Isotropic Mass Finishing for Surface Integrity and Part Performance
- Dave Davidson
- Nov 15, 2013
- 11 min read
Feature photo above: Isotropic Micro-Finishing of Gears by Mark Riley, BV Products
Contributing Editor: Dave Davidson | Deburring/Finishing Technologist ddavidson@deburring-tech-group.com | dryfinish@wixsite.com/iso-finish
When presented with edge and surface finishing problems, many manufacturers continue to reach for solutions that rely on out-of-date, time-consuming and labor-intensive methods. It is still not unusual to see precision parts and critical hardware being manually handled and edge and surface finishing operations being performed with abrasive hand tools, or manually controlled power tools that utilize coated abrasives or abrasive filaments. This situation often arises from insufficient planning and a lack of understanding what will be required to render the manufactured part or component acceptable for consumer use or end-user application. At the root of the problem is a manufacturing and design engineering culture that considers its work done when the part comes off the machining center or the fabricating machine. Too often, part edge and surface condition is simply someone else’s problem. In many cases not much thought is given to the problem until production is in full swing and parts start to fail quality assurance standards because they have burrs or undesirable surface conditions that not only affect function and performance but send costs through the roof.
This slideshow requires JavaScript.
Isotropic Micro-Finishing of Precision Components. Photos by Mark Riley, BV Products and Dave Davidson | SME Tech Community Advisor | ddavidson@deburring-tech-group.com | Sample processing available.
The videos above show isotropic finishing operations with high-speed centrifugal finishing systems. Dave Davidson | SME Tech Community advisor | ddavidson@deburring-tech-group.com This is a situation that deserves and is getting an increasing amount of scrutiny. It is a subject repeatedly discussed at the newly formed “Deburring, Edge-Finish, and Surface Conditioning Technical Group” sponsored by the Society of Manufacturing Engineers in Dearborn, MI. At one of the group’s monthly national teleconferences, Steven Alviti, a deburring and surface finish expert summarized his experience this way: “This group has been needed for a long time now. The sentiments expressed at the phone conference still hold true to this day. I face the same scenario time after time. The company develops a new product, they cost the product, they work out the productivity to decide what machinery they need to supply the demand, they spend $500,000.00 – $1,000,000.00 for CNC machinery, they get orders and start producing, they now have product to ship — but it has a burr! Now we get the call, after they have thrown five or six people at the cell with microscopes, exact-o-knifes, files, sandpaper and worse, and have figured out that they are in a jam. Now we come up with a mechanical or automated solution, but it’s like pulling teeth to have them spend $10,000 or $20,000 on a solution that should have been part of the initial phase. What ever this group can do to bring mass finishing into the initial stages of engineering will be a benefit to all involved.”

(Before and After Surfaces) This photograph was taken with an electron microscope at 500x magnification. Both micrographs to the left shows the surface of a raw unfinished “as cast” turbine blade (or a ground surface). The rough initial surface finish as measured by profilometer was in the 75 – 90 Ra (µin) range. As is typical of most cast, ground, turned, milled, EDM and forged surfaces this surface shows a positive Rsk [Rsk – skewness – the measure of surface symmetry about the mean line of a profilometer graph. Unfinished parts usually display a heavy concentration of surface peaks above this mean line, generally considered to be an undesirable surface finish characteristic from a functional viewpoint.] AFTER PROCESSING — After) These SEM photomicrographs to the right (500X magnification) was taken after processing the same turbine blade in a multi-step procedure utilizing centrifugal barrel methods with both grinding and polishing free abrasive materials in sequence. The surface profile has been reduced from the original 75 – 90 Ra (µin.) to a 5-9 Ra (µin.) range. Additionally, there has been a plateauing of the surface and the resultant smoother surface manifests a negative skew (Rsk) instead of a positive skew. This type of surface is considered to be very “functional” in both the fluid and aerodynamic sense. The smooth, less turbulent flow created by this type of surface is preferred in many aerodynamic, automotive and other high force loading applications. Another important consideration the photomicrographs indicate is that surface and sub-surface fractures seem to have been removed. Observations with backscatter emission with a scanning electron microscope (SEM) gave no indication of residual fractures.
The costs of neglecting to consider deburring and surface conditioning in production planning and engineering can be and often is – substantial. Frequently overlooked however, are the potentially serious problems that can develop from the ad hoc and interim solutions that are selected to deal with what now has become a manufacturing crisis. The manufacturers who resort to hand or manual finishing do not do so because of its cost, on a per piece basis, it is by far the most costly method of handling the problem – but often it is the most obvious solution and the easiest and the quickest to implement. Hiring some less-skilled temporary employees, and arming them with hand tools to attack the problem may not be very imaginative, but it is certainly much less strenuous from an engineering perspective than approaching the budgetary, capital asset acquisition and purchasing processes for something as mundane as deburring and surface finishing equipment. The reason this problem persists into the 21st century, is that there is a very imperfect understanding of the hidden and more serious cost this manual and uncontrolled approach imposes.
This slideshow requires JavaScript.
(Above: Sample processing of parts is available at no charge. Photos by Dave Davidson | SME MMR Tech Community | ddavidson@deburring-tech-group.com The parts above show a representation of the fine finishes that can be created with high energy finishing methods such as centrifugal isotropic finishing, The combination of low surface profiles. negative skew, isotropic surfaces and planarization can extend service life and improve performance.
The first casualty of this manual approach is the investment the manufacturer has made, often in the millions, for precise and computer-controlled manufacturing equipment. The idea behind this investment was to have the ability to produce parts that are uniformly and carefully manufactured to exacting specifications and tolerances. At this point, in too many cases, the parts are then handed off to manual deburring and finishing procedures that will guarantee that no two parts will ever be alike. Moreover, the increased complexity and precision requirements of mechanical products have reinforced the need for accurately producing and controlling the surface finish of manufactured parts. Variations in the surface texture can influence a variety of performance characteristics. The surface finish can affect the ability of the part to resist wear and fatigue; to assist or destroy effective lubrication; to increase or decrease friction and/or abrasion with cooperating parts and to resist corrosion. As these characteristics become critical under certain operating conditions, the surface finish can dictate the performance, integrity and service life of the component.
The role of mass finishing processes (barrel, vibratory and centrifugal finishing) as a method for removal of burrs, developing edge contour and smoothing and polishing parts has been well established and documented for many years. These processes have been used in a wide variety of part applications to promote safer part handling (by attenuation of sharp part edges) improve the fit and function of parts when assembled, and produce smooth, even micro-finished surfaces to meet either functional or aesthetic criteria or specifications. Processes for developing specific edge and/or surface profile conditions on parts in bulk are used in industries as diverse as the jewelry, dental and medical implant industries on up through the automotive and aerospace industries.

– These graphs graphically illustrate in both2-D and 3-D the difference between an as ground positively skewed surface, and the same typical surface processed with a sequence of high energy loose media operations to produce an improved surface topology that that is potentially very useful for mission critical components that require improved wear, fracture or fatigue resistance
Less well known and less clearly understood is the role specialized variants of these types of processes can play in extending the service life and performance of critical support components or tools in demanding manufacturing or operational applications.
Industry has always been looking to improve surface condition to enhance part performance, and this technology has become much better understood in recent years. Processes are routinely utilized to specifically improve the life of parts and tools subject to failure from fatigue and to improve their performance. These improvements are mainly achieved by enhancing part surface texture in a number of different, and sometimes complementary, ways.

This photo of typical gas engine turbine discs show clearly the difference between an as machined or ground component and one that has been edge and surface finished to produce isotropic surface effects with machining or grinding lines completely blended in
To understand how micro-surface topography improvement can impact part performance, some understanding of how part surfaces developed from common machining, grinding and other methods can negatively influence part function over time. A number of factors are involved:

Edge and surface condition can produce dramatic improvements in performance and service life as this comparison between manually deburred and mechanically edge-contoured parts demonstrates. The Turbo-Finish method also develops compressive stress and stress equilibrium in large critical rotating components. Courtesy of Turbo-Finish Corporation
High-speed dry spindle finishing of aerospace rotating parts. This process has reduced deburring work taking many hours to automated machine cycles of just a few minutes. Video credit: Dr. Michael Massarsky | Turbo-Finish Corporation | michael@turbofinish.com
Positive vs. Negative Surface Skewness. The skew of surface profile symmetry can be an important surface attribute. Surfaces are typically characterized as being either negatively or positively skewed. This surface characteristic is referred to as Rsk (Rsk – skewness – the measure of surface symmetry about the mean line of a profilometer graph). Unfinished parts usually display a heavy concentration of surface peaks above this mean line, (a positive skew). It is axiomatic that almost all surfaces produced by common machining and fabrication methods are positively skewed. These positively skewed surfaces have an undesirable effect on the bearing ratio of surfaces, negatively impacting the performance of parts involved in applications where there is substantial surface-to-surface contact. Specialized high energy finishing procedures can truncate these surface profile peaks and achieve negatively skewed surfaces that are plateaued, presenting a much higher surface bearing contact area. Anecdotal evidence confirms that surface finishing procedures tailored to develop specific surface conditions with this in mind can have a dramatic impact on part life. In one example the life of tooling used in aluminum can stamping operations was extended 1000% or more by improved surface textures produced by mechanical surface treatment.
This slideshow requires JavaScript.
Directionalized vs. Random (Isotropic) Surface Texture Patterns. Somewhat related to surface texture skewness in importance is the directional nature of surface textures developed by typical machining and grinding methods. These machined surfaces are characterized by tool marks or grinding patterns that are aligned and directional in nature. It has been established that tool or part life and performance can be substantially enhanced if these types of surface textures can be altered into one that is more random in nature. Post-machining processes that utilize free or loose abrasive materials in a high energy context can alter the machined surface texture substantially, not only reducing surface peaks, but generating a surface in which the positioning of the peaks has been altered appreciably. These “isotropic” surface effects have been demonstrated to improve part wear and fracture resistance, bearing ratio and improve fatigue resistance.

Turbine blades can be finished down to low micro-inch surface finish values of between 5 -10 micro-inches Ra with Centrifugal isotropic Finishing
Residual Tensile Stress vs. Residual Compressive Stress. Many machining and grinding processes tend to develop residual tensile stresses in the surface area of parts. These residual tensile stresses make parts susceptible to premature fracture and failure when repeatedly stressed. Certain high-energy mass finishing processes can be implemented to modify this surface stress condition, and replace it with uniform residual compressive stresses. Many manufacturers have discovered that as mass

In side by side testing, Centrifugal Iso-Burnishing processes developed very similar compressive stress levels to that obtained by shot-peening.
finishing processes have been adopted, put into service, and the parts involved have developed a working track record, an unanticipated development has taken place. Their parts are better—and not just in the sense that they no longer have burrs, sharp edges or that they have smoother surfaces. Depending on the application: they last longer in service, are less prone to metal fatigue failure, exhibit better tribological properties (translation: less friction and better wear resistance) and from a quality assurance perspective are much more predictably consistent and uniform. The question that comes up is why do commonly used mass media finishing techniques produce this effect? There are several reasons. The methods typically are non-selective in nature. Edge and surface features of the part are processed identically and simultaneously. These methods also produce isotropic surfaces with negative or neutral surface profile skews. Additionally, they consistently develop beneficial compressive stress equilibrium. These alterations in surface characteristics often improve part performance, service life and functionality in ways not clearly understood when the processes were adopted. In many applications, the uniformity and equilibrium of the edge and surface effects obtained have produced quality and performance advantages for critical parts that can far outweigh the substantial cost-reduction benefits that were the driving force behind the initial process implementation.

This large aircraft engine turbine disk has been processed with the Turbo-Finish method. This dry abrasive finishing method has been successful in bringing mass media finish economies to large complex rotationally oriented parts while simultaneously developing significant compressive stress. In addition to the uniform and consistent edge contours developed, the method also produces highly sophisticated isotropic surface finishes by radically altering the character of the as- machined or as-ground surface finish. PHOTO courtesy Dr. Michael Massarsky, Turbo-Finish Corporation
This assertion has been affirmed by both practical production experience and validation by experiment in laboratory settings. David Gane and his colleagues at Boeing have been studying the effects of using a combination of fixtured-part vibratory deburring and vibratory burnishing (referred to by them as “Vibro-peening” or “Vibro-strengthening”) processes to produce (1) sophisticated edge and surface finish values and (2) beneficial compressive stress to enhance metal fatigue resistance. In life cycle fatigue testing on titanium test coupons it was determined that the vibro-deburring/burnishing method produced metal fatigue resistance that was comparable to high-intensity peening that measured 17A with Almen strip measurements. The striking difference between the two methods however, is that the vibratory burnishing method produced the effect while retaining an overall surface roughness average of 1 μm (Ra), while surface finish values on the test coupon that had been processed with the 17A high intensity peening had climbed to values between 5-7 μm (Ra). The conclusion the authors reached in the study was that the practicality and economic feasibility of the vibro-deburring and burnishing method increased with part size and complexity.

The machining and milling lines on this medical device have been blended in using centrifugal barrel finishing. This is an important functional characteristic as the device is utilized in applications where it is placed in the body’s cavity.
Dr. Michael Massarsky of the Turbo-Finish Corporation was able to supply comparative measurements on parts processed by his method for edge and surface finish improvement. Utilizing this spindle oriented deburr and finish method it is possible to produce compressive stresses in the MPa = 300 – 600 range that formed to a surface layer of metal to a depth of 20 – 40 μm. Spin pit tests on turbine disk components processed with the method showed an improved cycle life of 13090 ± 450 cycles when compared to the test results for conventionally hand deburred disks of 5685 ± 335 cycles, a potential service life increase of 2 – 2.25 times, while reducing the dispersion range of cycles at which actual failure occurred. Vibratory tests on steel test coupons were also performed to determine improvements in metal fatigue resistance. The plate specimens were tested with vibratory amplitude of 0.52 mm, and load stress of 90 MPa. The destruction of specimens that had surface finishes developed by the Turbo-Finish method took place after:
(3 – 3.75)*104 cycles
a significant improvement over tests performed on conventionally ground plates that started to fail after:
(1.1 – 1.5)*104 cycles.
SUMMARY:

Mass media finishing techniques (barrel, vibratory, centrifugal and spindle finish) can be used to improve part performance and service life, and these processes can be tailored or modified to amplify this effect. Although the ability of these processes to drive down deburring and surface finishing costs, when compared to manual procedures, is well known and documented, their ability to dramatically affect part performance and service life are not. This facet of edge and surface finish processing needs to be better understood and deserves closer study and documentation. Industry and public needs would be well served by a research consortium of partners at the industry, university and governmental agency levels to better understand the role surface textures and stress equilibrium play in enhanced component life and performance . At the time of this writing possible FAA intervention bringing the use of manual deburring techniques on commercial aircraft engine components under closer control are apparently being considered.
ACKNOWLEDGEMENTS: The authors wishes to acknowledge the technical assistance of the following members of the Society of Manufacturing Engineer’s DESC Technical Group [Deburring, Edge-Finish, Surface Conditioning]. Dr. Michael Massarsky, Turbo-Finish Corporation; David H. Gane, Boeing; Edward F. Rossman Ph. D., Boeing; Jack Clark, Surface Analytics LLC; LaRoux Gillespie, PE, CMfgE, Deburring Consultants and SME; Rodney Grover, Society of Manufacturing Engineers.
This slideshow requires JavaScript.
AUTHOR BIOGRAPHY – David A. Davidson, [dryfinish@gmail.com]
Mr. Davidson is a deburring/surface finishing specialist and consultant. He has contributed technical articles to Metal Finishing and other technical and trade publications and is the author of the Mass Finishing section in the current Metal Finishing Guidebook and Directory. He has also written and lectured extensively for the Society of Manufacturing Engineers, Society of Plastics Engineers, American Electroplaters and Surface Finishers Association and the Mass Finishing Job Shops Association. Mr. Davidson’s specialty is finishing process and finishing product development.
For indormation contact Mr, Davidson at ddavidson@deburring-tech-group.com and see the websites at https://dryfinish.wixsite.com/iso-finishh and https://wordpress.com
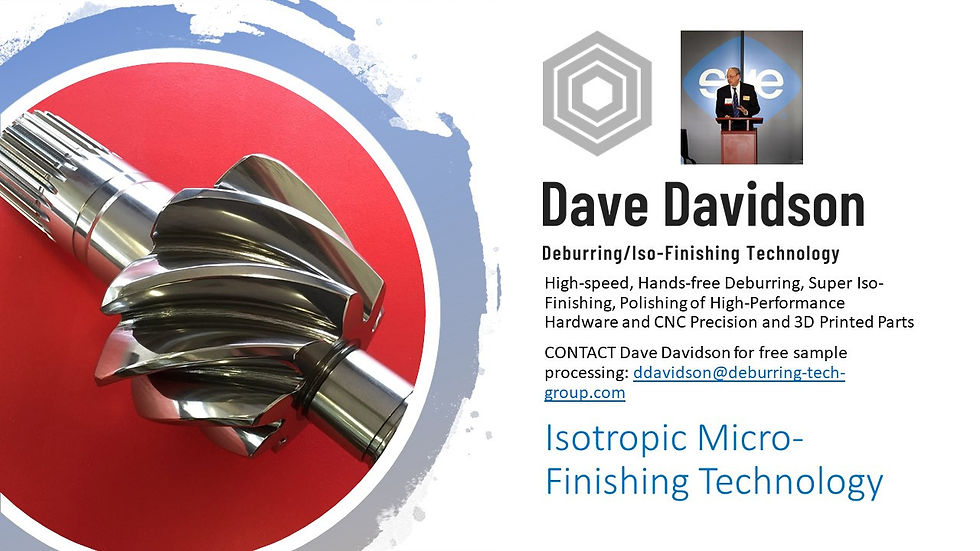
Comments