High Energy Micro-Finishing: Surface Texture Improvement and Surface Integrity for Precision Parts
- Dave Davidson
- Jul 28, 2011
- 9 min read
Need more information? Contact the Contributing Editor: Dave Davidson – Deburring/Finishing Specialist | dryfinish@gmail.com | 509.563.9859 | http://dryfinish.wordpress.com ask about: FREE SAMPLE PROCESSING | CONTRACT FINISHING | EQUIPMENT _____________________________________________________________
Below is a brief run-down of the surface finish factors contributing to extended service life and improved functional performace of manufactted parts and components.
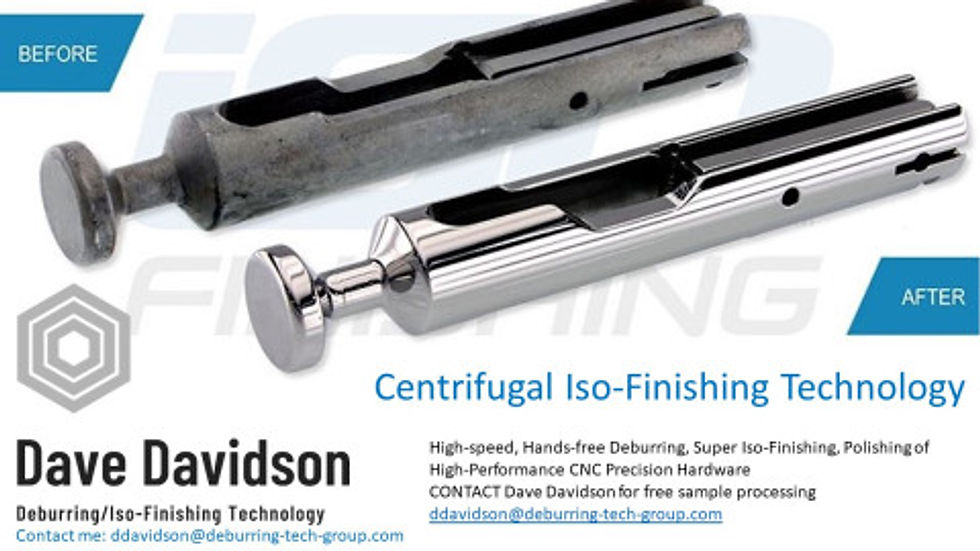
Before and After comparison of precision machined components with Centrifugal Iso-Finishing improves the fit and function of cooperating parts such as these.
The role of mass finishing processes as a method for removal of burrs, developing edge contour and smoothing and polishing parts has been well established and documented for many years. These processes have been used in a wide variety of part applications to promote safer part handling (by attenuation of sharp part edges) improve the fit and function of parts when assembled, and produce smooth, even micro-finished surfaces to meet either functional or aesthetic criteria or specifications. Processes for developing specific edge and/or surface profile conditions on parts in bulk are used in industries as diverse as the jewelry, dental and medical implant industries on up through the automotive and aerospace industries.
Less well known and less clearly understood is the role specialized variants of these types of processes can play in extending the service life and performance of critical support components or tools in demanding manufacturing or operational applications.
Industry has always been looking to improve surface condition to enhance part performance, and this technology has become much better understood in recent years. Processes are routinely utilized to specifically improve life of parts and tools subject to failure from fatigue and to improve their performance. These improvements are mainly achieved by enhancing part surface texture in a number of different, and sometimes complementary ways.
To understand how micro-surface topography improvement can impact part performance, some understanding of how part surfaces developed from common machining, grinding and other methods can negatively influence part function over time. A number of factors are involved:
Positive vs. Negative Surface Skewness. The skew of surface profile symmetry can be an important surface attribute. Surfaces are typically characterized as being either negatively or positively skewed. This surface characteristic is referred to as Rsk (Rsk – skewness – the measure of surface symmetry about the mean line of a profilometer graph). Unfinished parts usually display a heavy concentration of surface peaks above this mean line, (a positive skew). It is axiomatic that almost all surfaces produced by

This graphic illustrates the difference between positively skewed surfaces with neutral or negatively skewed surfaces which have been planarized or plateaued by surface finishing methods such as Centrifugal Iso-Finishing. Also illustrated in the bottom two before and after comparison micro-photographs (taken with SEM -scanning electron microscopy) is the difference between non-isotropic surfaces developed by grinding and machining methods and a surface that has been modified with Centrifugal Iso-Finishing in which abrasive tracks are dispersed and have much more random surface patterns. The resultant part benefit in terms of service life extension because of either improved wear resistance or improved fatigue failure resistance can be substantial with particular benefit to both aerospace and high-performance cooperating automotive components. Note especially the two top photos in the graphic: Top-Left (Before Centrifugal Iso-Finishing) (Before) This photograph was taken with an electron microscope at 500x magnification. It shows the surface of a raw unfinished “as cast” turbine blade. The rough initial surface finish as measured by profilometer was in the 75 – 90 Ra (µin) range. As is typical of most cast, ground, turned, milled, EDM and forged surfaces this surface shows a positive Rsk [Rsk – skewness – the measure of surface symmetry about the mean line of a profilometer graph. Unfinished parts usually display a heavy concentration of surface peaks above this mean line, generally considered to be an undesirable surface finish characteristic from a functional viewpoint.] Top-Right (After Centrifugal Iso-Finishing) (After) This SEM photomicrograph (500X magnification) was taken after processing the same turbine blade in a multi-step procedure utilizing orbital pressure methods with both grinding and polishing free abrasive materials in sequence. The surface profile has been reduced from the original 75 – 90 Ra (µin.) to a 5-9 Ra (µin.) range. Additionally, there has been a plateauing of the surface and the resultant smoother surface manifests a negative skew (Rsk) instead of a positive skew. This type of surface is considered to be very “functional” in both the fluid and aerodynamic sense. The smooth, less turbulent flow created by this type of surface is preferred in many aerodynamic applications. Another important consideration the photomicrographs indicate is that surface and sub-surface fractures seem to have been removed. Observations with backscatter emission with a scanning electron microscope (SEM) gave no indication of residual fractures. (Graphic courtesy of Jack Clark, Surface Analytics)
common machining and fabrication methods are positively skewed. These positively skewed surfaces have an undesirable effect on the bearing ratio of surfaces, negatively

3D Printed parts pose substantial challenges for surface finishing methods. As printed some of these parts display positively skewed surface roughness in the range of 500 – 800 micro inches Ra. The parts shown in the example above had a starting surface roughness of 350+ micro-inches Ra and were reduced to 12 jmicro-inches Ra with high-speed and hands-free Centrifugal Iso-Finishing method.
impacting the performance of parts involved in applications where there is substantial surface-to-surface contact. Specialized high energy finishing procedures can truncate these surface profile peaks and achieve negatively skewed surfaces that are plateaued, presenting a much higher surface bearing contact area. Anecdotal evidence confirms that surface finishing procedures tailored to develop specific surface conditions with this in mind can have a dramatic impact on part life. In one example the life of tooling used in aluminum can tab stamping operations was extended 1000% or more by improved surface textures produced by mechanical surface treatment. Some cutting tools have had service life extended by 200% or more.

Parts from many industries can benefit from Isotropic Micro-finishing and Centrifugal Iso-Finishing Technologies which offer wear resistance and fatigue failure resistance for critical components in aviation, aerospace and high-performance automotive industries. (Photo courtesy Mark Riley, BV Products)
Directionalized vs. Random (Isotropic) Surface Texture Patterns. Somewhat related to surface texture skewness in importance is the directional nature of surface textures developed by typical machining and grinding methods. These machined surfaces are characterized by tool marks or grinding patterns that are aligned and directional in nature. It has been established that tool or part life and performance can be substantially enhanced if these types of surface textures can be altered into one that is more random in nature. Post-machining processes that utilize free or loose abrasive materials in a high energy context can alter the machined surface texture substantially, not only reducing surface peaks but generating a surface in which the positioning of the peaks has been altered appreciably. These “isotropic” surface effects have been demonstrated to improve part wear and fracture resistance, bearing ratio and improve fatigue resistance.

The upper titanium test coupon exhibits sharp edges and machining/milling mark surface patterns consistent with many machining operations. The lower coupon shows how the sharp edges have removed and the milling pattern marks have been blended into a homogenous isotropic surface with a Centrifugal Iso-Finishing abrasive process. The process also induces substantial beneficial compressive stress that adds to the wear and fatigue failure resistance benefit to parts developed
Residual Tensile Stress vs. Residual Compressive Stress. Many machining and grinding processes tend to develop residual tensile stresses in the surface area of parts. These residual tensile stresses make parts susceptible to premature fracture and failure when repeatedly stressed. Certain high-energy mass finishing processes can be implemented to modify this surface stress condition, and replace it with uniform residual compressive stresses. by typical machining and grinding methods. These machined surfaces are characterized by tool marks or grinding patterns that are aligned and directional in nature. It has been established that tool or part life and performance can be substantially enhanced if these types of surface textures can be altered into one that is more random in nature. Post-machining processes that utilize free or loose abrasive materials in a high energy context can alter the machined surface texture substantially, not only reducing surface peaks, but generating a surface in which the positioning of the peaks has been altered appreciably. These “isotropic” surface effects have been demonstrated to improve part wear and fracture resistance, bearing ratio and improve fatigue resistance.

3-D Micro-Surface Topographical maps are coming into increasing use to better quantify surfaces as they relate to part service life and performance. This graphic contrasts surfaces after grinding operations (bottom row) and surfaces that have been modified with Centrifugal Iso-Finishing (top-row). Graphics were produced with SWLI optical interferometry and permits comparison of 2D and 3D views of the same surface area. Note the difference between the positively skewed micro-surface profiles of the unfinished parts in the bottom row with negatively skewed parts that were iso-finished that were iso-finsihed on the top row of pictures
Super-Hone Edge Prep refers to a group of processes that improves edge condition and surface physical properties for tooling. The processes involve complete envelopment and processing of all edge and surface areas of the tool and are non-selective in nature. These processes develop surface compression and stress relief on all surfaces, as well as uniformly micro-honing and polishing all edge areas, regardless of tool or edge geometry.
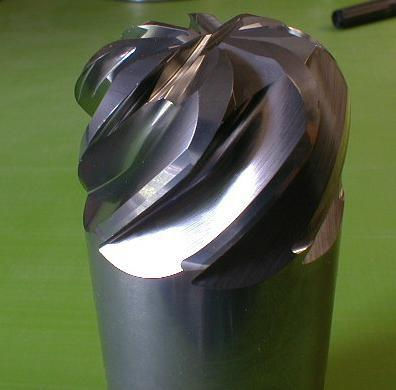
The need for some edge preparation on cutting tools in many applications has been well documented. Most of the processes currently utilized (including manual ones) concentrate on modifying the edge to produce an edge land to strengthen the edge. Although these types of processes improve cutting edge geometries they do not typically address surface profile topography issues at the cutting edge such as profile skewness, isotropiciy, load-bearing ratio and residual stress correction. Specialized high-energy finishing methods such as Centrifugal Iso-Finishing can and do.
Although the processes promote changes that are significant and crucial to improved tool performance, the changes in the physical cutting edge are so subtle that dimensional integrity of the tool is maintained. These alterations of the cutting edge surface area and supporting structures contributes to an improvement in mechanical strength and can avert premature wear or fracture of the tool.
The processes also have a tendency to improve overall symmetry of the cutting features, this is especially contrasted with manual honing methods, in which abrasive filament wheels, abrasive sticks or even coated abrasive paper are utilized to pre-condition edges by hand methods. Surface profile improvement is isotropic in nature, minimizing the fatigue and fracture problems associated with uni-directional surface patterns in surfaces created by production grinding methods. Smoother more isotropic surfaces provide greater lubricity for improved chip flow, often facilitating higher feed and speed rates with processed tools.
This edge conditioning procedure is an outgrowth of research to improve the tribological functionality of wear surfaces, with a view to extending useful service life and preventing premature failure of critical components that are highly stressed or strained. It has been found that surface treatment processes that can develop some measure of compressive stress and an isotropic micro-finish to edges and surfaces can improve load-bearing ratios and other wear-resistant factors far more than improvement in one of these areas alone.
When utilized to develop tool surface and edge improvements these processes can dramatically improve tool performance and maximize productivity in a number of areas:
o Greater tool life and durability o Increased machine feed rates o Increased tool speed rates o Improved surface finish on parts o Reduced tool change-over and downtime cycles due to break-in o Improved tool performance meeting high tolerance requirements
Summary. Many parts or tools that are subject to fatigue, fracture or wear can gain substantial improvements in life and performance from alterations to their overall surface texture. Improvements in overall smoothness, load bearing ratio, surface profile skewness and isotropicity can in many instances, improve life and performance and cut operational costs dramatically. Manufacturer s that have not subjected their parts to an analysis to determine the potential benefits of this kind of processing may be making parts “that are not all that they can be.”
Hands-free Centrifugal Iso-Finishing Technology
Centrifugal Isotropic Finishing (CIF) is a high-energy finishing method, which has come into widespread acceptance in the last few years. Although not nearly as universal in application as vibratory finishing, a long list of important CBF applications have been developed in the last few decades.
Similar in some respects to barrel finishing, in that a drum-type container is partially filled with media and set in motion to create a sliding action of the contents, CBF is different from other finishing methods in some significant ways. Among these are the high pressures developed in terms of media contact with parts, the unique sliding action induced by rotational and centrifugal forces, and accelerated abrading or finishing action. As is true with other high energy processes, because time cycles are much abbreviated, surface finishes can be developed in minutes, which might tie up conventional equipment for many hours.

(Left) Centrifugal Barrel Finishing principles – high-intensity finishing is performed with barrels mounted on the periphery of a turret. The turret rotates providing the bulk of the centrifugal action, the barrels counter-rotate to provide the sliding abrasive action on parts.
The principle behind CBF is relatively straightforward. Opposing barrels or drums are positioned circumferentially on a turret. (Most systems have either two or four barrels mounted on the turret; some manufacturers favor a vertical and others a horizontal orientation for the turret.) As the turret rotates at high speed, the barrels are counter-rotated, creating very high G-forces or pressures, as well as considerable media sliding action within the drums. Pressures as high as 50 Gs have been claimed for some equipment. The more standard equipment types range in size from 1 ft3 (30 L) to 10 ft3, although much larger equipment has been built for some applications.
Media used in these types of processes tend to be a great deal smaller than the common sizes chosen for the barrel and vibratory processes. The smaller media, in such a high-pressure environment, are capable of performing much more work than would be the case in lower energy equipment. They also enhance access to all areas of the part and contribute to the ability of the equipment to develop very fine finishes. In addition to the ability to produce meaningful surface finish effects rapidly, and to produce fine finishes, CBF has the ability to impart compressive stress into critical parts that require extended metal fatigue resistance. Small and more delicate parts can also be processed with confidence, as the unique sliding action of the process seems to hold parts in position relative to each other, and there is generally little difficulty experienced with part impingement. Dry process media can be used in certain types of equipment and is useful for light deburring, polishing, and producing very refined isotropic super-finishes.
Below are some process video footage demonstrations of high-speed centrifugal isotropic finishing. These automated edge and surface finishing methods are capable of producing very refined low micro-inch surfaces that can improve functional part performance and service life.
Below: Further Part Applications: Centrifugal Iso-Finishing Technology (Slide Album Below)
This slideshow requires JavaScript.
CONTRIBUTING EDITOR BIOGRAPHY – David A. Davidson, [dryfinish@gmail.com] Mr. Davidson is a deburring/surface finishing specialist and consultant. He has contributed technical articles to Metal Finishing and other technical and trade publications and is the author of the Mass Finishing section in the current Metal Finishing Guidebook and Directory. He has also written and lectured extensively for the Society of Manufacturing Engineers, Society of Plastics Engineers, American Electroplaters and Surface Finishers Association and the Mass Finishing Job Shops Association. Mr. Davidson’s specialty is finishing process and finishing product development.
More about Dave Davidson…
I am a deburring and surface finishing specialist, consultant and advisor to SME’s [Society of Manufacturing Engineers] Technical Community Network. The focus of my activity is assisting manufacturers and machine shops with reducing their dependence on hand or manual deburring and finishing methods, and helping them to upgrade the edge and surface finish quality of their parts. I currently work from Norwich, NY but I assist clients nation-wide. I can arrange for free sample processing and process development for your challenging deburring and finishing needs and can provide you with either contract finishing services or the in-house capability to produce improved hands-free finishes on precision parts. I can be contacted at 509.563.9859 or dryfinish@gmail.com. Let me know if I can be helpful.
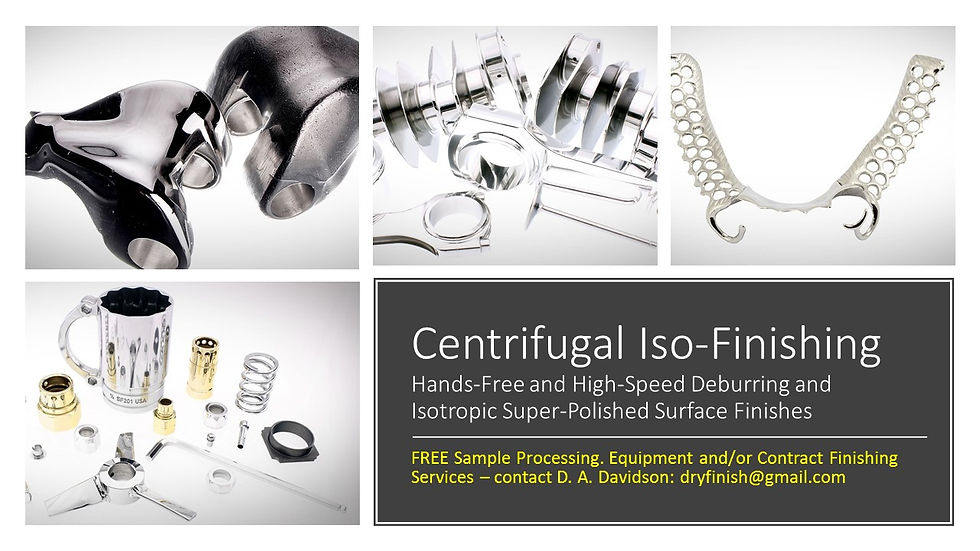
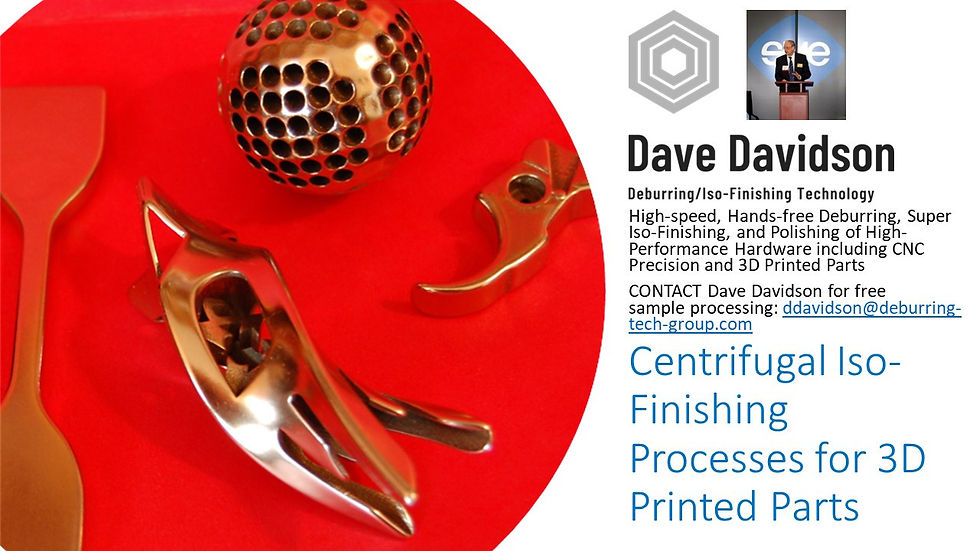
Comments