Deburring and Surface Finishing as a part of Manufacturing
- Dave Davidson
- Oct 9, 2011
- 4 min read

In many manufacturing applications, surface finish can play a critical role in the long term functionality, performance and longevity of parts, such as this bio-medical surgical implant. The correlation between surface finish and overall long-term part performance is often not well understood by the manufacturing and engineering community.
When presented with deburring and surface finishing problems, many manufacturers continue to reach for solutions that rely on out-of-date, time-consuming and labor-intensive methods. It is still not unusual to see precision parts and critical hardware being manually handled and edge and surface finishing operations being performed with abrasive hand tools, or manually controlled power tools that utilize coated abrasives or abrasive filaments. This situation often arises from insufficient planning and a lack of understanding what will be required to render the manufactured part or component acceptable for consumer use or end-user application. At the root of the problem is a manufacturing and design engineering culture that considers its work done when the part comes off the machining center or the fabricating machine. Too often, part edge and surface condition is simply someone else’s problem. In many cases not much thought is given to the problem until production is in full swing and parts start to fail quality assurance standards because they have burrs or undesirable surface conditions that not only affect function and performance but send costs through the roof.
This is a situation that deserves and is getting an increasing amount of scrutiny. It is a subject repeatedly discussed at the newly formed “Deburring, Edge-Finish, and Surface Conditioning Technical Group” sponsored by the Society of Manufacturing Engineers in Dearborn, MI. At one of the group’s monthly national teleconferences, Steven Alviti, a deburring and surface finish expert summarized his experience this way:
“This group has been needed for a long time now. The sentiments expressed at the phone conference still hold true to this day. I face the same scenario time after time. The company develops a new product, they cost the product, they work out the productivity to decide what machinery they need to supply the demand, they spend $500,000.00 – $1,000,000.00 for CNC machinery, they get orders and start producing, they now have product to ship — but it has a burr! Now we get the call, after they have thrown five or six people at the cell with microscopes, exact-o-knifes, files, sandpaper and worse, and have figured out that they are in a jam. Now we come up with a mechanical or automated solution, but it’s like pulling teeth to have them spend $10,000 or $20,000 on a solution that should have been part of the initial phase. What ever this group can do to bring mass finishing into the initial stages of engineering will be a benefit to all involved.”
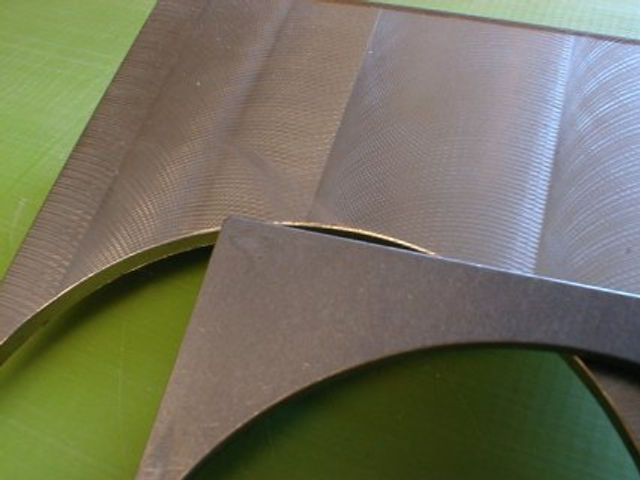
This photo vividly shows the difference between an as machined surface (the upper coupon with the fly-cutter milling) and the test coupon below which has had milling marks blended in, and a typical isotropic surface finish developed with centrifugal barrel finishing
The costs of neglecting to consider deburring and surface conditioning in production planning and engineering can be and often is – substantial. Frequently overlooked however, are the potentially serious problems that can develop from the ad hoc and interim solutions that are selected to deal with what now has become a manufacturing crisis. The manufacturers who resort to hand or manual finishing do not do so because of its cost, on a per piece basis, it is by far the most costly method of handling the problem – but often it is the most obvious solution and the easiest and the quickest to implement. Hiring some less skilled temporary employees, and arming them with hand tools to attack the problem may not be very imaginative, but it is certainly much less strenuous from an engineering perspective than approaching the budgetary, capital asset acquisition and purchasing processes for something as mundane as deburring and surface finishing equipment. The reason this problem persists into the 21st century, is that there is a very imperfect understanding of the hidden and more serious cost this manual and uncontrolled approach imposes. The first casualty of this manual approach is the investment the manufacturer has made, often in the millions, for precise and computer-controlled manufacturing equipment. The idea behind this investment was to have the ability to produce parts that are uniformly and carefully manufactured to exacting specifications and tolerances. At this point, in too many cases, the parts are then handed off to manual deburring and finishing procedures that will guarantee that no two parts will ever be alike.
This slideshow requires JavaScript.
ABOVE: Examples of Isotropic Micro-Finishing. Surface finishing for improving part performance and durability. [Pjotos by Mark Riley, BV Products]
Moreover, the increased complexity and precision requirements of mechanical products have reinforced the need for accurately producing and controlling the surface finish of manufactured parts. Variations in the surface texture can influence a variety of performance characteristics. The surface finish can affect the ability of the part to resist wear and fatigue; to assist or destroy effective lubrication; to increase or decrease friction and/or abrasion with cooperating parts; and to resist corrosion. As these characteristics become critical under certain operating conditions, the surface finish can dictate the performance, integrity and service life of the component.
The role of mass finishing processes (barrel, vibratory and centrifugal finishing) as a method for removal of burrs, developing edge contour and smoothing and polishing parts has been well established and documented for many years. These processes have been used in a wide variety of part applications to promote safer part handling (by attenuation of sharp part edges) improve the fit and function of parts when assembled, and produce smooth, even micro-finished surfaces to meet either functional or aesthetic criteria or specifications. Processes for developing specific edge and/or surface profile conditions on parts in bulk are used in industries as diverse as the jewelry, dental and medical implant industries on up through the automotive and aerospace industries.
Above: Centrifugal Barrel Equipment is used to produce Isotropic Finishes
This slideshow requires JavaScript.
Above: Part Finishing Gallery
Commentaires