Considerations for Developing Surface Finishing Processes for Additive Manufactured Parts
- Dave Davidson
- Jun 24, 2020
- 7 min read
Updated: May 29, 2021
Dave Davidson | Deburring/Finishing Technologist | Deburring/Finishing Tech Group ddavidson@deburring-tech-group.com | dryfinish.wixsite.com/iso-finish

Shown below is an excerpt of an SBIR solicitation for surface finishing solutions that might make additive manufactured parts more useful for use in commercial, industrial and technical settings. It gives a good overview of the challenges being faced by manufacturers, service bureaus and end-users of the technology.
Topic #: N182-126 Title: Effect of Surface Finish and Post-Processing on the Fatigue Life of Additively Manufacturing Parts Technology Areas: Materials / Processes Acquisition Program: Quality Metal Additive Manufacturing (QUALITY MADE)
OBJECTIVE: Develop a surface finishing process that can efficiently post-process additively manufactured metallic components to a consistent finish while enhancing material properties and part performance.
DESCRIPTION: Metal additive manufacturing (AM) is increasingly being considered for use on Marine Corps platforms and for parts with increasing complexity, strength, and performance requirements. The 3-dimensional layered construction, variations in powder bed heights across the bed, and other factors like the Marangoni effect due to surface tension gradients may cause marked surface roughness, which affects the resulting part performance [Ref 1]. Additionally, AM processes allow designers to break free from traditional design constraints and optimize the part topology, leading to parts with less material and greater complexity. The wider adoption of AM may be limited by the surface finish being produced by the various AM techniques and the extent of post-processing required after fabrication. The ability to control the surface finish is a function of the AM technique used, the manufacturing process parameters, material, geometry of the part, direction the part is oriented during the build, and the post-processing techniques utilized. Currently, the conventional post-processing machining and surface polishing and other best practices being performed are laboriously expensive and high-risk when dealing with the highly complex geometries and shapes associated with AM.
High cycle fatigue requires surface finishes of 0.2-µm or 8-µin as defined in ASTM E466 Appendix X1 and may be achieved through hand finishing [Ref 9]. The surface finish is especially of concern as advanced topology optimization strategies involve reducing excess material to retain only a complicated “spider web”-like structure where mechanical properties and part performance require it, limiting the accessibility to reach and access key areas for the desired surface finish through conventional methods. Topology optimization frequently results in hard to reach surfaces that further necessitate technology advancements. Further, it has been demonstrated that current techniques affect the endurance, strength, and fatigue limits in additively manufactured parts [Ref 2]. There is a growing concern that current post-processing techniques negatively impact mechanical properties in these complex regions. Additionally, post-processing for surface finish plays a key role in uncertainty quantification (UQ) of mechanical properties and is used in empirical modeling of the parts/processes.
These factors point to the growing need in the Navy and Marine Corps to simultaneously reduce the cost of post-processing while maintaining or enhancing material and part performance with post processing technologies. The ability to control manufacturing process parameters to better enhance surface finish for deposited materials are being addressed by other efforts, such as the Office of Naval Research (ONR)’s Quality Metal Additive Manufacturing program, but the need to enhance surface finish may always be required. This SBIR topic is specifically seeking novel technologies that efficiently post-process additively manufactured parts to improve the surface finish of complex additively manufactured parts while minimizing any negative impacts of post-processing. Naval materials of interest include titanium, aluminum, nickel, aluminum, bronze, and stainless steel alloys.
PHASE I: Report on the fatigue life and impact of surface finishing on additively manufactured alloys of interest to the Navy / Marine Corps (e.g., Al alloys, Ti-6Al-4V, 316L). Develop concepts for a new post-processing technology on AM surface finishes and fatigue life. Demonstrate the technical feasibility of a process to reliably deliver a uniform surface finish on AM components. During Phase I, ONR will provide exemplar 3D models and/or parts to guide Phase II development. Develop a Phase II plan.
PHASE II: Based on Phase I results and guidance in preparation for Phase II, mature proposed post-processing technologies for AM alloy parts of interest to the Navy / Marine Corps manufactured using powder bed fusion and/or directed energy deposition techniques. Using a design of experiments approach for exemplar technology optimized parts [Ref 8], collect sufficient experimental results to develop an empirical model and UQ that can predict fatigue life based on post-processing surface treatment and mechanical loading.
PHASE III DUAL-USE APPLICATIONS: Support the Marine Corps and Navy in transitioning the technology for use in intermediate- and depot-level maintenance to deliver required surface finish features. Mature and support a rapid process to assist in the qualification and certification of additively manufactured parts through understanding and UQ of reliability frameworks. Simultaneously explore the numerous dual-use applications requiring surface finishing for AM in industries such as aerospace, automobile manufacturing, medical implants, and weapon manufacturing.
REFERENCES:
1. Townsend, A., Senin, N., Blunt, L., Leach, R.K., Taylor, J.S. Surface texture metrology for metal additive manufacturing: a review, Precision Engineering, 46, October 2016, pp. 34-47, sciencedirect.com/science/article/pii/S0141635916300721
2. Sames, W. J., List, F. A., Pannala, S., Dehoff, R. R., & Babu, S. S. The metallurgy and processing science of metal additive manufacturing. International Materials Reviews, 61, March 7, 2016, pp. 315-360,
3. Bagehorn, S., Wehr, J., & Maier, H. J. Application of mechanical surface finishing processes for roughness reduction and fatigue improvement of additively manufactured Ti-6Al-4V parts. International Journal of Fatigue, 102, September 01, 2017, pp. 135-142. sciencedirect.com/science/article/pii/S0142112317302153
4. Ma, C., Andani, M. T., Qin, H., Moghaddam, N. S., Ibrahim, H., Jahadakbar, A., Amerinatanzi, A., ... Ye, C. Improving surface finish and wear resistance of additive manufactured nickel-titanium by ultrasonic nano-crystal surface modification. Journal of Materials Processing Technology, 249, November 01, 2017, pp. 433-440.
5. Mohammadian, N., Turenne, S., & Brailovski, V.. Surface finish control of additively-manufactured Inconel 625 components using combined chemical-abrasive flow polishing. Journal of Materials Processing Tech, 252, February 01, 2018, pp. 728-738. sciencedirect.com/science/article/pii/S0924013617304697
6. Alfieri, V., Argenio, P., Caiazzo, F., & Sergi, V. Reduction of surface roughness by means of laser processing over additive manufacturing metal parts. Materials, 10(1), January 2017, 30. ncbi.nlm.nih.gov/pmc/articles/PMC5344551
7. Townsend, A., Senin, N., Blunt, L., Leach, R. K., & Taylor, J. S. Surface texture metrology for metal additive manufacturing: a review. Precision Engineering, 46, October 2016, pp. 34-47. sciencedirect.com/science/article/pii/S0141635916300721
8. Example topology optimized part, insidemetaladditivemanufacturing.com/blog/design-for-slm-topology-optimisation-of-metallic-structural-nodes-in-architecture-applications, Accessed February 2018
9. ASTM E466-15, Standard Practice for Conducting Force Controlled Constant Amplitude Axial Fatigue Tests of Metallic Materials, ASTM International, West Conshohocken, PA, 2015, astm.org/Standards/E466.htm
One potential technology that has proved useful for addressing problems related to the need for lower micro-inch surface finishes while helping to improve metal fatigue failure resistance is Centrifugal Iso-Finishing technology...
Centrifugal Iso-Finishing Technology. Centrifugal isotropic finishing (CIF) is a high-energy finishing method, which has come into widespread acceptance in recent years. and a long list of important CIF applications for precision machined and additive parts have been developed in the last few years.

Similar in some respects to barrel finishing, in that a drum-type container is partially filled with media and set in motion to create a sliding action of the contents, CBF is different from other finishing methods in some significant ways. Among these are the high pressures developed in terms of media contact with parts, the unique sliding action induced by rotational and centrifugal forces, and accelerated abrading or finishing action. As is true with other high energy processes, because time cycles are much abbreviated, surface finishes can be developed in minutes, which might tie up conventional equipment for many hours.
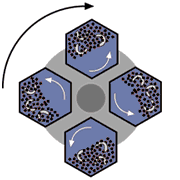
The principle behind CIF is relatively straightforward. Opposing barrels or drums are positioned circumferentially on a turret. (Most systems have either two or four barrels mounted on the turret; some manufacturers favor a vertical and others a horizontal orientation for the turret.) As the turret rotates at high speed, the barrels are counter-rotated, creating very high G-forces or pressures, as well as considerable media sliding action within the drums. Pressures as high as 50 Gs have been claimed for some equipment. The more standard equipment types range in size from 1 ft3 (30 L) to 10 ft3, although much larger equipment has been built for some applications.
Media used in these types of processes tend to be a great deal smaller than the common sizes chosen for barrel and vibratory processes. The smaller media, in such a high-pressure environment, are capable of performing much more work than would be the case in lower energy equipment. They also enhance access to all areas of the part and contribute to the ability of the equipment to develop very fine finishes. In addition to the ability to produce meaningful surface finish effects rapidly, and to produce fine finishes, CBF has the ability to impart compressive stress into critical parts that require extended metal fatigue resistance. Small and more delicate parts can also be processed with confidence, as the unique sliding action of the process seems to hold parts in position relative to each other, and there is generally little difficulty experienced with part impingement. Dry process media can be used in certain types of equipment and is useful for light deburring, polishing, and producing very refined isotropic super-finishes.
Below: Centrifugal Isotropic Finishing Operations Videos showing a multiple steps are used to take parts through coarse abrasive processing, smoothing and final polishing to achieve low micro-inch surface values on many different kinds of alloys.
Below is shown a factory floor video taken at a contract machining company that successfully uses Centrifugal Iso-Finishing for high-energy and hands-free deburring on a wide variety of machined components made from stainless steel, titanium, plastic, aluminum and other materials.
Below: Some examples of Centrifugal Iso-Finishing processes on additive manufactured parts. Other materials such as plastic, composites and carbon materials.
For additional technical information or (free) sample part processing Contact: Dave Davidson | Deburring/Finishing Technologist | Deburring/Finishing Tech Group | ddavidson@deburring-tech-group.com | dryfinish.wixsite.com/iso-finish
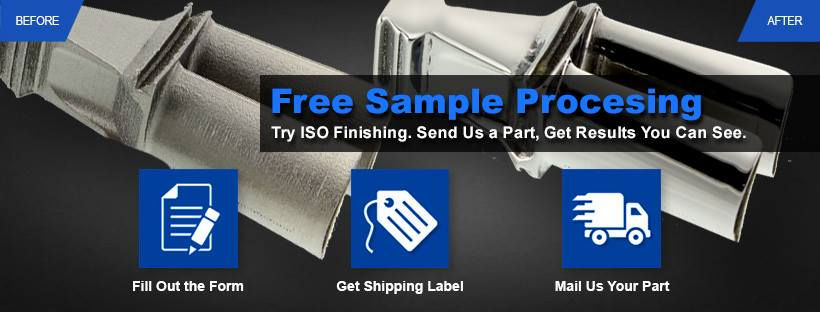
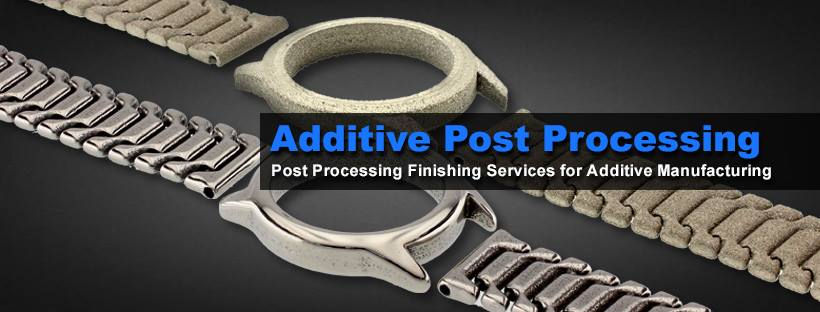

Centrifugal Iso-Finishing processes are also widely used on conventional parts from many
industries. Below is a selection of parts finished by one equipment manufacturer in a combination of wet processing (for grinding and smoothing) and dry polishing.


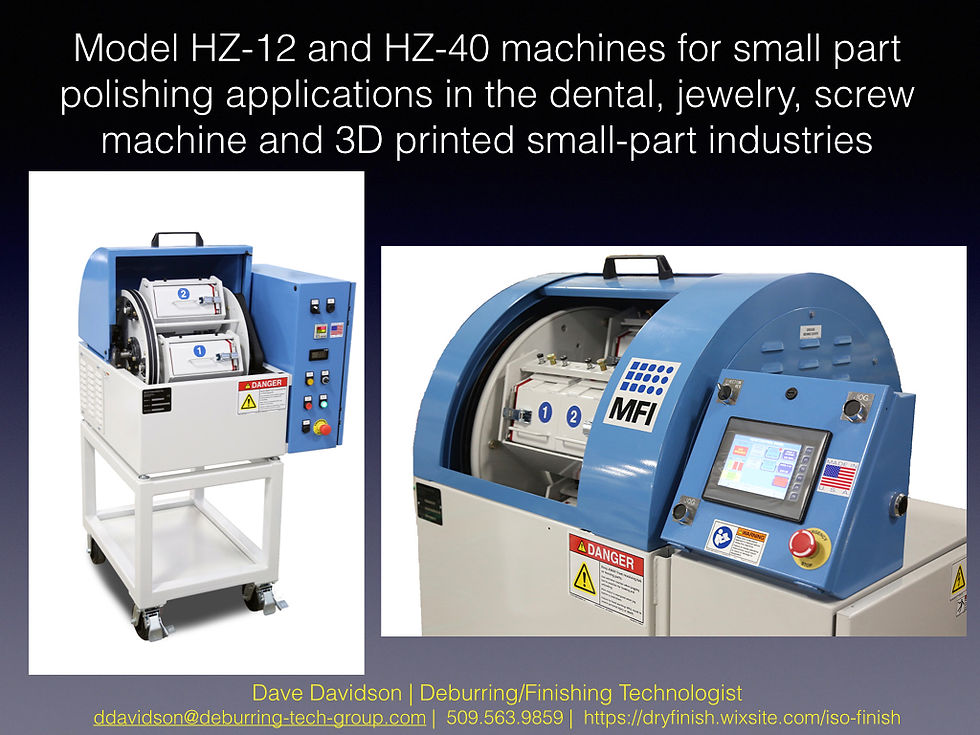

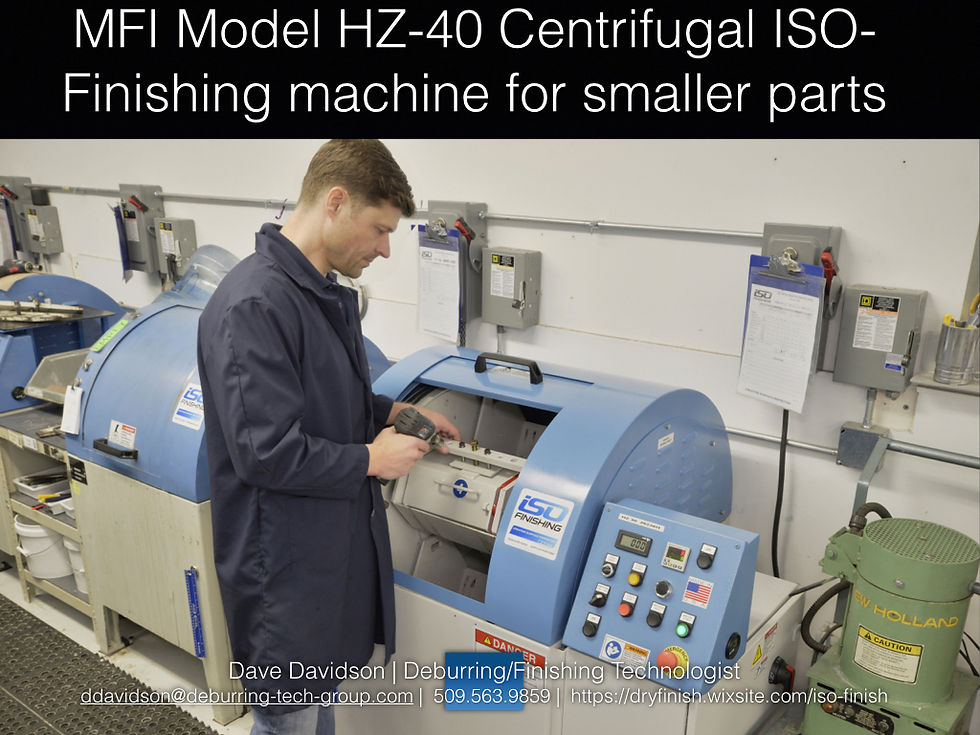

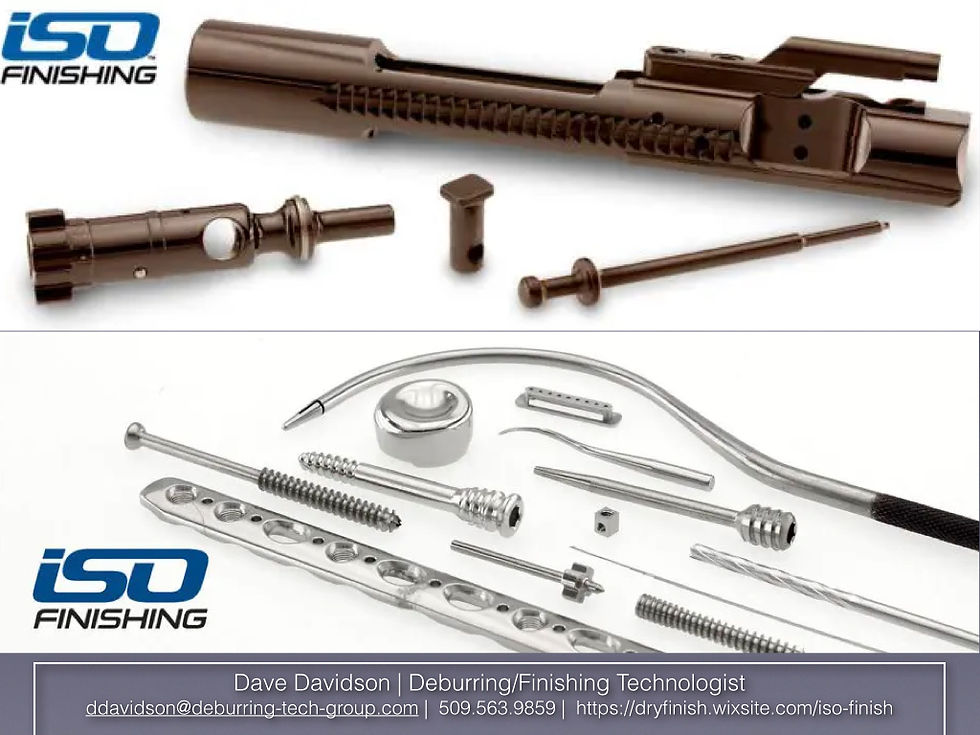
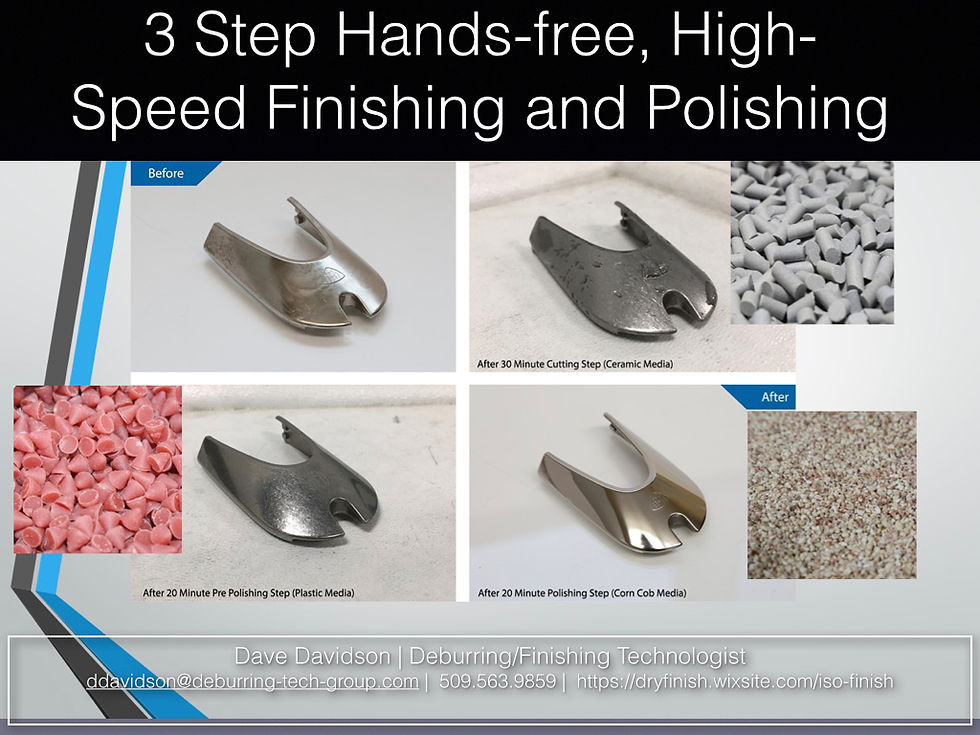

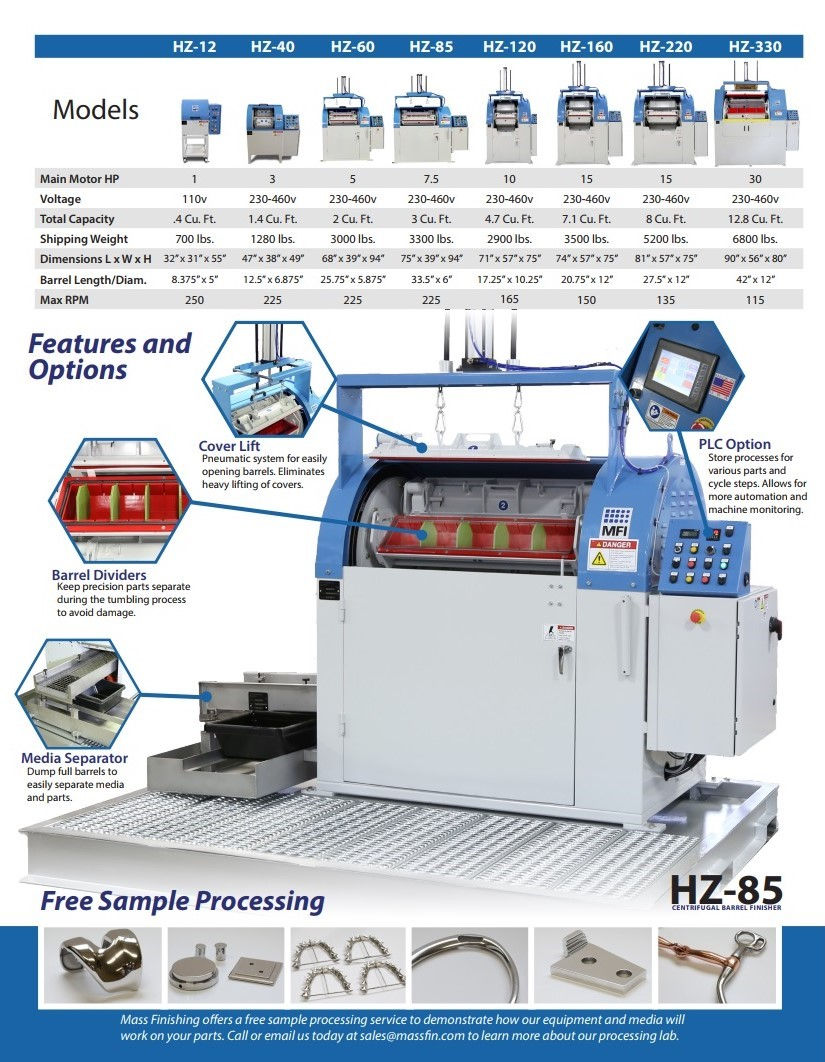
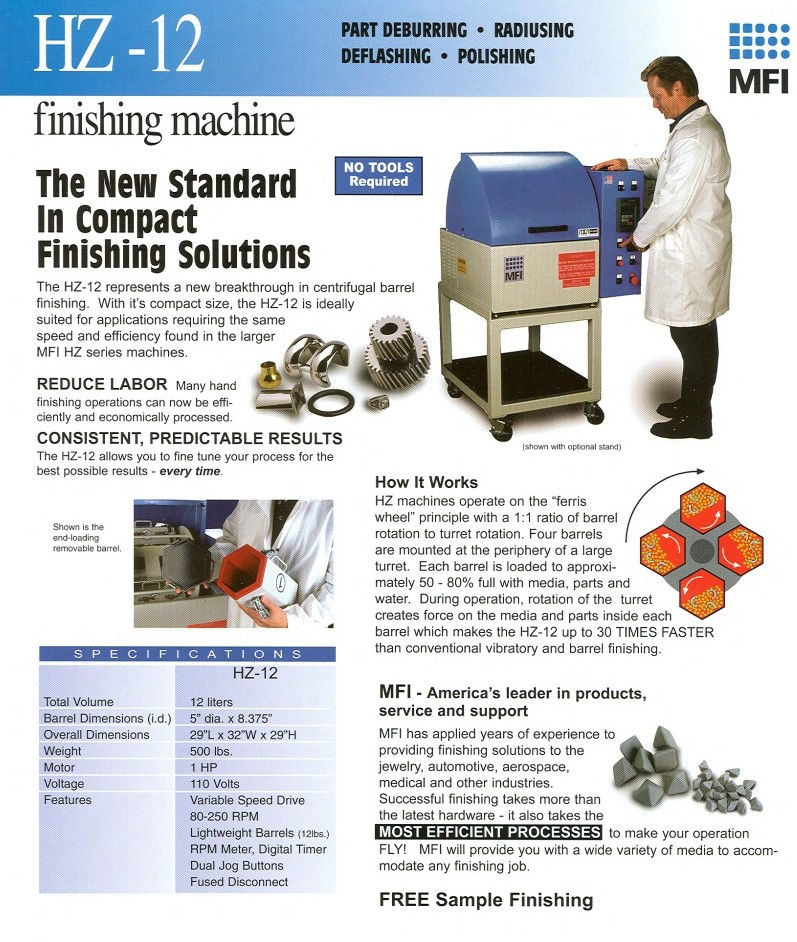
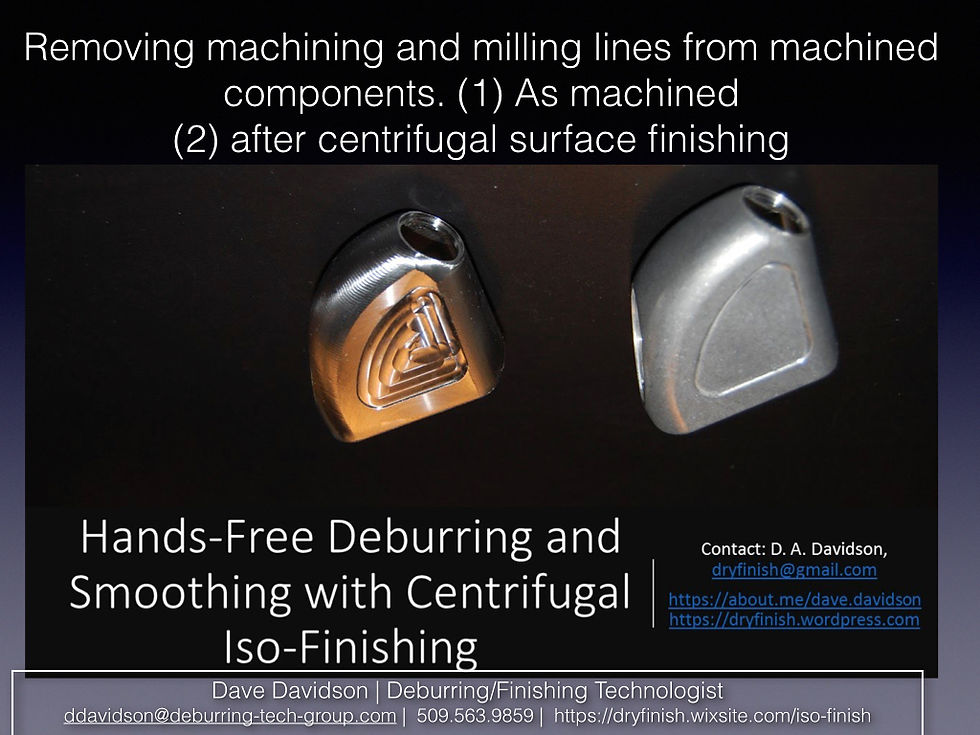
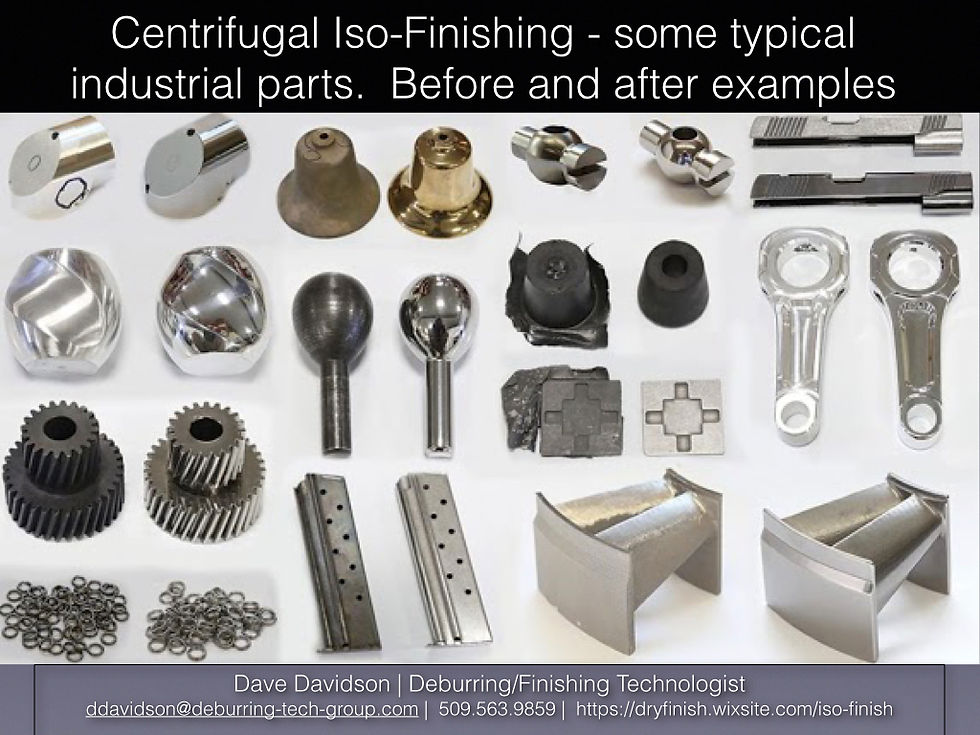
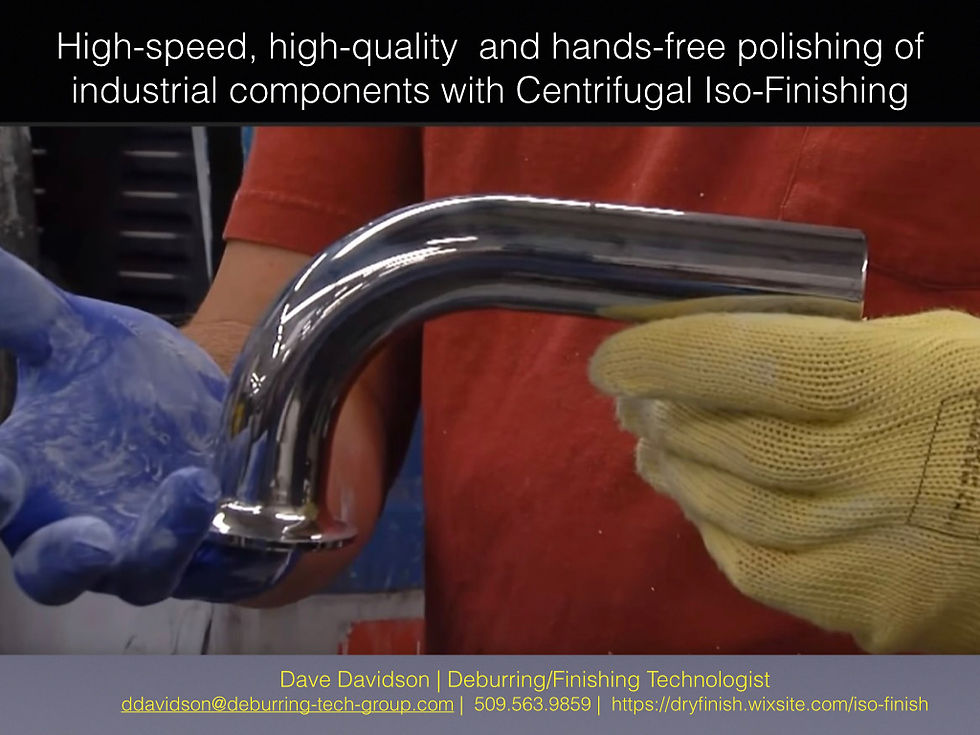

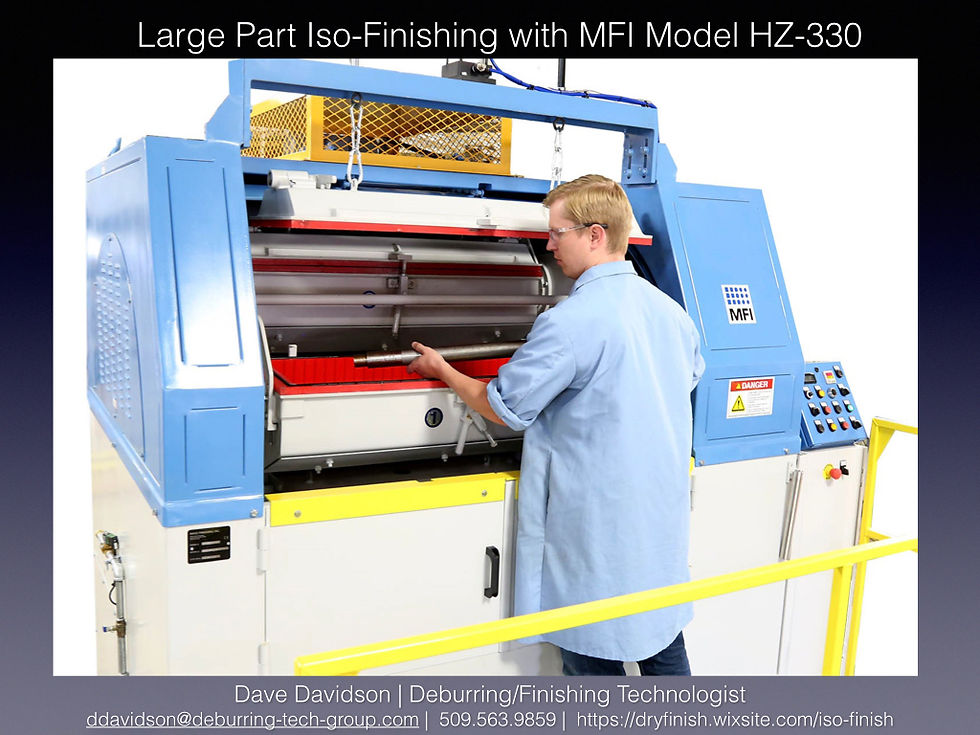
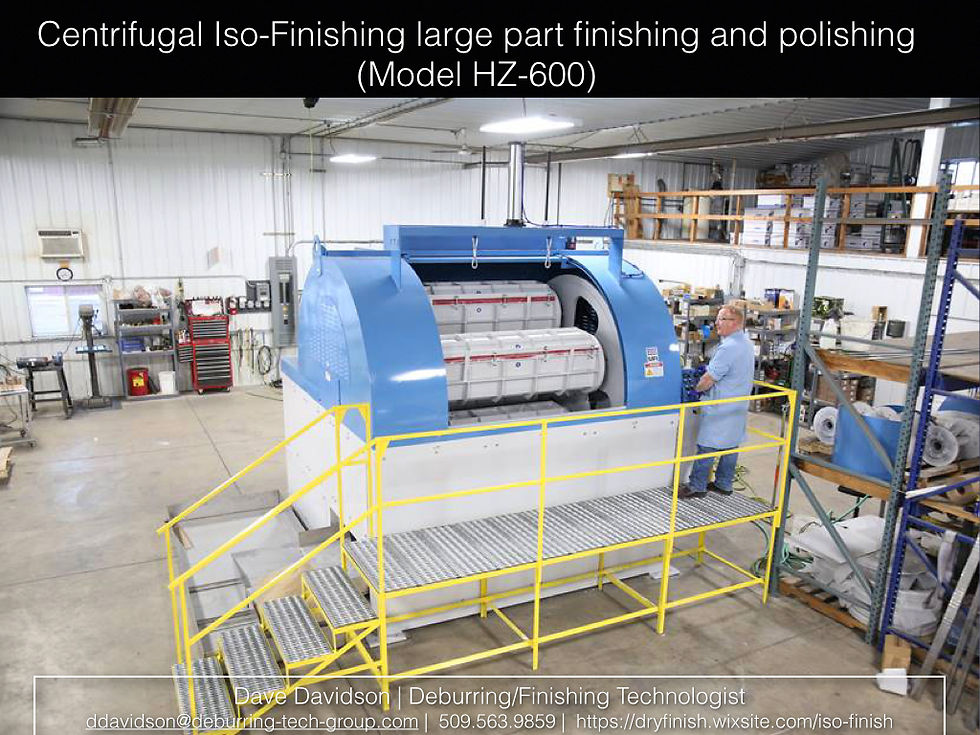

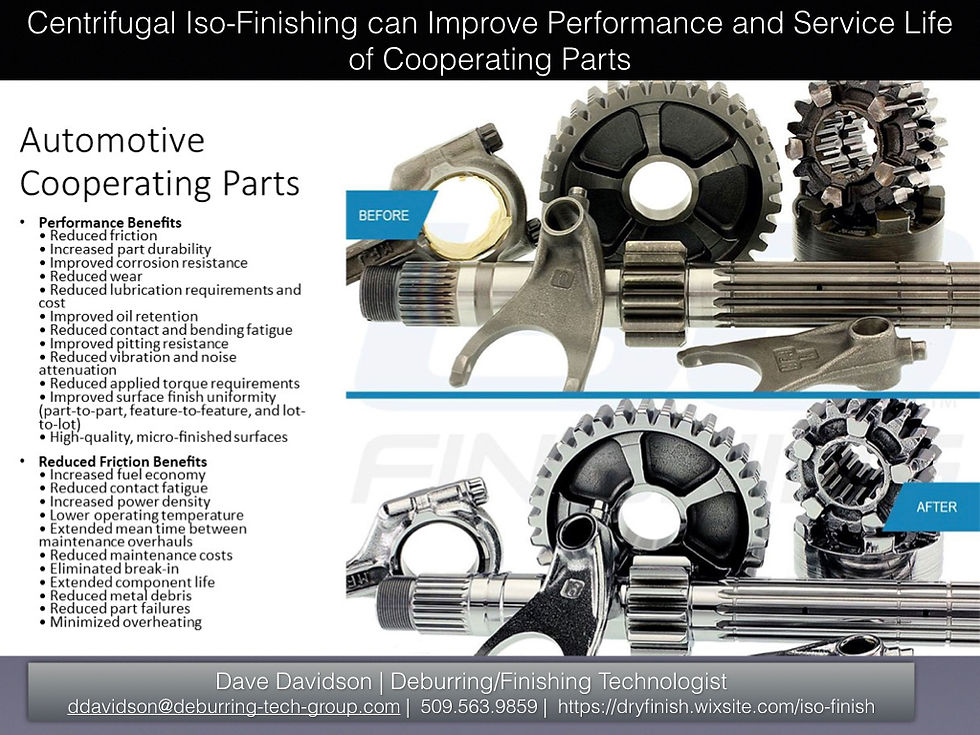

Comments