How can you produce high-quality edge and surface finishes on large lots of manufactured or machined
- Dave Davidson
- Apr 20, 2017
- 19 min read
The photo above: Isotropic Micro-Finishing of Automotive Components. (Photo by: Mark Riley, BV Products)

Mass Finishing Processes and Mechanical Surface Preparation
For more information and sample processing contact: David A. Davidson | Deburring/Finishing Technologist | ddavidson@deburring-tech-group.com |Advisor: SME Machining/Material Removal Technical Community |See Photo Gallery
What is mass finishing?
Mass finishing is a term used to describe a group of abrasive industrial processes by which large lots of parts or components made from metal or other materials can be economically processed in bulk to achieve one or several of a variety of surface effects. These include deburring, descaling, surface smoothing, edge-break, radius formation, removal of surface contaminants from heat treat and other processes, pre-plate and pre-paint or coating surface preparation, blending in surface irregularities from machining or fabricating operations, producing reflective surfaces with nonabrasive burnishing media, refining surfaces, and developing super-finish or micro-finish equivalent surface profiles.
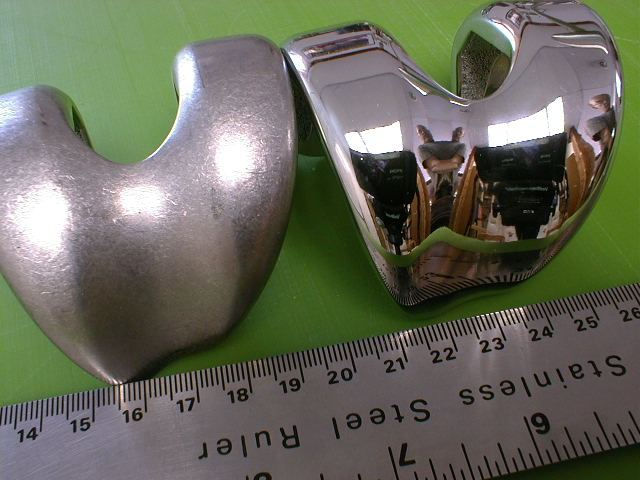
In many manufacturing applications, the surface finish can play a critical role in the long term functionality, performance, and longevity of parts, such as this bio-medical surgical implant. The correlation between surface finish and overall long-term part performance is often not well understood by the manufacturing and engineering community.
Mass finishing processes can be used to develop exceptionally high-quality surface finishes. This photo above shows an example of a centrifugal barrel finish processes used to develop precision micro-finished surfaces on surgical implants. The part on the left has undergone an abrasive smoothing operation, The part on the right has been processed in a follow-up polishing operation in the same equipment with ultra-fine polishing materials.
This slideshow requires JavaScript.
Above: Some examples of Mass Finishing effects on production parts
All mass finishing processes utilize a loose or free abrasive material referred to as media within a container or chamber of some sort. Energy is imparted to the abrasive media mass by a variety of means to impart motion to it and to cause it to rub or wear away at part surfaces. Although by definition, the term mass finishing is used generally to describe processes in which parts move in a random manner throughout the abrasive media mass, equipment and processes that utilize loose abrasive media to process parts that are fixtured come under this heading also.
Why mass finishing?
Nearly all manufactured parts or components require some measure of surface refinement prior to final assembly, or the final finish or coating required to make the parts acceptable to the consumer or end-user. Most manufacturing companies who employ mass finishing techniques do so because of the economic advantages to be obtained, especially when compared with manual deburring and surface finishing techniques. Mass finishing processes often reduce or eliminate many procedures that are labor intensive and require extensive part handling. This is especially important in meeting increasingly stringent quality control standards, as most mass finishing processes generate surface effects with part-to-part and lot-to-lot uniformity that cannot be replicated with processes in which parts are individually handled. It has become a manufacturing engineering axiom that part reject and rework rates will plummet if a mass finishing approach can be implemented to meet surface finish objectives.
Although each of the mass finishing process types carries with it a unique set of process strengths and weaknesses, all of them are sufficiently versatile to be able to process a wide variety of part types successfully. A plethora of abrasive media types, sizes, and shapes makes it possible, in many cases, to achieve very different results within the same equipment, ranging from heavy grinding and radiusing to final finishing. Components from almost every conceivable type of material have been surface conditioned using mass finishing techniques including ferrous and nonferrous metals, plastics, composition materials, ceramics, and even wood.
Below: Various parts deburred and finished with mechanically or chemically accelerated mass finishing methods
This slideshow requires JavaScript.
Mass Finishing cautions
Despite the immense versatility of these types of processes, some potential process limitations should be noted. It can be difficult to selectively treat certain part areas to the exclusion of other areas, which might have critical dimensional tolerance requirements. Unless masked or fixtured, all exterior areas of the part will be affected by the process to a greater or lesser degree, with effects on corners and edges being more pronounced than those on flat areas, and with interior holes, channels, and recesses being relatively unaffected in the more common processes.
Care must be exercised in media size, shape selection, and maintenance to prevent media lodging in holes and recesses, which might require labor-intensive manual removal. Some parts have shapes, sizes, or weights that may preclude them from being finished in some mass finishing processes because of the risk of impingement from part-on-part contact or of nesting due to certain features of the parts interlocking together when in proximity. Additionally, most processes that use water in conjunction with the abrasive media create an effluent stream, which must be treated prior to discharge into a municipal sewage or another disposal.
Mass Finishing — part of the manufacturing process
Much time and money can be saved both in mass finishing process operations and in process development if finishing considerations are given sufficient weight at the design, production, and quality control stages. Although it is a rule more breached than observed, it should be noted that mass finishing processes are not, and were never intended to be, methods for rectifying errors made in earlier stages of the manufacturing process. It should be equally obvious that processes developed for parts made with tools and dies that are sharp will no longer produce the same results when that tooling becomes dull. Mass finishing processes can produce remarkably uniform results if process parameters are followed carefully, but this assumes some measure of uniformity of surface condition for a given part within a lot, and from lot-to-lot, as received in the finishing area.
Mass Finishing equipment
One of the more obvious factors influencing mass finishing processes is equipment selection. There are five major equipment groups as follows: barrel, vibratory, centrifugal barrel, centrifugal disk, and spin/spindle finishing.
There are variations within each major grouping, and each equipment group has its own set of advantages. The first four groups are primarily used with parts immersed within a body of abrasive media and are capable of some independent movement within that mass. On occasion, fixturing or some subcompartmentalization may be used to isolate delicate or critical parts from each other. Part-on-part contact may also be minimized by using higher media-to-part ratio combinations. Common media-to-part ratios for noncritical parts run anywhere from 1:1 to 1:4 by volume. Parts with a higher need for cushioning and protection may utilize media/part ratios as high as 10:1 to 15:1. In contrast, all spin/spindle finishing processes utilize fixturing of parts, and in most cases movement of the fixture develops much of the action needed to abrade the parts.
Barrel Finishing
Barrel finishing is unquestionably the oldest of the mass finishing methods, with some evidence indicating that crude forms of barrel finishing may have been in use by artisans as far back as the ancient Chinese and Romans as well as the medieval Europeans. In this method, the action is given to the media by the rotation of the barrel. As the barrel rotates, the media and parts within climb to what is referred to as the turnover point. At this point, gravity overcomes the cohesive tendencies of the mass, and a portion of the media mass slides in a retrograde movement to the lower area of the barrel. Most of the abrading or other work being performed on parts within the barrel takes place within this slide zone. Typically the barrel is filled to 50% of its volume capacity to maximize the length of its slide zone. Under-filling will cause the parts to cascade and possibly be damaged. Overfilling may make the action gentler but will also excessively lengthen process cycle times.
Barrels used for wet abrasive operations are made from steel and lined with rubber, polyurethane or similar material to protect the steel shell from abrasive wear from the media and parts mixture. Various styles of tumbling barrel equipment are shown above. (1) Top-left: Octagonal horizontal machine is shown with an unloading slide or hopper to facilitate external separation of the parts/media mixture. (2) (Top-right) Multi-compartment tumbling barrel to facilitate tumbling of parts needing segregated processing. (3) (Middle-right) Trunion style machine with roller drive. Barrel with side disks are placed on roller drives. The machine can facilitate running different batch operations simultaneously. Barrels are loaded and unloaded by hoist. (4) (Bottom-Left) Large Conical style barrel. The barrel is tilted for loading and unloading operations of parts. (5) (Bottom-right) Small batch operation tilting-conical barrel, also used for drying parts after wet-process finishing in other equipment in conjunction with absorbent agricultural media such as ground corn cob.
Tumbling barrels are available in a variety of configurations, the most common being a horizontally oriented octagonal chamber, which provides a much more efficient media lift than a purely cylindrical shape. Other configurations include barrel chambers mounted on pedestals, barrels with front or end loading, perforated barrels encased in a water tank or tub, and so-called triple-action polygonal barrels. Also used extensively are oblique barrels, similar in some respects to small batch concrete mixers. This equipment is used for light deburring and finishing as well as part drying. It has the advantage of permitting operator inspection while in process, and its open end can be tilted down for ease of unloading, but it is much less efficient than horizontal equipment and suffers from the tendency of parts and media to segregate in extended time cycles.
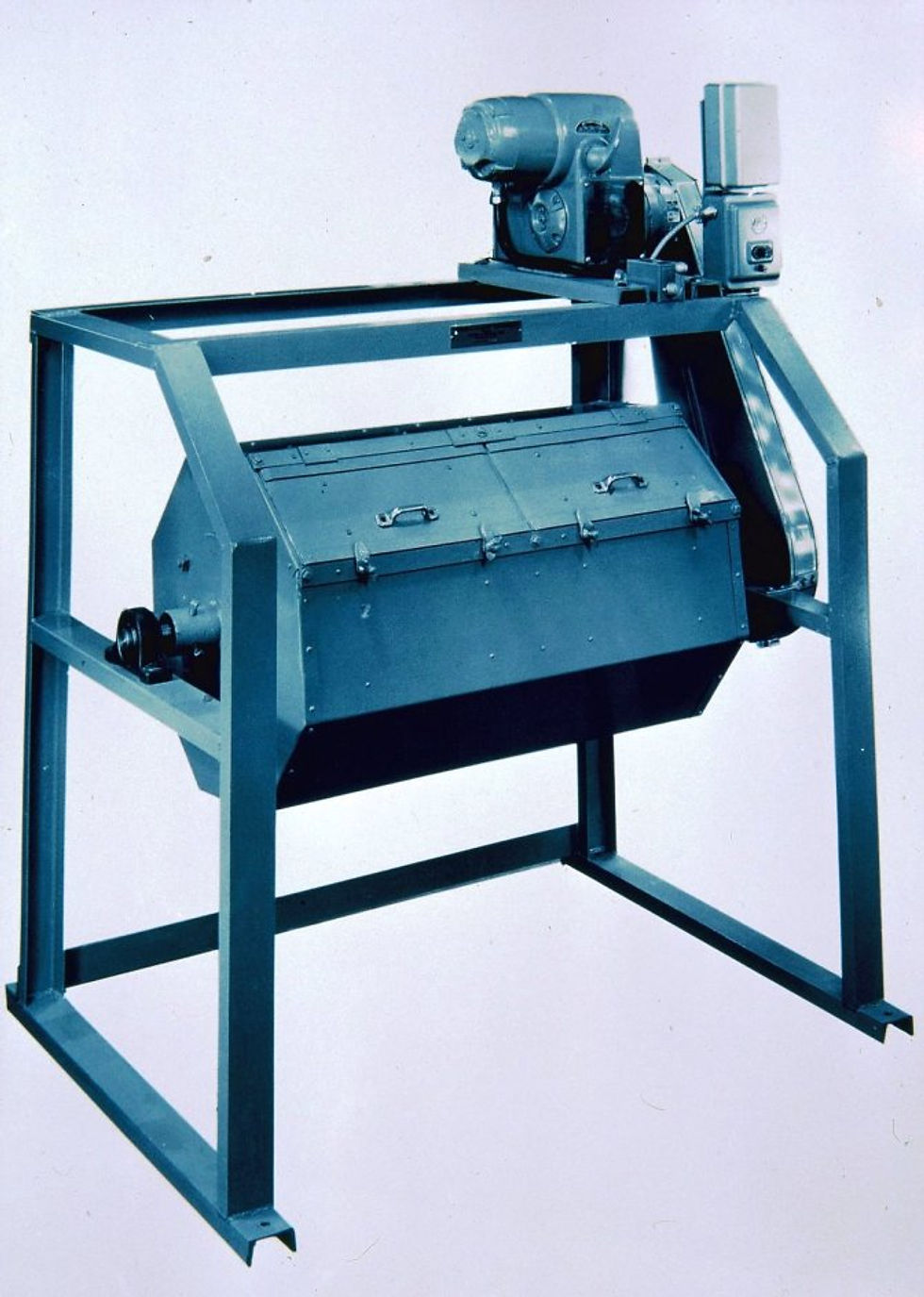
An example of a 30 in. x 36 in. octagonal horizontal barrel for dry process finishing plastics and light metals. Dry process barrels, such as this one were lined with hardwood panels. Dry agricultural media such as wooden pegs, walnut shell and corn cob treated with various abrasive, polishing or waxing preparations have been used for fine finishing of consumer articles such as eyewear, buttons and jewelry for many years to automate hand-buffing and polishing operations.
As is the case with most other mass finishing equipment, polyurethane, rubber, or linings made from similar material are used to extend equipment life, provide some measure of cushioning to parts, and furnish some measure of noise abatement. Although considered by some to be an outdated and obsolete finishing method, barrels still have a place in the finishing engineer’s repertoire. Although it is true that it is slower and presents some automation and materials handling challenges, it is sufficiently versatile to perform numerous finishing operations for many manufacturers. Furthermore, barrel finishing provides an excellent alternative for flat parts, which may nest in vibratory systems. Although perhaps requiring some measure of operator experience in order to be used effectively, barrel finishing is capable of producing some unique and desirable surface finishes and is highly efficient in compound and media usage.
Vibratory finishing systems
Vibratory finishing was introduced during the 1950s and, through a succession of design refinements, has become the primary workhorse of the industry. Equipment usually consists of a spring-mounted open chamber, lined with polyurethane or similar material, to which a vibratory motion generator is attached. The motion generator is usually mechanical in nature, consisting of a rotating shaft with eccentric weights affixed. (A few machines make use of electromagnetic motion generators.)

Examples of Bowl Shaped Vibratory Finishing Machines. Photo by Mark Riley, BV Products
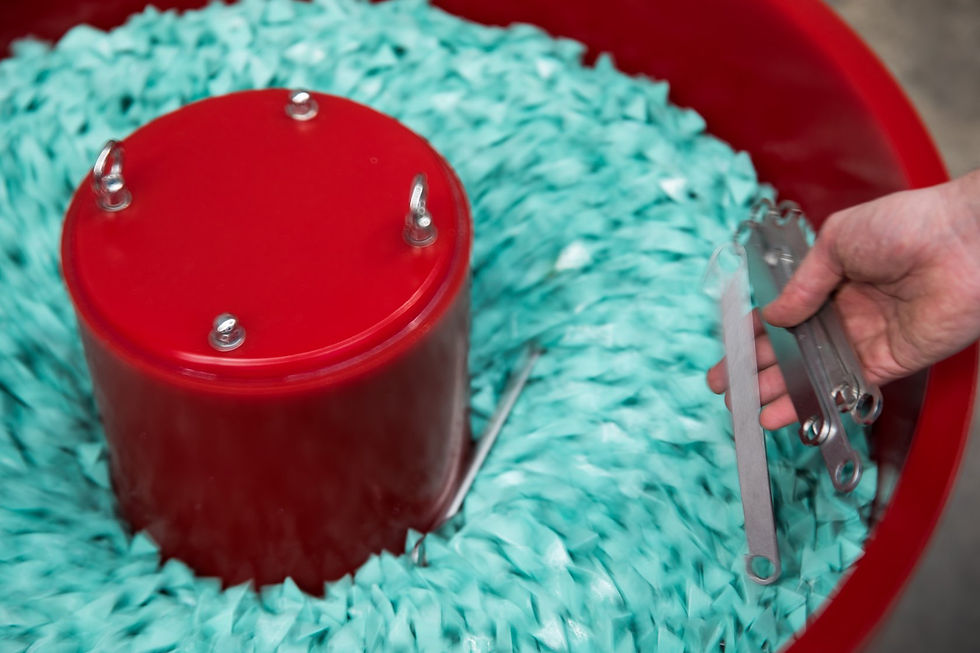
Bowl vibratory deburring and surface finishing machine in action. Photo courtesy of Mark Riley, BV Products
The motion of the media within the chamber can be controlled by adjusting the speed of rotation (frequency ranges between 900 and 3,000 rpm, more commonly between 1,200 and 1,800 rpm), the positioning of the eccentric weights, and the amount of the weight attached (amplitude: the amount of “rise and fall” being imparted to the container and media can range between 1/ in. [2 mm] to 3/ in. [10 mm]). The actual chambers are available in a variety of shapes (round bowl, oval, or U-shaped tub being the most common.) The adjustments noted above will not only affect the vibratory motion of the media but the roll or forward motion within the chamber (spiral motion in the case of many round bowls).
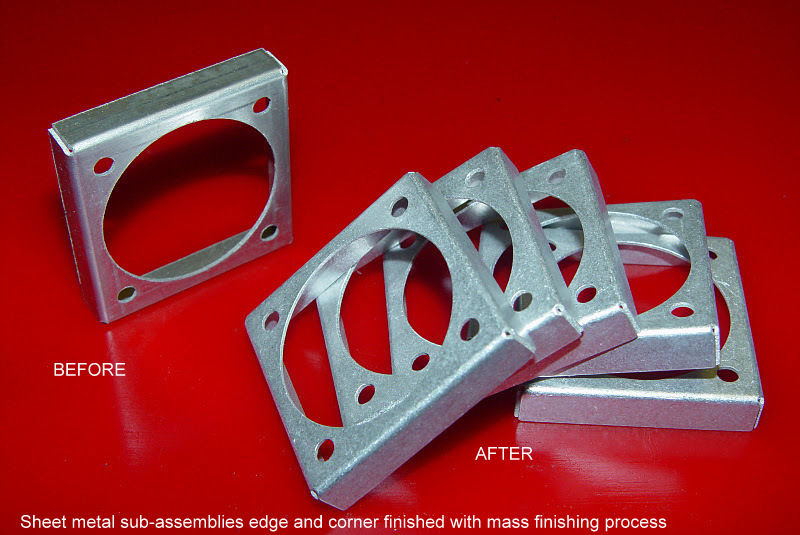
Above: Abrasive vibratory finishing of sheet metal fabricated component (Before and after)
A number of advantages have manifested themselves over traditional barrel finishing methods. Unlike barrel processing, the entire media mass is in motion at any given time, so parts are being constantly treated, making for shorter cycle times. The entire chamber is utilized to its full capacity and, in many cases, the vibratory motion of the machine can be harnessed to assist in unloading. Many round bowl equipment designs are capable of internal separation, where an integral separation deck is used to separate and retrieve media from parts being unloaded at the end of a cycle. The open nature of equipment allows for ease of operator monitoring of the process on a continuous basis.
Tub or Trough Style Vibratory Finishing Systems
This equipment ranges in size from 1 cubic foot (30 L) capacity up to 200 cubic feet (660 L). Tub vibrators are considered to have more aggressive media action than round-bowl machines, and they are capable of processing very large, bulky parts (as large as 6 ft by 6 ft) or potentially awkward part shapes (parts 40-ft long and longer). The vibratory motion generators consist of rotating shafts with sets of eccentric weights attached either at the bottom of the U-shaped tub or one of the sidewalls.
This equipment is usually loaded from the top of the chamber and usually unloaded through a discharge door located on a side panel. Parts and media can be screened on an external separation deck. This arrangement allows for relatively quick load/unload or media changeover cycles when compared with other equipment.
Tub-shaped or tubular-shaped vibrators are commonly utilized for continuous high volume applications where the time cycle required to process the parts is relatively short. Media return conveyors and feed hoppers are used to meter the correct ratio of media and parts to the loading area of the machine, while media and parts are separated on a continuous basis by a screen deck located at the unload or discharge area of the machine. Tub-type machinery is also used extensively for batch applications and can be easily sub-compartmentalized for parts that require total segregation from each other. A typical machine is shown below.
This slideshow requires JavaScript.
Above: Various vibratory finishing equipment configurations, including compartmented tub, Heavy duty tub, flow-through continuous and multiple bowls for two-step processing.

ABOVE: Large capacity tub style vibratory finishing machine for processing large structural parts such as this titanium airframe component. This process is being used to minimize the need for labor-intensive hand-deburring. Compressive stress equilibrium and part-to-part uniformity are also important advantages
Round-bowl Vibratory Systems
Round-bowl equipment normally has a processing chamber that resembles the bottom half of a doughnut. Although up to 20% slower than tub-style machines, and having occasionally more unwieldy media changeover routines, the advantages in automation and material handling for these machines have often given them an edge in any processing cost per part analysis. The vibratory motion generator on these machines is customarily a vertical shaft mounted in the center-post area of the bowl. Adjustments related to the eccentric weights on this shaft will affect the rolling motion of the media, as well as the forward spiral motion of the media in the bowl chamber. This spiral motion is one of the machine’s more salient advantages, as it promotes an even distribution and segregation of parts in the mass, thus lessening the chance of part-on-part contact.
This slideshow requires JavaScript.
ABOVE: Isotropic Micro-Finishing Part Applications. Photos and Video by Mark Riley, BV Products
Like tub machines, equipment size varies from small bench models, whose capacity are measured in quarts or gallons, to very large equipment in excess of 100 ft3 capacities. Successful processing requires appropriate media and compound selection, correct amplitude and frequency adjustments of the motion generator, and precisely determined water flow rate and compound metering rates. Unlike barrel systems, whose water levels are determined once at the beginning of the cycle, vibratory systems have a constant input and throughput of water into the system (both flow-through and recirculation systems are employed, although flow-through is generally much preferred).
Water levels are critical to process success. Too much water will impede the vibratory motion of the mass. Too little will permit a soils/sludge buildup on the media, reducing its cutting efficiency. Flow-through functions can be automated with appropriate controls and metering devices. For parts requiring relatively short cycle times, round-bowl machines can be configured to perform in a continuous mode, the parts being metered in and then making one pass around the bowl, and exiting via the internal separation deck. Some designs include a spiral bottom to enhance loading from the machine onto the separation deck, lessening the likelihood of part-on-part contact at the entrance to the separation deck.
Ease of use and economy are the hallmarks of vibratory finishing methods and have contributed to making this perhaps the most accepted deburring and surface conditioning method for finishing parts in bulk. The equipment performs well in either batch or continuous applications. Standard applications usually can be run most economically in round-bowl-type equipment. Larger parts may require more specialized tub-type equipment, large volumes of parts, which can be processed in relatively short cycles, can make use of continuous tub or bowl equipment, or even multi-path equipment. The latter can offer parts transfer from one operation to a secondary-type operation within the confines of the same machine, but different chambers. The vibratory action itself often will preclude the ability to develop super-finishes or micro-finishes (Exception: Chemically-Assisted Vibratory Iso-finishing.) These types of finishes are often best attempted in equipment in which the media action has a more rolling, glancing, or linear action than the short-stroke movement characteristic of vibratory finishing. Some micro-finishing can be achieved when chemical accelerants (usually acidic in nature) are used in a multi-stage vibratory process where the parts are first finished and smoothed abrasively and then treated with non-abrasive media and specialized chemical compounds to produce functionally useful low micro-inch polished surfaces. This type of process is widely used in the high-performance motorsports, wind-energy and aerospace industries to improve the efficiency and durability of cooperating metal components.
This slideshow requires JavaScript.
Above: Examples of Automotive and Motor-sports components processed with Chemically Assisted Vibratory processing. (Photos by Mark Riley, BV Products)
Centrifugal Iso-Finishing (High Energy Barrel Systems)
Centrifugal barrel finishing (CBF) is a high-energy finishing method, which has come into widespread acceptance in recent years. Although not nearly as universal in application as vibratory finishing, a long list of important CBF applications have been developed in the last few years, especially with manufacturers with demanding edge and surface finish requirements.
Below: Centrifugal Iso-Finishing (or Centrifugal Barrel Finishing) Machines
This slideshow requires JavaScript.
Videos above demonstrate centrifugal isotropic finishing and micro-finishing with Centrifugal Barrel Iso-Finishing Equipment
Centrifugal Iso-Finishing is similar in some respects to barrel finishing, in that a drum-type container is partially filled with media and set in motion to create a sliding action of the contents, but the method is different from other finishing methods in some significant ways. Among these are the high pressures developed in terms of media contact with parts, the unique sliding action induced by rotational and centrifugal forces, and accelerated abrading or finishing action. As is true with other high energy processes, because time cycles are much abbreviated, surface finishes can be developed in minutes, which might tie up conventional equipment for many hours.
The principle behind Centrifugal Iso-Finishing is relatively straightforward. Opposing barrels or drums are positioned circumferentially on a turret. (Most systems have either two or four barrels mounted on the turret; some manufacturers favor a vertical and others a horizontal orientation for the turret.) As the turret rotates at high speed, the barrels are counter-rotated, creating very high G-forces or pressures, as well as considerable media sliding action within the drums. Pressures as high as 50 Gs have been claimed for some equipment, but pressures in the 10-13 G range are more common. The more standard equipment types range in size from 1 cubic foot (30 L) to 10 cubic feet (300 L). Custom equipment up to 20 cubic feet (600 L.)have been built. See the video below:
This slideshow requires JavaScript.
Above: Some Centrifugal Iso-Finishing Equipment and Part Applications
Media used in these types of processes tend to be a great deal smaller than the common media sizes chosen for the barrel and vibratory processes. The smaller media, in such a high-pressure environment, are capable of performing much more work than would be the case in lower energy equipment. They also enhance access to all areas of the part and contribute to the ability of the equipment to develop very fine finishes. In addition to the ability to produce meaningful surface finish effects rapidly, and to produce fine finishes, CBF has the ability to impart compressive stress into critical parts that require extended metal fatigue resistance. Small and more delicate parts can also be processed with confidence, as the unique sliding action of the process seems to hold parts in position relative to each other, and there is generally little difficulty experienced with part impingement. Dry process media can be used in certain types of equipment and is useful for light deburring, polishing, and producing very refined super-finishes.
This slideshow requires JavaScript.
Above: Photo gallery of some high-energy isotropic finishing applications
This slideshow requires JavaScript.
Photo-gallery above: Centrifugal Isotropic Finishing Applications. Photos by Mike Klein, IsoFinishng, Inc.
Practicality and questions of cost-effectiveness often determine whether high-energy methods are selected over a conventional barrel or vibratory processes. If acceptable surface finishes can be developed in a few hours, conventional equipment may be the most economical alternative. CBF equipment’s strong suit is the ability to develop surface finishes that may require over-lengthy time cycles in conventional equipment and the ability to develop a wide range of special surface finishes required for demanding and critical applications. However, these high energy finishing processes are becoming more commonly utilized in the machining industry as more complex high-tolerance parts with difficult deburring and surface finish challenges emerge.
Centrifugal disk
Another high-energy finishing method that has become popular in recent years is the centrifugal disk. Most equipment is in the form of a cylinder or bowl with a spinning disk at the bottom. This disk propels the media upward against the interior sidewalls of the cylinder, which act as a brake, causing the mass to turn over and return to the center of the disk, where it is set in motion again. This unique media action is said to perform abrading operations at five to 10 times the speed of conventional vibratory action. As the machine is basically an open-end chamber, in-process inspection and monitoring are possible. Faster time cycles can also reduce work in progress and make the equipment a good choice for manufacturing cells. In general, larger or lengthy parts are not good candidates for disk finishing and, at times, higher than usual media-to-part ratios must be maintained to avert part-on-part contact. Equipment size ranges from 1 cubic foot (15 L) bench-top models to 20 cubic foot (600 L) floor machines.
One critical area of attention on this equipment is the gap between the spinner disk and the ring located around the exterior of the disk. Particles or fines of media that are capable of lodging in this area may cause significant damage to certain types of equipment. Correct media maintenance and attention to water flow-through rates can be an important factor in extending the useful service life of main components. Some equipment has the ability to run either wet or dry process media. Many equipment models, however, are designed for dedicated use in either wet or dry finishing and should not be used in the other mode without extensive consultation with the manufacturer. A centrifugal disc finishing system is shown in the video above.
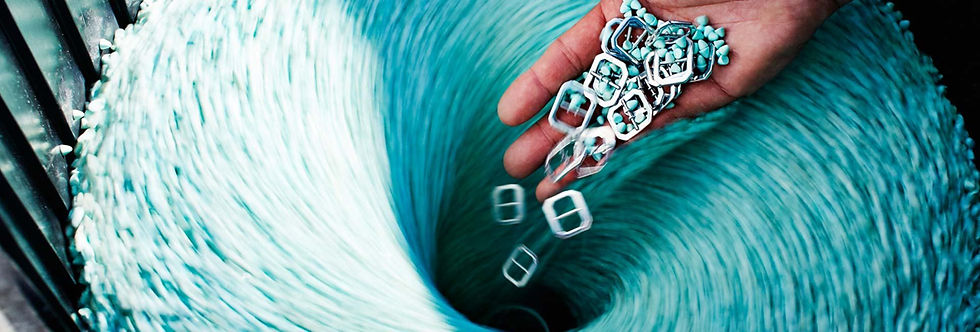
A centrifugal disk in operation. Photo courtesy of Mark Riley, BV Products
Spin/Spindle Finish Equipment
Spindle finishing is performed by fixturing parts at the end of a (stationary, rotating, planetary, or oscillating) spindle, and arranging for the part to be immersed in a mass of fine media, which may be vibrating, stationary, or directed at the workpiece by a spinner arrangement or rotation of the entire media chamber. As all parts must be fixtured, impingement from part-on-part contact is nonexistent. Time cycles can be very short, ranging from a few seconds to a few minutes. Equipment from various manufacturers may feature single or multi-fixture capabilities. Types of operations vary from heavy abrasive operations for deburring and stock removal, to the use of very fine dry polishing media in some equipment to develop color-buff-type finishes. One recent development in spindle finishing is the Turbo-finish method, which involves the high-speed rotation of components in a fluidized bed of fine abrasive or polishing material.
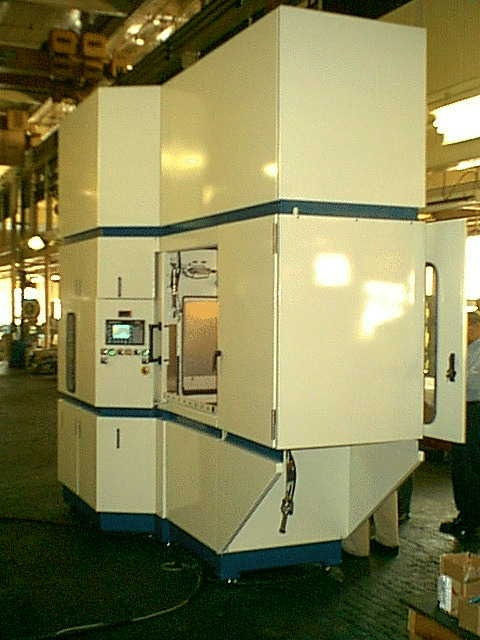
Turbo-Finish Model TF-522 Turbo-Abrasive Machining Center for high speed dry horizontal spindle finishing. Photo courtesy Turbo-Finish Corporation
This slideshow requires JavaScript.
Above: Turbo-Finish (High-speed dry spindle finishing) Photo gallery courtesy of Dr. Michael Massarsky, Turbo-Finish Corporation. Below a Turbo-Finish Model 522 deburring a twenty inch rotating turbine component
This slideshow requires JavaScript.
Wet Process Spindle Finishing
Unlike the Turbo-Finish method, which is a completely dry method utilizing relatively small granular abrasive media wet process spindle finishing uses conventional ceramic performed abrasive preformed shapes. In contrast with the dry Turbo-Finish method, which makes use of vertical spindle orientation for loading and unloading and horizontal orientation for part processing. Wet spindle operations load and unload with a more horizontal spindle orientation, and process rotating parts (turbine and compressor wheels, gears and other rotating hardware vertically.)
Also referred to as a “slurry deburring” or “flowing abrasive” machine, wet-process spindle finishing equipment generally includes a circular rotating tub that holds loose abrasive media and rotary spindles to which parts are held or fixtured. The result is a “form-fitting grinding wheel”.
The process is well suited to the deburring of gears, as well as to a wide range of complex parts including bearing cages, splined shafts, pump rotors, and jet compressor discs and blades. The fixtures are designed to hold the workpiece so that areas to be treated are exposed. The tub is rotated in one direction, while the spindle or spindles normally turn in the opposite direction. As the tub is rotated, the media is pushed to the outside by centrifugal force. Fixtures usually consist of chucking devices that are spring-loaded for clamping and released by an air cylinder, making the machine operation extremely simple. More sophisticated parts might require hydraulic hold tooling. Because parts are fixtured, there is no danger of impingement, nicks, or scratches from parts colliding with one another.
Mass Finishing Media
Media can be generally defined as the loose material contained in the work area of a mass finishing machine, which, when in motion, performs the work desired on part surfaces. Media may be natural or synthetic, abrasive or nonabrasive, random or pre-formed in shape. Much of the versatility inherent to mass finishing processes can be traced to the wide array of media types, sizes, and shapes available to industry. What follows is a rundown of the more commonly used media types.
Natural/mineral media
Crushed and graded stone was once the predominant source for tumbling abrasives in the early days on barrel finishing. Raw source material included both limestone and granite. Some naturally sourced materials still find some barrel finishing applications today, such as corundum and novaculite. As a general rule, problems with fracturing, rapid wear and attrition rates, lodging, and disposal of the high amount of solid or sludge waste material created mitigates against crushed and graded mineral materials being an effective media for many applications despite the lower cost.
Agricultural media
A variety of granular media such as ground corn cob, walnut shell, pecan shell, sawdust, and wooden pegs are used in all of the equipment discussed. These dry process media are used in conjunction with various fine abrasive compounds similar to compounds that might be used in buffing applications. These media are often used in secondary cycles, after initial cutting and smoothing, to produce very fine reflective finishes. Attractive decorative finishes can be produced for jewelry and other consumer articles and, by extension, very low Ra finishes can be produced for precision industrial components to produce important functional surface effects.

Dry process media such as these are used in conjunction with fine smoothing or polishing abrasive materials to produce micro-finishes or super-finishes in a variety of mass finishing equipment. These materials here are often used in secondary operations following the use of more abrasive materials that are used with aqueous compounds. The hardwood media was used extensively in dry barrel polishing of plastics and soft metals. The granular treated media is most often found in high energy mass finishing systems as a polishing material (Photo by Tyha Davidson)
Preformed abrasive media
These media have largely replaced the crushed and graded mineral materials mentioned above. Media preforms are made from either extruded ceramic/abrasive shapes, which are fired, or resin-bonded, or which have been molded. The preform concept was an important one for the finishing industry. Unlike the more random shaped mineral media, size and shape preform selection could prevent media lodging and promote access to complex part shapes. The uniformity and predictable wear rates of the media also made it possible to prevent both lodging and separation problems caused by undersized, worn media. A wide variety of shapes have been developed by various manufacturers over the years to accommodate these requirements, including cones, triangles, angle-cut cylinders, wedges, diamonds, tri-stars, pyramids, arrowheads, and others.
Ceramic media are generally harder and more abrasive and are customarily used for more aggressive applications. Plastic media, as a rule, are somewhat softer and capable of producing finer finishes.
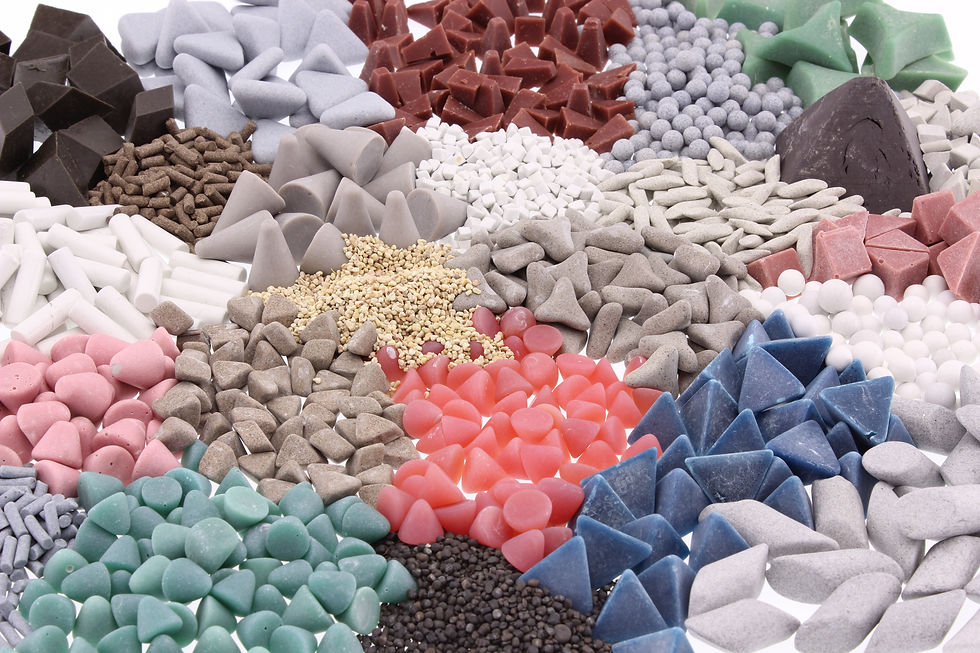
A wide variety of finishing media is available for mass finishing. Among those shown in the illustration are ceramic preformed abrasive shapes used for deburring and smoothing of ferrous and harder alloys. Plastic media used for deburring soft alloys, and in secondary operations to achieve further surface refinement. Non-abrasive media, such as porcelain and sintered bauxite are shown. These are useful in producing burnished surfaces and are also used to develop compressive stress in high-energy finishing operations that can rival that obtained by shot-peening. Dry agricultural media is also shown, this material is used in secondary operations to produce reflective polished surfaces in decorative finishing and also produce very low micro-inch surfaces useful for improving wear resistance and fatigue failure resistance in critical precision parts.
Burnishing media
Media made from case hardened steel, stainless steel, and other formulations are used widely in barrel and vibratory equipment to produce burnished surfaces. These media are very heavy (300 lb/ft3 versus 100 lb/ft3 for ceramic media) when compared with other media types and are nonabrasive in nature. It should be noted that not all vibratory equipment can turn or roll steel media. Because of the weight, enhanced or heavier duty equipment may be necessary. The media performs by peening or compressive action; the surface material is not removed, as is the case with abrasive media. Burnishing processes with steel media can be used either to develop reflective decorative finishes or provide functional finishes. One attribute of burnishing processes is that part surfaces are often work-hardened, which can extend the service life of components in moving assemblies. Steel media can be extremely long lasting, if care is taken to prevent corrosion of surfaces while in use and/or storage. Nonabrasive porcelain or sintered bauxite media are also used for some burnishing procedures and are prevalent in some centrifugal finishing applications.
Compounds
Many abrasive and burnishing applications use water with specially formulated compound additives. The proper selection and dosage of these additives (in either liquid or dry powder form) can have a critical effect on the viability of the process. These compounds perform an assortment of functions including water conditioning or softening, pH control, oil/soil and metallic and abrasive fine suspension to prevent redeposition on part surfaces, rust inhibition, cleaning, foam development or control, as well as media lubricity control. Some special compounds are used to chemically accelerate finishing cycle times; some of these may be intensely acidic or corrosive and may require some special handling.
This slideshow requires JavaScript.
Contributing Editor: Dave Davidson, Deburring/Finishing Technologist 509.563.9859 | ddavidson@deburring-tech-group.com| dryfinish.wixsite.com/iso-finish
If you have parts that need edge or surface finishing improvement and would like to have FREE sample part processing and a quotation developed for finishing the parts please contact Dave Davidson at ddavidson@deburring-tech-group.com I can also be reached at 509.563.9859 Information about equipment for bringing Centrifugal Iso-Finishing capability to your facility is also available…
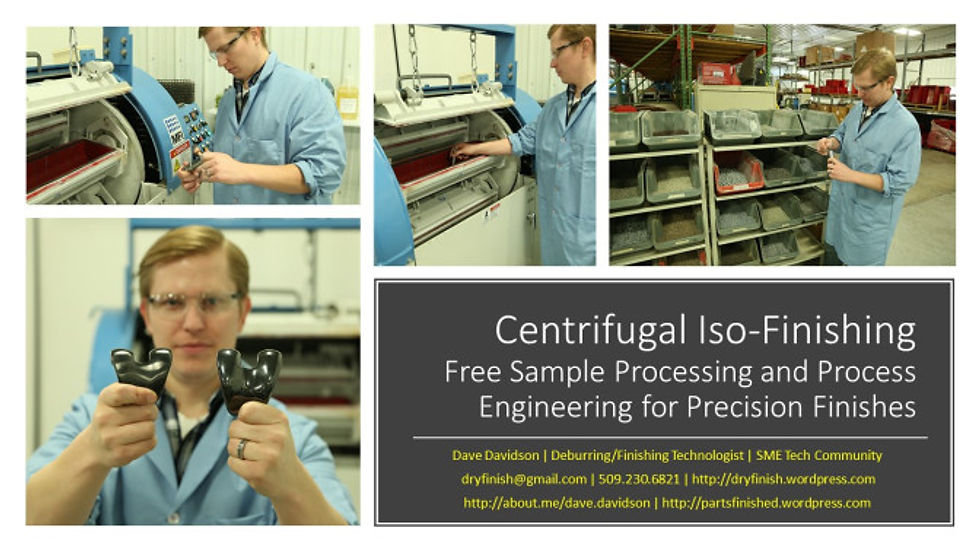
AUTHOR BIOGRAPHY – David A. Davidson, [dryfinish@gmail.com]
Mr. Davidson is a deburring/surface finishing specialist and consultant. He has contributed technical articles to Metal Finishing and other technical and trade publications and is the author of the Mass Finishing section in the current Metal Finishing Guidebook and Directory. He has also written and lectured extensively for the Society of Manufacturing Engineers, Society of Plastics Engineers, American Electroplaters and Surface Finishers Association and the Mass Finishing Job Shops Association. Mr. Davidson’s specialty is finishing process and finishing product development.

Comments