Centrifugal Iso-Finishing Complements the Additive Manufacturing Process
- Dave Davidson
- May 7, 2021
- 4 min read
Updated: Dec 25, 2021
Guest column contributed by Mike Klein, Iso-Finishing For additional information contact: Dave Davidson | Deburring/Surface Finishing Technologist Email: ddavidson@deburring-tech-group.com | See also the technical blog at: dryfinish.wordpress.com

ABOVE: Examples of 3D printed metallic parts that have been surface finished and polished with Centrifugal iso-Finishing Technology.
Additive manufacturing and 3D printed parts. Additive manufacturing is an innovative manufacturing process that creates 3D printed objects. As the name suggests, material is only added when and where it is necessary. Parts are created using computer-aided-design (CAD) software or 3D object scanners to deposit material one layer at a time in precise geometric shapes.
Additive manufacturing can be done using various materials, with the three most widely utilized being polymers, ceramics, and metals. While 3D printing and additive manufacturing are synonymous, there are several different types, including:
Powder Bed Fusion
Binder Jetting
Sheet Lamination
Directed Energy Deposition
Material Extrusion
Material Jetting
Vat Photopolymerization
Quickly and efficiently producing parts using a repeated process like 3D printing offers a timely and cost-effective approach to manufacturing. Its speed and low cost are ideal for producing low-volume, high-complexity, and ever-changing parts. The simplicity of the process makes the development of complex parts easier, cheaper, and more precise.
Applications of Additive Manufacturing
Additive manufacturing serves a wide range of applications. Recognizing the many benefits of 3D printed parts, researchers have continued to find ways to utilize the process to create solutions across countless fields. Many industries appreciate the advantages additive manufacturing offers.
The medical industry relies on additive manufacturing to create custom ankle replacements and other orthopedic parts. Likewise, the military and defense sectors have added 3D printing technology to print critical and replacement parts while in the field or at maintenance depots. Additive manufacturing can also streamline various processes, such as tool fabrication, research and development, and other rapid prototyping.
Surface Finishing for Additive Manufacturing
Surface finishing is an excellent complement to the additive manufacturing process and is necessary for additive manufactured products requiring a smooth surface and precise edges. The type of service finishing and polishing media used will depend greatly on the material, shape, and size of the 3D printed part. In many cases, additive manufactured parts will undergo one of two processes: vibratory finishing or centrifugal barrel finishing. Either process can be done wet or dry with abrasive media composed of plastic, ceramic, or organic material. The benefits of surface finishing for 3D printed components include enhanced surface quality, geometrical accuracy, and improved performance.
ABOVE: 3D printed parts surface finished with Centrifugal Iso-Finishing
Enhanced Surface Quality and Geometrical Accuracy
One of the biggest disadvantages of 3D printing is surface imperfections resulting from the process. During the production process, artifacts or burrs may appear on the surface of the part. Surface finishing removes artifacts and smoothes uneven surfaces to create a more aesthetically pleasing part and prepares the surface for any coatings it may receive.
Improved Part Performance
The application of 3D printed parts is very diverse and it is essential parts are high quality and perform exceptionally well. Surface finishing improves the performance of additive manufactured parts and components, resulting in more durable and longer-lasting parts. In addition to making parts stronger, surface finishing increases resistance to wear, corrosion, heat, and other elements known to cause parts to fail.
Centrifugal Iso-Finishing capabilities for 3D printed parts and components. Centrifugal ISO Finishing processes provides a range of finishing capabilities for 3D printed parts and components. This proven process is the ideal partner for additive manufacturers in a wide range of industries. For more information about the services, equipment and sample part processing offered contact Dave Davidson at 509.563.9859 or email us at ddavidson@deburring-tech-group.com

Centrifugal Iso-Finishing Technology
Centrifugal Barrel Finishing (CBF) is a high-energy finishing method where Centrifugal Barrel Machines are used. A great example of this type of machine is the HZ series. These machines are typically made up of four individual barrels (or drums) mounted on the outer edge of a turret. The turret is rotated in one direction, causing the barrels to rotate in the opposite direction creating very-high G-forces or pressures, as well as considerable media sliding action within the drums. The movement mimics that of a ferris wheel. This action is due to either a Timing Belt, V-Belts or Chain that is connected between the main shaft and the centerline of the 4 barrels. In operation, this turret rotation creates a high centrifugal force. This force compresses the load into a tight mass causing the media and parts to slide against each other removing burrs and creating a superior finish. Short cycle times are realized as a result of the high centrifugal energy being applied to the parts.
Centrifugal Iso-Finishing machines operate on the Ferris wheel principle. Each machine contains four barrels that are mounted on the periphery of a rotating turret The operator fills the barrel with media, parts and water 50-90% depending on the operation.
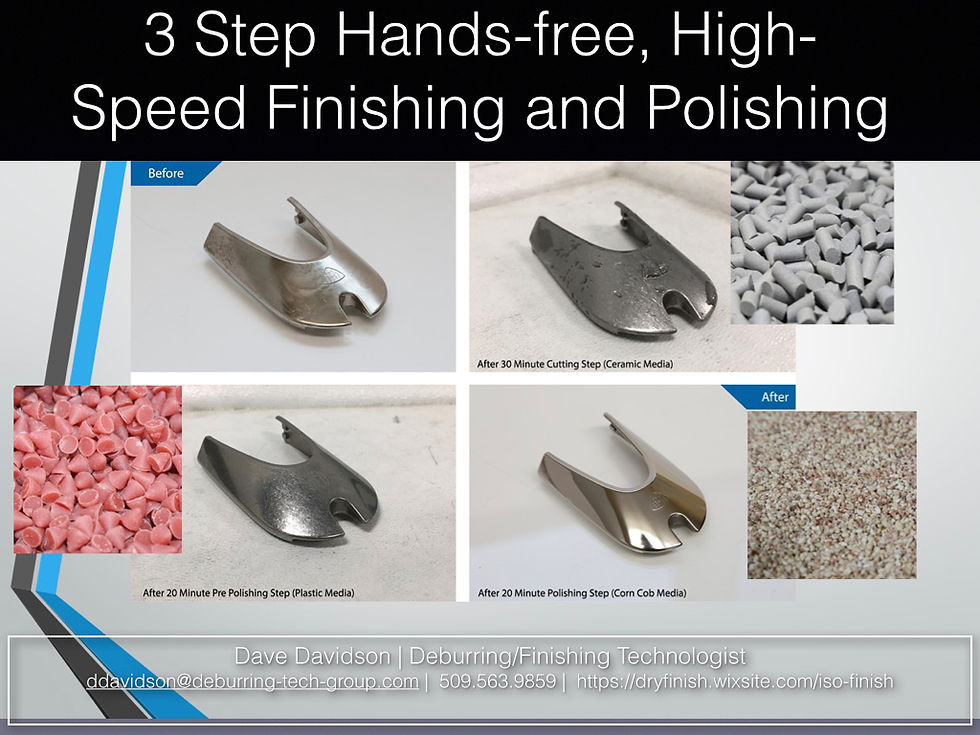
Highly polished surfaces on both additive manufactured and conventional parts is performed with two or three steps with differing media types...
During operation, the entire turret of the machine rotates like a high-speed ferris wheel. While the barrels counter-rotate at the same speed. As the speed increases, the media and parts rub against one another randomly and repeatedly, removing even the smallest imperfections. In a matter of minutes, the finishing cycle is complete and the parts are ready to be separated from the media.
Cycle times are typically five to ten times faster than other finishing methods, as the media is interacting with and pressing against the part edges and surfaces at high-pressure and intensity (on the order of 10-13G's)
ABOVE: A Model HZ-60 Centrifugal Iso-Finishing machine video demonstrating the operation of the machine.
A wide variety of small to moderately sized parts are deburred, finished and polished in Centrifugal Iso-Finishing equipment. These are high-speed and hands-free processes
The industries that make use of this type of finishing include the jewelry, medical, dental, aerospace, precision screw machine and CNC components and many others
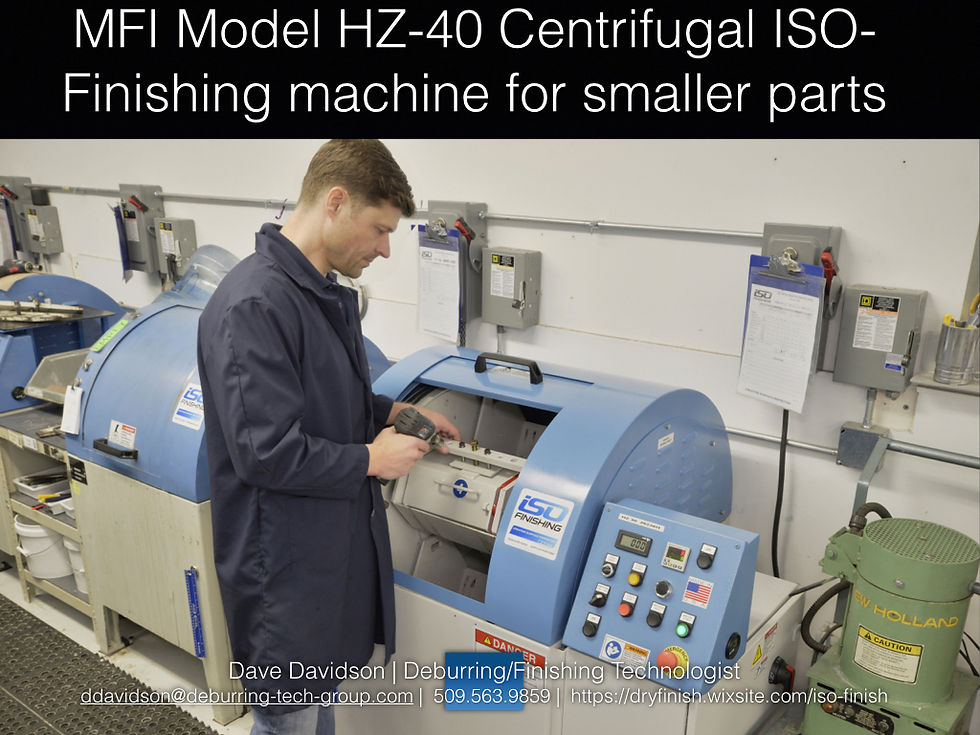


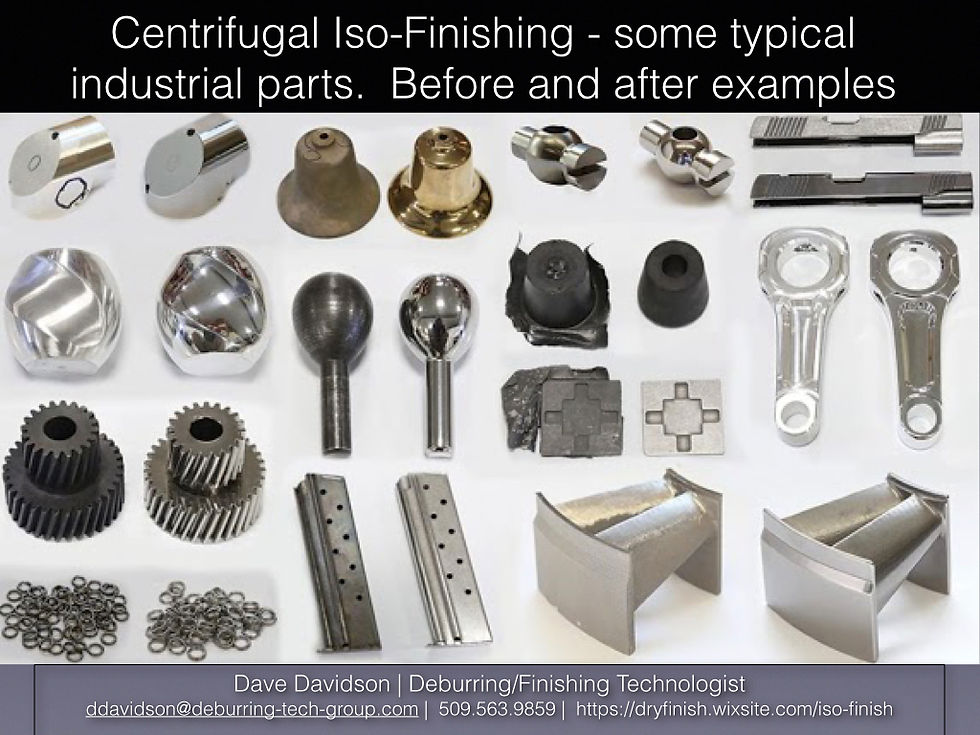
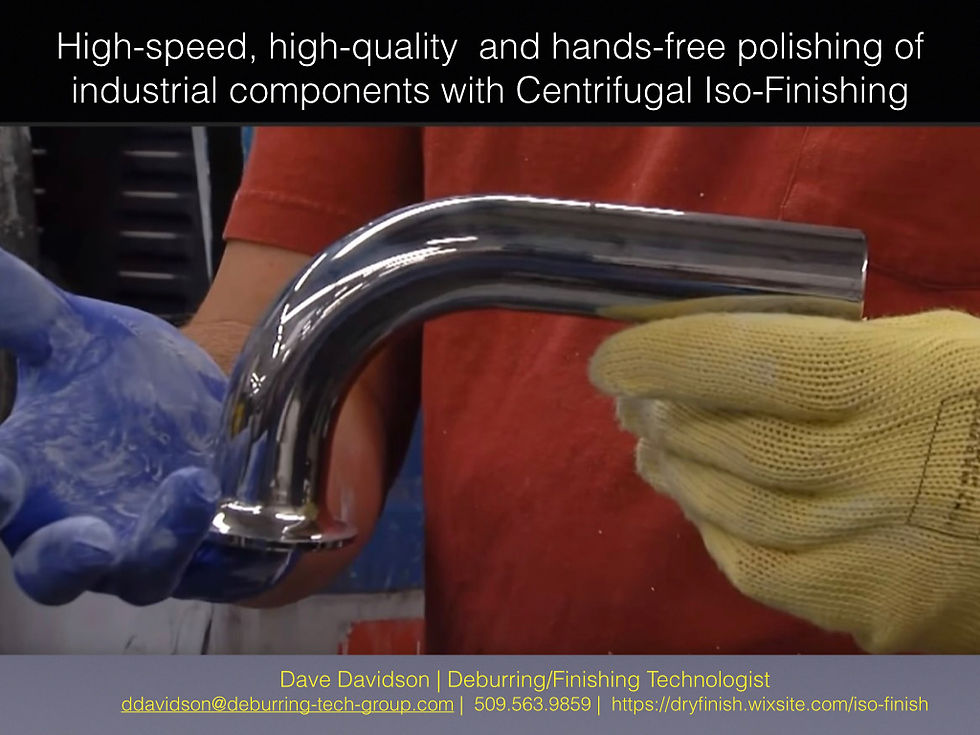
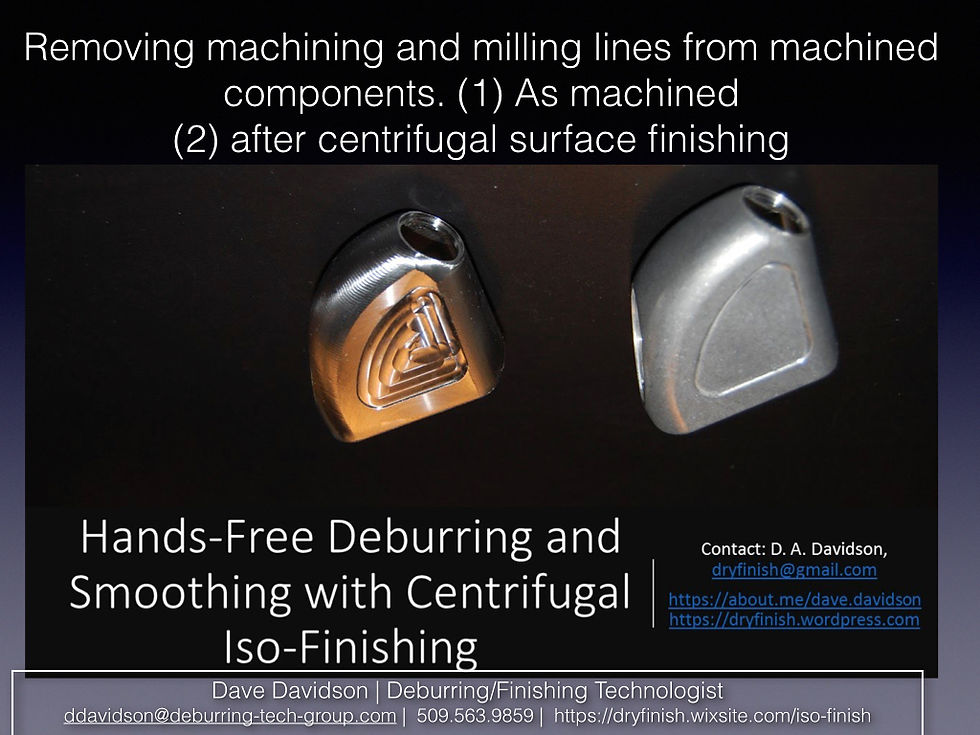

Comments