Barrel Finishing: Fundamental Fill Level Pointers
- Dave Davidson
- Feb 26, 2011
- 8 min read
For more information contact: Dave Davidson | dryfinish@gmail.com | 509.230.6821 Deburring/Finishing Technologist | SME Technical Community Advisor Free sample finishing |Tech support |Contract finishing | Equipment | https://about.me/dave.davidson | https://dryfinish.wordpress.com https://partsfinished.wordpress.com

Correct fill level loading is one of the fundamental operating parameters. The ideal fill level is approximately 50 percent this permits for the longest possible slide zone. Most abrading or polishing o parts occurs within the top 10 -20% of the media load, and maximizing the length of the slide zone is key to shorter cycle times
Examples of tumbling equipment is shown below.

Rotary Tumbling Barrel (trunnion drive style) of European Manufacture) This type of equipment is usually rubber or polyurethane lined to facilitate the use of ceramic and plastic media for abrasive smoothing and deburring operations. These media would be used with aqueous compounds that suspend abrasive and metallic coils and prevent redeposition into part surfaces

30 x 36 in. octagonal horizontal barrel for dry process finishing plastics and light metals. This type of equipment is used widely for polishing plastic materials such as acetate and acrylic to high gloss finishes. They can also be used to polish and brighten a variety of metal parts, but particularly softer non-ferrous metals. Used in the jewelry, dental and small par industries.
Shown above is an example of an octagonal horizontal rotary barrel. This style of equipment has been in use in North America and Europe since the early part of the twentieth century for bulk-processing large numbers of metal parts that required deburring, edge-break, radiusing, smoothing, burnishing and polishing. This style of equipment was widely used for abrasive finishing metals in various abrasive media along with water and compounds. Dry processing with finer polishing abrasives and natural materials were used to produce fine finishes on plastics and many non-ferrous metals with surfaces that rivaled that of traditional buffing and polishing operations. This kind of finishing is still commonplace in some industries that require high-quality decorative finishes in both North America and throughout Europe.
Tumbling barrels are available in a variety of configurations, the most common being a horizontally oriented octagonal chamber, which provides a much more efficient media lift than a purely cylindrical shape. Other configurations include barrel chambers mounted on pedestals, barrels with front or end loading, perforated barrels encased in a water tank or tub, and so called triple-action polygonal barrels. Also used extensively are oblique barrels, similar in some respects to small batch concrete mixers. This equipment is used for light deburring and finishing as well as part drying. It has the advantage of permitting operator inspection while in process, and its open end can be tilted down for ease of unloading, but it is much less efficient than horizontal equipment, and suffers from the tendency of parts and media to segregate in extended time cycles.
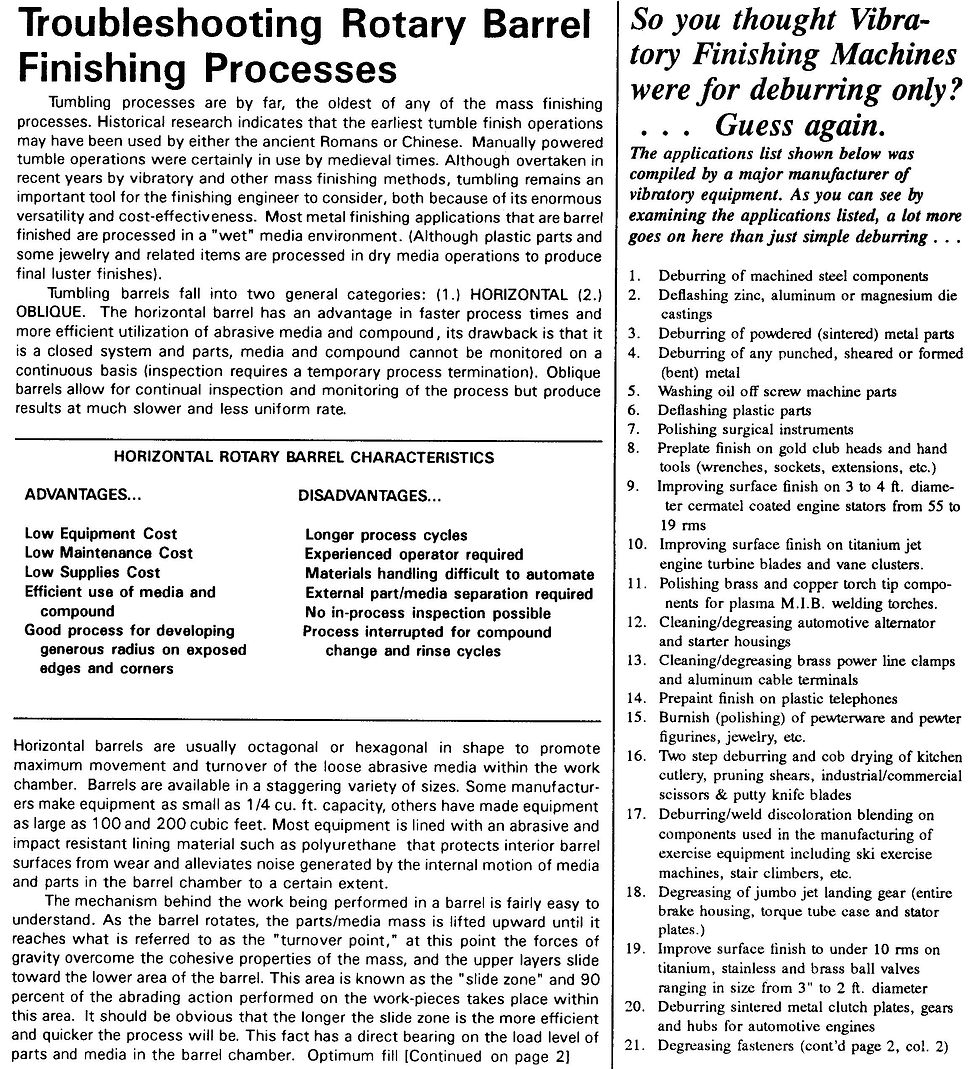
As is the case with most other mass finishing equipment, polyurethane, rubber, or linings made from similar material are used to extend equipment life, provide some measure of cushioning to parts, and furnish some measure of noise abatement. Although considered by some to be an outdated and obsolete finishing method, barrels still have a place in the finishing engineer’s repertoire. Although it is true that it is slower and presents some automation and materials handling challenges, it is sufficiently versatile to perform numerous finishing operations for many manufacturers. Furthermore, barrel finishing provides an excellent alternative for flat parts, which may nest in vibratory systems. Although perhaps requiring some measure of operator experience in order to be used effectively, barrel finishing is capable of producing some unique and desirable surface finishes and is highly efficient in compound and media usage.

Also: some notes excepted from the MFSA Quality Finishing guide (No .7 – Mass Finishing) Mass finishing systems are used for processing castings, forgings. stamped and machined parts made from metal or from plastics, ceramics, wood, molded rubber, fiberglass, or any other material that can be stamped, forged, cast, extruded or machined. The variety of parts that can be finished has few limits. Uniform finishes can be produced on parts in large quantities economically. Bright reflective surfaces can be achieved. Operations that can be performed by mass finishing include fine finishing with low microinch values, remoiing burrs and rough location points, preparing parts for welding and spot welding, forming radii, cleaning, descaling, deflashing, deburring, corner rounding or chamfering, closing pores in castings, removing flux, relieving highlights in antique finishing, blending machine marks, improving threads, preparing part surfaces for painting and plating, changing stresses in metal parts, blending castings for uniform appearance, improving surfaces for oil retention, removing rust and/ or inhibiting corrosion, polishing after plating, drying, providing low-reflection surfaces, prolonging the life of dies, and preparing parts for automatic threading, assembly and extrusion. Stock removal or dimensional change during mass finishing is predictable, and can be controlled within predetermined limits. Even threaded parts made of steel, aluminum or brass can be processed, and at the same time held within dimensional tolerance. Mass finishing operations may be interwoven with other steps in the manufacturing process, including material removal, heat treating, descaling, grinding and/or other deburring, surface conditioning, finishing processes. To achieve a smooth flow of parts from one department to another, the mass finishing department may be located as near the previous machining, stamping,heat treating operations, as possible so that little time is lost in parts transfer. After stamping,forging,machining, grinding and other operations, many parts can be mass finished to achieve desired surface improvement and/or prepared for electroplating, painting, other finishing processes, assembly or shipping. A part to be blanked and then formed may be mass finished after blanking to remove burrs prior to forming. If a part is to be heat treated, it is sometimes desirable to accomplish deburring and surface finishing prior to heat treatment. In other cases burrs may be more readily removed after heat treating, and surface finishing may be accomplished along with descaling. Scale removal prior to grinding may increase grinding wheel life 50 percent, and diamond life 25 percent, while increasing production 25-30 percent because wheels need not be dressed so frequently. Mass finishing is not, and can not be expected to be, a means of correcting mistakes made in the fabrication of parts or components. Therefore, adequate quality control of parts routed from fabrication to finishing is essential. Components to be processed to a predetermined level of surface finish quality must be delivered to the finishing machine at a uniform, consistent quality level. Parts must exhibit the specified physical properties, dimensions, also have clean surfaces. If fabrication quality is permitted to vary, the finishing machines will not be able to achieve the surface quality level desired in the specified time, if at all. Poor quality parts require more finishing time, whether the part is a die casting loaded with defects, or a stamping formed on a dull die. The finishing cycle can serve as a check on quality of fabricated parts. If the time required for mass finishing to specifications increases, parts may not be leaving the fabrication process at the correct quality level. By keeping fabricating tools clean and sharp, better parts with smaller burrs, smoother surfaces, less surface soil are produced. Shorter finishing cycles, lower costs, increased machine through-put result. Rotation of a barrel loaded with parts and media carries the mass continually upward to the turnover point. At this point the force of gravity overcomes the tendency of the mass to stick together, and the upper layers slide, rather than fall, toward the lower area of the barrel. Work is done on parts by this differential sliding action. The area in which the mass slides is called the effective slide area. Although some abrading action occurs as the workload turns over, about 90 percent of the deburring and surface improvement is accomplished during the slide. Maximum abrading action is obtained when the slide is longest. This occurs when the barrel is loaded to 50 to 60 percent of capacity. Higher load levels (to 80 percent) are desirable for some work-pieces, such as large or heavy components. Increasing the load level decreases the length of slide, thus reducing probability of work pieces contacting each other, and reducing contact force. Barrel rotation speeds may range from 50 to 250 sfpm (0.25to 1.25 smps) depending on type and shape of part being processed and type and/or quality of finish desired. For gentle finishing of delicate parts, a speed of 50 sfpm (0.25 smps) is satisfactory. For maximum abrasive action a speed of 250 sfpm (1.25 smps) can be used. Speeds of 100 to 200 sfpm (0.5 to 1 smps) for cutdown, and 50 to 100 sfpm (0.25 to 0.5 smps) for burnishing are recommended. Slower speeds are suggested for heavy or delicate parts. Excessive rotational speed increases the height of the turnover point until media and parts fall or “cascade” with little or no sliding action. This reduces the efficiency of the process, can cause part damage by part-on-part impingement. The load ratio of media to parts in rotary barrels varies with the type of part in process. Generally, three parts media to one of parts (by volume) can be used. For most delicate parts a load ratio of 7 to I may be used. For delicate aluminum parts a ratio of 12 to 1 is suggested. Water is added to about 1 inch below the load level for cutting, and tojust cover the load of media and parts for burnishing. An appropriate compound is always added. Most parts can be processed in the mass of media in rotary barrels. However, in some cases fixtures are used to prevent part-on-part impingement, bending or interlocking of complicated or delicate parts. Fixtures also protect heavy parts from impact damage. Some fixtures may be mounted on the doors of the barrel. Fixtures may be used to mask and protect certain part areas. Also, fixtures tend to cause one area of a part to receive more abrading action than another; hence, it may be necessary to reverse barrel rotation for half the cycle to improve finish uniformity. Submerged barrel finishing (tubbing) is done in a perforated barrel loaded with work-pieces and media, rotated in a tank containing a water solution of compound. The process is used for certain types of jewelry finishing and for chemical cleaning of parts. The system permits fines, metal slivers and contaminants to pass through the barrel perforations and settle out in the tank. Sometimes the method is automated so that the barrel is moved from station to station (different tanks and/or solutions), submerged and rotated at each station of the installation. Variations in rotary barrel equipment include the open-end tilting type, bottle-necked tilting-type, horizontal-octagonal (conventional), horizontal-polygonal, -multiple-drum, compartmentalized (common),end-loading, submerged.The open-end tilting barrel and the bottle necked tilting barrel are used for finishing and drying parts, for ball burnishing and self tumbling. Parts run in this barrel can be inspected during the cycle, water and compound can be added. Barrel can be tilted to discharge the load. The horizontal barrel (in all its design variations) can process batch after batch of parts uniformly if the media, water, cycle time, and compounds are controlled within specified limits. The rotary barrel is an outstanding tool for generation of radii on stampings, but is less effective in finishing part cavities or recesses. Flat parts requiring a heavy radius on all edges can be processed more efficiently in rotary barrels; barrels have the ability to do a considerable amount of work on part edges because of the differential slide which occurs during rotation.
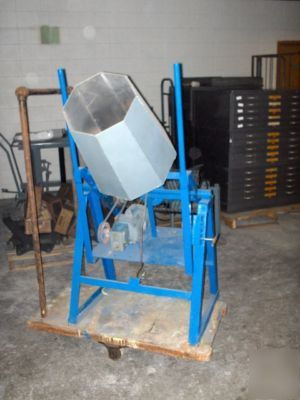
Oblique or tilting open-end barrel used for tumbling, burnishing or drying. Barrel can be tilted down for unloading
Comments