CASE STUDY: Centrifugal Iso-Finishing Technology for 3D printed (additive manufactured) parts
- Dave Davidson
- Sep 24, 2020
- 4 min read
Updated: May 16, 2021
Contributed by Cole Mathisen, MFI
For additional technical information and help with sample part processing your parts
CONTACT: Dave Davidson | Deburring/Surface Finishing Technologist

3D LOGIC’S CHALLENGE: Established in early 2018, 3D Logics was adept at creating parts that were accurate and consistent, but often had inherent surface roughness. The company had persistent finishing challenges with metal products, particularly titanium and nickel-based Inconel parts which are extremely tough and require high energy and very exact media to properly finish. Being a startup with just a few employees, 3D Logics wanted a partner that could provide finishing expertise and advice, as well as a selection of specialized media that would enable them to provide high end finished parts to their growing customer base.
THE SOLUTION: Centrifugal Iso-Finishing. 3D Logics evaluated many different types of finishing equipment but ultimately settled on Centrifugal Iso-Finishing machines made by MFI. MFI had the whole package they were looking for – the best systems (made in Minnesota), years of experience and a large selection of media. 3D Logics purchased an HZ-40 High Energy Centrifugal Iso-Finishing (CBF) Machine, and MFI partnered with them to help their employees gain a better understanding of which media to use depending on the material, size and shape of the item. Whenever 3D Logics has a new part, they can send it the MFI technical team, who will develop the finishing process and send a report so 3D Logics can provide their customers with the highest quality metal and plastic/polymer parts.
THE RESULTS: Thanks to their HZ-40 CBF and technical assistance from MFI, now 3D Logics can put a mirror finish on their titanium parts, and get precisely finished parts in 20 to 30 minutes. 3D Logics Owner Sterling Logan is very pleased with his HZ-40 CBF and happy to recommend MFI to anyone who has finishing questions. He appreciates the MFI technical team’s help, quick response, and honesty to tell him when a barrel finisher isn’t the best finishing solution. That’s because they don’t just want to sell him a machine and media, they want him to have the best possible solution.

“Our customers immediately noticed a difference when we started using the Centrifugal Iso-Finishing machine. They asked, ‘Wow, are these 3D parts? This is incredible, these parts are amazing. What did you do?’ MFI gives us a leg up on the competition and we’re happy to partner with them. Anyone seriously looking at barrel finishers should take a close look at MFI. They would be in good hands.”
3D Logics Owner: Sterling Logan
3D Logics is now an ISO 9001:2015 & ISO 13485:2016 certified manufacturing facility.
For information about 3D Logics, visit their website at https://3dlogics.com/
Or reach out directly:
Address: 5293 NE Elam Young Parkway, Suite 150, Hillsboro, OR 97124
Email: info@3dlogics.com Telephone: (503) 455-8450
Guest column contributed by Cole Mathisen, Sales manager: MFI
Improve Surface Finish and achieve a High-Polish on Additive parts in minutes with Centrifugal Iso-Finishing Technology.
Additive manufacturing is quickly becoming a feasible option for full-scale manufacturing.
The combination of modern software, new materials and printer technology is allowing additive manufacturing or AM to bring efficiency and flexibility to manufacturing operations. The parts created using these processes are often left with very rough surfaces and scale and other imperfections. Companies using additive manufacturing need to come up with a quick solution for smoothing and polishing their parts.3D Printing of models is often referred to as “Rapid Prototyping. Using traditional hand polishing methods to improve the extremely rough surfaces of these parts is anything but “Rapid.” An operator can spend days to get all of the surfaces smoothed out by hand. Centrifugal Iso-Finishing processes can achieve a polish on several parts at once (Like the ones featured above) in just two hours.
The Process: Achieving a polish on a 3D Printed part depends greatly on the material and the initial roughness and scale left over from the printing process. On relatively clean (no heavy heat scale or atmospheric discoloration) titanium or stainless steel 3D printed parts with an initial surface roughness of 300-400 micro-inch Ra here is a typical example process that is used with Centrifugal Iso-Finishing Machines:
Step One: Heavy grinding with aggressive plastic or ceramic media for 60 – 90 Minutes Step Two: Pre-Polish with lighter plastic for 30 Minutes Step Three: High Polish with dry corn cob polishing media for 30 minutes or wet porcelain m for 15 Minutes Total process time: Two Hours (Not including loading) Equipment Recommendation: 3D printed parts that have a high production volume to justify tumbling equipment tend to be smaller in size. For this reason the HZ-40 is a popular option. Its small footprint (roughly 3′ x 4′) makes it ideal for fitting into tight lab operations. See videos of HZ-40 and other machines in operation below:
A slightly larger and more automated machine model is shown below running a typical three-step process for developing fully polished part surfaces:
For additional information or help with getting your printed parts sample finished contact: Dave Davidson at davidson@deburring-tech-group.com or 509-563-9859 (mobile and WhatsApp)


See below excerpts from a Keynote presentation about Centrifugal Iso-Finishing Technology.



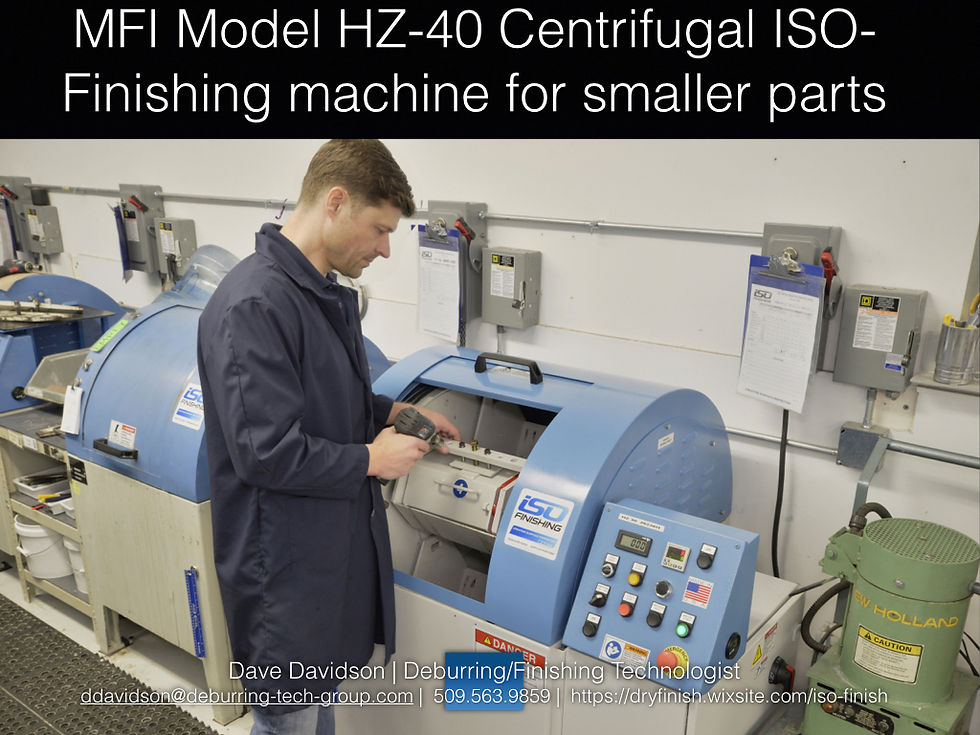
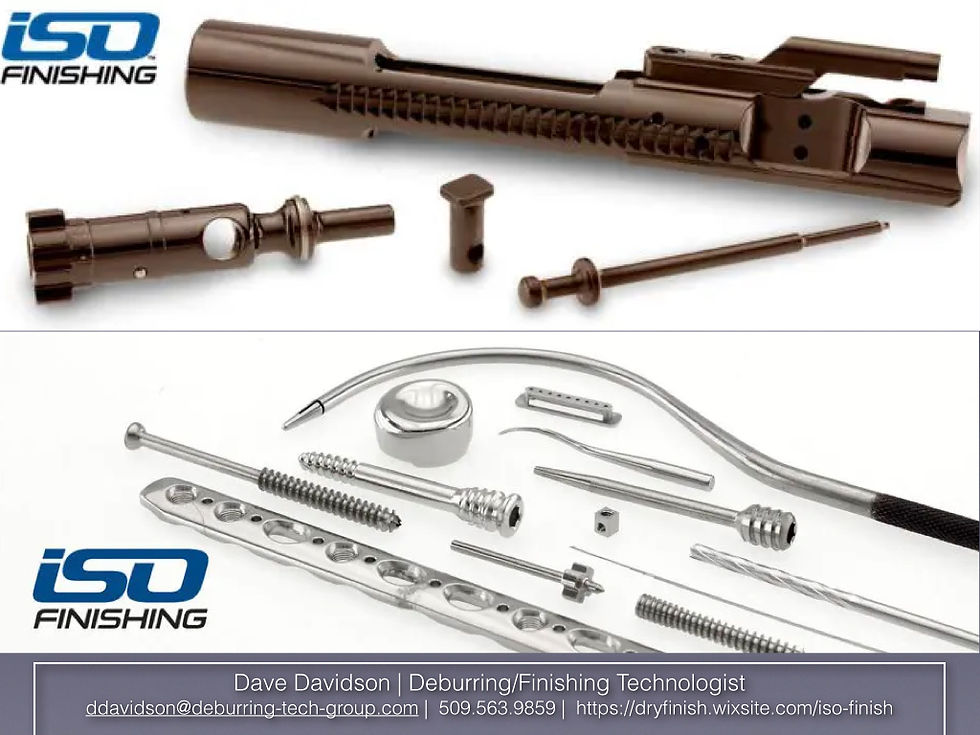
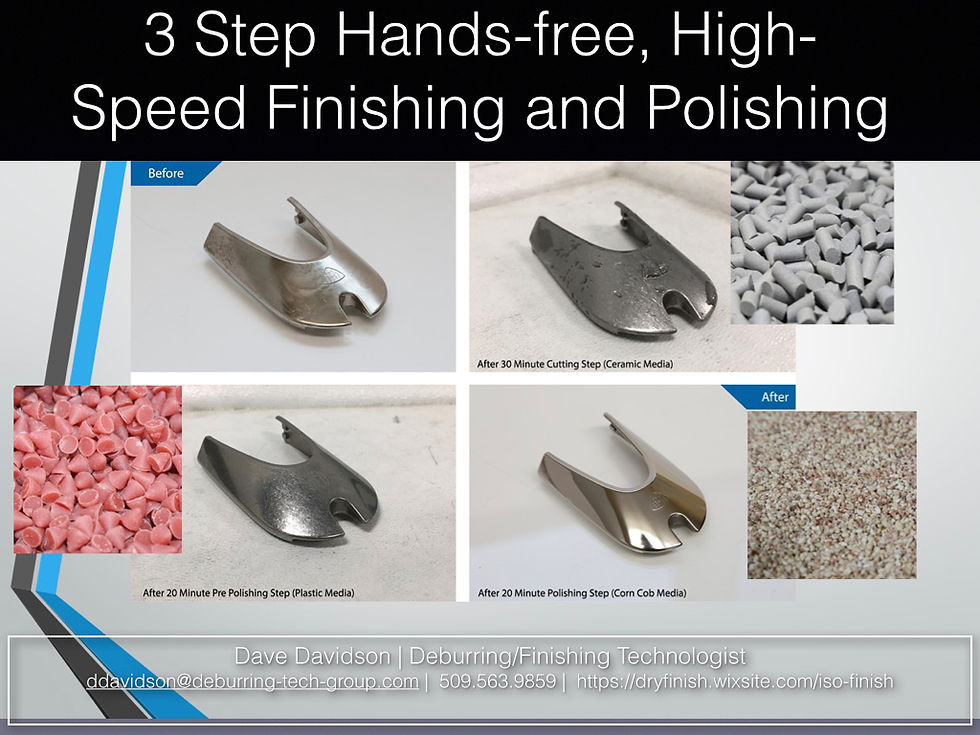


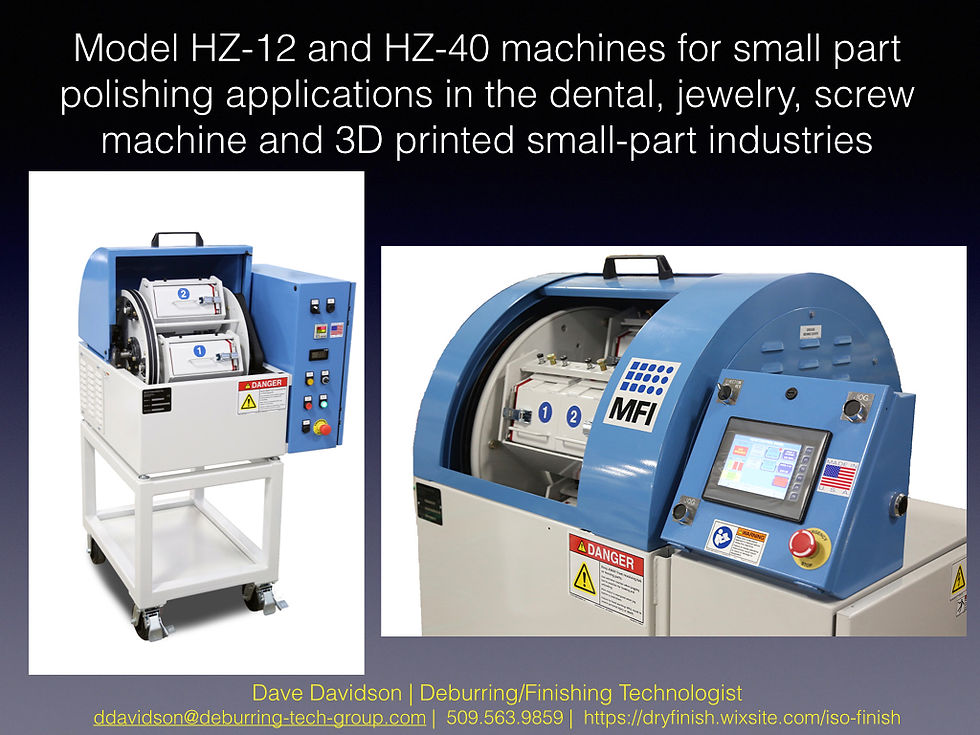
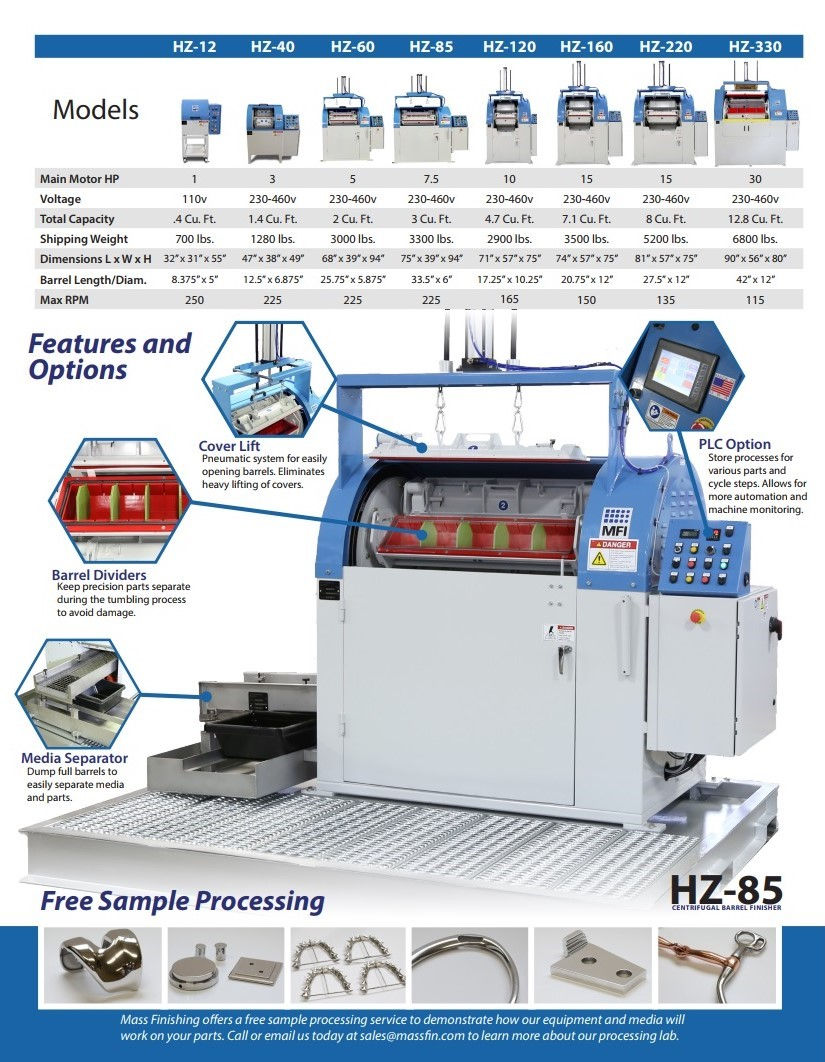
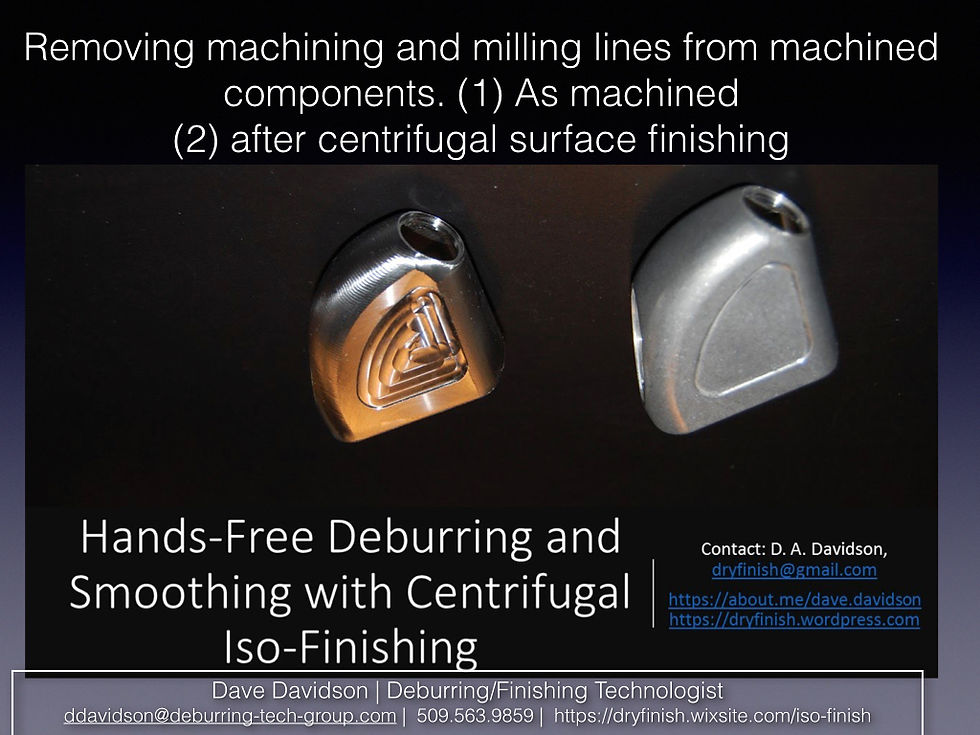
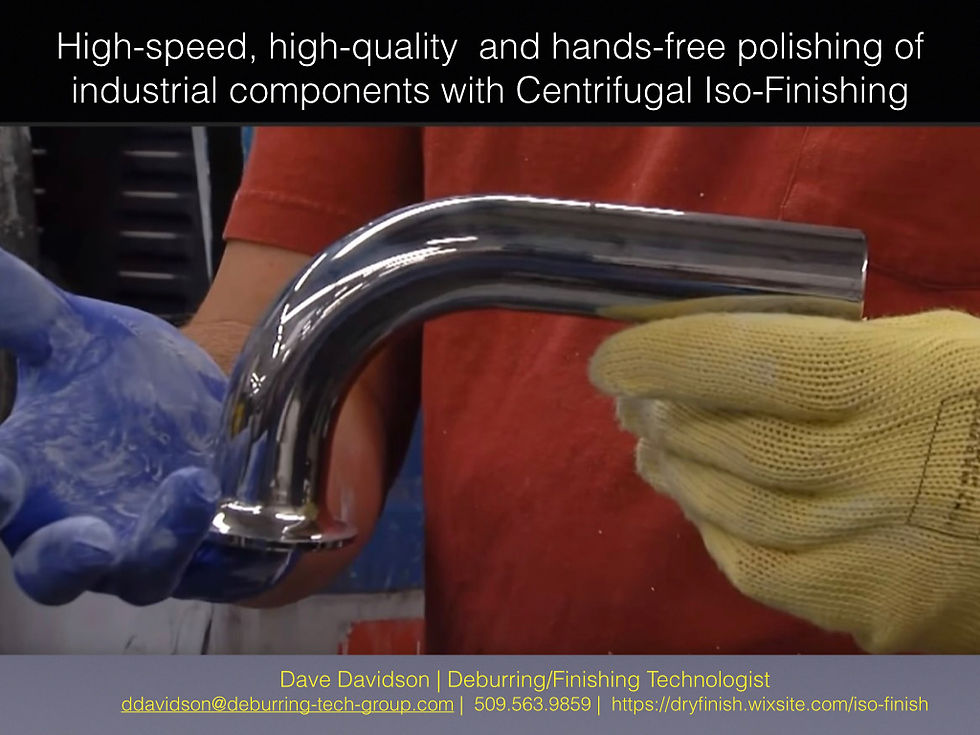
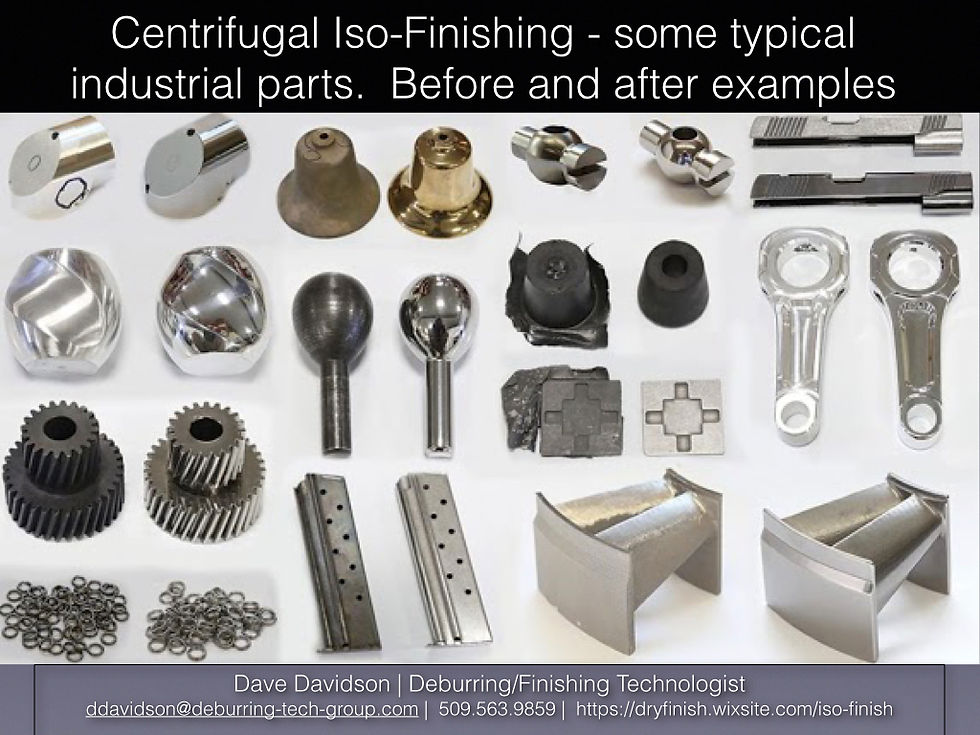
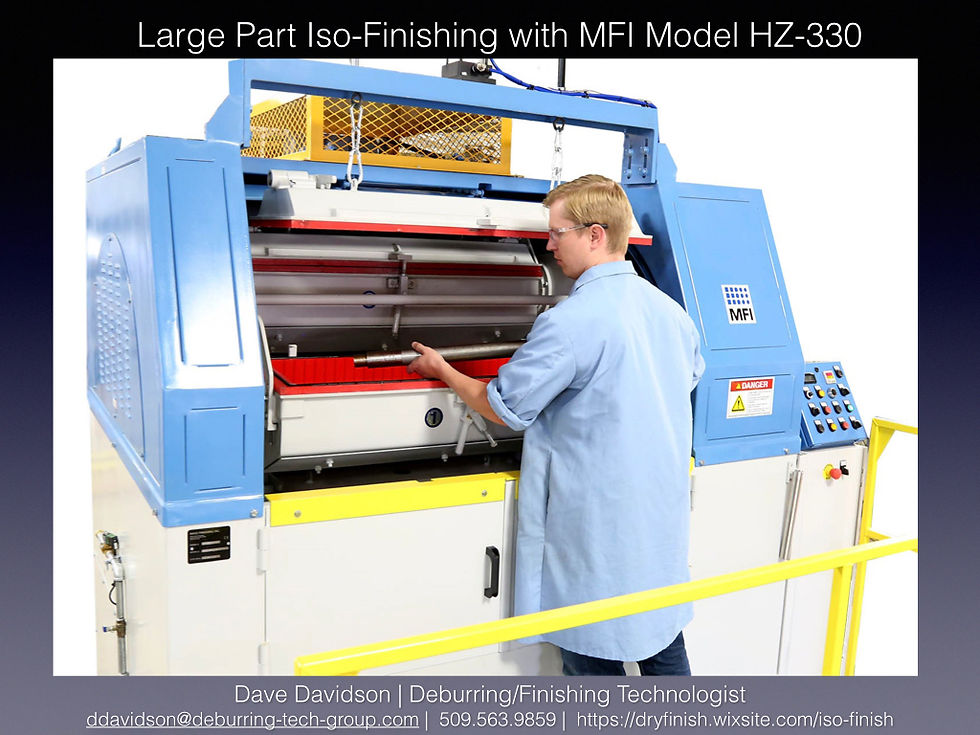
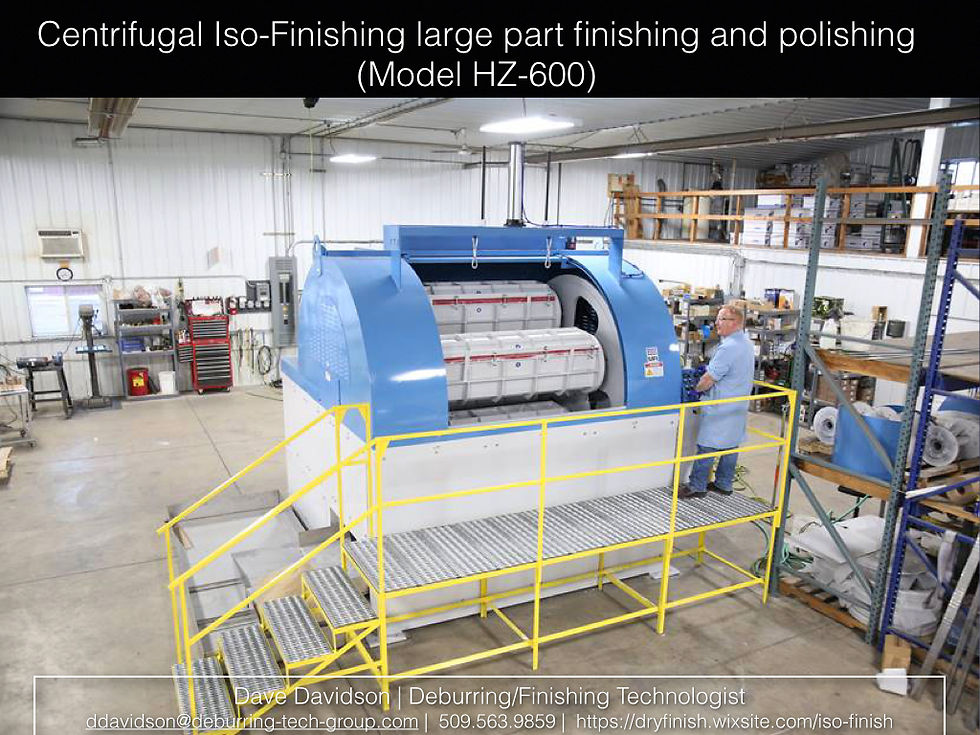
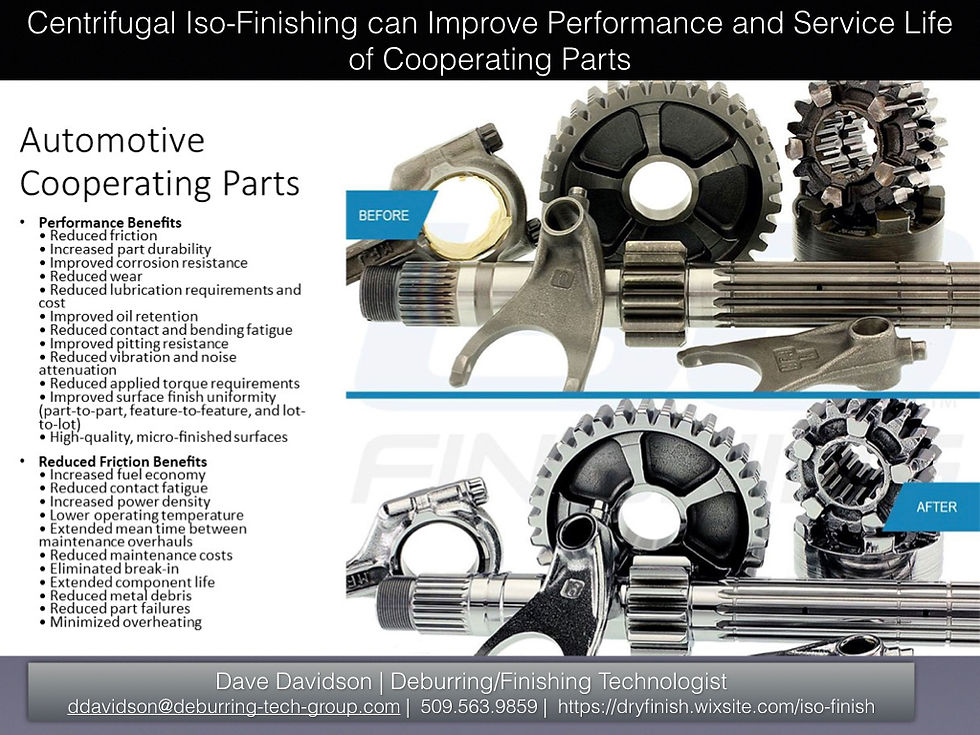


Comments