Fundamentals of Waste Water Treatment for Metal Finishing and Other Industrial Applications
- Dave Davidson
- Aug 31, 2017
- 13 min read
Updated: Jul 24, 2020
Dave Davidson, Contributing Editor | dryfinish@gmail.com | 509.230.6821 https://about.me/dave.davidson | https://dryfinish.wordpress.com
Editor’s note: The technical descriptions below were supplied by Chuck Case, President of Waste Water Engineers, Inc. Chuck is a very experienced system designer and Wastewater Engineers Inc. systems can be found at hundreds of installations throughout the United States.
Introduction to Waste Water Treatment with the Wastewater Engineers System

Wastewater Engineers Inc – Model RT-200-HO Waste Water Treatment System
Industrial wastewater treatment is any process that separates and removes contaminants from industrial process waters, or effluent. These contaminants include oils, dissolved heavy metals, suspended solids and organic compounds. Either the local municipality or the Federal Government regulates the specific contaminants. A series of limits are set to determine the suitability for discharge. These limits must be met for the water to be legally discharged. If these limits are not met, the water must be pre-treated before being discharged, to remove the majority of the regulated contaminants. Although we are technically providing pre-treatment systems, we refer to them as treatment systems.
What makes Wastewater Engineers, Inc. different from other companies offering similar systems? We have a commitment to the industry. We specialize in this area, and can provide common sense advice derived from years of experience. We provide a written guarantee of our systems’ performance. We bring fluid management expertise to our clientele, providing added benefits and cost savings. We provide complete, turn-key systems, which handle the water from source to discharge. We provide excellent service after the sale, and back our systems with warranties up to 3 years.
We have adopted a three-phase approach to treating industrial wastewater. The three phases are Pre-treatment , Chemical Treatment, and Post-treatment. (SEE ALSO: Process Diagram below)
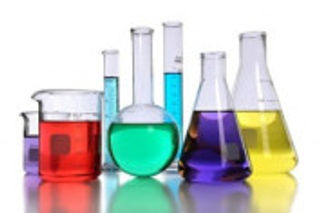
Pre-Treatment. Free Oil And Soluble Oil. Often, it is necessary to remove gross oils from a waste stream prior to chemical treatment. We supply traditional belt and wheel skimmers and also an innovative honeycomb “on the flow” coalescer, which can separate up to 97% of free oils in the first pass. This range of “on the flow” coalescers are called L-OR and OR series. Emulsified oils and grease products require an emulsion breaker to achieve the floating characteristics of free oils. Once “popped” the oils may be easily skimmed or coalesced. Our WE-KAO-L product easily breaks that complicated emulsion, so that even the most difficult fluid can be treated. Gross Contaminants And Debris. Often, it is necessary to remove gross solids from a waste stream prior to chemical treatment. Filtration and settlement are the two favored methods of reducing the solids content of wastewater. Our range of filters and settling tanks are made to suit each application.
Soluble Metals, Phosphates And Other Contaminants. In most instances we will recommend chemical precipitation to allow these contaminants to “fall” out. The range of our precipitants is very effective and less harsh than acidic/alkaline pH adjustments. Don’t forget; our RT clarification chemistry has an affinity for a wide range of soluble contaminants, so in many cases complicated precipitants may not be needed.
Chemical Treatment. Reactant Powder chemistry – Even excellent pre-treatment methodology cannot fully remove the necessary amount of contaminants to meet discharge limits to sewer, or recycling specifications. Suspended solids, typically 20 micron and smaller will not settle out of solution. Oil, even after any emulsions are split, is rarely below 100ppm. Dissolved heavy metals, even when precipitated do not fall readily from water, and do not filter readily. Our line of Reactant Powders capture and encapsulate those suspended solids, oils, and dissolved heavy metals into a large floc, which falls readily from water and filters with ease. The floc produced will pass TCLP criteria as non-leaching and non-hazardous. The treated water is sufficiently free of contamination to meet even the strictest of discharge regulations, and is often times an excellent candidate for reuse. Our RT equipment is designed to accommodate this phase of treatment easily and safely.
Post-Treatment. Post treatments can be either “polishing” of cleaned water, or pH adjustments. Some “ols”, that is; alcohols and glycols and such, have to pass through charcoal or other final capturing methods to finally strip out the impurities. Ammonia traces can be effectively removed with a zeolite column. Interestingly, we can adjust our chemical treatment to leave in soaps, detergents, inhibitors, and other expensive replenishment’s, giving you more savings. If bacterial contaminants are an issue, we supply either a chemical oxygenator or effectively remove the colony by passing the clean water through Ultra-Violet purifiers. An amazing number of options are open to us, individually or in combination.
Applications. Our systems have been installed in a wide variety of industries, and for use in a wide variety of applications. Any industry that uses water in their production process is a potential user of this technology.
Industry / Activity
Die Casting
Electronics
Metal Finishing and Machining
Equipment Manufacturing
Paper and Printing
Stamping
General
Type of Effluent
Quench Pits
Die Lube
Circuit Board Wash
Water-soluble coolants and grinding fluids,
Parts washing
Electro-polishing, Vibratory finishing fluids
Latex and water-based curtains
Equipment wash water
Flexographic and water base links
Glue, starch, suspended solids
Die wash Floor wash, Parts wash, Vibratory fluids
Mop water, Floor scrubber water, Tank wash, Equipment wash, Ultra-filtration and Reverse Osmosis (RO) concentrates Compressor blowdown, Die marking ink,
Ground water remediation.
Eaton Case History – Mass Finishing/Vibratory Treatment & Recycle System
Background. A major automotive parts supplier, Saginaw, MI. received several notices from the local (Saginaw, MI) sewer authority for infractions in their mass finishing/vibe effluent stream. The citations were for excess solids and dissolved heavy metals. Plant engineers had tried passing the effluent through the existing (whole plant) Ultra Filtration system but found that dissolved metals were unaffected (still too high) and the membrane life was dramatically shortened by related solids in the effluent stream.
Wastewater Engineers, Inc. Treatment & Recycle System. Several vendors with a variety of approaches were given the opportunity to propose alternatives to the Ultra Filter approach. Wastewater Engineers, Inc. was eventually chosen and installed its Fully Automated, turnkey system.
The system includes:
A float-activated sump pump at the plants’ existing collection sump 1500-gallon capacity Solids Settling Tank (conical bottom w/programmed, air actuated discharge valve). This configuration ‘burps’ the tank every 4 hours, thus allowing the gross amount of solids to gravity discharge.
A gravity bed filter resides beneath the Settling Vessel. “Burped’ solids are captured on the filter bed and automatically deposited into a collection hopper.
Model RT500-HO/FAP fully automated Reactor. Collects settled fluid, introduces flocculent and separates resultant solids/liquid, automatically. A 500-gallon batch treatment is approximately 40 minutes.
Treated fluids are automatically transferred from the Reactor to a Recycle Vessel. The recycle vessel features 2500-gallon holding capacity and a jet well pump. The pump is outfitted with (8) headers to deliver treated fluid to the various vibe machines for re-use.
System Performance The Wastewater Engineers, Inc. system was installed and running on January 6, 2004. It has processed approximately 8,000 gallons – (16) 500-gallon batches per 3-shift day since its installation, e.g., over 4,600,000 gallons to date.
Discharge limits for solids are 200 ppm. Without treatment, the process was generating approx. 5,100 ppm. With the WE, Inc. system, the solids are now averaging 17 ppm.
Dissolved metals are generated at (average for Zn, Cr & Fe totals) at 60 ppm with a discharge limit of <1.0 ppm. Since the WE, Inc. system was installed, most readings are below detection limits with the highest reading of <0.03 ppm.
Recycling has reduced vibe compound usage from (8) 55-gallon drums per month (@ $400.00 per drum) to < (1.5) 55-gallon drums per month. The WE, Inc. process does not extract necessary performance ingredients from the compound.
The parts being run at this facility are highly critical, 100% non-inspection requirement from Ford, GM, & Daimler Chrysler. Rust/corrosion protection is absolutely essential. No rejection of parts, using recycled fluid, has been cited.
Reliability Hardware: The Wastewater Engineers, Inc. system was delivered with our standard, 3-year, and 100% parts replacement warranty. There have been “$0” out of pocket expenses for the client and less than $500.00 from WE, Inc. Downtime has been minimal. The Plant Engineering Department and Maintenance Supervisor continue to praise reliability. Environmental Performance: Discharged fluids from the process have never exceeded discharge limits since the system was installed. Note: Wastewater Engineers, Inc. provides a written guarantee that processed fluids will meet or exceed standards to local sewer and that the solids produced from the process will pass Federal TCLP as non-hazardous. For further details or to arrange a facility tour, please contact us!
Case History – Fastener Manufacturer - Background. A large (1.2 million sq. ft.) fastener manufacturer and steel coil treatment facility had a costly problem. This facility has a 150,000 gallon per day Zinc/Phosphate wastewater treatment system. Despite this capability, oils contamination from cold heading operations within the facility impose a solids and oil burden which the waste treatment system cannot process.
The oil spills and leakage from operating equipment is present on floors adjacent to production machines. Riding floor scrubbers are in constant operation, (8) hours per shift, (3) shifts per day, (6) days per week. In addition, each of (200) cold heading machine operators maintain safe & clean conditions in work areas using mop & bucket w/cleaner. Total dirty floor cleaner waste is over (1,200) gallons per day.
PROBLEM: This facility had been using a (7,000) gal. Capacity floor pit to accumulate cleaner waste. A liquid waste hauling firm had been contracted to pick up and dispose of this material, however; solid debris such as sand, dirt, zinc-stearate, scrap metal particulate, etc., was left behind. Up to 25% solids began to accumulate, thus; a special arrangement with the hauling service added solids removal to the pick up service, resulting in a 40 cents per gallon charge. Wastewater Engineers, Inc. was contracted and requested to propose cost savings. Investigation and engineering studies indicated an opportunity to reduce costs and to provide the customer with additional savings via recycling.
SOLUTION : Wastewater Engineers, Inc. proposed an affordable system to handle the stream.
PHASE I: Gross Contaminants Removal. W.E., Inc. designed and built a special receiving box. This unit features a perforated (removable) screen, which captures larger debris such as papers, broken pallet wood chips, miscellaneous fasteners, scrap metals and general debris. The system operator simply dumps accumulations into trash barrels. A series of baffles in the receiving box promotes dirt settling. A pump transfers fluids from the receiving box, through a canister type bag filter and into a (2000) gallon capacity holding tank. The holding tank provides storage and retention time for oils to precipitate to the surface where a belt-type oil skimmer removes gross oils.
PHASE II: Polish Fluids Via Batch Treatment. The riding floor scrubber operator was assigned the responsibility of operating the treatment system. Upon demand, operator “starts” a transfer pump to fill an RT reactor unit. W.E., Inc. provided float & level controls and a “mix tank filled” indicator light on the RT control panel. This allows the operator freedom to perform other duties while the RT unit is filling. The Operator pushes “start” button on RT unit’s turbine mixer, adds WE reactant and allows (5) minutes of mixing and reaction time. The WE reactant initiates a process of precipitation and agglomeration of contaminants, and; produces a large “floc” which results in a complete separation and encapsulation of contaminants. The rapid settling of the “floc” allows the operator to open drain/filter valves after only (1) minute automated, operator is required to attend the reaction/treatment batch process for less than (10) minutes per batch.
Fluids are automatically pumped via float activated pump from the RT unit to a clean (recycling) tank. Approximately 90% of the active soap ingredients remain intact after the Wastewater Engineers Inc. process, thus; a reduction in floor cleaning chemical can be realized.
RESULTS: Savings in Treating Vs Haul Away This facility has saved over 60% Vs haul away and reduced chemical floor cleaning expense by 90%.
COST SAVINGS
Hauling:Volume/yearHauling cost @ $0.40/gallonTreatment cost @$0.15/gallon360,000 gallon$144,000$54,000
Cleaner (soap): Before Installation of Wastewater Engineers, Inc. system:Cost of cleanerGallons/weekCost/year$3.79350$66,325.00
After installation of Wastewater Engineers, Inc. system.Cost of cleanerGallons/weekCost/year$3.7950$9,475.00
Savings Summary:Hauling Cost$144,000Treatment cost$54,000Savings$90,000Cleaner cost before system$66,375Cleaner cost after system$9,475Savings$56,900
Total Savings: $146,850
Additional Information:
A 200 gallon capacity unit was initially sold making the complete “hardware” cost of all items at $31,450. Payback (ROI) was (3) months. System was installed in Jan. 5, 1991. Because of added daily volumes from parts washing fluids and vibratory fluids (both streams have high oils & solids), an RT 500 HO Unit was installed in March, 1995. The original (200) gallon unit treated (6) batches/day, (6) days/wk for (3) years. Approx. $50. For repair parts (float valve) was total maintenance cost over the (3) years of service. The original RT 200 was moved to another plant and is still in service. This business has purchased additional systems for (4) additional plants, (5) turn-key systems in all. Floor cleaner effluent was tested for sewer discharge standards – all characteristics were within discharge limits. Most critical were zinc sterate, oils & solids. Sludge passed original TCLP and each year for (3) additional years. This business has sealed all floor drains and is a “zero discharge” facility. All water-based processed fluids are now being recycled.
Case History – Vibratory, Metal Finishing Job shop
A very busy job shop has in business for over (18) years. Because business has been good, this company purchased a new and larger building next door – and they began to prepare the facility for moving the entire operation.
PROBLEM: Several permits were required, including a wastewater discharge permit. This new requirement was a jolt of reality. Approximately 10,000 gallons of vibratory fluids per day would have to meet discharge limits. An independent laboratory was commissioned to determine the characteristics of the present streams:
The Following Are Highlights:CharacteristicExisting StreamDischarge LimitspH10.36.0-9.0TSS (total suspended solids)23,150 ppm300 ppmTOC (oil & grease)12,000 ppm50 ppmPb (Lead)22 ppm0.01 ppmZn (Zinc)180 ppm4 ppmPhenol15 ppm1 ppm
The management at this company realized their several dozen different clientele were capable of requiring deburring and finishing parts with a variety of incoming contaminants – namely stamping oils, straight oils, soluble oils, rust inhibitors, parts washing residue, etc. In short, a wide variety of chemistries and, the potential to dissolve metals in their process were “typical”. Several waste hauling firms were contacted for haul-away quotes.
Only licensed and reputable firms were invited to quote their services. Prices ranged from 18 cents per gallon + $75.00 an hour (min. 4 hours) trucking charge to $1.10 per gallon and no extra trucking charge. Management agreed that the most attractive bid was a flat fee of 30 cents per gallon. Even so, the prospect of 30 cents per gallon for 10,000 gallons per day equated to $3,000 per day! This new expense would be devastating to this company.
SOLUTION: Wastewater Engineers, Inc. proposed an affordable system to handle the stream.
PHASE I: Create a closed-loop system to replace the pass-through method, which had been used previously. Because the vibratory process generates degraded media (various stone, plastic, ceramic, steel, etc.) the solids content was most challenging.
Various filtration techniques for sub-micron to larger sized solids particulate would be too costly and/or too slow. Wastewater Engineers, Inc. engineered a floor sump with a float-activated pump and a specially engineered baffled settling tank. Here, an oil skimmer was installed and a magnetic canister-type bag filter was employed. Thus, 95% of particulate volume and 75% of metal particulate could be settled and filtered respectively. A (75) GPM, float-activated pump was used on the settling unit to transfer treated fluid to a clean holding tank.
The entire system now has a total of 2,000 gallons. The above described mechanical methods are approximately 95% effective in maintaining vibe fluid cleanliness, and allowed for recycling.
Depending on the “dirt load” of incoming parts and metal burrs, the need to divert (200) gallons for chemical treatment ranges from (1) to (2) batches per day. To accomplish a treatment, Wastewater Engineers, Inc. provided a diverter valve, which allows filling of a RT-200-HO Reactor. The plant custodian is the operator. Wastewater Engineers, Inc. provided a pre-measured scoop and operator simply starts the turbine mixer, adds the scoop of powdered reactant and allows (5) minutes of mixing time. The mixer is then shut off and operator simply opens the drain valves. Operator attendance is approximately (10) minutes per (200) gallon batch. Processed fluid is automatically pumped from the RT Reactor to be recycled in the closed loop system.
This facility has reduced their tumbling/vibratory fluids ($385.00 per drum) from (4) drums per week to (30) gallons and has avoided the haul-away costs entirely. Samples of the sludge and treated fluids were sent to an independent lab for analysis. The sludge passed TCLP, and the fluid passed local sewer discharge standards.
“I was concerned about filling out waste manifests for a waste hauler and the possibility of future liability for a landfill clean-up. With this system, we are not required to haul away and we have no related paper work” , says Terry Desch, Plant Manager.
“The cost to treat the system fluids is less than ½ the haul-away fees of our winning bidders charges and we are saving a substantial amount of money from our cleaning fluids purchases ,” says Plant Purchasing Agent.
Three Step Treatment Process Diagram

Other Information on Mass Finishing and Related Technologies…
A Mass Finishing technology for deburring, finishing and polishing of machined and manufactured parts and components
Centrifugal isotropic Finishing
Centrifugal Isotropic Finishing (CIF) is a high-energy finishing method, which has come into widespread acceptance in the last few years. Although not nearly as universal in application as vibratory finishing, a long list of important CBF applications have been developed in the last few decades.
Similar in some respects to barrel finishing, in that a drum-type container is partially filled with media and set in motion to create a sliding action of the contents, CBF is different from other finishing methods in some significant ways. Among these are the high pressures developed in terms of media contact with parts, the unique sliding action induced by rotational and centrifugal forces, and accelerated abrading or finishing action. As is true with other high energy processes, because time cycles are much abbreviated, surface finishes can be developed in minutes, which might tie up conventional equipment for many hours.
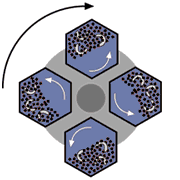
Centrifugal Barrel Finishing principles – high-intensity finishing is performed with barrels mounted on the periphery of a turret. The turret rotates providing the bulk of the centrifugal action, the barrels counter-rotate to provide the sliding abrasive action on parts.
The principle behind CBF is relatively straightforward. Opposing barrels or drums are positioned circumferentially on a turret. (Most systems have either two or four barrels mounted on the turret; some manufacturers favor a vertical and others a horizontal orientation for the turret.) As the turret rotates at high speed, the barrels are counter-rotated, creating very high G-forces or pressures, as well as considerable media sliding action within the drums. Pressures as high as 50 Gs have been claimed for some equipment. The more standard equipment types range in size from 1 ft3 (30 L) to 10 ft3, although much larger equipment has been built for some applications.
Media used in these types of processes tend to be a great deal smaller than the common sizes chosen for the barrel and vibratory processes. The smaller media, in such a high-pressure environment, are capable of performing much more work than would be the case in lower energy equipment. They also enhance access to all areas of the part and contribute to the ability of the equipment to develop very fine finishes. In addition to the ability to produce meaningful surface finish effects rapidly, and to produce fine finishes, CBF has the ability to impart compressive stress into critical parts that require extended metal fatigue resistance. Small and more delicate parts can also be processed with confidence, as the unique sliding action of the process seems to hold parts in position relative to each other, and there is generally little difficulty experienced with part impingement. Dry process media can be used in certain types of equipment and is useful for light deburring, polishing, and producing very refined isotropic super-finishes.
Below are some process video footage demonstrations of high-speed centrifugal isotropic finishing. These automated edge and surface finishing methods are capable of producing very refined low micro-inch surfaces that can improve functional part performance and service life.
CONTRIBUTING EDITOR BIOGRAPHY – David A. Davidson, [dryfinish@gmail.com]
Mr. Davidson is a deburring/surface finishing specialist and consultant. He has contributed technical articles to Metal Finishing and other technical and trade publications and is the author of the Mass Finishing section in the current Metal Finishing Guidebook and Directory. He has also written and lectured extensively for the Society of Manufacturing Engineers, Society of Plastics Engineers, American Electroplaters and Surface Finishers Association and the Mass Finishing Job Shops Association. Mr. Davidson’s specialty is finishing process and finishing product development.
More about Dave Davidson…
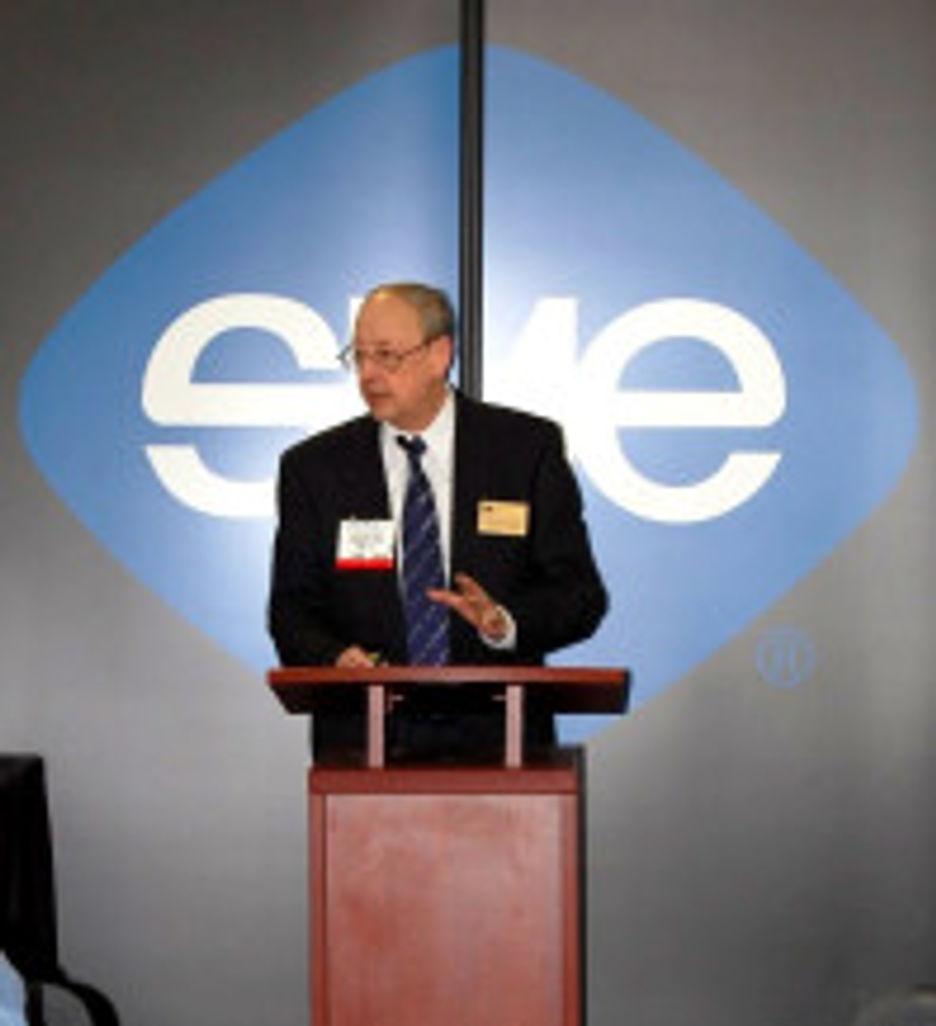
I am a deburring and surface finishing specialist, consultant and advisor to SME’s [Society of Manufacturing Engineers] Technical Community Network. The focus of my activity is assisting manufacturers and machine shops with reducing their dependence on hand or manual deburring and finishing methods, and helping them to upgrade the edge and surface finish quality of their parts. I currently work from Colville, WA but I assist clients nation-wide. I can arrange for free sample processing and process development for your challenging deburring and finishing needs and can provide you with either contract finishing services or the in-house capability to produce improved hands-free finishes on precision parts. I can be contacted at 509.230.6821 or dryfinish@gmail.com. Let me know if I can be helpful.
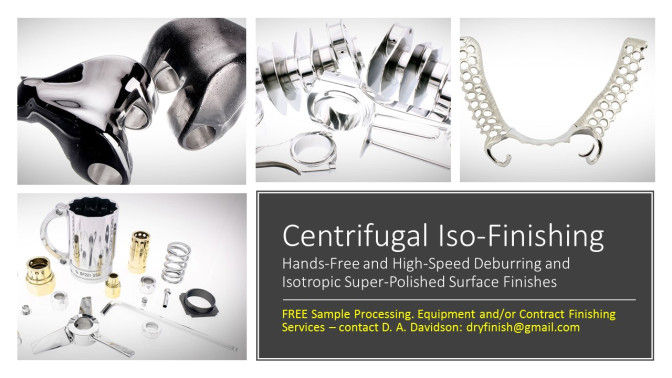
Contributing Editor: Dave Davidson, Deburring/Finishing Technologist 509.230.6821 | dryfinish@gmail.com | https://about.me/dave.davidson

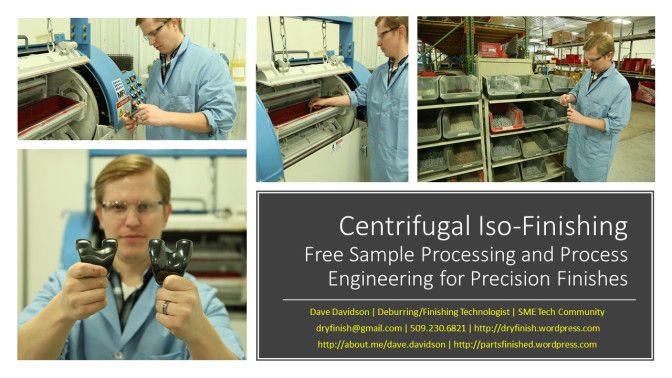
Comments