Centrifugal Iso-Finishing and Polishing of Dental Parts, Jewelry and other Small Parts...
- Dave Davidson
- Oct 23, 2018
- 3 min read
Updated: Dec 10, 2020
For additional technical information or free sample part finishing contact: Contributing editor: Dave Davidson | Deburring/Finishing Technologist ddavidson@deburring-tech-group.com | dryfinish.wixsite.com/iso-finish
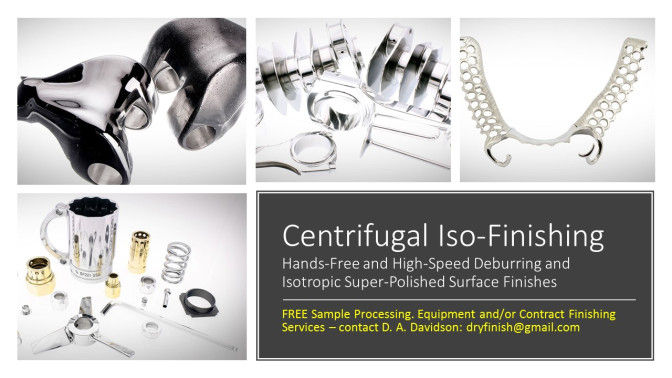
If you have parts that need edge or surface finishing improvement and would like to have FREE sample part processing and a quotation developed for finishing the parts please contact Dave Davidson at ddavidson@deburring-tech-group.com I can also be reached at 509.563.9859. Information about equipment for bringing Centrifugal Iso-Finishing capability to your facility is also available…

For (free) sample part processing information contact Dave Davidson at ddavidson@deburring-tech-group.com
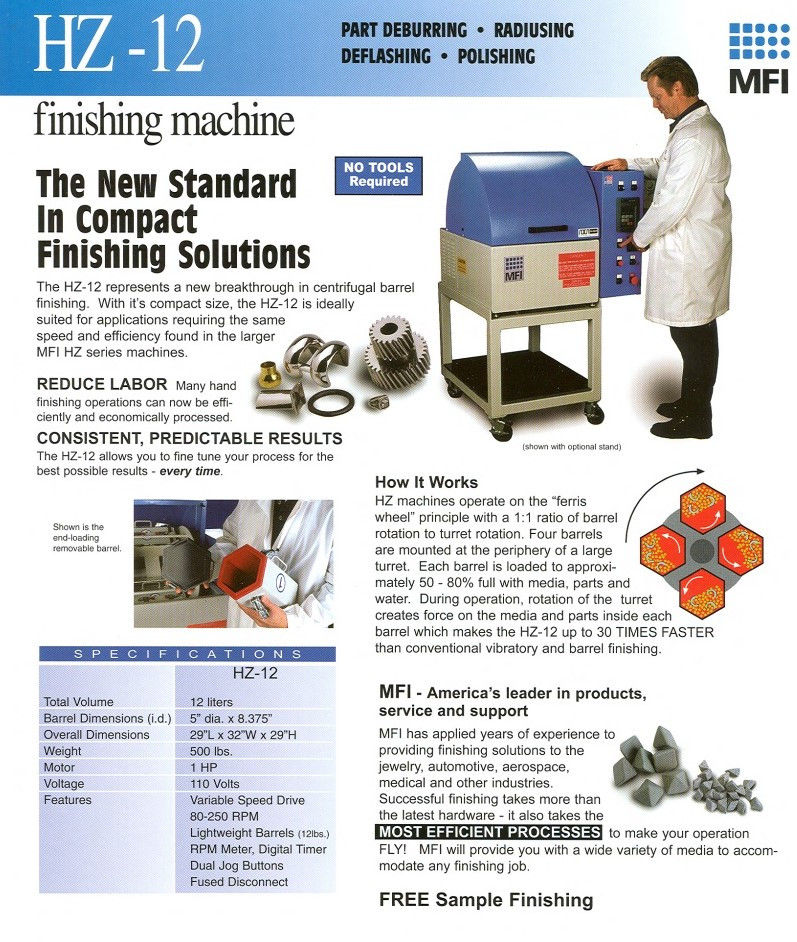
The HZ-12 features smaller, removable barrels. By purchasing a second set of four barrels, the operator can run one set of barrels while loading and preparing another. This can dramatically reduce downtime on the machine.
The HZ-12 works well in small places like dental and medical device labs or in manufacturing and finishing cells. Despite its smaller foot-print, it still packs the same high-end finishing punch of its larger model counterparts.
Mobility and Simplicity. The HZ 12 comes complete with a steel frame stand on wheels. This means you can roll it easily around your production facility. It also plugs into a standard 120-volt power outlet.
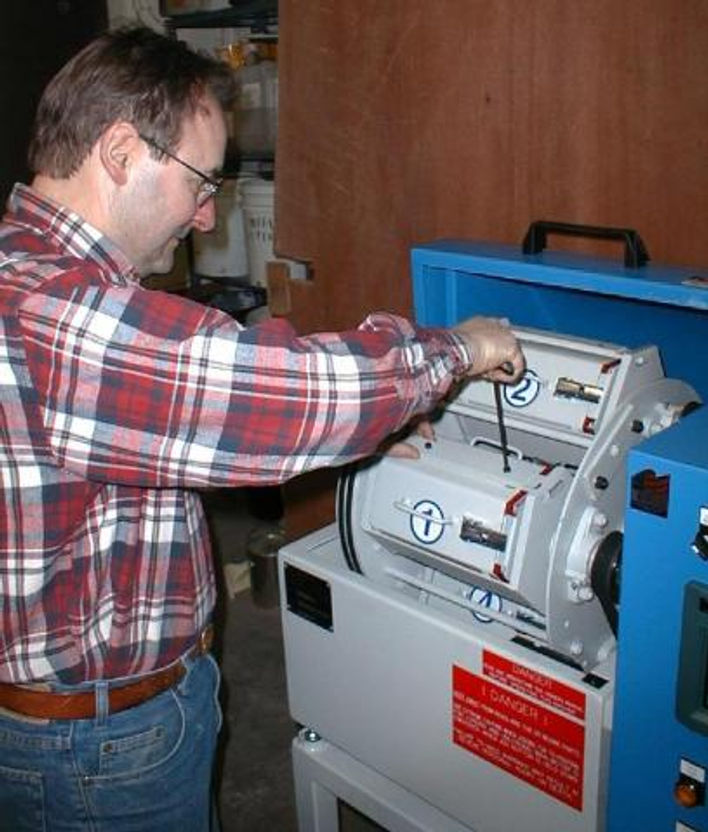
Centrifugal Barrel Finishing (CBF) systems are the fastest and most economical form of finishing and deburring machines available. Barrel tumblers are the industry workhorse in polishing, deburring and deflashing parts. From jet engine blades in the aerospace industry to heart valves and medical implants, these high-speed tumbling machines are the versatile and money-saving solution for polishing and deburring.
In a matter of minutes, this deburring and finishing tool can deburr, clean up, smooth and polish metal, acrylic or rubber and other materials. They can drastically reduce the finishing time over vibratory finishing machines. They also are useful for minimizing hand-deburring and finishing operations
Isotropic or Iso Finishing. The finish achieved by these machines is isotropic, meaning parts are polished uniformly and evenly in all directions, something that cannot be achieved by hand. Variable speed control allow these tumbling machines to achieve whatever finish the operator desires, from a simple polish at lower speeds, to full scale deburring and edge radiusing at full RPM.
Below: Watch the HZ-12 in Action:
ABOVE: For heavier volume users, there is also the HZ-40 machine for running larger lots.
See some examples of part applications in the photos below.


HZ Series Standard Features
Variable Frequency Drive to easily adjust machine speed
Four individual barrels
Durable, Hot Poured Polyurethane lined barrels and barrel covers
Field replaceable liners
Compact size
Convenient Operator Control Console
High-quality control components for years of reliable service
Cycle complete buzzer
User adjustable process timer
120 volt wiring. 1 or 3 phase
Integral hood safety switch
Machine Specifications:
Main Motor HP 1.0
Voltage 120
Total Capacity 12 Liters
Shipping Weight 700 lb.x
Dimensions LxWxH 34″x30″x30″
Barrel Length/Diameter 8.375″x5″
Max G-Force 11.32
Optional Features
Extra Barrels
Electric Hoist
100 Gallon Sludge Tank
PLC Touch Screen Control Package
Custom Engineering Also Available
Custom screen sizes are available depending on the media your job requires. These screens can also be quickly changed out to fit different jobs. Mass Finishing can also create multi-level media classification separators that have the ability to sort two different types of media and parts.
The free-standing media separator features a variable speed control switch. Once a finishing job is complete, simply pour barrels or buckets of finished parts and media into the separator and watch as the media falls through the screen, leaving finished parts on top. The heavy duty wheels and frame stand allow the operator to move the separator to the next machine or into a storage area when not in use.
MFI Table and Sludge Tank
Create the perfect finishing area to maximize production

Mass Finishing’s Model 633 Table & Sludge Tank is the perfect addition to any finishing operation. With a tough frame built out of anodized aluminum and PVC, this workstation can take a beating and is easily cleaned off with the spray of a water hose.
Finishing parts with certain types of media can generate a slurry mixture consisting of worn down pieces of media and the imperfections of your parts. Having an area where you can rinse off parts quickly can speed up your operation and make your workers much happier. Multiple shelving levels gives the operators space to set things like chemical cleaners, towels and tools. MFI also offers optional media pans and screens.

Many different small parts can be deburred, smoothed and polished in te HZ-12 centrifugal finishing machine.

For information and assistance in having your parts run through our (free) sample part iso-finishing program CONTACT Dave Davidson at ddavidson@deburring-tech-group.com
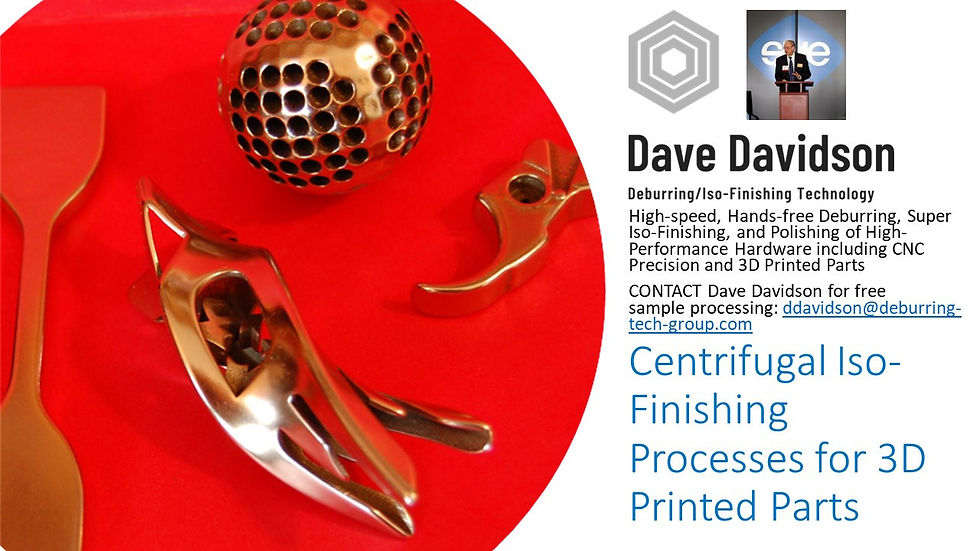
#Burnishing #Polishing #smoothing #surfacefinishing #IsotropicFinishing #Finishing #3DPrinting #aerospace #MetalFinishing #microfinishing #Deburring #AdditiveManufacturing #partfinishing #tumbling #CentrifugalBarrelFinishing #isotropic #abrasive #Precisionmachinedparts #Jewelry
Comments