Mass Finishing Basics
- Dave Davidson
- Jul 21, 2011
- 4 min read
Feature Photo Above: Isotropic Micro-Finishing for High-Performance Automotive or Aerospace Components can improve performance and service life. (Photo Credit: Mark Riley, BV Products)
Free Sample Processing Available for your parts, contact dryfinish@gmail.com or 509.230.6821
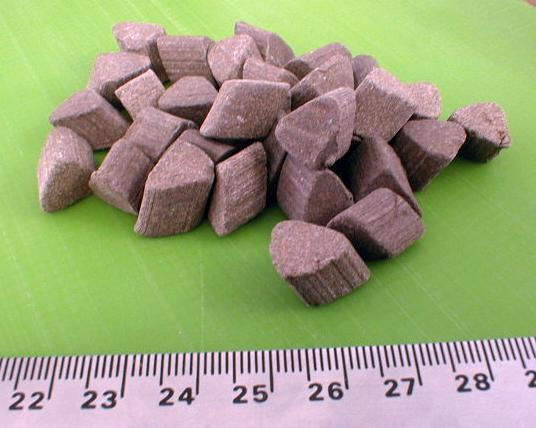
Ceramic 3/8 inch angle cut triangle shaped abrasive media. This type of media is used for initial heavy grinding and roughing operations in centrifugal barrel finishing and other equipment. It can produce deburring, edge-contour, machine mark blending and smoothing effects very rapidly. Often used to reduce or eliminate hand or manual deburring operations
WHAT IS MASS FINISHING? Mass finishing is a term used to describe a group of abrasive industrial processes by which large lots of parts or components made from metal or other materials can be economically processed in bulk to achieve one or several of a variety of surface effects. These include deburring, descaling, surface smoothing, edge-break, radius formation,removal of surface contaminants from heat-treat and other processes ,pre-plate and pre-paint or coating surface preparation, blending in surface irregularities from machining or fabricating operations, producing reflective surfaces with non-abrasive burnishing media, refining surfaces, and developing super-finish or micro-finish equivalent surface profiles.
All mass finishing processes utilize a loose or free abrasive material referred to as media within a container or chamber of some sort. Energy is parted to the abrasive media mass by a variety of means to impart motion to it and to cause it to rub or wear away at part surfaces. Although by definition the term mass finishing is used generally to describe processes in which parts move in a random manner through-out the abrasive media mass, equipment and processes that utilize loose abrasive media to process parts that are fixtured come under this heading also.
MASS FINISHING CAUTIONS. Despite the immense versatility of these types of processes, some potential process limitations should be noted. It can be difficult to selectively treat certain part areas to the exclusion of other areas, which might have critical dimensional tolerance requirements. Unless masked or fixtured, all exterior areas of the part will be affected by the process to a greater or lesser degree, with effects on corners and edges being more pronounced than those on flat areas, and with interior holes, channels, and recesses being relatively unaffected in the more common processes. Care must be exercised in media size, shape selection, and maintenance to prevent media lodging in holes and recesses, which might require labor-intensive manual removal. Some parts have shapes, sizes, or weights that may preclude them from being finished in some mass finishing processes because of the risk of impingement from part-on-part contact or of nesting due to certain features of the parts interlocking together when in proximity. Additionally, most processes that use water in conjunction with the abrasive media create an effluent stream, which must be treated prior to discharge into municipal sewage or other disposal.
MASS FINISHING—PART OF THE MANUFACTURING PROCESS
Much time and money can be saved both in mass finishing process operations and in process development if finishing considerations are given sufficient weight at the design, production, and quality control stages. Although it is a rule more breached than observed, it should be noted that mass finishing processes are not, and were never intended to be, methods for rectifying errors made in earlier stages of the manufacturing process. It should be equally obvious that processes developed for parts made with tools and dies that are sharp will no longer produce the same results when that tooling becomes dull. Mass finishing processes can produce remarkably uniform results if process parameters are followed carefully, but this assumes some measure of uniformity of surface condition for a given part within a lot, and from lot-to-lot, as received in the finishing area.
MASS FINISHING EQUIPMENT. One of the more obvious factors influencing mass finishing processes is equipment selection. There are five major equipment groups as follows: barrel, vibratory, centrifugal barrel, centrifugal disk, and spin/spindle-finishing.
There are variations within each major grouping, and each equipment group has its own set of advantages. See illustrations below:
This slideshow requires JavaScript.
The first four groups are primarily used with parts immersed within a body of abrasive media and are capable of some independent movement within that mass. On occasion, fixturing or some sub-compartmentalization may be used to isolate delicate or critical parts from each other. Part-on-part contact may also be minimized by using higher media-to-part ratio combinations. Common media-to-part ratios for noncritical parts run anywhere from 1:1 to 1:4 by volume. Parts with a higher need for cushioning and protection may utilize media/part ratios as high as 10:1 to15:1. In contrast, all spin/spindle finishing processes utilize fixturing of parts, and in most cases movement of the fixture develops much of the action needed to abrade the parts.
This slideshow requires JavaScript.
This slideshow requires JavaScript.
Further reading: Internet resources
(1) “Isotropic Mass Finishing for Surface Integrity and Part Performance”, Article From: Products Finishing, Jack Clark, from Surface Analytics, LLC and David Davidson, from SME Deburr/Finish Technical Group, Posted on: 1/1/2015, [Barrel, vibratory, centrifugal and spindle finish can improve part performance and service life.] http://www.pfonline.com/articles/isotropic-mass-finishing-for-surface-integrity-and-part-performance
(2) “Turbo-Charged Abrasive Machining Offers Uniformity, Consistency” Article From: Products Finishing, by: Dr. Michael Massarsky, President from Turbo-Finish Corporation, and David A. Davidson, from SME Deburr/Finish Technical Group. Posted on: 6/1/2012. [Method can deburr, produce edge contour effects rapidly] http://www.pfonline.com/articles/turbo-charged-abrasive-machining-offers-uniformity-consistency
(3) “Turbo-Abrasive Machining and Finishing”. MANUFACTURING ENGINEERING – Aerospace Supplement, by: Dr. Michael Massarsky, President from Turbo-Finish Corporation, and David A. Davidson, from SME Deburr/Finish Technical Group. [Method first developed for the aerospace industry can improve surface integrity and part performance] http://www.slideshare.net/dryfinish/turboabrasive-machining-me-aerospace-supplement-reprint
(4) “The Role of Surface Finish in Improving Part Performnce”, MANUFACTURING ENGINEERING, by Jack Clark, Surface Analytics.com and David A. Davidson, from SME Deburr/Finish Technical Group. http://www.slideshare.net/dryfinish/november-2012-f4-deburring-1-final
(5) “Free Abrasives Flow for Automated Finishing”, MANUFACTURING ENGINEERING, , by: Dr. Michael Massarsky, President from Turbo-Finish Corporation, and David A. Davidson, from SME Deburr/Finish Technical Group. [Exciting new methods of surface finishing that go beyond deburring to specific isotropic surface finishes that can increase service life] http://www.slideshare.net/dryfinish/october-2013-f2-deburring-1
(6) Turbo-Abrasive Machining Demonstration Video: https://www.youtube.com/watch?v=jYxqCxMIHNo
(7) SME Spokane, WA Factory Floor video, Centrifugal Finishing in the Precision Machine Shop: Demonstration) https://www.youtube.com/watch?v=dUdKjaysTYM
AUTHOR BIOGRAPHY – David A. Davidson, [dryfinish@gmail.com]
Mr. Davidson is a deburring/surface finishing specialist and consultant. He has contributed technical articles to Metal Finishing and other technical and trade publications and is the author of the Mass Finishing section in the current Metal Finishing Guidebook and Directory. He has also written and lectured extensively for the Society of Manufacturing Engineers, Society of Plastics Engineers, American Electroplaters and Surface Finishers Association and the Mass Finishing Job Shops Association. Mr. Davidson’s specialty is finishing process and finishing product development.
INDEX TERMS: Tumbling, Mass Finishing, Barrel Finishing, Isotropic Finishing, Centrifugal Barrel Finishing, Vibratory Finishing, Deburring Automation
Comments