Mass Finishing Processes. What can they do? Where can they be used and on what kind of materials?
- Dave Davidson
- Jul 20, 2018
- 4 min read
Updated: Jul 18, 2020

Contributing Editor: Dave Davidson, Deburring/Finishing Technologist 509.563.9859 ddavidson@deburring-tech-group.com | dryfinish.wixsite.com/iso-finish
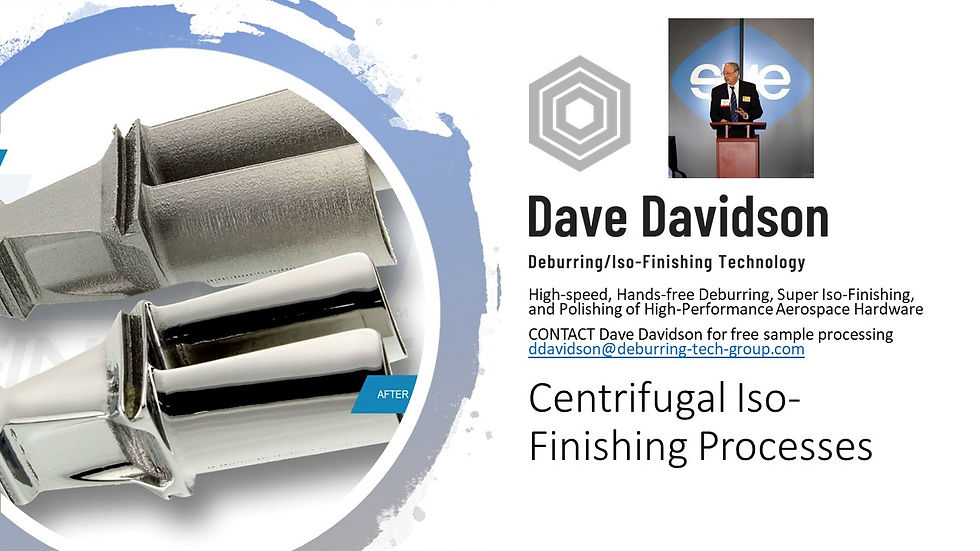
Mass finishing can economically enhance the utility, attractiveness, and value of the metal, plastic, ceramic or other parts manufactured for industrial or consumer use. Mass finishing processes improve surface properties, upgrade product quality, and enhance the image of the manufacturing industry. Edge, corner, surface finishing, including the removal of burrs, defects, and sharp edges improves part appearance and handling safety, and prepares surfaces for subsequent coating. Other benefits include easier assembly, improved operating performance, increased strength (in part by the elimination of surface stress concentrations), and longer product life. By imparting compressive stresses to the surfaces, fatigue strength can be improved. Some typically manufactured parts being mass-finished can be seen the pictures shown below:
Mass finishing processes can develop active metal surfaces–usually with random scratch patterns. On such metal surfaces, it is possible to react chemicals, electroplate, adhere paint, anodize, phosphatize, chromate or color efficiently. The design of a metal product affects finish quality and can influence deburring and finish costs. Many of the design factors applicable to parts to be mechanically polished and electroplated need not be considered for the mass finishing operation alone. These systems are flexible so that parts of almost any shape can be processed, weight and size permitting.
However, review of the part design by those knowledgeable in deburring and finishing can facilitate the relocation of webs, hole size changes, etc., where such changes have no effect on part function. Finishing cost reductions can be substantial. Designers can well keep in mind the fact that part surfaces and edges will be deburred, deflashed, radiused and/or refined by media of some type. Therefore, if possible, part dimensions and contours involving holes, fillets, edges and significant surfaces should be such that media can reach the surfaces to accomplish the desired result efficiently. Parts to be electroplated after mass finishing are, of course, subject to the design considerations, including the designation of significant surfaces.
Mass finishing is the processing of parts or components to be finished in a container, usually, with abrasive or non-abrasive media, water and compound. Some secondary polishing processes can create near-buff polished surfaces once the surfaces have been prepared with abrasive smoothing steps.. Action or movement of the container is created to cause media to press and/or rub against component surfaces, edges, and corners, or components to rub against each other, to remove burrs, radius edges and corners, improve surfaces, alter and/or enhance surface characteristics. Systems involve rotary barrels, vibratory tubs and round bowl machines, centrifugal machines with turret-mounted drums, centrifugal disc machines, and spindle finishing machines.
General operating equipment types are:





Less common mass finishing processes include reciprocal finishing, resonant energy finishing, chemically accelerated mass finishing and rotary barrel finishing with vibration.
One method I especially favor is hands-free and high-speed centrifugal iso-finishing. This method not only minimizes hand-deburring but can produce very highly polished reflective surfaces that can add significant amounts of functionality to many parts. This includes not only improved fit and form but substantial also wear and fatigue failure resistance
Centrifugal Iso-finishing.
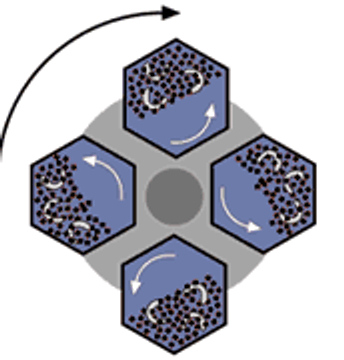
Similar in some respects to barrel finishing, in that a drum-type container is partially filled with media and set in motion to create a sliding action of the contents, CBF is different from other finishing methods in some significant ways. Among these are the high pressures developed in terms of media contact with parts, the unique sliding action induced by rotational and centrifugal forces, and accelerated abrading or finishing action. As is true with other high energy processes, because time cycles are much abbreviated, surface finishes can be developed in minutes, which might tie up conventional equipment for many hours.
The principle behind CBF is relatively straightforward. Opposing barrels or drums are positioned circumferentially on a turret. (Most systems have either two or four barrels mounted on the turret; some manufacturers favor a vertical and others a horizontal orientation for the turret.) As the turret rotates at high speed, the barrels are counter-rotated, creating very high G-forces or pressures, as well as considerable media sliding action within the drums. Pressures as high as 50 Gs have been claimed for some equipment. The more standard equipment types range in size from 1 ft3 (30 L) to 10 ft3, although much larger equipment has been built for some applications.
Media used in these types of processes tend to be a great deal smaller than the common sizes chosen for the barrel and vibratory processes. The smaller media, in such a high-pressure environment, are capable of performing much more work than would be the case in lower energy equipment. They also enhance access to all areas of the part and contribute to the ability of the equipment to develop very fine finishes. In addition to the ability to produce meaningful surface finish effects rapidly, and to produce fine finishes, CBF has the ability to impart compressive stress into critical parts that require extended metal fatigue resistance. Small and more delicate parts can also be processed with confidence, as the unique sliding action of the process seems to hold parts in position relative to each other, and there is generally little difficulty experienced with part impingement. Dry process media can be used in certain types of equipment and is useful for light deburring, polishing, and producing very refined super-finishes.
CBF equipment’s strong suit is the ability to develop surface finishes that may require over-lengthy time cycles in conventional equipment and the ability to develop a wide range of special surface finishes required for demanding and critical applications in the medical, aerospace, high-performance motorsports and precision machined component and additive industries.
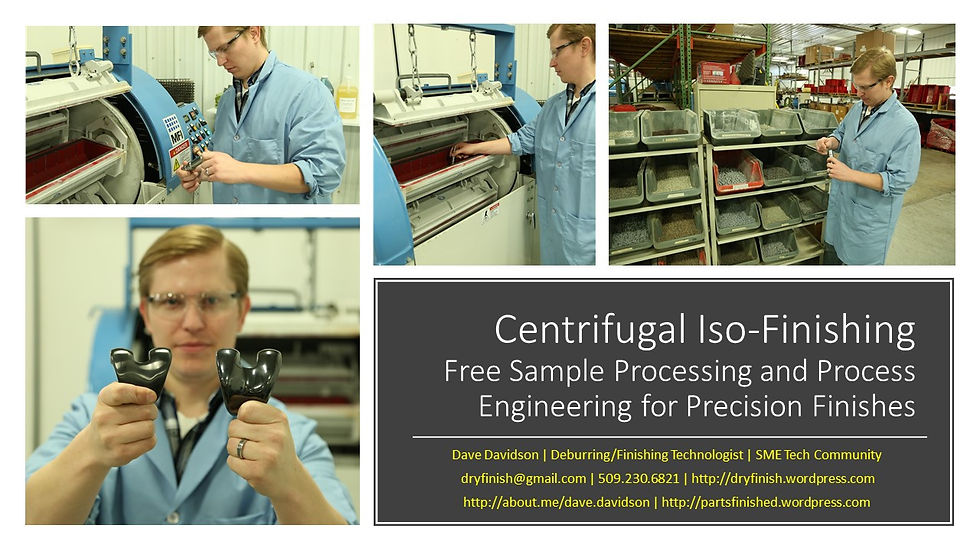


Need more information? Want to sample deburr or finish some parts? Contact Dave Davidson at ddavidson@deburring-tech-group.com

INDEX TERMS: #Burnishing #barrelfinishing #Polishing #smoothing #surfacefinishing #IsotropicFinishing #Finishing #aerospacefinishing #3DPrinting #aerospace #MetalFinishing #microfinishing #dryprocessfinishing #WetProcessFinishing #dryprocessmedia #Deburring #partfinishing #tumbling #CentrifugalBarrelFinishing #turbine #smallpartfinishing #abrasive #Precisionmachinedparts #Jewelry
Comments