Centrifugal Isotropic Finishing for Improved Part Performance
- Dave Davidson
- Jul 26, 2014
- 11 min read
(Above) Automotive Parts Finished with Isotropic Micro-Finishing. Photo Credit: Mark Riley, BV Products
by Dave Davidson (dryfinish@gmail.com) and Jack Clark (jclark@surfaceanalytics.com)
SEE THE PROCESS IN ACTION, watch the video…

Centrifugal barrel machine for high speed and high-intensity mass media finishing
Centrifugal barrel finishing (CBF) is a high-energy finishing method, which has come into widespread acceptance in the last 25–30 years. Although not nearly as universal in application as vibratory finishing, a long list of important CBF applications have been developed in the last few decades. Similar in some respects to barrel finishing, in that a drum-type container is partially filled with media and set in motion to create a sliding action of the contents, CBF is different from other finishing methods in some significant ways. Among these are the high pressures developed in terms of media contact with parts, the unique sliding action induced by rotational and centrifugal forces, and accelerated abrading or finishing action. As is true with other high energy processes, because time cycles are much abbreviated, surface finishes can be developed in minutes, which might tie up conventional equipment for many hours.
This slideshow requires JavaScript.
The principle behind CBF is relatively straightforward. Opposing barrels or drums are positioned circumferentially on a turret. (Most systems have either two or four barrels mounted on the turret; some manufacturers favor a vertical and others a horizontal orientation for the turret.) As the turret rotates at high speed, the barrels are counterrotated, creating very high G-forces or pressures, as well as considerable media sliding action within the drums. Pressures as high as 50 Gs have been claimed for some equipment. The more standard equipment types range in size from 1 ft3 (30 L) to 10 ft3, although much larger equipment has been built for some applications.
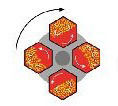
Centrifugal barrel principle. Four drums are mounted on the periphery of a rotating turret, the drums counter rotate creating a vigorous slide of media within the drum as well as high centrifugal pressure of the media against part surfaces.
Media used in these types of processes tend to be a great deal smaller than the common sizes chosen for barrel and vibratory processes. The smaller media, in such a high-pressure environment, are capable of performing much more work than would be the case in lower energy equipment. They also enhance access to all areas of the part and contribute to the ability of the equipment to develop very fine finishes. In addition to the ability to produce meaningful surface finish effects rapidly, and to produce fine finishes, CBF has the ability to impart compressive stress into critical parts that require extended metal fatigue resistance. Small and more delicate parts can also be processed with confidence, as the unique sliding action of the process seems to hold parts in position relative to each other, and there is generally little difficulty experienced with part impingement. Dry process media can be used in certain types of equipment and is useful for light deburring, polishing, and producing very refined superfinishes.
Practicality and questions of cost effectiveness often determine whether high-energy methods are selected over conventional barrel or vibratory processes. If acceptable surface finishes can be developed in a few hours, conventional equipment is usually the most economic alternative. CBF equipment’s strong suit is the ability to develop surface finishes that may require over-lengthy time cycles in conventional equipment and the ability to develop a wide range of special surface finishes required for demanding and critical applications.

Centrifugal Barrels can be segmented too separate parts during processing to prevent part-on-part contact. This is especially useful for larger or more delicate parts.
Centrifugal Disk Machines
Another high-energy finishing method that has become popular in recent years is the centrifugal disk. Most equipment is in the form of a cylinder or bowl with a spinning disk at the bottom. This disk propels the media upward against the interior sidewalls of the cylinder, which act as a brake, causing the mass to turn over and return to the center of the disk, where it is set in motion again. This unique media action is said to perform abrading operations at five to 10 times the speed of conventional vibratory action. As the machine is basically an open end chamber, in-process inspection and monitoring are possible. Faster time cycles can also reduce work in progress and make the equipment a good choice for manufacturing cells. In general, larger or lengthy parts are not good candidates for disk finishing and, at times, higher than usual media-to-part ratios must be maintained to avert part-on-part contact.
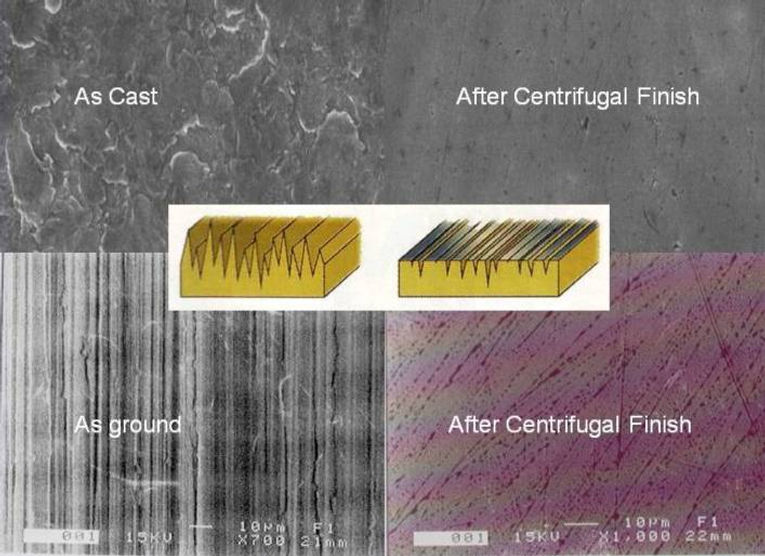
High magnification photography indicates that machined, ground and cast surfaces can be substantially changed from their initial characteristics by high energy finishing contributing to significant increases in part performance and life.
Equipment size ranges from 1/2 ft3 (15 L) bench-top models to 20 ft3 (600 L) floor machines. One critical area of attention on this equipment is the gap between the spinner disk and the ring located around the exterior of the disk. Particles or fines of media that are capable of lodging in this area may cause significant damage to certain types of equipment. Correct media maintenance and attention to water flow-through rates can be an important factor in extending the useful service life of main components. Some equipment has the ability to run either wet or dry process media. Many equipment models, however, are designed for dedicated use in either wet or dry finishing and should not be used in the other mode without extensive consultation with the manufacturer.
Spin/Spindle Finish Equipment

An abrasive mass finishing media used for “roughing” or cutting in mass finishing machine finishing operations.
Spindle finishing is performed by fixturing parts at the end of a (stationary, rotating, planetary, or oscillating) spindle, and arranging for the part to be immersed in a mass of fine media, which may be vibrating, stationary, or directed at the workpiece by a spinner arrangement or rotation of the entire media chamber. As all parts must be fixtured, impingement from part-on-part contact is nonexistent. Time cycles can be very short, ranging from a few seconds to a few minutes. Equipment from various manufacturers may feature single or multifixture capabilities. Types of operations vary from heavy abrasive operations for deburring and stock removal, to the use of very fine dry polishing media in some equipment to develop color-buff-type finishes. One recent development in spindle finishing is the turbofinish method, which involves the high-speed rotation of components in a fluidized bed of fine abrasive or polishing material.
MASS FINISHING MEDIA
Media can be generally defined as the loose material contained in the work area of a mass finishing machine, which, when in motion, performs the work desired on part surfaces. Media may be natural or synthetic, abrasive or nonabrasive, random or preformed in shape. Much of the versatility inherent to mass finishing processes can be traced to the wide array of media types, sizes, and shapes available to industry. What follows is a rundown of the more commonly used media types.

Parts of all sizes, shapes and compositions have been deburred, edge-finished, surface conditioned and even polished using mass finishing methods such as centrifugal barrel finishing. These parts exhibit isotropic surface conditions that can extend service life and improve function.
Natural/Mineral Media
Crushed and graded stone was once the predominant source for tumbling abrasives in the early days on barrel finishing. Raw source material included both limestone and granite. Some naturally sourced materials still find some barrel finishing applications today, such as corundum and novaculite. As a general rule, problems with fracturing, rapid wear and attrition rates, lodging, and disposal of the high amount of solid or sludge waste material created mitigates against crushed and graded mineral materials being an effective media for most applications.
Agricultural Media

Larger capacity CBF machine designed for superfinishing and polishing of cam and crankshafts, is said to accomodate 42 inch shafts.
A variety of granular media such as ground corn cob, walnut shell, pecan shell, sawdust, and wooden pegs are used in all of the equipment discussed. These dry process media are used in conjunction with various fine abrasive compounds similar to compounds that might be used in buffing applications. These media are often used in secondary cycles, after initial cutting and smoothing, to produce very fine reflective finishes. Attractive decorative finishes can be produced for jewelry and other consumer articles and, by extension, very low Ra finishes can be produced for precision industrial components.
Preformed Media
These media have largely replaced the crushed and graded mineral materials mentioned above. Media preforms are made from either extruded ceramic/abrasive shapes, which are fired, or resin-bonded, or which have been molded. The preform concept was an important one for the finishing industry. Unlike the more random shaped mineral media, size and shape preform selection could prevent media lodging and promote access to complex part shapes. The uniformity and predictable wear rates of the media also made it possible to prevent both lodging and separation problems caused by undersized, worn media. A wide variety of shapes have been developed by various manufacturers over the years to accommodate these requirements, including cones, triangles, angle-cut cylinders, wedges, diamonds, tristars, pyramids, arrowheads, and others. Ceramic media are generally harder and more abrasive and are customarily used for more aggressive applications. Plastic media, as a rule, are somewhat softer and capable of producing finer finishes.
Burnishing Media
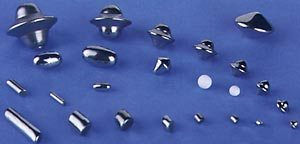
Steel burnishing media, is used in some systems to improve surfaces after initial abrasive cutting operations, unlike polishing, burnishing produces its effects by a compressive alteration of surface peaks and asperities, it also has a tendency produce substantial work-hardening of surfaces.
Media made from case hardened steel, stainless steel, and other formulations are used widely in barrel and vibratory equipment to produce burnished surfaces. These media are very heavy (300 lb/ft3 versus 100 lb/ft3 for ceramic media) when compared with other media types and are nonabrasive in nature. It should be noted that not all vibratory equipment can turn or roll steel media. Because of the weight, enhanced or heavier duty equipment may be necessary. The media performs by peening or compressive action; surface material is not removed, as is the case with abrasive media. Burnishing processes with steel media can be used either to develop reflective decorative finishes or provide functional finishes. One attribute of burnishing processes is that part surfaces are often work-hardened, which can extend the service life of components in moving assemblies. Steel media can be extremely long lasting, if care is taken to prevent corrosion of surfaces while in use and/or storage. Nonabrasive porcelain media are also used for some burnishing procedures and are prevalent in some centrifugal applications.
COMPOUNDS

Prepared aluminum oxide or sintered bauxite nugget media is used in high energy machinery to produce burnishing and cold hardening effects on many parts. Part surfaces usually must often be prepared with an abrasive operation prior to this burnishing step, which produces substantial cosmetic and aesthetic improvement in addition to the functional surface changes.
Many abrasive and burnishing applications use water with specially formulated compound additives. The proper selection and dosage of these additives (in either liquid or dry powder form) can have a critical effect on the viability of the process. These compounds perform an assortment of functions including water conditioning or softening, pH control, oil/soil and metallic and abrasive fine suspension to prevent redeposition on part surfaces, rust inhibition, cleaning, foam development or control, as well as media lubricity control. Some special compounds are used to chemically accelerate finishing cycle times; some of these may be intensely caustic or corrosive and may require some special handling.
Below is excerpted from SME Technical Paper MR79-569 by J. Bernard Hignett
[ed. note: Harperizer and Harperized are trade names that refer to a specific OEM’s brand of centrifugal barrel finishing equipment]
Metal fatigue is the most common cause of fracture in metal components. It is usually caused by numerous repeated applications of low stress—stress much lower than that needed for fracture in a single application. The higher the stress, however, the fewer applications are needed to cause failure. It follows that fatigue failure will be most cannon in components that are highly stressed and subject to repeated applications of stress in their functioning. A fatigue crack usually starts because the tensile componentof stress at the surface of the material is too high. It is thus beneficial to impart compressive stress of components to oppose any tensile stress towhich the component may be subjected in service.
Edge and surface finishing improvement can reduce the risk of fatigue failure. Surface imperfections can act as stress raisers and removal of these will invariably improve performance of any highly stressed part. For critical components it is desirable to achieve very high surface finishes to facilitate inspection for stress raises. Removal of burrs and uniform radiusing of all sharp edges and corners will similarly improve performance.
As has already been discussed, the CBF process can simultaneously deburr, edge radius and surface finish an immense range of components. It can also impart very high compressive stresses uniformly to the parts while edge .land surface finishing so offering unique capability of improving the resistance to fatigue failure of many highly stressed parts. The capability to improve resistance to fatigue failure is demonstrated by the results of some tests made by a manufacturer of stainless steel coil springs which were taken from a standard production run, Half of the components had the conventional finishing process of barreling, followed by shot peening, and the other half were processed in a centrifugal barrel machine for 20 minutes. The springs were tested to failure by compressing them from 1.104″ length to .730″, corresponding to a stress change from 9 to about 50,000 psi. The results were that all springs finished by the conventional method failed at between 160,000 and 360,000 cycles. The springs that had been Harperized failed at between 360,000 and 520,000 cycles, an average performance improvement of 60%.
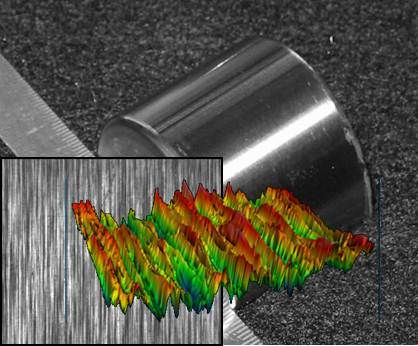
This photo shows bearing surface as seen by 2D and 3D scanning measurement. The surface peaks and asperities are typical of machined or ground surfaces. Photo courtesy of Jack Clark, Surface Analytics and Colorado State University Mech Eng Dept.
The tests indicated a benefit potentially greater than mere improvement of resistance to fatigue failure. It was noted that some of the parts that were processed in centrifugal barrel equipment had clearly visible surface defects or inclusions. Such defects were not visible in the parts that had been barreled and peened. It was the parts with the visible defects which were always those that failed below 400,000 cycles so that if in inspection department were instructed ot to accept parts with such defects, then performance of the springs put into service would be of consistently much higher quality.
Even more striking results were observed during a series of tests in another set of production springs of a somewhat different type. The springs which were not processed in CBF equipment all failed life tests before 600,000 cycles. None of the springs which were Harperized had failed at 800,000 cycles, the limit of the test.

After high energy centrifugal finishing the surfaces are far more functional for the bearing application. More isotropic, more plateaued, more negatively skewed and have imparted a beneficial compressive stress. All of these attributes improving the load bearing and tribological properties of the part. Photo courtesy of Jack Clark, Surface Analytics. and Colorado State University Mech Eng Dept.
Using CBF markedly to improve resistance to fatigue failure by a combination of edge and surface finishing, together with imparted very high compressive stresses, is cheaper than finishing by conventional means and then shot peening. There are opportunities to improve the ultimate resistance to fatigue failure of many parts, and, of prime importance, enable much better quality control by facilitating inspection. There is no longer need for components to be designed to allow a proportion of parts to fail prematurely due to surface defects. Of course, the technique has wide use for spring components, for instrument parts, for bearings and throughout the aerospace industry. There are also many opportunities to utilize improved and more consistent performance to design some of the cost out of many more mundane components within the metalworking industry, in particular, some automotive parts.
Further reading: Internet resources
(1) “Isotropic Mass Finishing for Surface Integrity and Part Performance”, Article From: Products Finishing, Jack Clark, from Surface Analytics, LLC and David Davidson, from SME Deburr/Finish Technical Group, Posted on: 1/1/2015, [Barrel, vibratory, centrifugal and spindle finish can improve part performance and service life.] http://www.pfonline.com/articles/isotropic-mass-finishing-for-surface-integrity-and-part-performance
(2) “Turbo-Charged Abrasive Machining Offers Uniformity, Consistency” Article From: Products Finishing, by: Dr. Michael Massarsky, President from Turbo-Finish Corporation, and David A. Davidson, from SME Deburr/Finish Technical Group. Posted on: 6/1/2012. [Method can deburr, produce edge contour effects rapidly] http://www.pfonline.com/articles/turbo-charged-abrasive-machining-offers-uniformity-consistency
(3) “Turbo-Abrasive Machining and Finishing”. MANUFACTURING ENGINEERING – Aerospace Supplement, by: Dr. Michael Massarsky, President from Turbo-Finish Corporation, and David A. Davidson, from SME Deburr/Finish Technical Group. [Method first developed for the aerospace industry can improve surface integrity and part performance] http://www.slideshare.net/dryfinish/turboabrasive-machining-me-aerospace-supplement-reprint
(4) “The Role of Surface Finish in Improving Part Performnce”, MANUFACTURING ENGINEERING, by Jack Clark, Surface Analytics.com and David A. Davidson, from SME Deburr/Finish Technical Group. http://www.slideshare.net/dryfinish/november-2012-f4-deburring-1-final
(5) “Free Abrasives Flow for Automated Finishing”, MANUFACTURING ENGINEERING, , by: Dr. Michael Massarsky, President from Turbo-Finish Corporation, and David A. Davidson, from SME Deburr/Finish Technical Group. [Exciting new methods of surface finishing that go beyond deburring to specific isotropic surface finishes that can increase service life] http://www.slideshare.net/dryfinish/october-2013-f2-deburring-1
(6) Turbo-Abrasive Machining Demonstration Video: https://www.youtube.com/watch?v=jYxqCxMIHNo
(7) SME Spokane, WA Factory Floor video, Centrifugal Finishing in the Precision Machine Shop: Demonstration) https://www.youtube.com/watch?v=dUdKjaysTYM
AUTHOR BIOGRAPHY – David A. Davidson, [dryfinish@gmail.com]
Mr. Davidson is a deburring/surface finishing specialist and consultant. He has contributed technical articles to Metal Finishing and other technical and trade publications and is the author of the Mass Finishing section in the current Metal Finishing Guidebook and Directory. He has also written and lectured extensively for the Society of Manufacturing Engineers, Society of Plastics Engineers, American Electroplaters and Surface Finishers Association and the Mass Finishing Job Shops Association. Mr. Davidson’s specialty is finishing process and finishing product development.
#edgeconour #Burnishing #SurfaceFinishing #radiusing #dryprocessfinishing #surfaceplateauing #surfacetopography #massfinishing #NontraditionalFinishing #abrasive #deburring #TumblingMassFinishing #edgefinish #highenergyfinishing #compressivestress #metalfatigueprevention #centrfugalbarrelfinishing #mechanicalfinishing
Comments