Centrifugal Iso-Finishing Technology: The machines
- Dave Davidson
- Apr 6, 2020
- 4 min read
Updated: Apr 23, 2021
Contributed by Cole Mathisen, Sales and Marketing Manager, MFI
For additional information contact: Dave Davidson | Deburring/Finishing Technologist ddavidson@deburring-tech-group.com | +1.509.563.9859 | dryfinish.wixsite.com/iso-finish
Reduce Hand-deburring and polishing labor. Many hand operations can now be efficiently and economically replaced with automated mechanical processing that finishes parts in bulk operations.
How it works. Centrifugal barrel machines work on the ferris wheel principle, with barrels mounted on the periphery of a rotating turret, while the barrel rotates in the opposite direction. The combined high-speed rotation and counter-rotation accelerate the cycle times needed to deburr and produce quality surface finishes. With these models, four barrels are mounted at the periphery of a larger turret. Each barrel is then loaded to approximately 50 -80% full with finishing media and parts, and water (for abrasive wet processes). During operation, rotation of the turret creates forces on the media and parts in the barrel which makes this process up to ten times faster than processes run in a conventional barrel or vibratory finishing equipment system.
Consistent and repeatable results. This machine can allow you to fine-tune your process for the best possible result – every time.

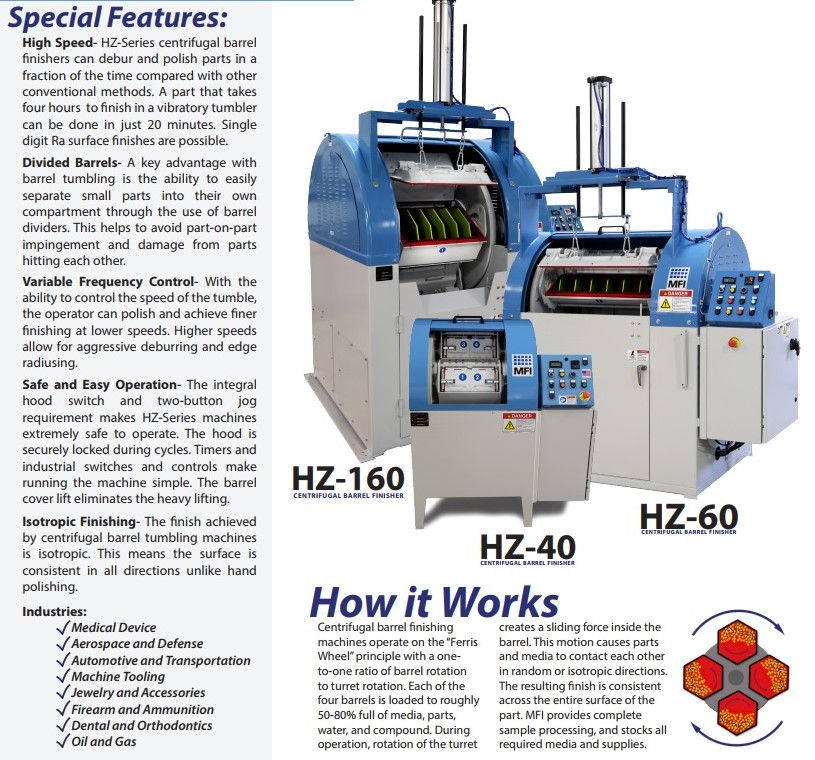
Our process engineering team has applied years of experience to providing finishing solutions to the jewelry, dental, automotive, aerospace, screw machining and other small parts. We are the small part finishing and polishing experts.
See the video below for a demonstration of the Centrifugal Iso-Finishing process...
What kind of parts are being deburred, finished and polished with Centrifugal Iso-Finishing?
High-speed and Hands-free Deburring and Super Iso-Finishing Precision Components from many Industries. The industries served include:
• Medical Implants and Orthopedic Devices
• Dental and Orthodontic Parts
• Aerospace Engine Components
• Aerospace Airframe and Structural Components
• Automotive Engine and Powertrain Components (Isotropic Finishing)
• High-Performance Motorsports and Powertrain (Isofinishing)
• Motorcycle engine and powertrain
• Machine Tooling,
• Metal 3D Printed Parts
• Plastic 3D Printed Parts
• Injection Moldings and Machined Plastics
• Springs
• Acrylic and Acetate Polishing
• Precious Jewelry and Fashion Accessory Polishing
• Screw Machine Part Deburring and Super-Finishing
• Eyewear Components
• Firearms and ammunition
• Metal Injection Molded Parts (MIM)
• Investment Castings
• Powdered Metal Parts Smoothing and Polishing
• Deflashing and smoothing of plastics and rubber
• Surface Burnishing for Compressive Stress
Ask about the (free) sample part processing program
See also our sample part processing form here: https://lnkd.in/guGnPZG
Mass Finishing technology for deburring, finishing and polishing of machined and manufactured parts and components
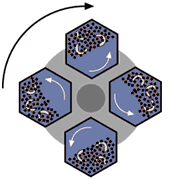
Centrifugal Isotropic Finishing (CIF) is a high-energy finishing method, which has come into widespread acceptance in the last few years. Although not nearly as universal in application as vibratory finishing, a long list of important CBF applications have been developed in the last few decades.
Similar in some respects to barrel finishing, in that a drum-type container is partially filled with media and set in motion to create a sliding action of the contents, CBF is different from other finishing methods in some significant ways. Among these are the high pressures developed in terms of media contact with parts, the unique sliding action induced by rotational and centrifugal forces, and accelerated abrading or finishing action. As is true with other high energy processes, because time cycles are much abbreviated, surface finishes can be developed in minutes, which might tie up conventional equipment for many hours.
Centrifugal Barrel Finishing principles – high-intensity finishing is performed with barrels mounted on the periphery of a turret. The turret rotates providing the bulk of the centrifugal action, the barrels counter-rotate to provide the sliding abrasive action on parts.
The principle behind CBF is relatively straightforward. Opposing barrels or drums are positioned circumferentially on a turret. (Most systems have either two or four barrels mounted on the turret; some manufacturers favor a vertical and others a horizontal orientation for the turret.) As the turret rotates at high speed, the barrels are counter-rotated, creating very high G-forces or pressures, as well as considerable media sliding action within the drums. Pressures as high as 50 Gs have been claimed for some equipment. The more standard equipment types range in size from 1 ft3 (30 L) to 10 ft3, although much larger equipment has been built for some applications.
High-speed and hands-free Centrifugal Iso-Finishing can deburr, finish and polish all types of small manufactured parts much faster and efficiently than conventional vibratory and rotary barrel finishing
Media used in these types of processes tend to be a great deal smaller than the common sizes chosen for the barrel and vibratory processes. The smaller media, in such a high-pressure environment, are capable of performing much more work than would be the case in lower energy equipment. They also enhance access to all areas of the part and contribute to the ability of the equipment to develop very fine finishes. In addition to the ability to produce meaningful surface finish effects rapidly, and to produce fine finishes, CBF has the ability to impart compressive stress into critical parts that require extended metal fatigue resistance. Small and more delicate parts can also be processed with confidence, as the unique sliding action of the process seems to hold parts in position relative to each other, and there is generally little difficulty experienced with part impingement. Dry process media can be used in certain types of equipment and is useful for light deburring, polishing, and producing very refined isotropic super-finishes.
See also: dryfinish.wixsite.com/iso-finish for additional part finishing applications.
See examples of part-finishing performed with Centrifugal Iso-Finishing processes below...
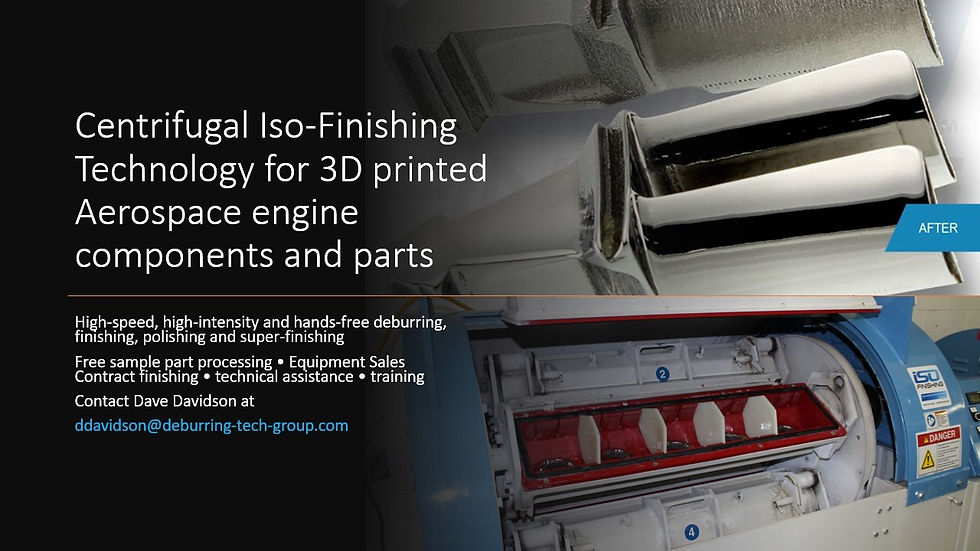

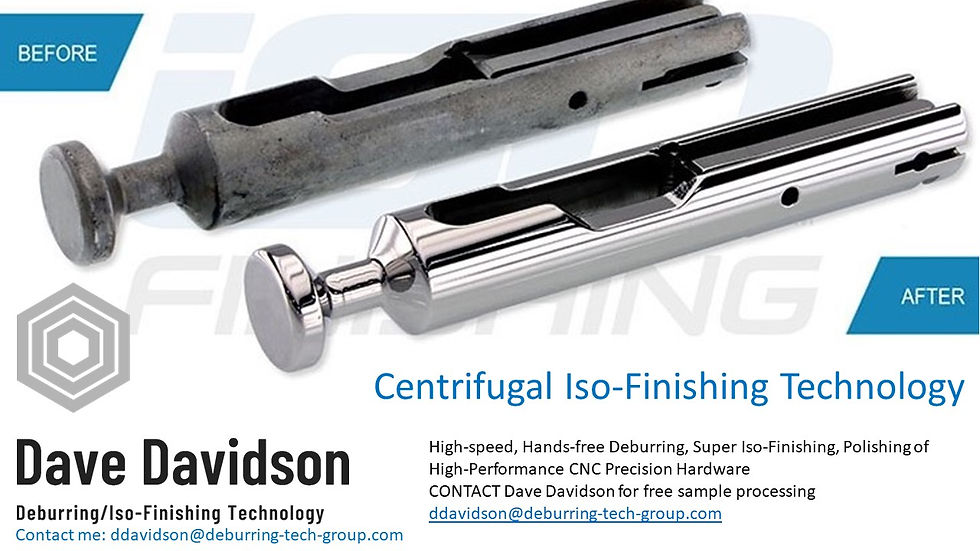
Comments