37 things you can do with Mass Media Finishing (Centrifugal Barrel or Vibratory Finishing) Equipment
- Dave Davidson
- May 29, 2014
- 5 min read
Updated: Mar 16, 2021
Dave Davidson | Deburring Technologist | ddavidson@deburring-tech-group.com | dryfinish.wordpress.com


The applications list shown below was compiled by a major OEM (Original Equipment Manufacturer) of finishing equipment. As you can see by examining some of the commercial applications listed, a lot more goes on here than just simple deburring. These applications say as much about the ingenuity of the people who developed them as it does about the versatility of the processes themselves.
1. Deburring and radiusing of machined steel components.
2. Deflashing zinc, aluminum or magnesium die castings.
3. Deburring and edge-contour of powdered (sintered) metal parts
4. Deburring of any punched, sheared, or formed (bent) metal

5. Washing oil off of screw machine parts. or dry processing of screw machine parts for oil absorption, smoothing and polishing especially in high-pressure centrifugal machines (to reduce or eliminate effluent from conventional aqueous finishing)
6. Deflashing plastic parts, also radiusing abrasively or producing dry process polishing effects.

7. Pre-plate finishing items such as golf clubs, hand tools, small components, costume jewelry and many other items.
8. Improving surface finish on 3 ft. (900mm) – 4 ft. ( 1200mm) cermatel coated jet-engine stators from 55 micro-inch Ra to 19 micro-inch Ra

9. Improving surface finish on turbine blades and vane clusters. In sequential multiple processing as low as 5 micro-inch Ra
10. Improving surface finish and polishing of surgical instruments and biomedical implants and devices.
11. Polishing brass and copper torch tip components for plasma M.I.B. welding torches.
12. Cleaning/degreasing automotive used alternator and starter housings.
13. Cleaning/degreasing brass power line clamps and aluminum cable terminals.
14. Prepaint finish on plastic telephones.
15. Burnishing (polishing) of pewterware and pewter figurines, jewelry etc.
16. Two-step deburring and cob drying and polishing of kitchen cutlery, pruning shears, industrial/commercial scissors and putty knife blades.
17. Deburring and weld discoloration blending on components used in the manufacture of exercise machines, stair climbers, etc.
18. Degreasing of jumbo jet landing gear (entire brake housing, torque tube case and stator plates)
19. Improve surface finish to under 10 micro-inch Ra on titanium, brass and stainless ball valves from 3 inches (75mm) to 2 feet (600mm in diameter
20. Deburring sintered metal clutch plates, gears and hubs for automotive engines.
21 Degreasing fasteners (nuts, bolts, etc) used in the assembly of aircraft brakes.
22. Deburring saw cut endmill blanks prior to fluting and sharpening
23. Coloring pure sterling silver grain to casting grade in a part-on-part (no media with special compound)

Vibratory Bowl machine showing finishing action. Photo courtesy of Mark Riley, BV Products
24. Deburring and blending clear plastic kidney dialysis pump bodies.
25. Smooth and burnish brass, bronze and stainless steel boat propellers (replacing most hand grinding and buffing operations)
26. Deburr and dry stainless steel cooking stove coil supports
27. Deburr and smooth machined cast iron manifolds for C.A.T. tractors.
28. Descale screwdriver blades, worm gears and other parts with heat treat scale
29. Separating floor tile that sticks together, and scrub firing sand from surfaces utilizing a vibratory finishing operation with dry performed media.
30. Burnishing zinc belt buckles.

Centrifugal disc for rapid small part finishing showing the toroidal movement of media in work-chamber
32. Separating unwanted scrap “knockouts” from fine blanked parts utilizing a vibratory screen separator
33. Burnishing 303 stainless steel food service stainless steel food service ketchup pump cylinders using 5/16 x 3/4 inch angle cut cylinder media in a vibratory process
34. Pre-paint finish of golf balls us using a large and small media combination in a vibratory process. Larger media drives smaller media points into dimpled areas of the part. The method left a much smoother and uniform surface finish than the blasting method which had been utilized previously.
35. Deburr and finish surgical needles 2″ (50mm) to 18″ (450mm) in length utilizing a non-abrasive media in a vibratory finishing machine.
36. Multiple function vibratory processes (burnish, degrease, chip removal, and deburring) of brass locking cylinders that are internal parts for keyed locks. Two vibratory machines with PLC controls were utilized to adjust the wash, rinse, drain and shake out cycles which vary from 30 seconds to an hour or more. Process is a part-on-part method with alkaline cleaning liquids
37. Deflashing of plastic circuit breaker components. The process used steel media in a continuous flow-through vibratory finishing machine, and able to process 3000 parts per hour o a continuous basis.
This slideshow requires JavaScript.
Centrifugal Iso-Finishing Technology
Centrifugal barrel finishing (CBF) is a high-energy finishing method, which has come into widespread acceptance in recent years. Although not nearly as universal in application as vibratory finishing, a long list of important CBF applications have been developed in the last few decades.
Similar in some respects to barrel finishing, in that a drum-type container is partially filled with media and set in motion to create a sliding action of the contents, CBF is different from other finishing methods in some significant ways. Among these are the high pressures developed in terms of media contact with parts, the unique sliding action induced by rotational and centrifugal forces, and accelerated abrading or finishing action. As is true with other high energy processes, because time cycles are much abbreviated, surface finishes can be developed in minutes, which might tie up conventional equipment for many hours.
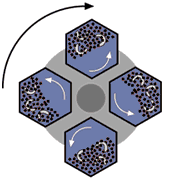
Centrifugal Barrel Finishing principles – high-intensity finishing is performed with barrels mounted on the periphery of a turret. The turret rotates providing the bulk of the centrifugal action, the barrels counter-rotate to provide the sliding abrasive action on parts.
The principle behind CBF is relatively straightforward. Opposing barrels or drums are positioned circumferentially on a turret. (Most systems have either two or four barrels mounted on the turret; some manufacturers favor a vertical and others a horizontal orientation for the turret.) As the turret rotates at high speed, the barrels are counter-rotated, creating very high G-forces or pressures, as well as considerable media sliding action within the drums. Pressures as high as 50 Gs have been claimed for some equipment. The more standard equipment types range in size from 1 ft3 (30 L) to 10 ft3, although much larger equipment has been built for some applications.
Media used in these types of processes tend to be a great deal smaller than the common sizes chosen for the barrel and vibratory processes. The smaller media, in such a high-pressure environment, are capable of performing much more work than would be the case in lower energy equipment. They also enhance access to all areas of the part and contribute to the ability of the equipment to develop very fine finishes. In addition to the ability to produce meaningful surface finish effects rapidly, and to produce fine finishes, CBF has the ability to impart compressive stress into critical parts that require extended metal fatigue resistance. Small and more delicate parts can also be processed with confidence, as the unique sliding action of the process seems to hold parts in position relative to each other, and there is generally little difficulty experienced with part impingement. Dry process media can be used in certain types of equipment and is used for light deburring, polishing, and producing very refined isotropic super-finishes.
For more information or help with making arrangements for the sample part finishing of your parts CONTACT: Dave Davidson, Deburring/Finishing Technologist | 509.563.9859 | dryfinish.wordpress.com ddavidson@deburring-tech-group.com | https://about.me/dave.davidson

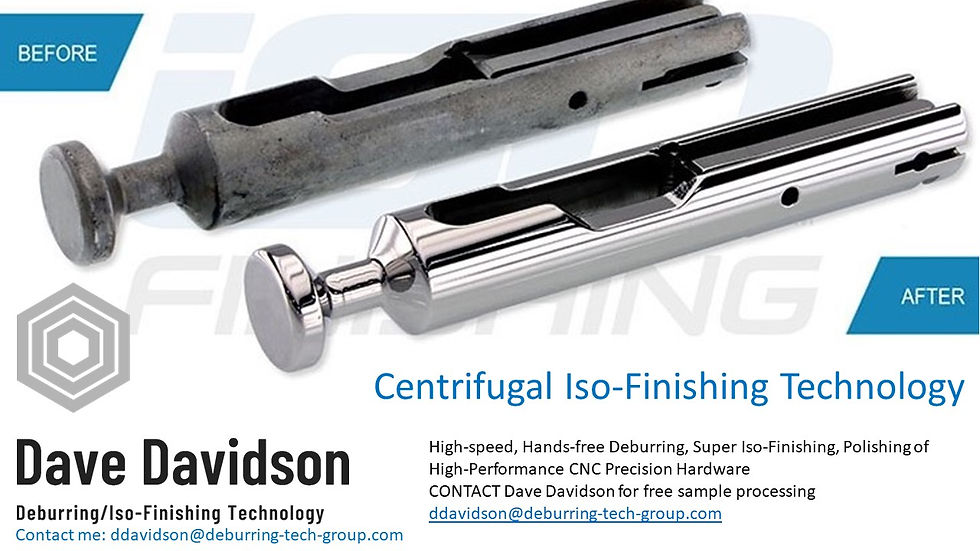

Comments