Evaluation of Post-Processing Surface Finish on 3D Printed Metal Parts.
- Dave Davidson
- May 7, 2019
- 2 min read
Updated: May 26, 2021
Contributing Editor: Dave Davidson, Deburring/Finishing Technologist | 509.563.9859 ddavidson@deburring-tech-group.com | https://dryfinish.wixsite.com/iso-finish Contact us for additional technical information and help with
free sample finishing of your parts

If you have parts that need edge or surface finishing improvement and would like to have FREE sample part processing and a quotation developed for finishing the parts please contact Dave Davidson at ddavidson@deburring-tech-group.com I can also be reached at 509.563.9859 Information about equipment for bringing Centrifugal Iso-Finishing capability to your facility is also available.
Centrifugal Isotropic Finishing has been shown to be very useful in reducing the rough surfaces common to 3D printed parts and developing highly finished surfaces. Below is an example of surface finish that can be achieved with the method. The part shown in the slide below has had surface roughness reduced from 356.24µin Ra. to 12.06µin Ra.


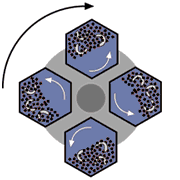
HOW IT WORKS. Centrifugal Iso-Finishing Technology operation is similar to the operation of a "Ferris Wheel" but this Ferris wheel operates at high rotational speed with the turret swinging the barrels around its periphery while the barrels counter-rotate at high speed. This motion imparts high centrifugal force to the parts and media in the processing chambers and finishing and polishing work is performed ten times faster than conventional low-energy finishing equipment. (For video examples of some of the equipment in operation refer to: https://dryfinish.wordpress.com/2017/02/23/centrifugal-isotropic-finishing-operations-on-precision-parts-video/ ). On many parts, single digit micro-inch Ra surface finishes can be achieved. See some examples of the equipment show below:

Media used in these types of processes tend to be a great deal smaller than the common sizes chosen for barrel and vibratory processes. The smaller media, in such a high-pressure environment, are capable of performing much more work than would be the case in lower energy equipment. They also enhance access to all areas of the part and contribute to the ability of the equipment to develop very fine finishes. In addition to the ability to produce meaningful surface finish effects rapidly, and to produce fine finishes, CBF has the ability to impart compressive stress into critical parts that require extended metal fatigue resistance. Small and more delicate parts can also be processed with confidence, as the unique sliding action of the process seems to hold parts in position relative to each other, and there is generally little difficulty experienced with part impingement. Dry process media can be used in certain types of equipment and is useful for light deburring, polishing, and producing very refined isotropic super-finishes. An example of the multi-step processing used to develop fine finishes from the initial rough surfaces can be seen in the video below. The media type and time cycles will vary with parts from various alloys. See below:
Above: Video showing a three step Centrifugal Iso-Finishing process for polisning both additive and CNC manufactured parts.
Hands-Free and High-Speed Finishing and Polishing. Many Additive Manufactured (3D printed) parts can be finished and polished with this rapid deburring, smoothing and finishing method. Time cycles can be as much as 1/10th that of conventional mass finishing methods. CONTACT: Dave Davidson at ddavidson@deburring-tech-group.com
Contributing Editor: Dave Davidson, Deburring/Finishing Technologist | 509.563.9859 ddavidson@deburring-tech-group.com | https://dryfinish.wixsite.com/iso-finish Contact us for additional technical information and help with
free sample finishing of your parts
See also below an excerpt from the "Centrifugal Iso-Finishing Technology" presentation side deck.



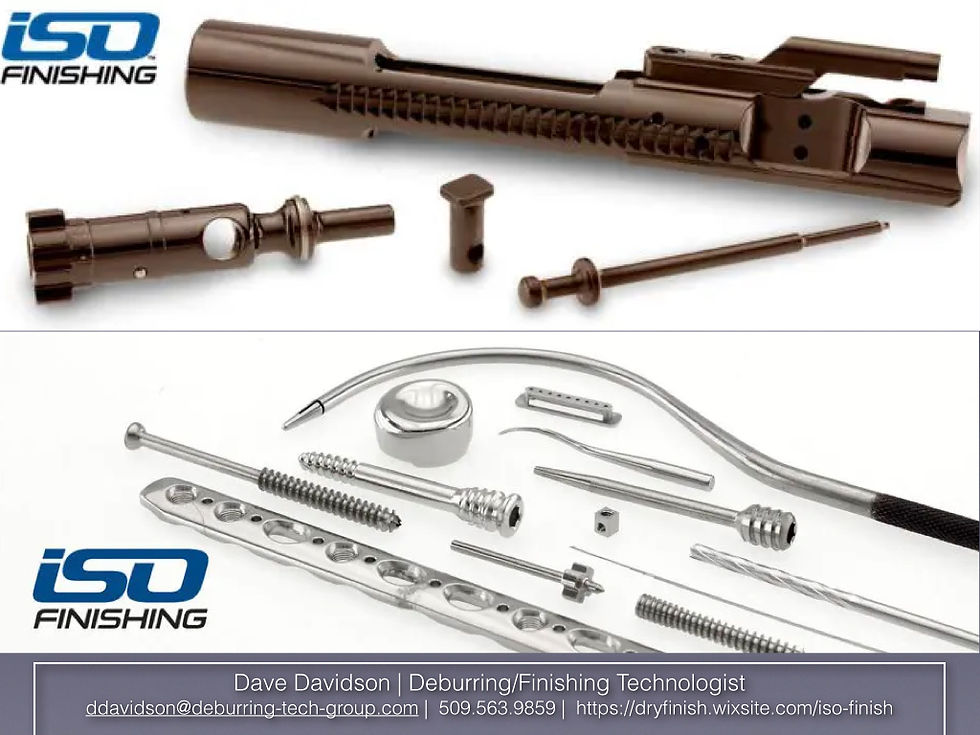
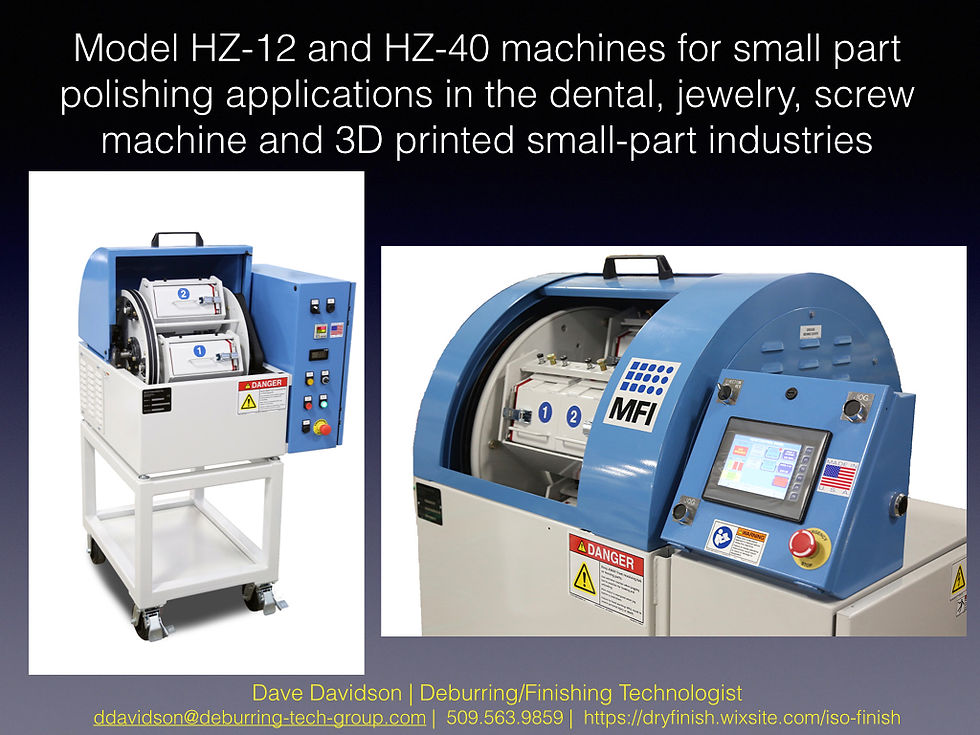
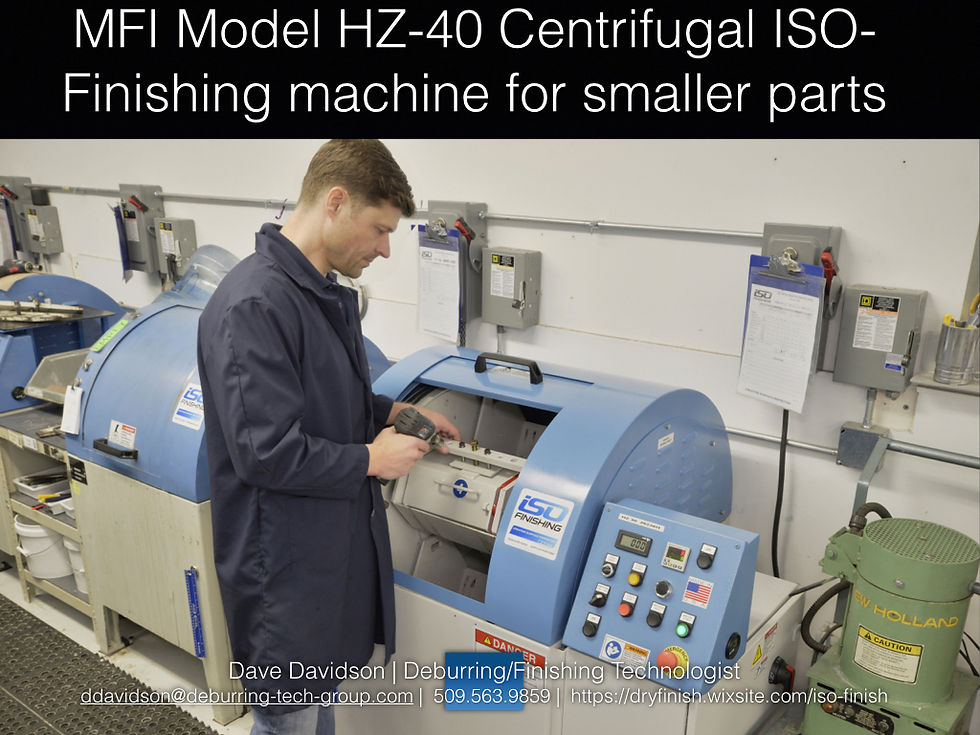
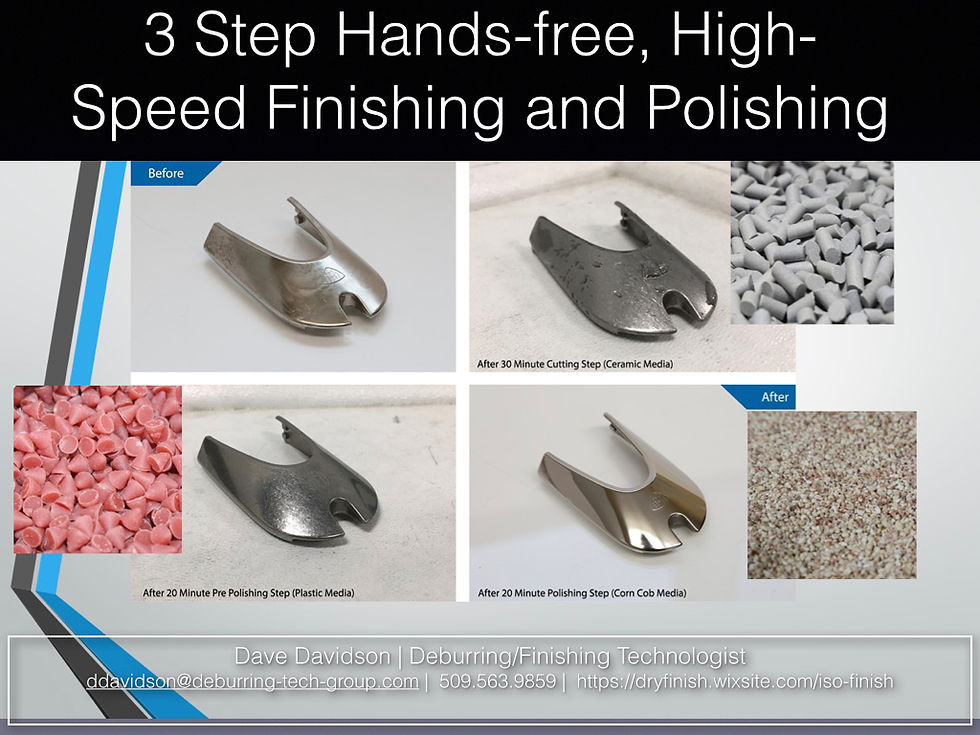

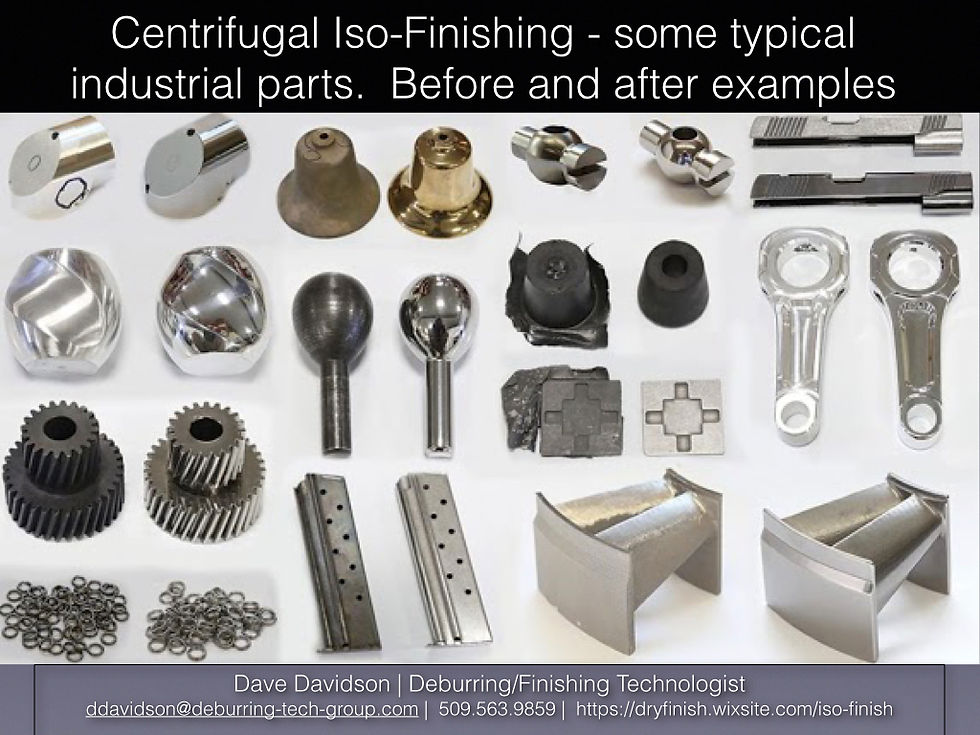
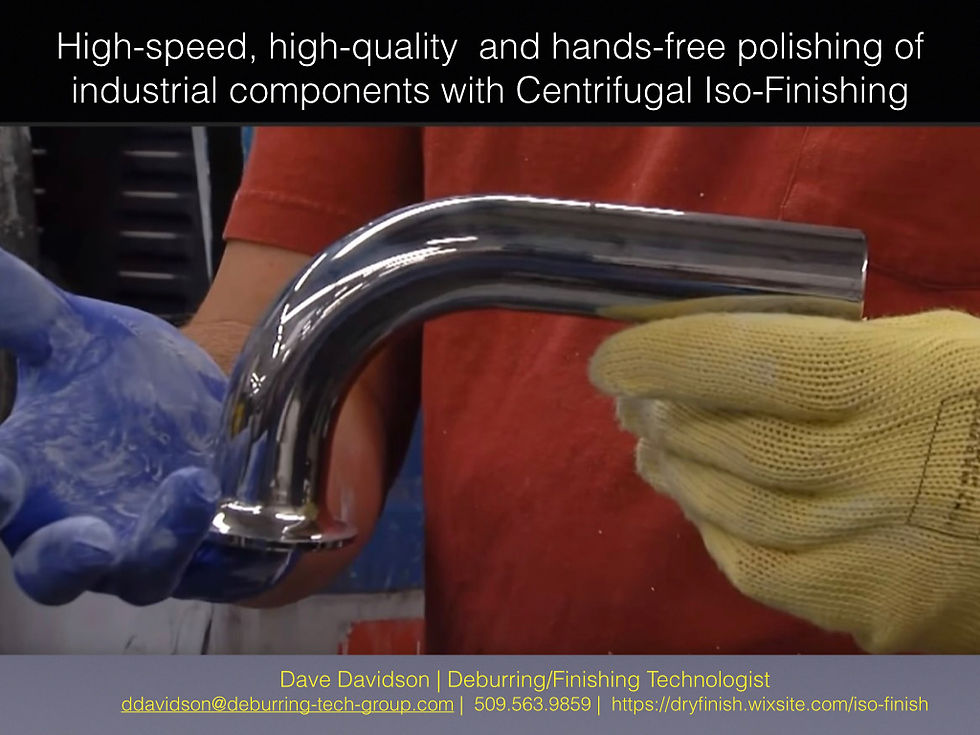
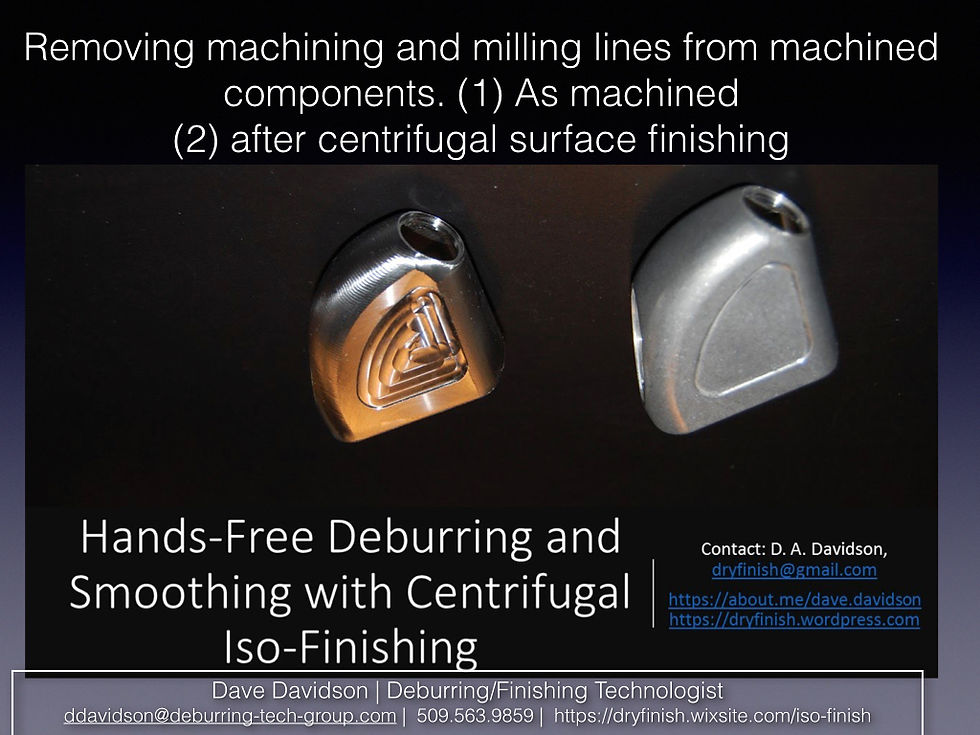

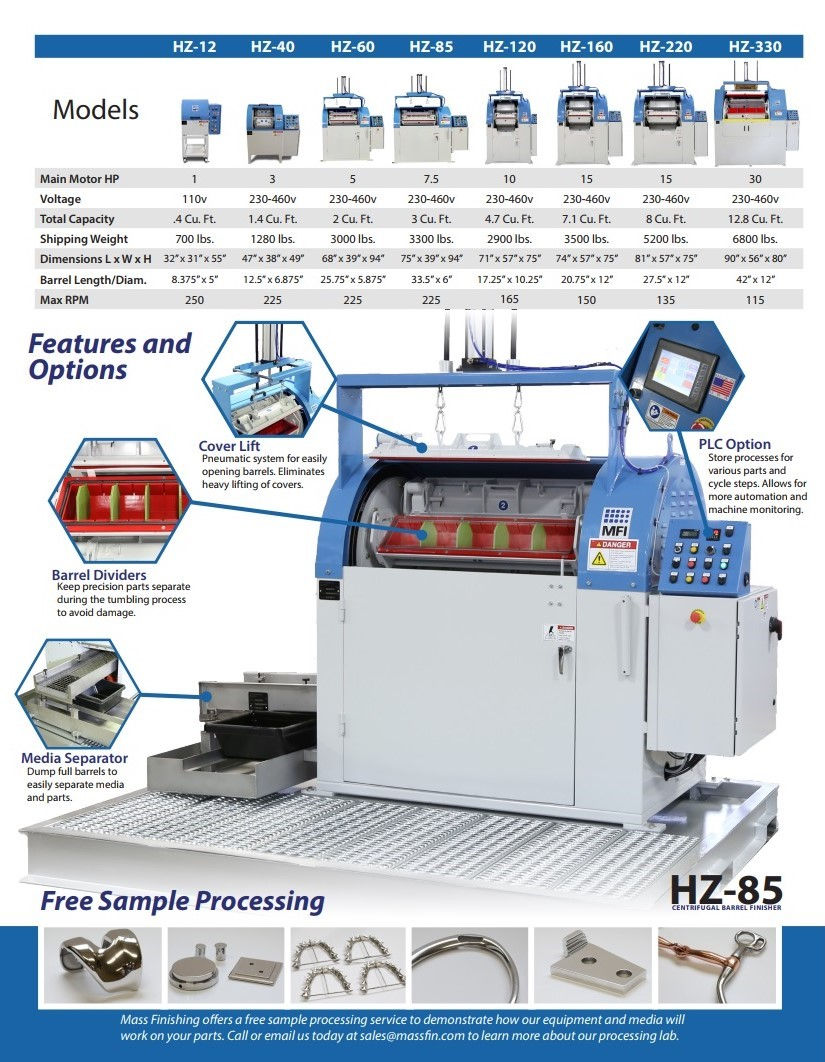
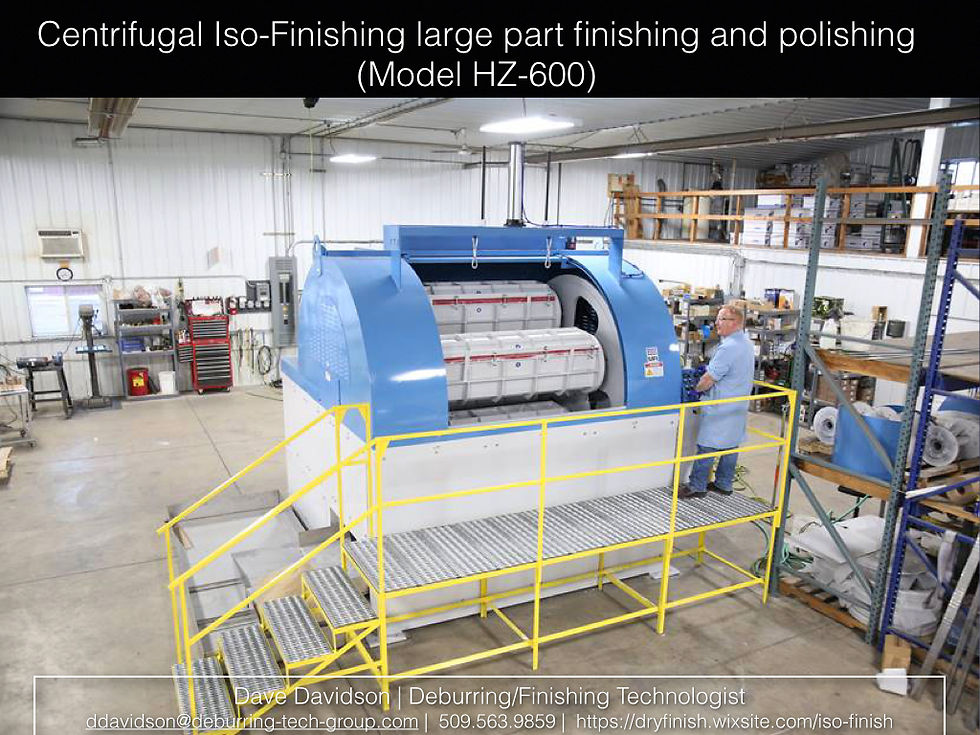
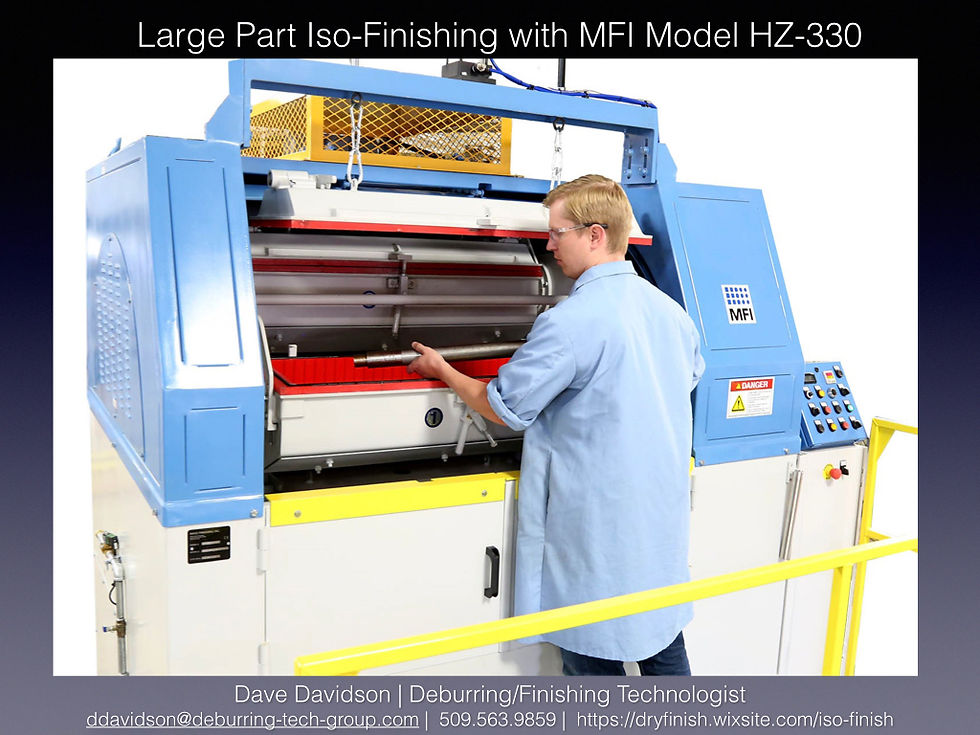
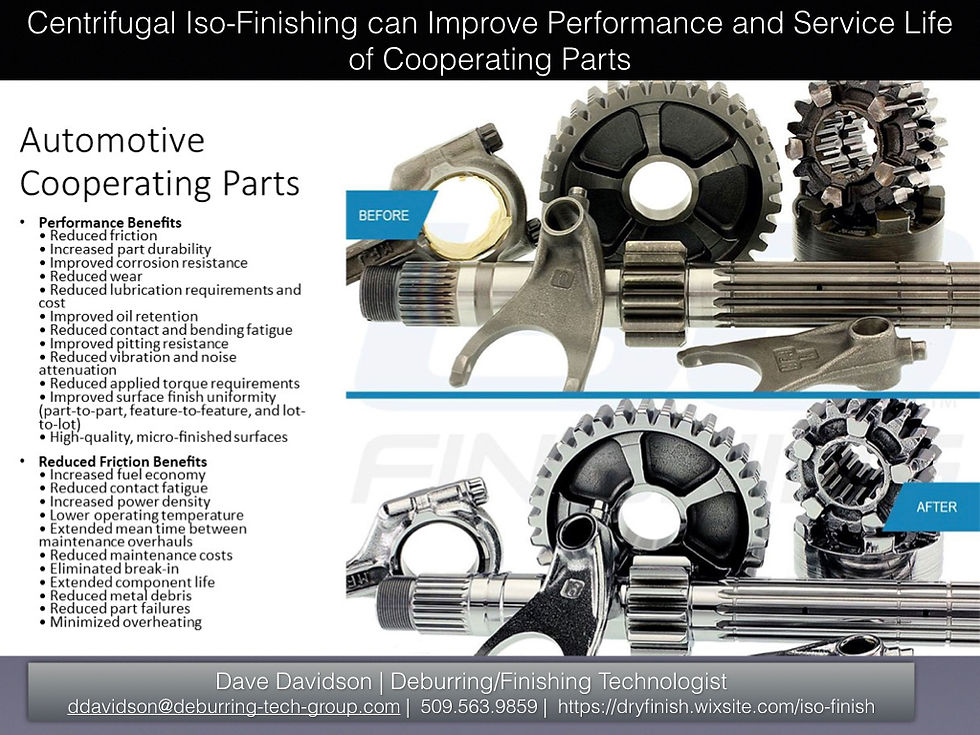


Comments