Mass Media Finishing Large Aircraft and Aircraft Engine Components (Part 2)
- Dave Davidson
- Dec 1, 2011
- 4 min read

Figure 4 – This shafted gear utilized in helicopter turbine applications has been processed in centrifugal barrel finishing equipment to produce very specific isotropic finishes with very high load bearing ratios to improve gear tooth life and overall performance efficiency.
Dr. Michael Massarsky of the Turbo-Finish Corporation was able to supply comparative measurements on parts processed by his method for edge and surface finish improvement. Utilizing this spindle oriented deburr and finish method it is possible to produce compressive stresses in the MPa = 300 – 600 range that formed to a surface layer of metal to a depth of 20 – 40 μm. Spin pit tests on turbine disk components processed with the method showed an improved cycle life of 13090 ± 450 cycles when compared to the test results for conventionally hand deburred disks of 5685 ± 335 cycles, a potential service life increase of 2 – 2.25 times, while reducing the dispersion range of cycles at which actual failure occurred. Vibratory tests on steel test coupons were also performed to determine improvements in metal fatigue resistance. The plate specimens were tested with vibratory amplitude of 0.52 mm, and load stress of 90 MPa. The destruction of specimens that had surface finishes developed by the Turbo-Finish method took place after:
(3 – 3.75)*104 cycles
a significant improvement over tests performed on conventionally ground plates that started to fail after:
(1.1 – 1.5)*104 cycles.

Figure 5 — Centrifugal barrel machines such as these can produce exceptional edge and surface finishes in very short cycle times. Accelerated process effects can be developed because of the high speed interaction between abrasive media and part surfaces, and because media interaction with parts are characterized by high pressure by virtue of the high centrifugal forces developed in the processes. Smaller turbine blades can be processed in the 5 x 8 inch compartments in the 12-liter capacity machine shown to the right. Larger centrifugal machines such as the 220 liter or 330 liter capacity machine shown to the left can handle much larger parts as the barrel compartments are as much as 42 inches in length. Larger parts processed in this type of machinery can be processed one at a time within the barrel compartment suspended within the media mass or be fixtured. Barrel compartments can be divided into processing segments to accommodate more than one part.
In his Deburring and Edge-Finishing Handbook, Gillespie makes a very astute observation: “Typical burrs are not the result of poor planning or poor engineering. They are a natural result of machining and blanking processes. Large burrs, however, may be the result of poor planning.” A similar axiom could be said to exist regarding surface finishes. “Rough, non-isotropic surface finishes with undesirable stress conditions are not the result of poor planning or poor engineering. They are a natural result of almost all common machining and fabrication methods. These results can be exacerbated by abusive machining and grinding, and improved or reversed with mass media finishing techniques.”
Mass media finishing techniques improve part performance and service life, and these processes can be tailored or modified to amplify this effect. Although the ability of these processes to drive down deburring and surface finishing costs when compared to manual procedures is well known and documented, their ability to dramatically effect part performance and service life are not. This facet of edge and surface finishing deserves closer scrutiny and this is also true of larger and more complex parts – only more so.
REFERENCES:
(1) Gane, David H., Rumyantsev, H.T., Diep, Bakow, L. “Evaluation of Vibrostrengthening for Fatigue Enhancement of Titanium Structural Components on Commercial Aircraft”. Ti-2003 Science and Technology; Proceedings of the 10th World Conference on Titanium, Hamburg Germany, 13-18 July 2003, Edited by G. Lutejering and J Albrecht.WILEY-VCH Vol 2. pp 1053-1058
(2) Massarsky, M. L., Davidson, D. A., “Turbo-Abrasive Machining, CODEF PROCEEDINGS, 7th International Deburring Conference, Berkeley, CA.: CODEF [Consortium on Deburring and Edge Finishing], University of California at Berkeley, June 2004
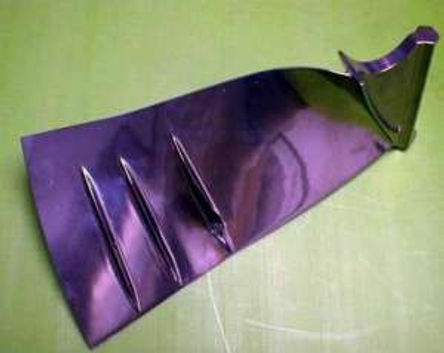
Figure 6 – This large power generation turbine blade was made utilizing 6-axis machining technology. Centrifugal barrel finishing technology was used to clear and blend in the milling cutter paths and then develop very refined and burnished isotropic surfaces in the foil area.
(3) Massarsky, M. L., Davidson, D. A.., “Turbo-Abrasive Machining – A New Technology for Metal and Non-Metal Part Finishing”, THE FINISHING LINE, Vol. 18 No. 4, Dearborn MI: Association of Finishing Processes, Society of Manufacturing Engineers, Oct. 30, 2002
(4) Massarsky, M. L., Davidson, D. A., “Turbo-Abrasive Machining and Turbo-Polishing in the Continuous Flow Manufacturing Environment”, SME Technical Paper MR99-264, CONFERENCE PROCEEDINGS: 3rd International Machining and Grinding Conference, Cincinnati, OH, Oct 4-7, 1999, Dearborn, MI: Society of Manufacturing Engineers, 1999
(5) Gillespie, LaRoux, Deburring and Edge Finishing Handbook, Dearborn, MI: Society of Manufacturing Engineers, 1999
(6) Davidson, D. A., “Mass Finishing Processes”, 2002 METAL FINISHIING GUIDE BOOK AND DIRECTORY, White Plains, NY: Elsevier Science, 2002
(7) Davidson, D. A., “Micro-Finishing and Surface Textures”, METAL FINISHING”, (White Plains, NY: Elseveir) July, 2002
(8) Massarsky, M. L., Davidson, D. A., “Turbo-Abrasive Machining and Turbo-Polishing in the Continuous Flow Manufacturing Environment”, SME Technical Paper MR99-264, CONFERENCE PROCEEDINGS: 3rd International Machining and Grinding Conference, Cincinnati, OH, Oct 4-7, 1999, Dearborn, MI: Society of Manufacturing Engineers, 1999

Figure 7 – Mass finishing methods are usually thought of in terms of facilitating the surface finishing of large numbers of smaller parts. As can be seen from this illustration, very large structural components such as this titanium airframe bulkhead can be processed also. When coupled with both fixtured and sequential finish techniques these kinds of processes can not only be used to replace costly manual deburr operations, but also produce significant compressive stress and work-hardening effects that can dramatically increase metal fatigue resistance properties. Studies have shown that as part size grows, the more economical and practical vibratory deburring and vibratory peening/burnishing processes become as potential replacements for hand deburring and conventional shot peening process combinations.
Comentarios