Automated Edge and Surface Finishing of Orthodontic Clear Aligners with Centrifugal Iso-Finishing.
- Dave Davidson
- Aug 21, 2020
- 5 min read
Updated: Sep 12, 2021
Contributing editor. Contact me for technical assistance and sample part finishing.
Dave Davidson | Deburring/Finishing Technologist | Deburring/Finishing Tech Group ddavidson@deburring-tech-group.com | dryfinish.wixsite.com/iso-finish

Edge and surface finish automation with Centrifugal Iso-Finishing Technology.

Centrifugal Iso-Finishing is used widely throughout the dental, medical and jewelry industry for the deburring, surface finishing and polishing of parts and components. One dental/orthodontic part application that is seeing increasing utilization of the technology in recent years is the automated edge and surface finishing of clear plastic aligners. Previously after the edges of the product had been trimmed, the edges would have to be deburred with hand tools in a time consuming and tedious manual operation. Centrifugal Iso-Finishing is now being used to automate this manual finishing operation. See the example below:
Demonstration video shows the Centrifugal Iso-Finishing process used for edge and surface finishing of orthodontic clear plastic aligners.
Larger production volumes can be processed with the larger model HZ-85 which has more automated material handling features built in.
Above: Other Model HZ-85 features are discussed in this demonstration video
Below: Many other products in the dental industry are also finished and polished with Centrifugal Iso-Finishing Equipment. Some further equipment information is shown below:

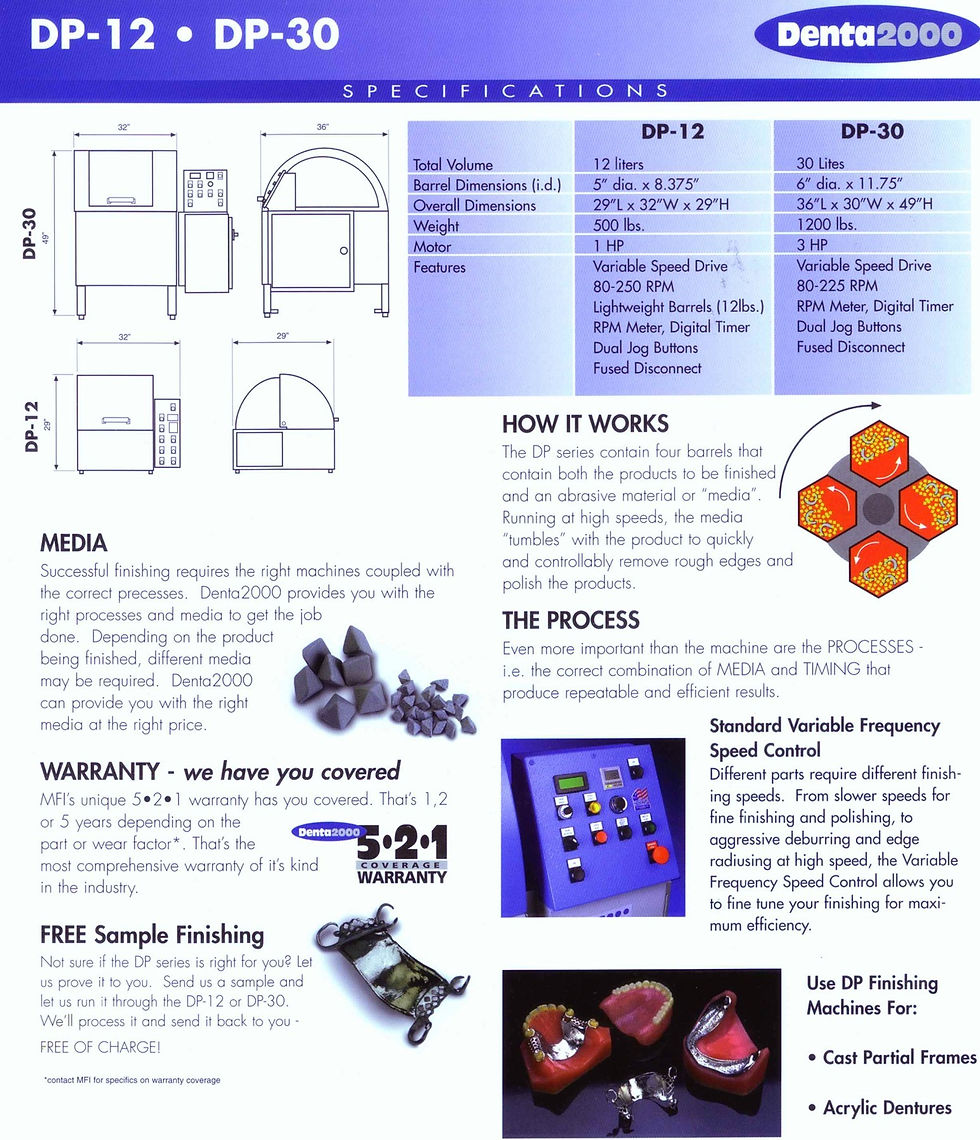

Contact us for (free) sample part finishing | equipment | contract finishing | technical assistance.

Centrifugal Isotropic Finishing (CIF) is a high-energy finishing method, which has come into widespread acceptance in the last few years. Although not nearly as universal in application as vibratory finishing, a long list of important CBF applications have been developed in the last few decades.
Similar in some respects to barrel finishing, in that a drum-type container is partially filled with media and set in motion to create a sliding action of the contents, CBF is different from other finishing methods in some significant ways. Among these are the high pressures developed in terms of media contact with parts, the unique sliding action induced by rotational and centrifugal forces, and accelerated abrading or finishing action. As is true with other high energy processes, because time cycles are much abbreviated, surface finishes can be developed in minutes, which might tie up conventional equipment for many hours.
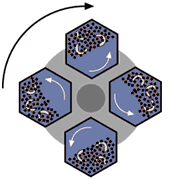
Centrifugal Barrel Finishing principles – high-intensity finishing is performed with barrels mounted on the periphery of a turret. The turret rotates providing the bulk of the centrifugal action, the barrels counter-rotate to provide the sliding abrasive action on parts.
The principle behind CBF is relatively straightforward. Opposing barrels or drums are positioned circumferentially on a turret. (Most systems have either two or four barrels mounted on the turret; some manufacturers favor a vertical and others a horizontal orientation for the turret.) As the turret rotates at high speed, the barrels are counter-rotated, creating very high G-forces or pressures, as well as considerable media sliding action within the drums. Pressures as high as 50 Gs have been claimed for some equipment. The more standard equipment types range in size from 1 ft3 (30 L) to 10 ft3, although much larger equipment has been built for some applications.
High-speed and hands-free Centrifugal Iso-Finishing can deburr, finish and polish all types of small manufactured parts much faster and efficiently than conventional vibratory and rotary barrel finishing
Media used in these types of processes tend to be a great deal smaller than the common sizes chosen for the barrel and vibratory processes. The smaller media, in such a high-pressure environment, are capable of performing much more work than would be the case in lower energy equipment. They also enhance access to all areas of the part and contribute to the ability of the equipment to develop very fine finishes. In addition to the ability to produce meaningful surface finish effects rapidly, and to produce fine finishes, CBF has the ability to impart compressive stress into critical parts that require extended metal fatigue resistance. Small and more delicate parts can also be processed with confidence, as the unique sliding action of the process seems to hold parts in position relative to each other, and there is generally little difficulty experienced with part impingement. Dry process media can be used in certain types of equipment and is useful for light deburring, polishing, and producing very refined isotropic super-finishes.
Below are some process video footage demonstrations of high-speed centrifugal isotropic finishing. These automated edge and surface finishing methods are capable of producing very refined low micro-inch surfaces that can improve functional part performance and service life.
SEE below: Background information and overview on dental aligners.
ABSTRACT: The first part of this discussion, excerpted from Wikipeida, gives a technical overview of aligners and their use as a treatment in the dental and orthodontic fields for correcting various forms of tooth misalignment. The second part will show how centrifugal iso-finishing technology is being used by many manufacturers of these orthodontic items to automate the edge-finishing and surface polishing and replace the substantial amount of hand-work that was previously necessary. Prior to the implementation of centrifugal iso-finishing these items were being edge finished entirely with hand-tools.
What are dental and orthodontic aligners and how are they used? Treatment begins with taking x-ray and photographs for diagnostic purposes, followed by capturing the patient's bite, teeth, and gums via a bite registration and polyvinyl siloxane impressions or an intra-oral digital scanner. The latter method has greatly increased in popularity in recent years as digital scanning technology has improved. The dentist/orthodontist completes a written evaluation that includes diagnosis and treatment plan. Dental impressions are scanned in order to create a digital 3D representation of the teeth. Technicians move the teeth to the desired location with the program Treat, which creates the stages between the current and desired teeth positions. Anywhere from six to forty-eight aligners may be needed. Each aligner moves teeth .25 to .33 millimeters.
A computer graphic representation of the projected teeth movements, created in the software program ClinCheck, is provided to the doctor and patient for approval or modification before aligners are manufactured. The aligners are modeled using CAD-CAM (computer-aided-design and computer-aided-manufacturing) software and manufactured using a rapid prototyping technique called stereolithography.

The molds for the aligners are built in layers using a photo-sensitive liquid resin that cures into a hard plastic when exposed to a laser. The aligners are made from an elastic thermoplastic material that applies pressure to the teeth to move into the aligner's position. Patients that need a tooth rotated or pulled down may have a small, tooth-colored composite attachment bonded onto certain teeth. Since the form-fitted plastic used in clear aligners is not as rigid as the metal used in traditional braces, sometimes the flexibility in the materials need to be compensated in the areas that require movement. Alternatively, attachments may be used to facilitate movement by changing the shape of the tooth. More attachments can make the aligners less aesthetically pleasing. Reproximation, (also called interproximal reduction or IPR and colloquially, filing or drilling), is sometimes used at the contacts between teeth to allow for a better fit.
Each aligner is intended to be worn an optimal 22 hours a day for one to two weeks. On average the treatment process takes 13.5 months, although treatment time varies based on the complexity of the planned teeth movements. The aligner is removed for brushing, flossing and eating. As clear aligners are made from plastic, they can be warped by hot liquids. While undergoing treatment you should limit your intake of hot liquids to protect the shape of your aligners and stop them from becoming stained. Once the treatment period has concluded, the patient is advised to continue wearing a retainer at night for the foreseeable future.
Below: Fine finishes can be developed for a wide variety of parts from all industries....
Comments