High-Speed Precision Finishing and Polishing Processes in Centrifugal Barrel Equipment
- Dave Davidson
- Jun 8, 2022
- 5 min read
CONTACT INFORMATION: Dave Davidson | Mobile: +1.509.563.9859 (WhatsApp - International) (Work email) ddavidson@deburring-tech-group.com * Web-page https://dryfinish.wixsite.com/iso-finish

Large numbers of parts can be uniformly edge and surface finished in mass finishing equipment. Process development in recent years has facilitated the creation of very refined surfaces by processing parts in a series of successively finer processes in high energy centrifugal equipment
Nearly all manufactured and fabricated components require some edge and surface finish preparation prior to final assembly. Although many parts today are still individually handled and processed with hand tools or hand-held power tools, it has become almost universally accepted that utilization of mass finishing techniques are far to be preferred on both their economic and technical merits, whenever possible. Utilizing energy developed from motion imparted to the containers or vessels in mass finishing equipment, loose abrasive or polishing media can produce a wide range of desirable edge and surface effects.
Roughly machined, milled, molded, stamped 3D-printed or cast parts can be transformed into attractive parts free or burrs, sharp edges and corners with uniform surfaces that can range from the utilitarian to the highly aesthetic. Among the specific tasks these processes are specified to perform are: cleaning, deburring, descaling, surface smoothing, edge-break, radius formation, removal of surface contaminants from heat treat and other processes, preplate, prepaint or coating surface preparation, blending in surface irregularities from machining or fabricating operations, producing reflective surfaces with nonabrasive burnishing media that also, refining and polishing surfaces, and developing superfinished or low microfinish equivalent surface profiles.

Centrifugal Barrel Finishing or Centrifugal Iso-Finishing. Although many types of manufactured components with high volume output are abrasively processed with barrel and vibratory finishing equipment, many different types of parts with specialized or precision edge and surface finish requirements are processed in high energy centrifugal barrel equipment.
Centrifugal barrel finishing (CBF) is a high-energy finishing method, which has come into widespread acceptance in the last 25–30 years. Although not quite as universal in application as vibratory finishing, a long list of important CBF applications have been developed in the last few decades.
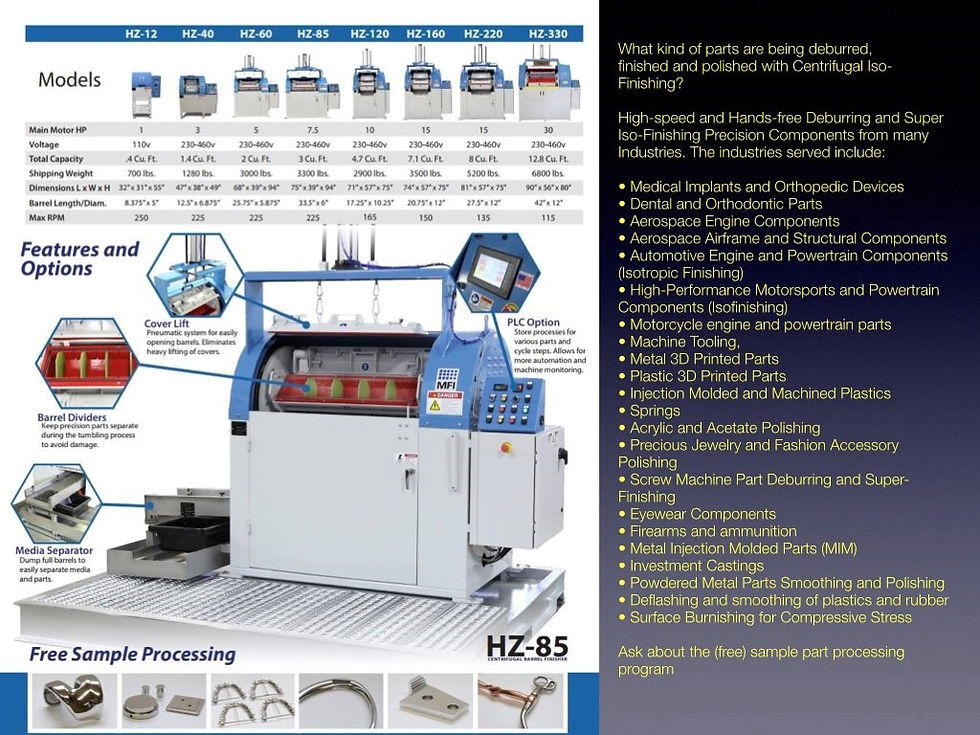
ABOVE: This Centrifugal Barrel Finishing machine chart shows a variety of machine models of varying size and production capacity. Also listed are a wide variety of parts from many different industries that are processed with this method because of its ability to produce high-quality edges and surfaces.
Similar in some respects to barrel finishing, in that a drum-type container is partially filled with media and set in motion to create a sliding action of the contents, CBF is different from other finishing methods in some significant ways. Among these are the high pressures developed in terms of media contact with parts, the unique sliding action induced by rotational and centrifugal forces, and accelerated abrading or finishing action. As is true with other high-energy processes, because time cycles are much abbreviated, surface finishes can be developed in minutes, which might tie up conventional equipment for many hours.
The principle behind CBF is relatively straightforward. Opposing barrels or drums are positioned circumferentially on a turret. (Most systems have either two or four barrels mounted on the turret; some manufacturers favor a vertical and others a horizontal orientation for the turret.) As the turret rotates at high speed, the barrels are counterrotated, creating very high G-forces or pressures, as well as considerable media sliding action within the drums. Pressures as high as 50 Gs have been claimed for some equipment. The more standard equipment types range in size from 1 cubic ft. (30 L) to 10 cubic ft (330 L), although much larger equipment has been built for some applications.
Media used in these types of processes tend to be a great deal smaller than the common sizes chosen for barrel and vibratory processes. The smaller media, in such a high-pressure environment, are capable of performing much more work than would be the case in lower energy equipment. They also enhance access to all areas of the part and contribute to the ability of the equipment to develop very fine finishes. In addition to the ability to produce meaningful surface finish effects rapidly, and to produce fine finishes, CBF has the ability to impart compressive stress into critical parts that require extended metal fatigue resistance. Small and more delicate parts can also be processed with confidence, as the unique sliding action of the process seems to hold parts in position relative to each other, and there is generally little difficulty experienced with part impingement with proper media and part loading. Dry process media can be used in certain types of equipment and is useful for light deburring, polishing, and producing very refined isotropic super finishes.
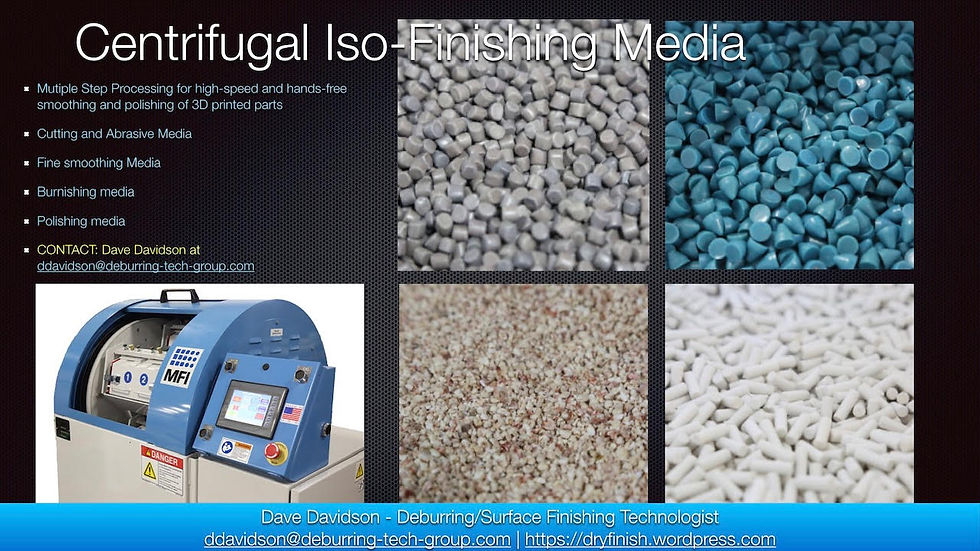
ABOVE: Shown are a few of the many different types of media commonly used in Centrifugal barrel finishing applications including deburring, cleaning, radiusing, smoothing, burnishing and polishing.
Practicality and questions of cost-effectiveness often determine whether high-energy methods are selected over a conventional barrel or vibratory processes. If acceptable surface finishes can be developed for less challenging requirements in a few hours, conventional equipment is usually the most economic alternative. CBF equipment’s strong suit is the ability to develop surface finishes that may require manual intervention or over-lengthy time cycles in conventional equipment and the capability to develop a wide range of special surface finishes required for demanding and critical applications.
SELECTED APPLICATION EXAMPLES:
REFERENCES:
Davidson, D. A. “Micro-Finishing and Surface Texture”, METAL FINISHING, (New York, NY: Elsevier Science) July 2002
Davidson, D. A. “Mass Finishing Processes”, 2005 METAL FINISHING GUIDEBOOK AND DIRECTORY, (New York, NY: Elsevier Science), 2005
Hignett, J. Bernard, “Centrifugal Barrel Deburring and Surface Conditioning – Some Recent Developments”, Technical Paper: MR79-567, (Dearborn MI:, Society of Manufacturing Engineers), 1979
Gillespie, Laroux, Deburring and Edge-Finishing Handbook, (Dearborn MI: Society of Manufacturing Engineers), 1999
CENTRIFUGAL ISO-FINISHING VIDEOS
ABOVE: This demonstration video shows the operation of the very popular Model HZ-40 machine which is used widely in the jewelry, dental, medical, 3D printed part, screw machine part industries and other small parts
ABOVE: This Model HZ-60 machine has operating characteristics very similar to the Model HZ-40 but is built with automated material handling features to facilitate heavier production volumes of parts.
ABOVE: This model HZ-85 machine is very similar to the HZ-60 but is a stretched version of for processing even higher volumes of parts.
ABOVE: This video was shot on the factory floor of a large-sized contract machining operation located in the Pacific Northwest that uses a larger Model HZ-120 machine This contract machining company does machining for a wide variety of industries including work for the medical, aerospace and other precision part industries. They deburr, finish and polish over 50 different part numbers with Centrifugal Iso-Finishing Technology for these demanding applications. Their adoption of this technology vastly reduced the amount of manual finishing they had to perform while improving overall surface finish quality and uniformity.
ABOVE: Background information on MFI, the equipment manufacturer of Centrifugal iso-Finishing machines. The video gives information about the equipment manufacturing operation as well as the process development the company performs as a part of its free sample part processing program for customers where they demonstrate the finishes that can be achieved on customer provided parts prior to the purchase of the machine.
SAMPLE PART PROCESSING INFORMATION
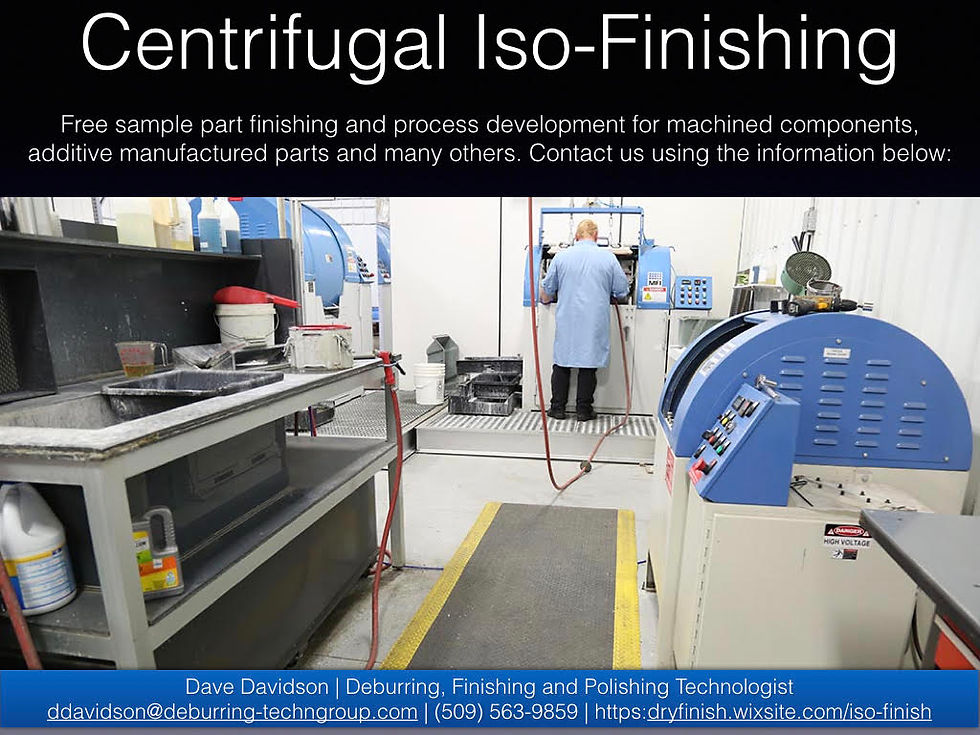

Comments