CASE STUDY: Meeting the Lean Deburring and Finishing Challenge at MacKay Manufacturing with Centrifu
- Dave Davidson
- Mar 28, 2017
- 4 min read
by Dave Davidson, Deburring/Finishing Technologist and Contributing Editor ddavidson@deburring-tech-group.com | 509.563.9859 | dryfinish.wordpress.com
MacKay Manufacturing is a progressive precision CNC contract machining operation located in Spokane WA (close to the Idaho border). It drew our attention because of the extensive use it makes of centrifugal iso-finishing technology to minimize the need for hand-deburring and produce super-isofinishes on the parts it makes for the medical and aerospace industries as well as other consumers of precision machined products. First some background on them. (See also some of the parts they make here at this link: https://www.mackaymfg.com/home/gallery/ (Editor’s note: In the feature photo shown above, are some medical camera housing parts where the machining marks and cutter paths have been removed and smoothed in an entirely hands-free operation. Listen to Katie MacKay describe in detail how MacKay Manufacturing uses centrifugal iso-finishing to perform this type of work).
“We take on the jobs no one else wants to do,” says MacKay Manufacturing Vice President Katie MacKay in a company video. “We really thrive on doing the tough stuff.” MacKay’s products combine complexity with small size: parts for cruise missiles and space shuttles, artificial-heart valves, small vacuum chambers, surgical tools. MacKay markets itself not only on its ability to turn out such intricate work but also the setting in which it does that work. You don’t expect a machine shop to brag about its tasteful décor, the basalt columns and fine furnishings in its lobby, or the bistro design in the employee break room. MacKay does.
There’s an important business point to such detail, the company says. Consider the matter of workplace temperature. “Our climate control system keeps all of our manufacturing materials and equipment at a constant temperature,” Katie MacKay says. “No temperature fluctuation means dimensional stability and better consistency part after part. Besides, it makes it a lot easier to focus on our work if we’re not freezing or sweating our tails off, right?” Employees seem to agree. More than 40 percent of MacKay’s workforce has been with the company for 10 years or more.
Below: Katie MacKay talks about the MacKay experience with Centrifugal Iso-Finishing operations on parts made from titanium, stainless steel, steel, aluminum, plastics and others destined for medical, aerospace and other precision machining applications.
For over thirty years, MacKay Manufacturing Inc. has offered discriminating engineering and purchasing professionals precision manufacturing services and industry-leading processes. In the medical field, we serve designers of endoscopic, arthroscopic, orthopedic, and vascular instruments. Our surgical devices meet the critical standards of the medical instrument industry.
General manufacturing needs are all covered—from prototyping, through manufacturing, to assembly and shipping. Over 125 dedicated employees bring decades of technical expertise to every customer and part we manufacture. As agencies continue to escalate their oversight of the manufacturing process, we recognize the need for maintaining robust documentation control and tracking our production processes. This documentation control assures customers that we have purchased the correct raw materials and are properly utilizing and tracking them through every step of the manufacturing process.
This case study is made up of a series of video interviews that cover three areas of the company’s operations. (1) CNC machining technology. (2) Implementing Lean into their precision machining operations and contract manufacturing. (3) Utilization of Centrifugal Isotropic Finishing as a primary method for reducing hand and manual deburring operations and for developing precision surfaces and even micro-finished surfaces on machined parts.
For further information on this finishing technology contact:
Contributing Editor: Dave Davidson, Deburring/Finishing Technologist 509.563.9859 | dryfinish@gmail.com | https://dryfinish.wixsite.com/iso-finish
If you have parts that need edge or surface finishing improvement and would like to have FREE sample part processing and a quotation developed for finishing the parts contact Dave Davidson at
dryfinish@gmail.com I can also be reached at 509.563.9859 Information about equipment for bringing Centrifugal Iso-Finishing capability to your facility is also available…
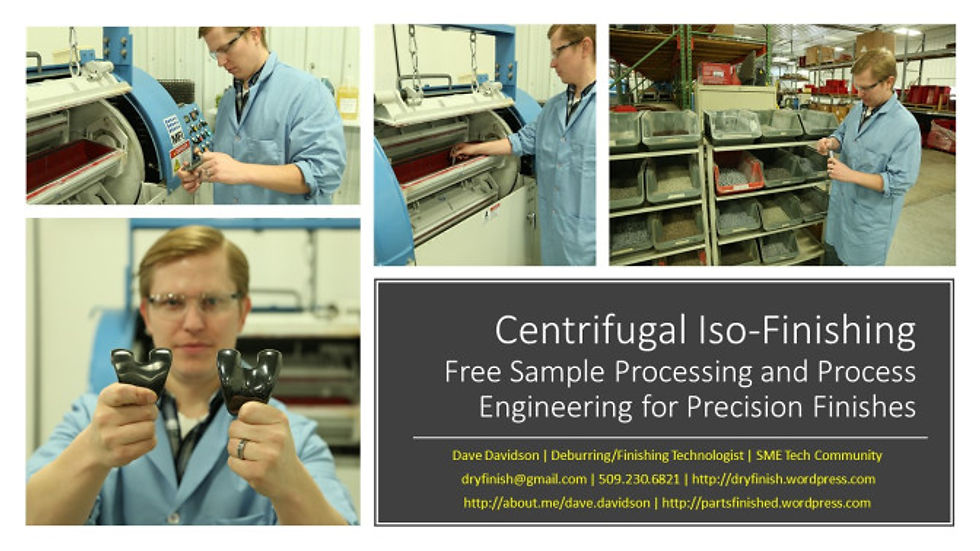
Some operations videos are shown below including precision machining and centrifugal isofinishing.
Above: Katie describes MacKay Manufacturing’s Lean Transformation experience.
Below: Process video about Centrifugal Iso-finishing operations smoothing and polishing aluminum parts. Parts made from other alloys are processed with a variant of this basic process. Both additive manufactured (3D printed) and conventionally manufactured components are increasingly deburred and finished with this high-speed and hands-free micro-finishing method.
This slideshow requires JavaScript.
Above: examples of parts finished with Isotropic Finishing and Micro-finishing technology
Centrifugal Isotropic Finishing
Centrifugal barrel finishing (CBF) is a high-energy finishing method, which has come into widespread acceptance in the last 25-30 years. Although not nearly as universal in application as vibratory finishing, a long list of important CBF applications have been developed in the last few decades.
Similar in some respects to barrel finishing, in that a drum-type container is partially filled with media and set in motion to create a sliding action of the contents, CBF is different from other finishing methods in some significant ways. Among these are the high pressures developed in terms of media contact with parts, the unique sliding action induced by rotational and centrifugal forces, and accelerated abrading or finishing action. As is true with other high energy processes, because time cycles are much abbreviated, surface finishes can be developed in minutes, which might tie up conventional equipment for many hours.

Centrifugal Barrel Finishing principles – high-intensity finishing is performed with barrels mounted on the periphery of a turret. The turret rotates providing the bulk of the centrifugal action, the barrels counter-rotate to provide the sliding abrasive action on parts.
The principle behind CBF is relatively straightforward. Opposing barrels or drums are positioned circumferentially on a turret. (Most systems have either two or four barrels mounted on the turret; some manufacturers favor a vertical and others a horizontal orientation for the turret.) As the turret rotates at high speed, the barrels are counter-rotated, creating very high G-forces or pressures, as well as considerable media sliding action within the drums. Pressures as high as 50 Gs have been claimed for some equipment. The more standard equipment types range in size from 1 ft3 (30 L) to 10 ft3, although much larger equipment has been built for some applications.
Media used in these types of processes tend to be a great deal smaller than the common sizes chosen for barrel and vibratory processes. The smaller media, in such a high-pressure environment, are capable of performing much more work than would be the case in lower energy equipment. They also enhance access to all areas of the part and contribute to the ability of the equipment to develop very fine finishes. In addition to the ability to produce meaningful surface finish effects rapidly, and to produce fine finishes, CBF has the ability to impart compressive stress into critical parts that require extended metal fatigue resistance. Small and more delicate parts can also be processed with confidence, as the unique sliding action of the process seems to hold parts in position relative to each other, and there is generally little difficulty experienced with part impingement. Dry process media can be used in certain types of equipment and is useful for light deburring, polishing, and producing very refined isotropic super-finishes.
AUTHOR BIOGRAPHY – David A. Davidson, [dryfinish@gmail.com]
Mr. Davidson is a deburring/surface finishing specialist and consultant. He has contributed technical articles to Metal Finishing and other technical and trade publications and is the author of the Mass Finishing section in the current Metal Finishing Guidebook and Directory. He has also written and lectured extensively for the Society of Manufacturing Engineers, Society of Plastics Engineers, American Electroplaters and Surface Finishers Association and the Mass Finishing Job Shops Association. Mr. Davidson’s specialty is finishing process and finishing product development.
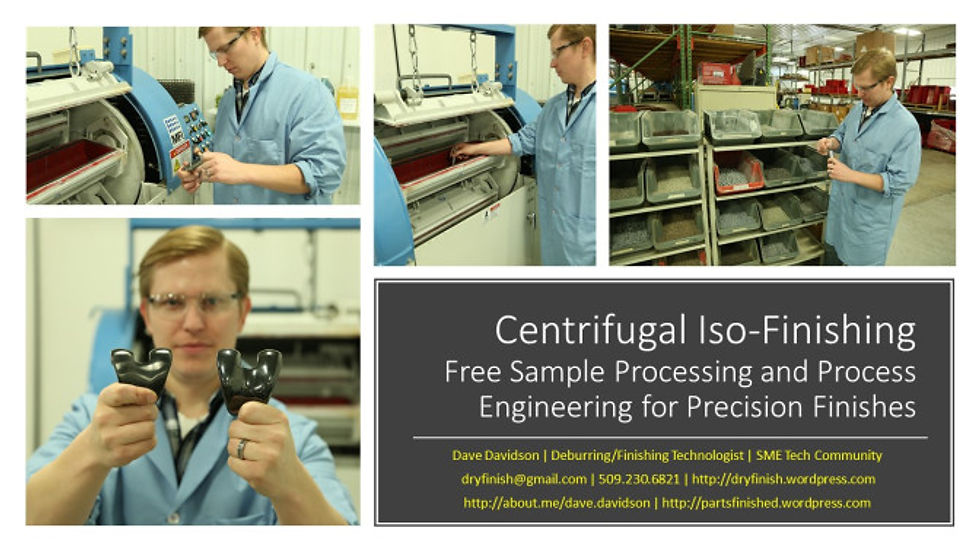
Comments