Knife Deburring and Polishing Made Easy with Centrifugal Iso-Finishing Technology
- Dave Davidson
- Jan 1, 2021
- 2 min read
Updated: Sep 12, 2021
Guest column by Cole Mathisen. MFI
Need more information? Want to have your parts sample finished? CONTACT: Dave Davidson | Deburring/Surface Finishing Technologist

If you’re looking for a solution for knife polishing and deburring, high-energy barrel tumblers provide a fast, environmentally friendly solution. In a matter of minutes, you can take blades from your machining or heat-treating process and put them into a centrifugal barrel tumbler and have blades and other knife components ready for assembly.
Centrifugal Iso-Finishing processes are free of hazardous and expensive accelerated chemicals. We rely simply on the intense physical force of the machine.
How to Polish Knives
Barrel tumbling works by using a one-to-one ratio of turret rotation to barrel rotation creating a Ferris Wheel type motion. This creates a compression and wave sliding effect inside the chamber of each barrel.
With the HZ-40 you can process 16 short (3-5 inch) blades at a time while keeping them separated in individual compartments to eliminate part-on-part damage. The HZ-60 provides 48 blade capacity while the HZ-40 gives you 60. Long blades, up to 33 inches long can fit in the tumbling chamber of the HZ-85.
Utilizing an abrasive preformed type of media, Centrifugal Iso-Finishing has produced acceptable stonewashed finishes in as little as 5 minutes of run time. With an added step with a non-abrasive type of media, we can polish the blades in 10-20 minutes.
BELOW: See the videos showing Model HZ-40 and HZ-60 centrifugal iso-finishing machines in action
Centrifugal Iso-Finishing machines are at work with custom and production knife makers around the world with solutions for creating unique matte and stonewashed finishes along with mirror polishes on blades.

Save Time and Money
In many cases, customers tumbling blades in vibratory machines are saving 8 hours or more by switching to high energy machines. That’s an entire workday! Utilizing outdated equipment or hand finishing knife blades is expensive, time-consuming and in some cases dangerous for operators.
Knife deburring and polishing is a hands-free operation in high-energy centrifugal barrel tumblers. Seeing is believing, so we offer sample processing at no cost to prove that we can give you the return on investment and quality you need to make your business successful. Call or email us today to talk to a sales rep about options.
High-energy finishing is quickly becoming the industry standard for some of the world’s finest knife makers. Centrifugal Barrel Tumblers and Centrifugal Iso-Finishing processes provide unmatched speed and performance even on hardened materials. In as little as five minutes of tumbling, machine lines are removed and blended evenly. Mirror finishes are also possible in one short secondary step.
Make Your Knives More Durable
At full speed, Centrifugal Iso-Finishing machines like the HZ-85 can apply upwards of 12 G’s of force on the media and parts rotating inside. This leads to greater stress relief than shot peening or any other method.
Let us show you what we can do for your knife deburring and polishing operation. Contact us today for free sample processing. Follow our LinkedIn page at https://www.linkedin.com/company/18237645/admin/

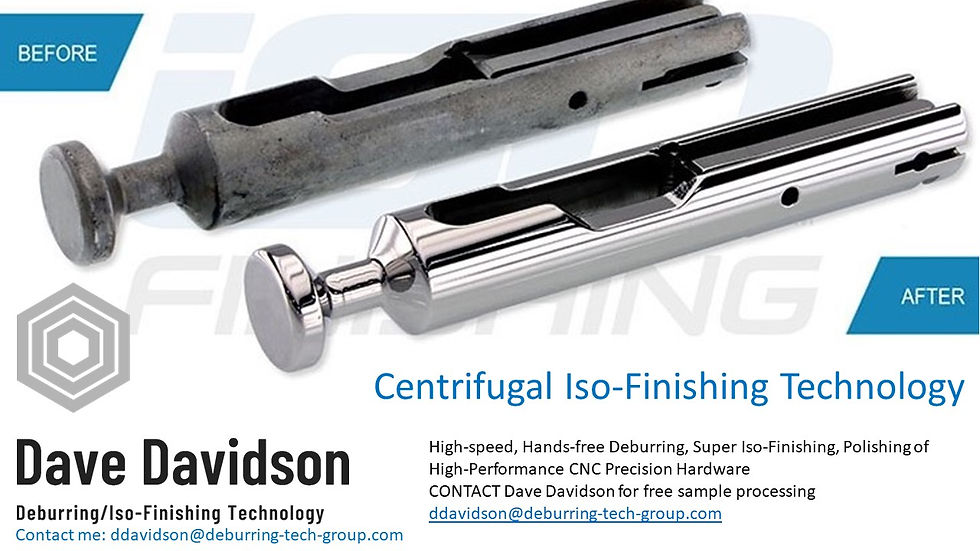
Contact me at ddavidson@deburring-tech-group.com for more information on sample finishing your parts

See below some of the many different types of parts being finished with Centrifugal Iso-Finishing processes...


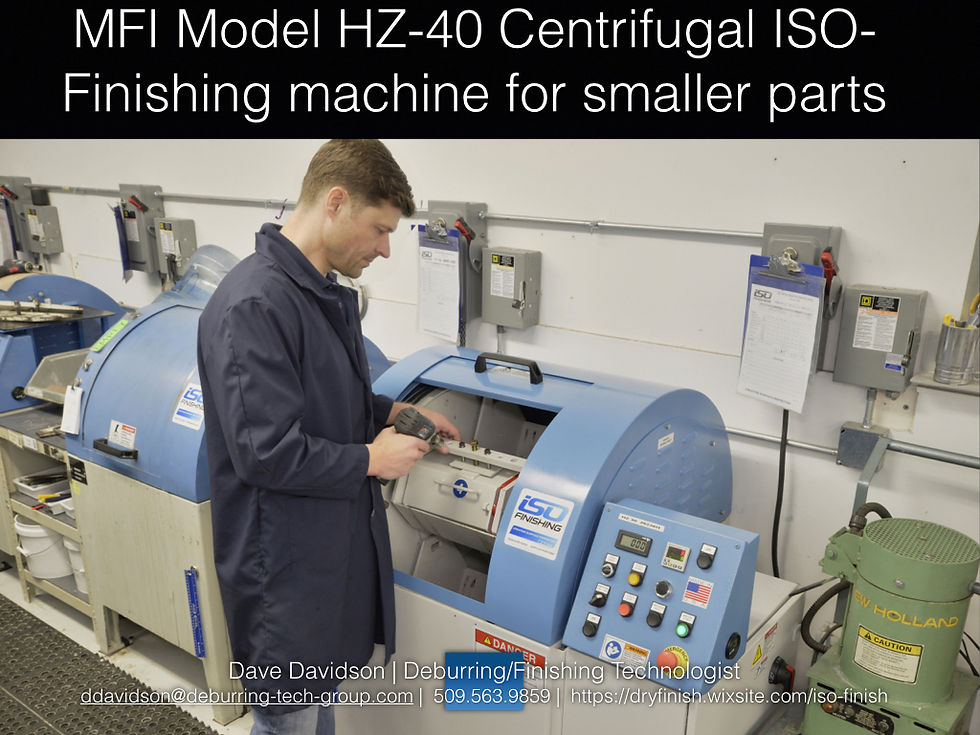

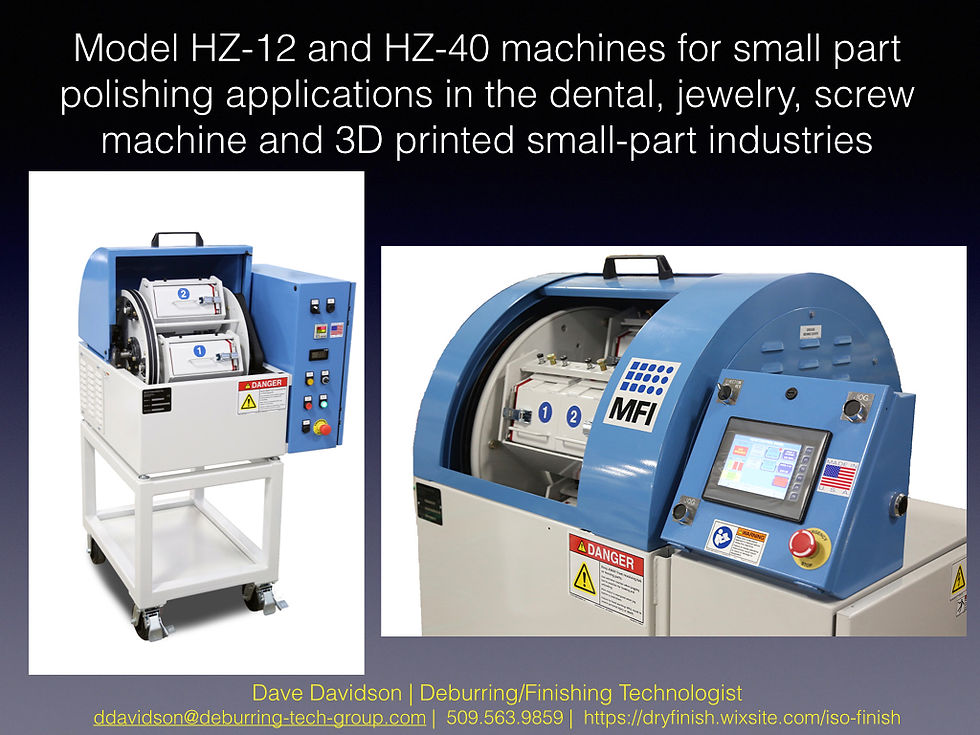
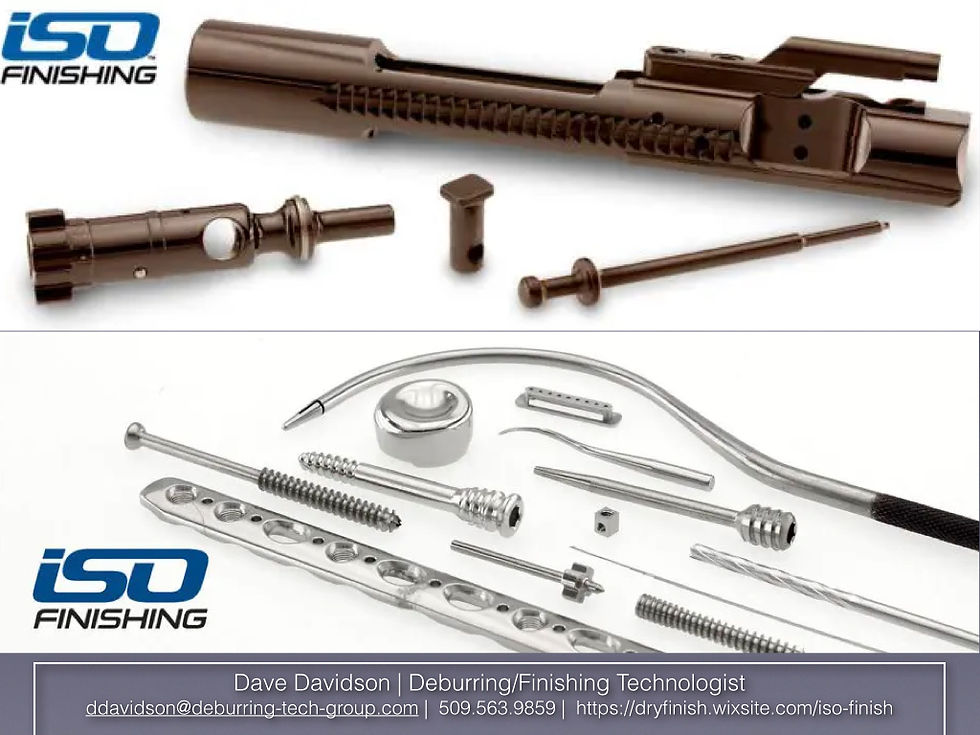
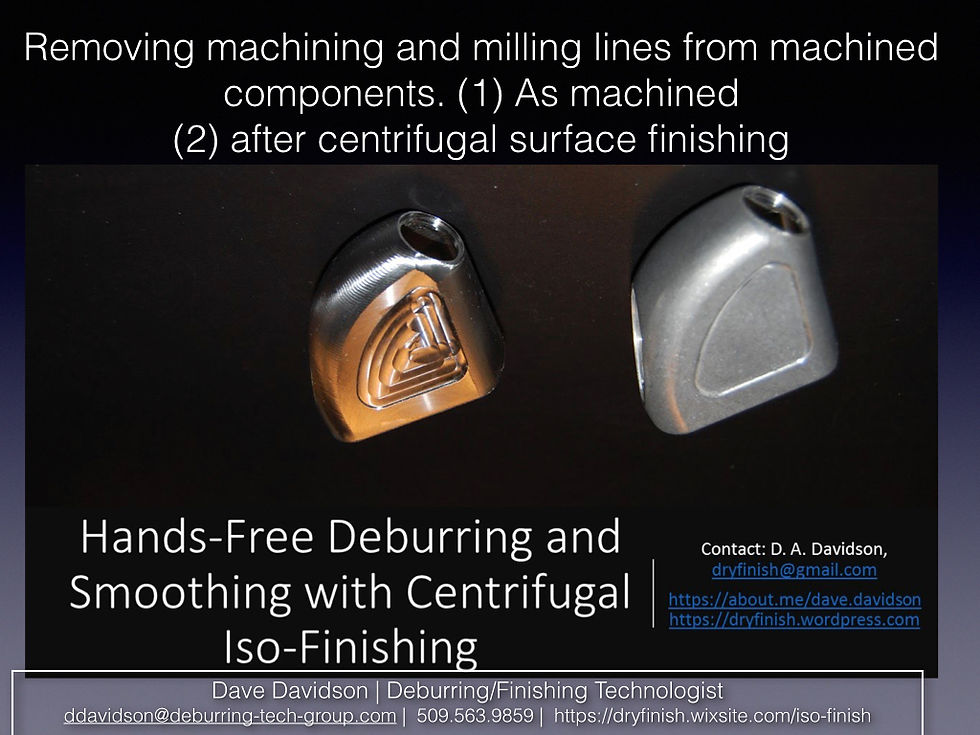
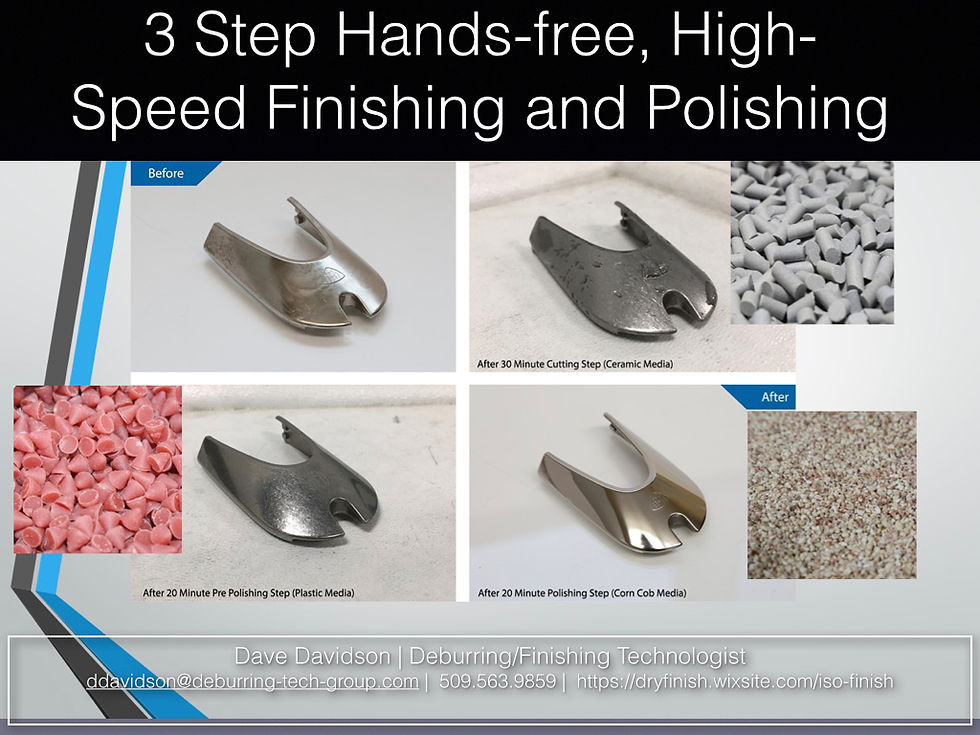



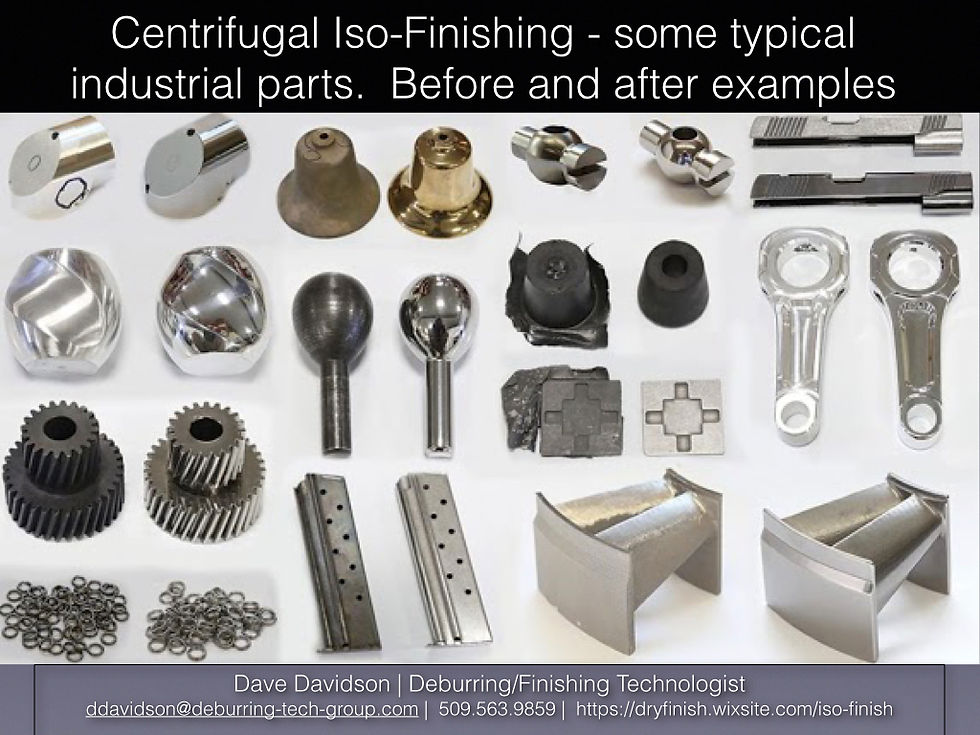
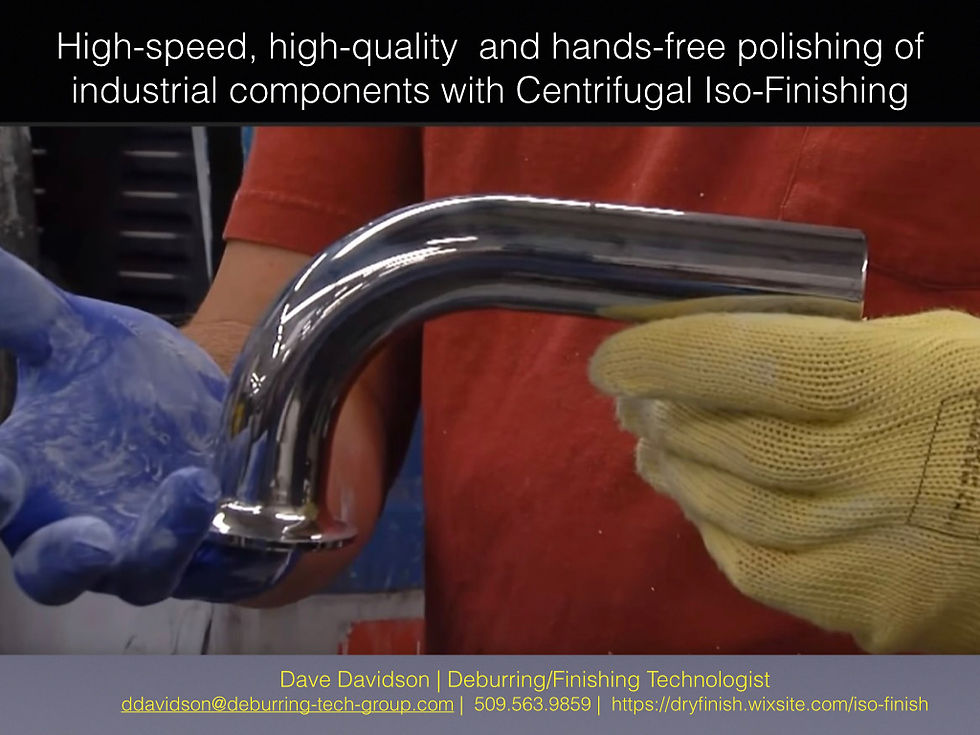
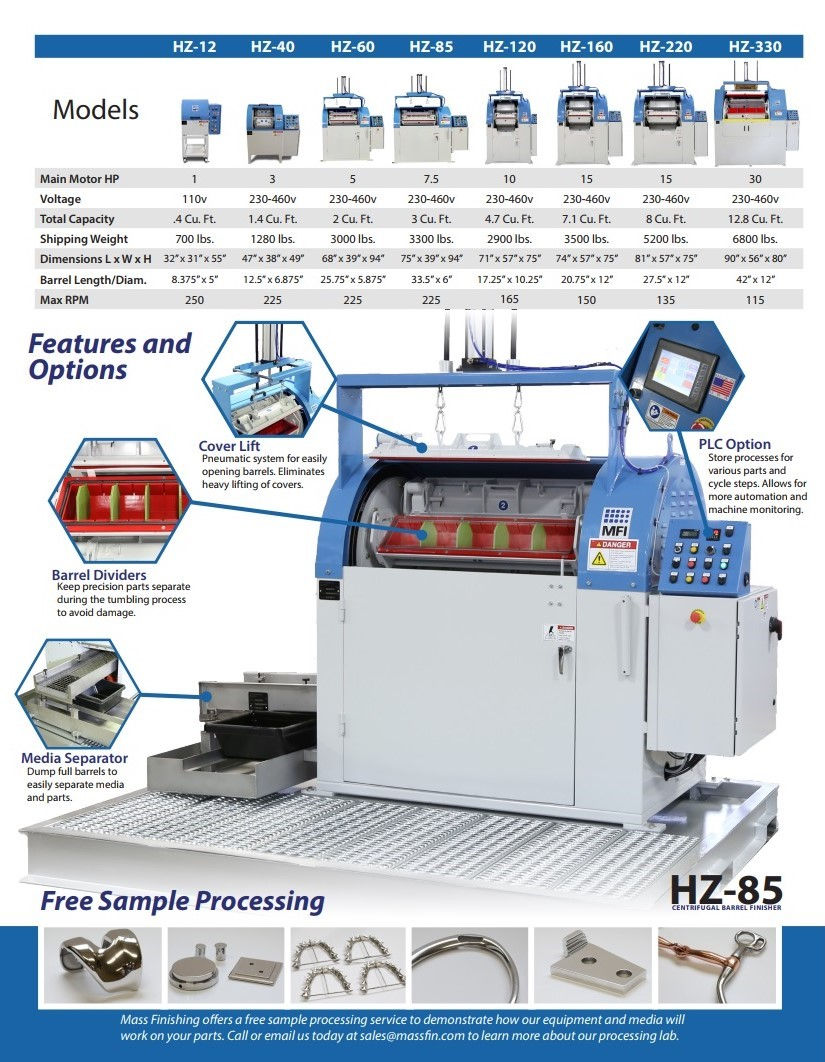
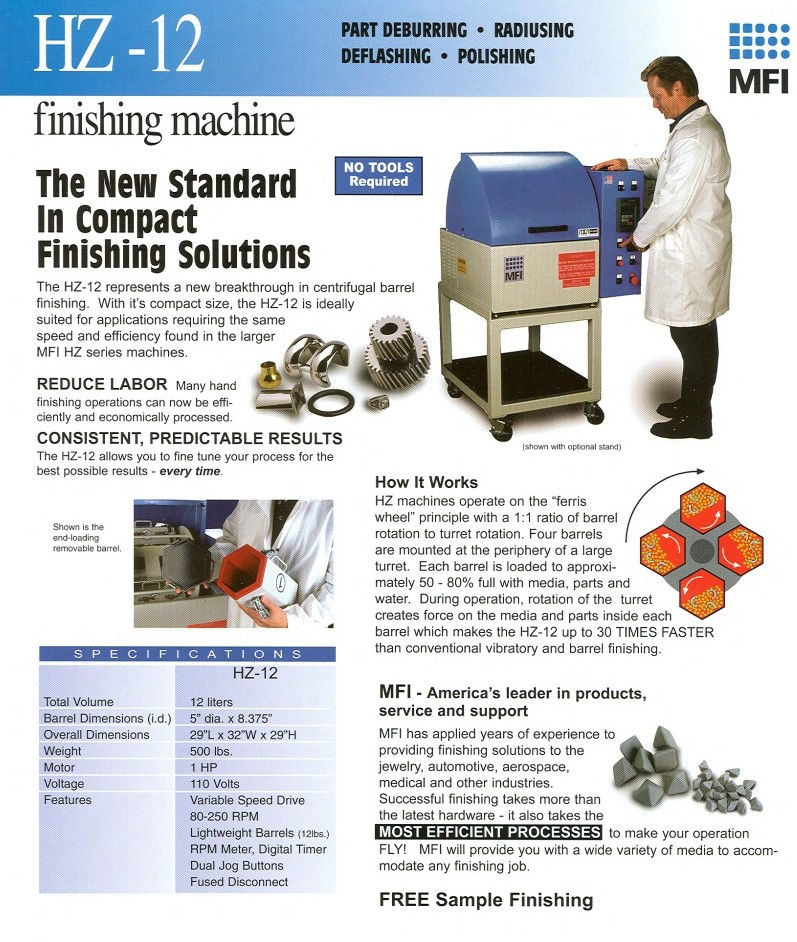
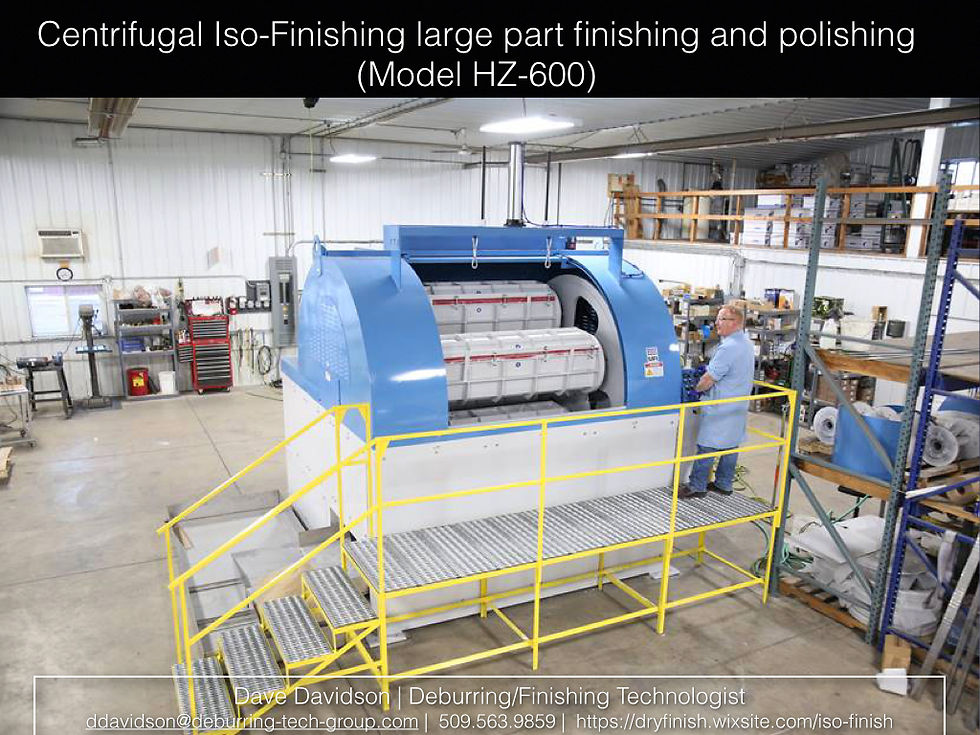
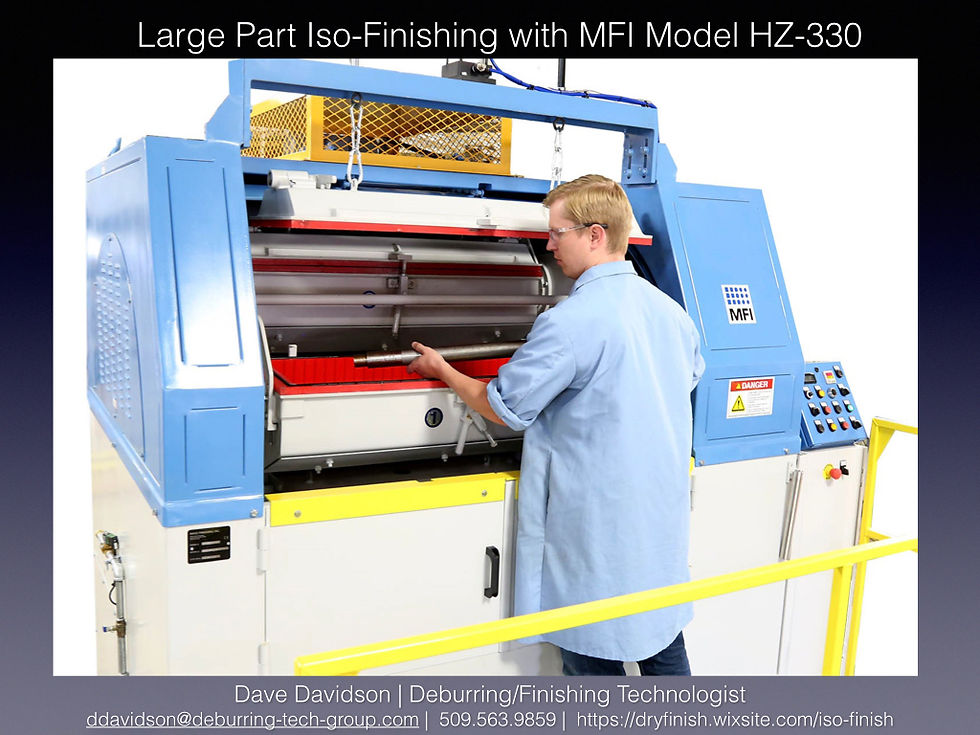
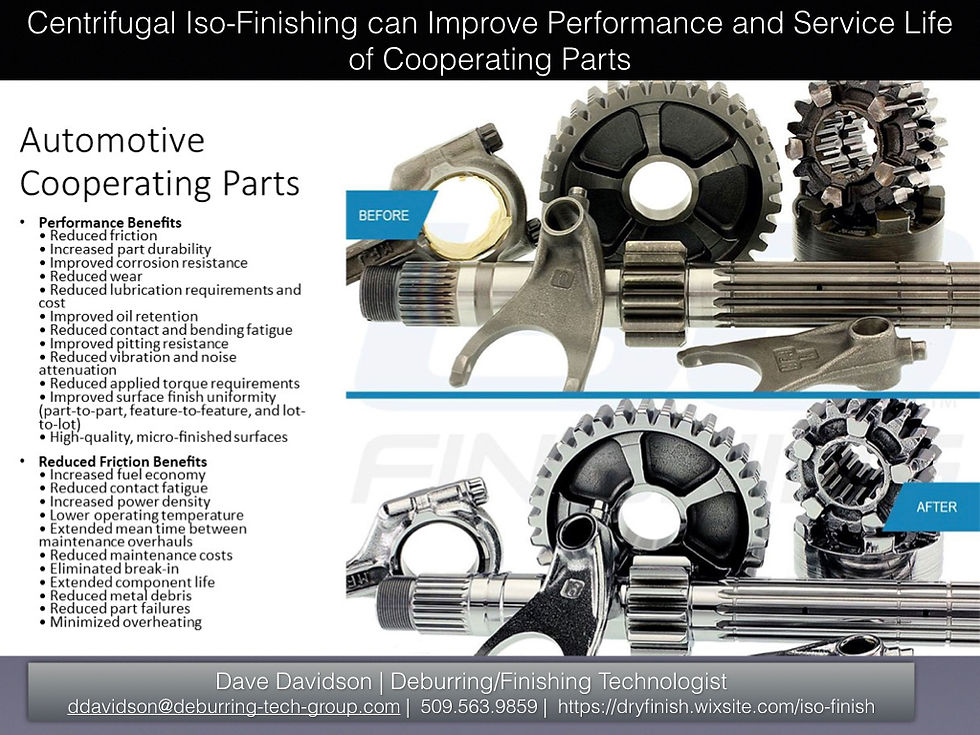


Comments