Isotropic Micro-Finishing Automotive Parts
- Dave Davidson
- Mar 23, 2017
- 1 min read
[Above Photo by Mark Riley, BV Products]
Isotropic Micro-Finishing and Super-Finishing is used to develop finishes that can actually improve functional performance and increase the service life potential of many types of manufactured parts. It has special application for engine components in high-performance racing engine industry. There are a variety of benefits to processing parts to develop isotropic surfaces. They include:
Reducing Friction, Vibration and Noise
Improve shifting
Extend Service Life and Reduce Maintenance Costs
Reducing Lubricant Temperature
Improve performance.
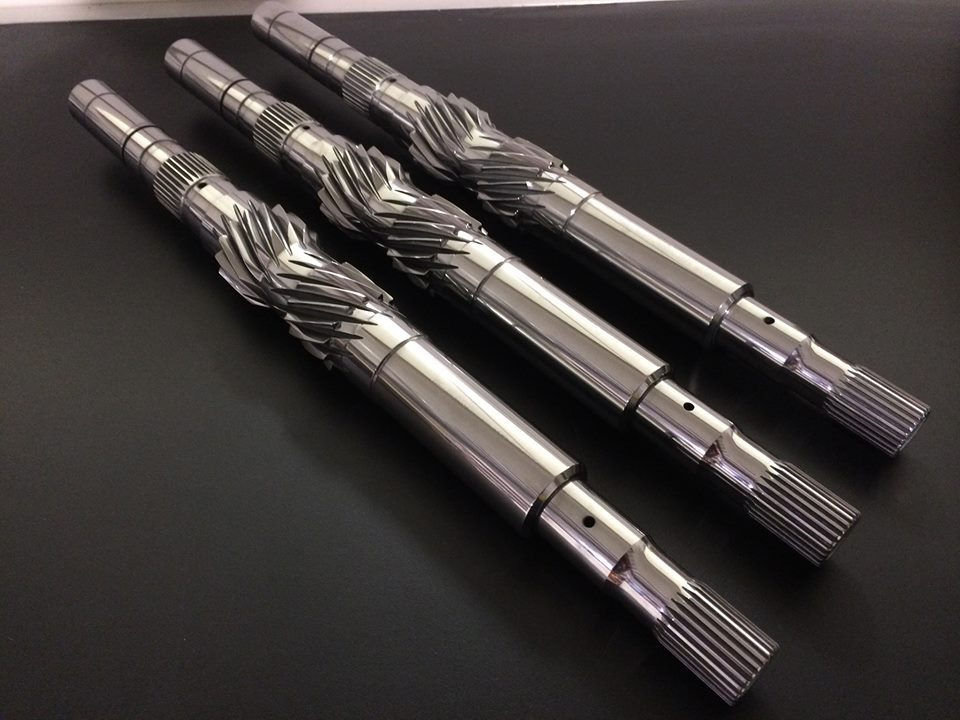
Isotropic Micro-Finishing, Part photo by Mark Riley, BV Products
Contact us for information on free sample part processing at dryfinish@gmail.com.
FREE SAMPLE PROCESSING * CONTRACT FINISHING SERVICES * TURN-KEY FINISHING SYSTEMS
For additional information or sample processing information contact: by Dave Davidson – Deburring/Finishing Specialist SME Manufacturing C248 – Spokane, Washington Advisor: Machining/Material Removal Technical Community dryfinish@gmail.com | 509.230.6821 http://dryfinish.wordpress.com
Below is some process video footage demonstrations of high-speed centrifugal isotropic finishing. These automated edge and surface finishing methods are capable of producing very refined low micro-inch surfaces that can improve functional part performance and service life.
Some additional Isotropic Micro-Finishing Part photography can be seen below (Photo Credit: Mark Ripley, BV Products)
This slideshow requires JavaScript.
Many parts from a wide variety of industries also processed to improve performance, minimize hand deburring and improve edge and surface finish quality. (See below:)
This slideshow requires JavaScript.
Comments