big business. It’s fast, easy, clean and, because deburring occurs “at no additional cost”, it is very economical. Continuous machines operating in from 7 to 12 minute cycles can handle vast quantities of parts. A user of this kind of system was happy but concerned about the cost of the compound. He was using quite a bit more than had been estimated prior to purchase. Thick, stamped parts came to this plant in solid-bottom steel tote containers. These were hoisted up over a vibratory shaker which metered parts into the vibrator at a controlled rate. When empty, the tote container was allowed to drain out the residual several gallons of heavy stamping oil into the shaker. When this oil hit the vibrator. the machine almost died for fifteen or so minutes. A screen installed between the feeder and vibrator prevented the excess oil from entering the vibrator, materially reducing compound consumption.
Conclusion: For every pound of oil put into a cleaning machine, a given number of pounds of cleaner is required to remove it. Often the simple answers like this one work the best.
14. A very large steel media machine was installed in a customer’s plant. The steel media mass had no action in spite of all manner of weight and other adjustments. It didn’t work. Nothing. Still, it had worked beautifully during check-out in the manufacturer’s plant before shipment. After exhausting the obvious weight adjustments and trying several other compounds, there was no choice. Empty the machine, groove the lining to give the media a place to grip, and try again. The machine was emptied with shovel, scoop and aching backs. It was grooved and abraded all over the bottom and reloaded with the same steel media. Full of bright expectations, the machine was turned on. Nothing. Absolutely no improvement. All of these efforts had done not one lick of good.
A plant maintenance man noted this predicament and asked if water could make a difference. He indicated that the water being used came up directly from the limestone wells underneath the plant and that they had softer, city water piped in as well. He was asked to change it. Like getting a shot in the arm, the machine began to get up and fly. The change in water made so dramatic a difference, it was unbelievable. The weights had to be readjusted to tone down its action.
Conclusion: About 99% of the compound and water “solution” is water. Its importance to the overall system cannot be overemphasized. This lesson has served us well over the years in a great number of other troublesome situations.

Above: [Editor's Note]: Isotropic Finishing. In recent years much ink has been spilled and much written and advertised about the benefits of isotropic finishing. Most of the commercial advertising features photos of parts that are bright, shiny and polished, leading many to conclude that a surface with an isotropic finish is one that is brightly polished. This misses the point. These parts better illustrate the meaning of "isotropic". The part to the left displays a surface that is typical of machined surfaces. In this case machining marks and step-overs from a fly-cutter operation are clearly visible. The part to the right, despite the non-reflective surface is clearly iso-tropic as the scratch patterns apparent in the surface are random and have no aligning pattern. This type of surface is highly functional in terms of part performance and endurance. Parts that are bight and shiny may have isotropic surfaces as well. The reflectivity, however, is a function of surface profile skewness. Common machining (and other fabrication) methods develop positively skewed surface profiles. When finishing methods modify these surfaces into being negatively or neutrally skewed, reflective surfaces with a polished appearance are the result. Photo courtesy of Jim Riley, BV Products
15. Occasionally, it’s fun. A new compound was being used in a new customer’s vibrator running zinc die castings with a very light cutting, ceramic media. Performance - excellent. Everyone was happy.
Brand “X” arrives with his super compound at a lower cost. Talks customer into trying it. In about 15 minutes, the entire machine load of media turned black and, even worse, all the parts came out with an unacceptable, black residue. Frustrated, the brand “X” man left with no sale. The customer put the original compound back on stream. In 15 to 20 minutes the entire machine load of media was sparkling clean again.
Interesting sidelight to this one. Customer had brand “Y”, brand “Z” and a host of others come into his plant to sell compound. His requirement to each of them was, “It’s okay for you to try your compound. But, when it doesn’t work. You are responsible for cleaning up the media and all parts that get black!” One after another, they tried their magic formulae and, one after another, they saw the media and parts turn black. And, one after another, they had no idea of how to clean up the machine and the customer never told them. He already knew how good some products could be in some applications.
CORROSION: A basic understanding of the fundamentals of corrosion, gained from several years with a company that made corrosion-resisting chemical process equipment, has been of great help over the years.
16. A small cantilevered rotary barrel was being used for deburring machined steel parts. Due to corrosion problems on the steel parts they deburred in this little machine, they were using oil in it instead of a compound and water. Parts came out filthy dirty, cycles were very, very long, but they had no corrosion. They had “solved” their problem.
Conclusion: Patchwork solutions often create others. Don’t live with improper solutions unless there really is no alternative.
17. Brass stampings were to be vibratory finished before copper-nickel-chrome electroplate: Quality was equal to that of the best quality jewelry. A vibratory process did the job very well. But, soon some peculiar pits and other defects in the after-plated surface of their parts were noted even though they could see nothing wrong in the part surfaces before plating. Spring and summer had arrived. Corrosion was taking place on these parts prior to their going to plate.
A post-dip in a corrosion inhibitor solution was a successful answer.
Later, another problem. Occasionally, for no apparent reason, a slight pitting of parts after plating was occurring. Several suggestions were tried and nothing seemed to help. Then a detailed description of the process: after vibratory finishing, parts were kept immersed in buckets of inhibitor solution before plating to make extra certain that no corrosion would occur. What kind of buckets? Galvanized. Bingo.
They changed to plastic buckets and never had the problem again. Why? The parts that were pitting were those that sat immersed in the inhibitor solution, especially over long weekends. The contact of a galvanized (zinc) bucket with brass, in the presence of even a moderate-to-poor electrolyte solution, set up enough of a galvanic cell to cause some galvanic corrosion - even while immersed in the inhibitor solution!
Conclusion: Corrosion can be one of the most insidious problems in all of mass finishing. To search for its contribution can take a lot of time, but when you look for it, it can often be found. Or, when all else fails ... look for corrosion as the culprit.
18. Corrosion problems are very frustrating. Take the example of the man running cast iron parts for air conditioning use in 15-minute cycles in a round vibrator with ceramic media. His parts were corroding after getting to his customer’s plant. To the rescue went a new high-powered inhibitor to be used at 3 to 4 ounces per gallon (23 - 31 ml./liter) of water as a post-dip. No help. Even at full strength. he got rust on his parts. He was cleaning his parts in the vibrator using a powdered cleaner. sprinkled over the mass at the beginning of the cycle. His “solution system” was metering in just plain water. So, by the end of the cycle. all the powdered compound had been washed out leaving only water on the parts. Then, even a super inhibitor could not stop the corrosion that had already started. Simple solution: meter a ferrous metals deburring compound into the water stream to give enough inhibition to prevent corrosion from starting. The post dip solution then worked perfectly at a mere 3 to 4 ounces per gallon (23 - 31 ml./liter).
Conclusion: If corrosion gets a chance to start, it will continue. For this reason, never let it get started.

Above: [Editor's note] A vibratory finishing time study. Isotropic surfaces are being developed on the parts (middle) and is further improved with a second step which is utilizing a different media and compound combination. Photo courtesy of Jim Riley, BV Products.
19. We firmly believe that stress induced in metal parts has, does and will cause corrosion of parts before, during and/or after mass finishing operations. A marvelous case history was to have been reported here, but the required proof was never obtained. Suffice it to say, all conventional means of solving this corrosion problem were to no avail. The presence of localized corrosion was noted where the parts had been most severely distorted during forming. And, stress is a viable means of causing corrosion when it can.
Conclusion (meager though it may be): Do not overlook stress as the cause of corrosion when all other avenues fail. it could be significant.
EQUIPMENT PROBLEMS
20. in the early days of vibratory finishing machines, one major manufacturer advertised his equipment as having a “high amplitude.” Amplitude is the displacement of a vibratory tub during the process. This resulted in the development oi the ‘Ampli-/-Chek;‘, Copyright 3M Co. This is a stick-on label with a series of circles of progressively larger sizes. Placed on a vibrating machine, either round bowl or tub type, a “cats-eye” is developed when the largest circles still overlap. Read toward the smaller circles until the circles just touch, like a figure “8”. The diameter of that circle is the amplitude of the machine.
Now to our story. Running a media test in a large plant had given results contrary to expectations. The salesman, prepared with several “Ampli-/-Chek”s put one on each test vibrator, then showed the plant manager that the test had been unfair; that the test machines were not at all equal in action. The plant manager finally knew why his two “identical” machines had never performed equally. One was running at a much higher amplitude than the other.
Conclusion: Equal machines or equivalent media or equivalent compounds are only that if they perform in exactly the same way in all respects. Make sure they do before assuming otherwise.
21. A little learning is a dangerous thing. We understand and appreciate that all too often. But it brings us to a visit to the West coast to start up a new vibratory machine and we couldn’t make it go. We had just written the first draft of an in-house guide on how to set the weights on round bowl machines, so we knew how to do it. We did not lack for confidence. In despair, we called the plant and asked for Herman, the man that set up the machine for test. He told us how to set it and, with our obviously superior knowledge, we told him why it wouldn’t work. He insisted. We tried it his way and it worked.
Conclusion: When all else fails. ask an expert. It makes sense to ask a lot earlier in most instances, but at least do it then. (This still hurts our pride a bit, but it has impressed us over the years.) And remember, a little learning is a dangerous thing . . . at times! (Thanks again, Herman.)
22. A similar thing happened in an equipment manufacturer’s plant. Late the night before a customer was to check out his new round vibrator, they could not make it run properly. With enough variables to fill the plant, they had been unsuccessful. Time to start all over. Check weight rotation. Don’t bother, it was already done. Check it anyway. Voila! It was running backward. It had been running in the right direction when the check-out man had found the oil lubrication pump running backwards. The electrician had been asked and he changed it. But, he changed the leads at the main panel, not at the oil pump. Result: The pump ran properly while the machine ran backward.
Conclusion: Even “experts” overlook the obvious at times. When big problems arise, stand back. Assume nothing. Start all over. Begin again with the basics.
23. When a client has trouble getting good results, he’ll often look at the “obvious" places for a quick answer. Often that is not where the answer lies. For example, one was having trouble getting top quality in his operations. Some parts were excellent and some were marginal at best. He was using 8 or 10 round vibratory machines varying in size from 1 cubic foot capacity up to about 25 cubic feet (28 to 700 Iiters). The obvious possibilities were checked. Speeds all okay. Amplitudes all about the same. Media and compound all identical. How about the metering pumps? Not one of them was delivering the correct amount of compound for the amount of water being used. And almost a third of them were delivering no compound at all. No wonder they had problems.
Conclusion: The compound metering system must work properly if excellent results are to be expected. It is just as important as weight adjustments and media and all of the other variables. It’s just not as easy to verify.
24. One of the biggest problems in mass finishing has been with the little bench-top vibratory finishing machines. These inexpensive machines are supposed to perform like their big brothers, but they can’t.
Why? ln order to make them cheap, many manufacturers take off things, such as adjustable weight systems, and seldom do they have good compound metering systems (especially since many of these systems would almost double the price of the machine.) They often have poor drains, so the dirty solution can’t get out or media clogs them.
Conclusion: You often get what you pay for. Buy a “cheapie” and that’s what you may get. Be sure the machine works as it should before getting the wrong one. Verify your process and get it guaranteed. Reputable manufacturers will do that gladly.

Above: [Editor's Note} A very wide variety of mass finishing media is available in a wide variety of shapes, composition, sizes and abrasive content. An equal number of liquid compounds are also marketed. Process development is a key function of many of the machine and material manufacturers in the deburring and mass finishing industry. This is an activity that is not recommended for either the inexperienced or the faint-hearted. The potential variables involved in developing a successful process can be daunting. Photo courtesy of Mike Klein, Iso-Finishing Inc.
PARTS PROBLEMS 25. Flexibility to help solve your own problems and to save your company some money is not always there. An example is a zinc die caster who was running a “family” die with six cavities making vent levers forThe customer’s evaluation was that some of the levers had not had enough of the flash line blended. It was then realized that the only rejected parts were from cavity number 6. All of the others were fine. This meant that the trim die was not getting close enough to the part for this one part. He would not change the trim die. claiming it was too expensive.automobiles. They were being buffed prior to electroplating with copper, nickel and chromium. Test parts were run in a vibrator with plastic media to develop a beautiful, low micro-inch, pre-plate finish.
Conclusion: To reap. you must sow. He who helps himself, really helps everyone. It’s almost impossible to save money without some investments on your part. Often the investment is more than just a financial one.
26. A plastics manufacturer on the other hand wanted to deflash compression molded appliance parts. A process was developed using a round vibratory machine with steel media. The customer evaluated samples and indicated that about 12 minutes was as long as he could run the parts. He sent in more parts to be run for 8. 10. 12 and 14 minutes. saying that if the flash wasn’t off in 12 minutes, he’d dress up the molding dies to reduce the flash so that it would come off.
Conclusion: Was this a change in an industry? Or was it the people that were different? Those who help themselves get the most out of all aspects of their suppliers and their technology.
27. Another example applies here as well. Two large vibrators with plastic media had been built for a manufacturer of plumbing components to put a pre-plate finish on brass shower ells. Process development went weil; produced excellent parts. Machines built and installed. Lousy results. And yet the original samples had plated beautifully. Everything this company manufactured was given a pre-plate finish by buffing. Everything they manufactured went through their plating line for a high-quality chrome plate. Every part of their plating line was under the control of a very young high school girl who counted drops to determine the quality of their several plating baths. Better quality baths, minor adjustments in bath content or type were to no avail. No changes would be made. None were made. The vibratory machines were returned to the equipment manufacturer, in spite of showing them the differences in electroplate thicknesses of the samples vs. the in-plant parts.
Conclusions: The plant manager suggested that the process had failed. It had not. It had succeeded in every way. But he had failed - failed to get a more economical manufacturing system in his plant (similar to the type being used by several of their competitors) and he had failed to have a good knowledge of electroplating, since it had so obviously changed. It’s true. He and his company are the ones that really lost the most.
Above: [Editor's Note] Shown in this slide presentation are parts that have been Isotropically Super-Finished in vibratory finishing equipment in a two-stage process that includes abrasive treatment followed up by a secondary treatment with non-abrasive burnishing media utilized with acidic compounds that wear away surface peaks. Very low micro-inch surfaces can be achieved with this type of processing. Photos courtesy of Jim Riley, BV Products
28. One of our favorite possessions is our new “grandfather’s” clock. It stands proudly in our front hall, chiming every 15 minutes. A beautiful sound. Several years after we owned this clock, the chime stopped. The salesman said the bearings were shot and needed to be re-built. Expensive and frustrating. After removing the top of the clock and its hands and face, it was noted that the chime, once started, worked fine. It just didn’t start as it should. Then, it was observed that two steel stampings were used to cause the chime to start. One lifted the other and, when the second was high enough, the chime started. The problem was that the lift was not high enough. The burrs on the stamping had worn down so that the effective thickness of the stampings were not as great, so the chime could not start. Some cellophane tape was put over the contact parts of both pieces and the chime worked once again.
The manufacturer of the clock was contacted with the suggestion (among other things) that it would make sense to ship a roll of tape with each clock. Somehow, no reply was received. That tape lasted almost a year and then wore out. It was replaced with pressure-sensitive label stock. The chimes have worked perfectly that way for almost 10 years since.
Conclusion: Don’t try to take advantage of burrs. They’re not sufficiently uniform to use in any way. Remove them and have the part(s) designed so that they work properly when burr-free. lt will do a lot for customer satisfaction. too.
29. A major manufacturer of computer equipment was to check out a very large tub-type vibratory machine with plastic media and were bringing their flatness gauges with them. It was to deburr large, machined aluminum castings. The flatness of something Iike 15 thousandths (.4 mm.) had to be held over the 24 by 30” (60 x 75 cm.) machined surfaces. Parts were checked going in. 8 to 12 thousandths (.2 - .3 mm.) used up. They were then checked after processing. Down to 4 to 6 thousandths (.l - .15 mm.) The process had made the parts flatter, evidently taking off the high spots.
Conclusion: It’s a fine process. Believe it.
PEOPLE PROBLEMS
30. Some people get just too dam greedy. A good example is in the case of chain - the kind used for children’s swings, etc. it’s made of steel wire precoated with zinc. After cutting and forming into chain links. the zinc coating must be burnished and the cut ends must be deburred. The chain had been run in big rotary barrels with two men on each of two shifts using powdered compounds. The city was getting after them for dumping all that stuff into their sewer. A vibratory system with steel media and a mildly acidic compound was introduced and paid for itself very quickly. No more city problems, better product quality, greatly reduced labor and compound costs. A super conclusion, you’d think. But herein steps greed.
Brand “X” again. Another “super” compound at a (slightly) lower cost. Converted immediately. About 5 or 6 months later, a frantic phone call for help: they had 17 railroad ears full of chain that had all turned white. When zinc corrodes, zinc oxide, a white powder, is formed. The chain was corroding. Brand “X” had found a way to make a cheaper compound - they left the zinc inhibitor system out of it.
Conclusion: Look long and hard before you leap. This example, while dramatic, shows how costly such changes can be. All the money saved by the new process, and then some, went up in smoke so they could save a few pennies more. Don’t let excessive greed spoil your systems.
[Editor's Note] Above: Although vibratory finishing remains the predominant mass deburring and finishing method utilized by industry, in recent years centrifugal barrel finishing (aka Centrifugal Iso-Finishing) has been finding its way into an increasing number of deburring and surface finishing applications.
(1) Deburring - as the method can make use of much smaller dimensioned media, it is capable of processing parts with more intricate geometries. Any machining operation that already make use of vibratory finishing methods and still is left with substantial amounts of hand-deburring should explore this method as a way of obtaining relief from the hand-deburring.
(2) Super-finishing and Polishing. As a high-intensity and high-speed method, Centrifugal Iso-Finishing is capable of producing highly polished surface finishes rapidly and is widely utilized in the jewelry, dental and medical industries as a result. These jewelry like finishes have been utulized within the aerospace and automotive industries to develop very useful functional surfaces on a growing variety of parts.
31. In an automotive plant they had lost the second load of steel media due to excessive corrosion. It seems the operator felt that excessive foam was being developed in the machine, so he used a fire hose on it to flush out the foam. Technical personnel were not allowed to talk to him about changing his ways. It would be a waste of time. The two machines were scrapped by the company and their value was never realized because the operator couldn’t be changed.
Conclusion: The company allowed that to happen. It must eventually pay an awesome price for it in the marketplace (and it is.) Needless to say, the use or recommendation of that company’s products cannot be justified. Remember that suppliers can sometimes be the most enthusiastic supporters of their customer’s products. Unfortunately, this works two ways.
[Editor's Note] Above: This slide show presentation displays a cross section of parts and components that have been processed with Centrifugal Barrel Finishing (or Centrifugal Iso-Finishing)
32. An automotive die casting was to be deburred. A special size of case hardened, steel media was developed and about 40 cubic foot (1100 liters) of it was made up for the job. The machines were built and then came the run-off test before shipment. The customer had sent in several tote containers of parts. After processing, every part had three pieces of media lodged in it. After a flourish of nasty, the truth came out: The customer’s design team had changed the ID of the part a few thousandths of an inch and had not bothered to tell the engineer about it. The media was reprocessed to a slightly smaller size and worked fine.
Conclusion: When a part changes, no matter how slightly, the original process will not work as well or at all. In your operations, let the right hand know what the left hand is doing. Keep everyone informed about changes made to them during all phases of manufacture.
33. Run off a new machine to deburr and clean steel stampings with a threaded center hole, in steel media, in a vibrator. Easy job. Customer shipped in parts from his outside supplier for verification before shipment. Parts run and customer checked hole with a thread gauge. About one-fourth of the parts failed. More parts were run; more parts rejected. Finally, the customer checked parts going into the vibrator and only put in just those parts that passed the thread gauge test. All of those came out perfectly, passing all tests with ease.
Conclusions: 1. The test for this new equipment explained to the customer why he was having problems meeting his customer’s specs. Parts, as received from his outside vendor, were not good enough. He ultimately moved the stamping and threading operations in-house and got 100% satisfaction. 2. Before making judgments about a process, be sure your own work is up to snuff.
34. Soon after the concept of machine capacity calculation was first published a new round bowl vibrator was checked out in the user’s plant. He was about to charge it with media from a competitor’s machine sitting beside it. When asked if the published formulae in the article could be checked out, he agreed. The new “model 20” machine computed to 20.1 cubic feet in “working capacity” while the competitor’s “model 20” machine computed to only 13.4 cubic feet and was more expensive.
Conclusion: “Caveat emptor” - Let the buyer beware. Look before you buy. Some published data in this industry are not as accurate as it could be. The entire “working capacity” concept and the calculations for it should be used to check these data. Two tools are available for doing it yourself. One is a published Technical Paper. ” and the other a computer program that makes these and many other mass finishing computations, estimations and conversions much easier.

[Editor's Note] This photo shows the action of a centrifugal disc finishing machine, which like vibratory machines are "open" systems (in contrast to closed systems such as rotary and centrifugal barrel machines) process cycle times are abbreviated because of the aggressive media action of the machine. One application limitation would be in the processing of "long" parts, which is a difficult application for disk systems. Many of John Kittredge's comments might also have application to centrifugal disk finishing systems. Photo courtesy of Jim Riley, BV Products.
35. Some problems are downright serious. This was the case with a good customer who was setting up a duplicate system for cleaning and deburring his stamped steel parts in a second plant. The parts came down a sequential stamping operation where 10 gauge steel was stamped to shape, a center flange pushed up and threaded with a class A automotive thread. Covered and dripping with stamping and threading oils, the parts went to the vibrator. A seven to ten-minute cycle. Beautiful results. Only one problem. In the second plant, nothing worked. Identical machine, identical media, identical compound, essentially identical water and the same engineer. The air got a bit blue. It had just been determined that the only way to find the problem was to take several hundred parts from this plant down to the other plant and run them and also to bring several hundred parts from that plant up to this one to run them. Just then, above the engineer's office partition, a head appeared. A coworker asked if it would make any difference that one plant was using cold rolled steel ad the other plant was using hot rolled. It did. Conclusions: (1.) Confidence in the process allowed the conclusion that something other than the mass finishing system was the problem. Eventually, the work outlined would have led to the same findings. but not before spending a lot of extra time and money getting at the answer.
(2.) Be sure of your facts - all of them - before getting in too deep. When sure of the process, confidence follows.
36. Finally. a very sad, but true tale. One that is all too prevalent in our business world. One that we must get rid of soon. It concerns a media manufacturer who was recently bemoaning the fact that they had tried for years to sell media to a customer, only to be rejected on price. They were always 1 or 2 cents a pound more expensive. Then this customer called them with a problem their existing media supplier had not been able to solve.
He solved the problem - developing a new process based on different media. He got one load of media and then lost it again to the original supplier for 1 or 2 cents per pound. The buyer believes that process development is a free, no-cost undertaking. He believes that he should not have to pay for it - that it is obviously a burden placed only on others. But where will he go the next time he has a problem? He already knows his existing supplier is not too swift. Will he continue to “save money” this way?
Conclusion: A fellow by the name of Dr. W. Edwards Deming who, after WW II almost single-handedly got the Japanese to manufacture quality and therefore become awesome competitors, states in part,that buying from the lowest cost supplier isn't always the way to improve quality and, hence. overall costs and profits. He suggests, rather, that you should develop your suppliers so that they give both excellent products as well as excellent service, if and when needed. This, he claims, is the way to make money in the long run. His record of success leaves no room for argument with this or any other of his concepts.
SUMMARY AND CONCLUSIONS
Problems can become challenges, rather than just a lot of agony and turmoil. Challenges can make the solutions to problems beneficial, rather than stop-gaps which just let us get through another day.
This paper has dealt with some of the problems that have occurred in the field of mass finishing and has shown the effect they have had. Some of these will seem humorous by today’s standards while others are much more serious. Many of these “formative failures” have taught beneficial lessons - lessons about the mass finishing process and industry, about people, and about ourselves. If we failed to carry them with us and to learn from them, we would have failed ourselves. If we failed to pass them on, we might have escaped more easily, but the help they might be to others would have been lost. Many of them form the basis of an excellent learning process.
As we approach retirement age, one of our most satisfying endeavors has been to teach the fundamentals of mass finishing to interested users and purveyors of these systems. It is satisfying because of the value attendees place on these sessions and to be able to instill some sense of purpose and understanding to it all. It is also frustrating because so few plant engineers and other responsible people have any concept of deburring and/or surface conditioning. Why? Because we don’t teach it in our schools in spite of our protestations. This is the most awesome people problem we face today. Let’s fix it!
REFERENCES
1. “The Testing of Vibratory Finishing Media”, John B. Kittredge, SME Technical Paper MR77-466.
2. “Vibratory Cleaning, Deburring & Surface Conditioning with Steel Media”, John B. Kittredge, SME Technical Paper MR79-748. 3. “Media Selection Guide”, SME Tool and Manufacturers Handbook 1984.
4. “Vibratory Finishing Equipment”, lohn B. Kittredge, SME Technical Paper MR89-149.
5. “Selection of Mass Finishing Equipment”. John B. Kittredge, SME Technical Paper MR87-153.
6. “The Vibratory Finishing Compound Solution System”, John B. Kittredge, SME Technical Paper MR82-239.
7. “Mechanism of Compounds in Mass Finishing - An Update”, Patrick C. Ramnarine, SME Technical Paper
MR87-151.
8. “Mass Finishing Compound Technology”, Patrick C. Ramnarine, SME Technical Paper MR89-111.
9. “Understanding Vibratory Finishing” by John B. Kittredge, PRODUCTS FINISHING magazine reprint, 1981
10. “Attacking the Astronomical Odds in Mass Finishing”, John B. Kittredge, SME Technical Paper MR83-675.
11. “How to Calculate the Number of Parts in a Vibratory Finishing Machine” by John B. Kittredge, INDUSTRIAl. FINISHING, August 1987, page 31.
12. “The Mathematics of Mass Finishing” by John B. Kittredge, SME Technical Paper MR81-399.
13. “MFcCALC”, version 3.0, a Mass Finishing computer CALCulations, estimations and conversions program, by John B. Kittredge Consultant.
14. “Ed Deming wants big changes, and he wants them fast”, by Lloyd Dobyns, Smithsonian, August 1990, pages 74-82.
15. “An Open Letter to our Colleges, Universities, John B. Kittredge, PRODUCTS FINISHING, October 1990,
page
For additional information, or help with arranging for (free) sample processing of your parts Contact Dave Davidson at ddavidson@debrring-tech-group.com...

Comments