Isotropic Micro-Finishing of Surgical Implants and Medical Devices
- Dave Davidson
- Apr 30, 2017
- 2 min read
by Dave Davidson, Deburring/Finishing Specialist and SME Technical Community Advisor. http://about.me/dave.davidson | 509.230.6821 For technical information or to make arrangements for FREE sample part processing contact me: dryfinish@gmail.com see also: https://dryfinish.wordpress.com

Dental parts also must meet rigorous surface finish standards. In the past, it was not uncommon to see many of these parts finished with manual methods. Centrifugal Isotopic finishing can not only replace tedious hand methods but can also produce exceptional part-to-part uniformity and consistency
Implant parts and medical and dental devices often must meet exacting requirements for edge and surface finishing, it is not unusual to see requirements that parts meet surface finish standards approaching 1-2 microinches. High-energy finishing methods are used to produce these types of finishes [Note: this type of surface finishing is also becoming a requirement for some non-medical applications such as the preparation of parts for PVD coatings. Isotropic Micro-Finishing is capable of producing the very fine surface finish values required for these types of coatings, which conform much more closely to substrate surface finish values than does plating, which has a tendency to level or flatten out peaks or asperities of the surface finish.]

Centrifugal Barrel Finishing Machine. A high energy finishing method capable of producing very fine surface finish values on a wide variety of materials and part configurations

Dental tools and hardware are finished using centrifugal isotropic finishing to produce very refined polished surfaces
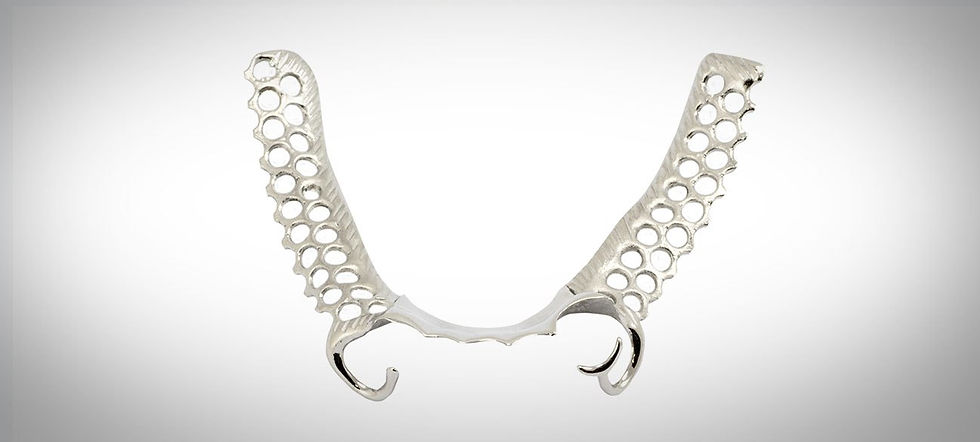
Hand deburring and polishing reduction…Parts such as this one can easily become a finishing nightmare for dental laboratories and manufacturers. Centrifugal Isotropic finishing can minimize the need for hand and manual operations

Centrifugal Isotropic finishing excels at producing fine finishes on small parts.

Titanium component finished with centrifugal isotropic finishing

Titanium part finishing and polishing in two steps. (1) Part to the left – finished and smoothed abrasively (2) Part to the right – polished in dry polishing media for final finishing. These multi-step processes are capable of producing very low micro-inch finishes

Before and after example of implant finishing with centrifugal isotropic micro-finishing methods. Multi-step Isofinishing is capable of producing exceptional surface finish quality

Even parts produced by investment castings such as these stainless steel parts can be polished with a minimum of hand or manual processing.


Centrifugal Isofinishing can be used to develop superior finishes on both plastic and metal medical components. A combination of wet and dry process finishing cycles are used to produce these effects.
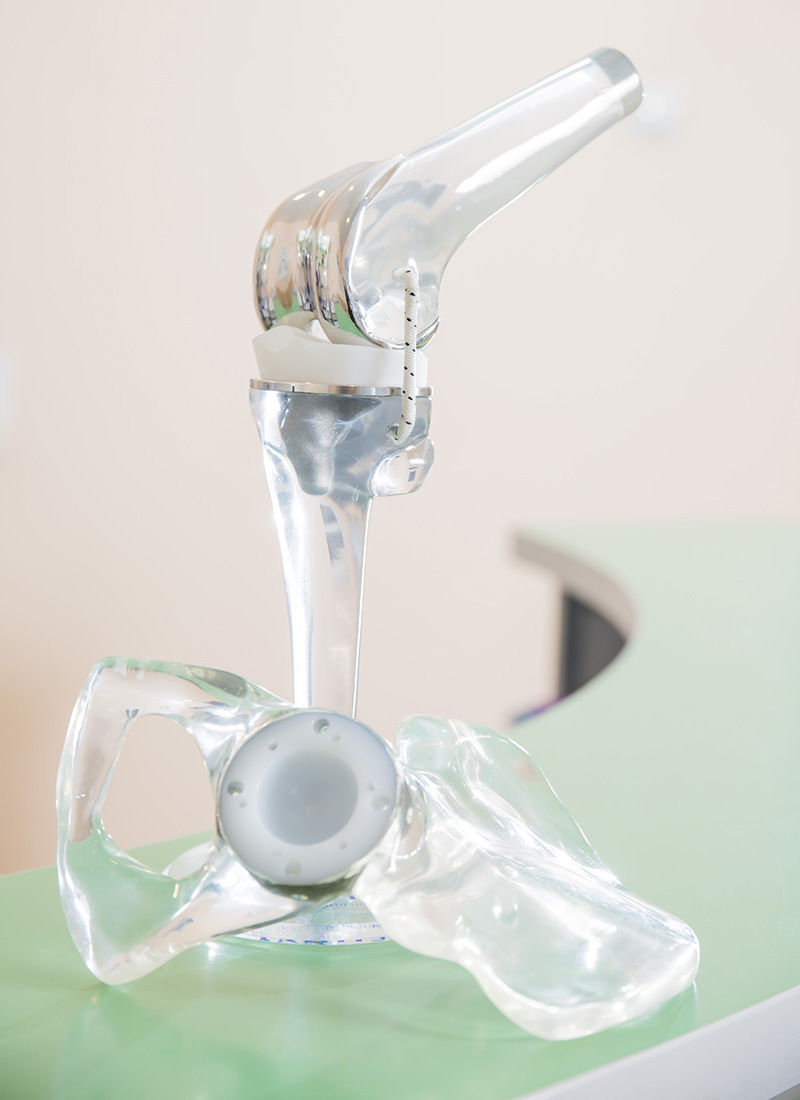
As components are immersed in abrasive or polishing media complex components can be processed so that features will finished evenly, Part-to-part and lot-to-lot consistency are a hallmark of centrifugal isotropic processing.
FREE SAMPLE PROCESSING * CONTRACT FINISHING SERVICES * TURN-KEY FINISHING SYSTEMS
For additional information or sample processing information contact: by Dave Davidson – Deburring/Finishing Specialist SME Manufacturing C248 – Spokane, Washington Advisor: Machining/Material Removal Technical Community dryfinish@gmail.com | 509.230.6821 http://dryfinish.wordpress.com
Below is some process video footage demonstrations of high-speed centrifugal isotropic finishing. These automated edge and surface finishing methods are capable of producing very refined low micro-inch surfaces that can improve functional part performance and service life.
Comentários