Edge and Surface Preparation of Carbide and HSS Tooling with Centrifugal Isotropic Micro-Finishing
- Dave Davidson
- May 5, 2017
- 1 min read
Dave Davidson, Deburring/Finishing Specialist, dryfinish@gmail.com See also: https://dryfinish.wordpress.com/2017/02/23/centrifugal-isotropic-finishing-operations-on-precision-parts-video/
Background
1.1. For many decades there has been an awareness of cutting tool edge condition and tool surface finish and the effect it has on piece part quality and tool life. There have been many independent studies, tests, and implementations of edge conditioning methods to create extended life in turning, drilling, and milling cutter tooling – some published but most kept “secret” as a manufacturing advantage.
1.2 Some of the effects noted from this testing is that finishing processes, when applied to tooling can have a significant effect on overall tooling service life, the surface finish that the tool develops on the material being cut, the maximum spindle speed and feed rate the tool can run at. Reduction of and more consistent and predictable break in period with less chatter. Reduced heat build up on the tool from improved chip flow.
1.3 Improved edges and surfaces can have a substantial effect on coating performance. The better the finish, the better the coating as the new coatings conform closely to the surface texture of the tooling parent material
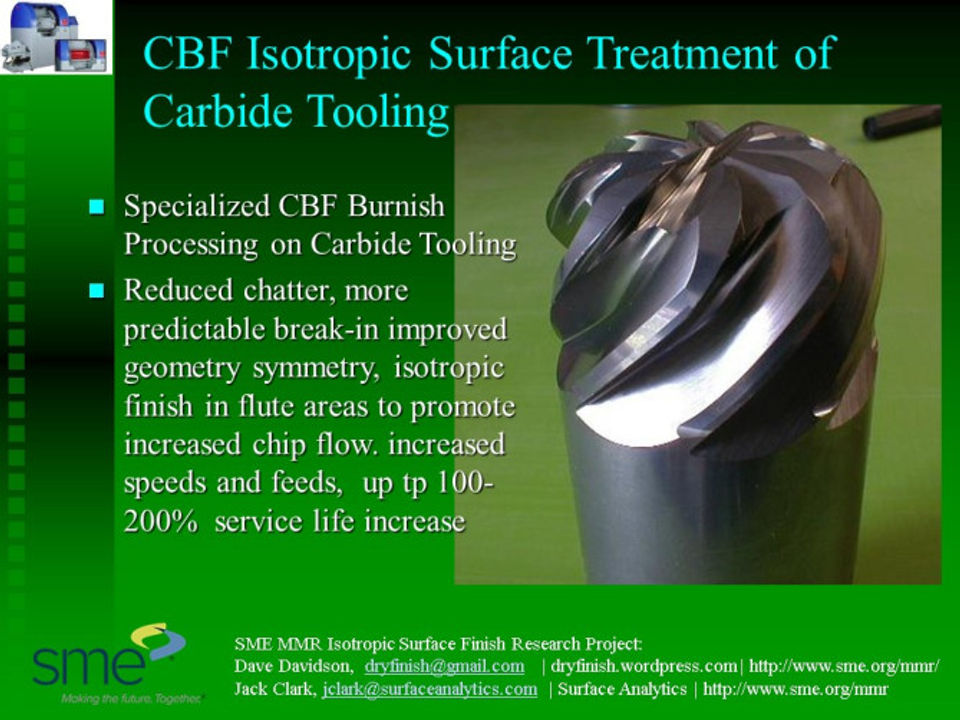

Contact us for information on free sample part processing at dryfinish@gmail.com.
FREE SAMPLE PROCESSING * CONTRACT FINISHING SERVICES * TURN-KEY FINISHING SYSTEMS
For additional information or sample processing information contact: by Dave Davidson – Deburring/Finishing Specialist SME Manufacturing C248 – Spokane, Washington Advisor: Machining/Material Removal Technical Community dryfinish@gmail.com | 509.230.6821 http://dryfinish.wordpress.com
Below is some process video footage demonstrations of high-speed centrifugal isotropic finishing. These automated edge and surface finishing methods are capable of producing very refined low micro-inch surfaces that can improve functional part performance and service life.
コメント