Measuring and Mapping Surface Textures and Surface Finishes in 3D with SWLI
- Dave Davidson
- Jan 1, 2018
- 4 min read
Updated: Jul 18, 2020
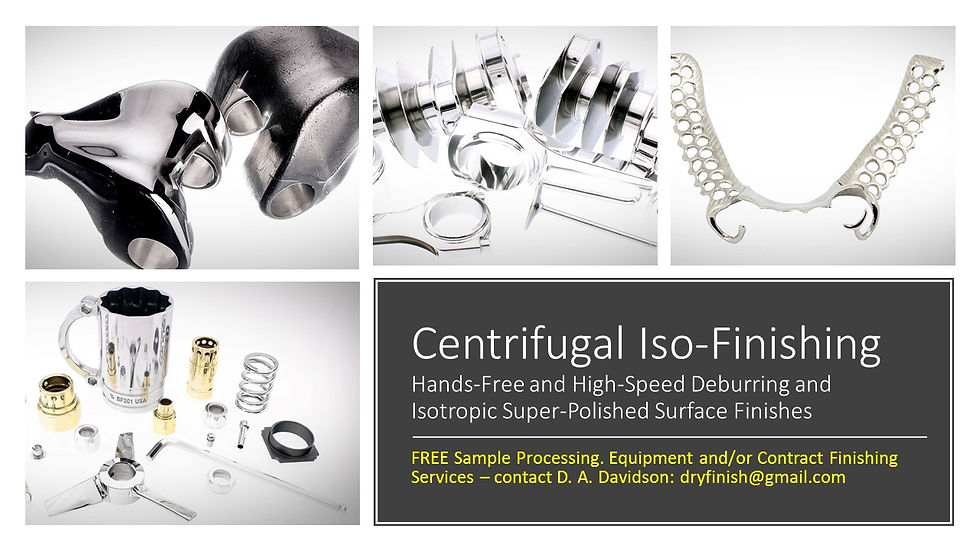
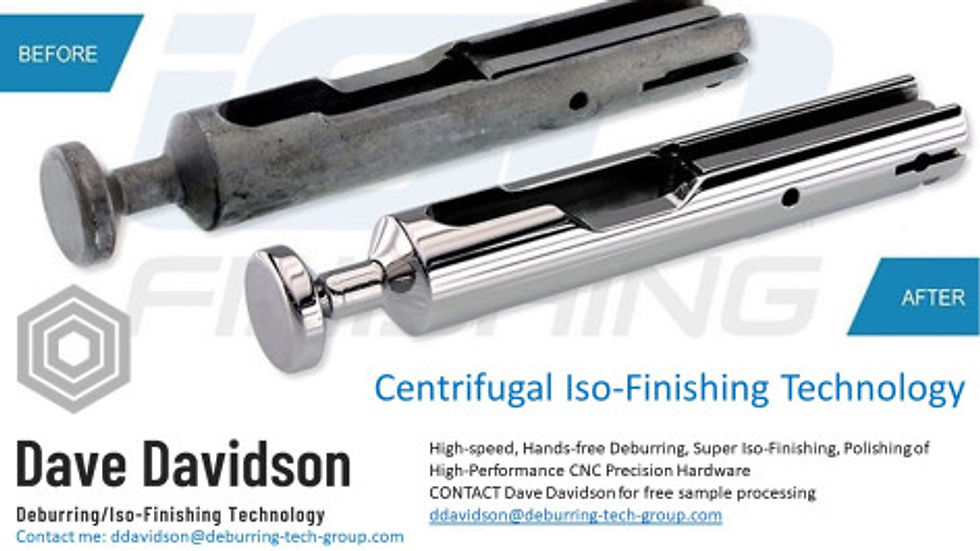

Article and surface measurement graphics contributed by Jack Clark, Surface Analytics, LLC
A Scanning White Light Interferometer (SWLI) is a device for measuring the physical geometrical (3D) characteristics of an object using broadband white light. Fourier analysis (and other methods) are used to convert interference intensity data (fringes) to the spatial frequency domain, allowing production of an extremely accurate surface map.
SWLI, also called coherence scanning interferometry (CSI) by the International Standards Organization (ISO), captures intensity data at a series of positions along the vertical axis determining where the surface is located by using the shape of the white-light interferogram. The white light interferogram actually consists of the superposition of fringes generated by multiple wavelengths, obtaining peak fringe contrast as a function of scan position. In an SWLI system, an imaging interferometer is vertically scanned to vary the optical path difference resulting in a series of interference patterns formed at each pixel in the instrument field of view. The data are stored digitally and processed in a variety of ways to produce Area (3D) results.
While profilometer traces are standard in many manufacturing operations, there is a growing realization that a better understanding of how surface finish and condition relates to the functional performance of parts in service can only be had with 3D mapping.
The surface measuring unit pictured in the feature photo above is a:
Model: NewView 7300, Manufacturer: Zygo Corporation, Middlefield, CT
Roughness and Form Measurement
Non-contact
Scanning White Light
<1Å z resolution
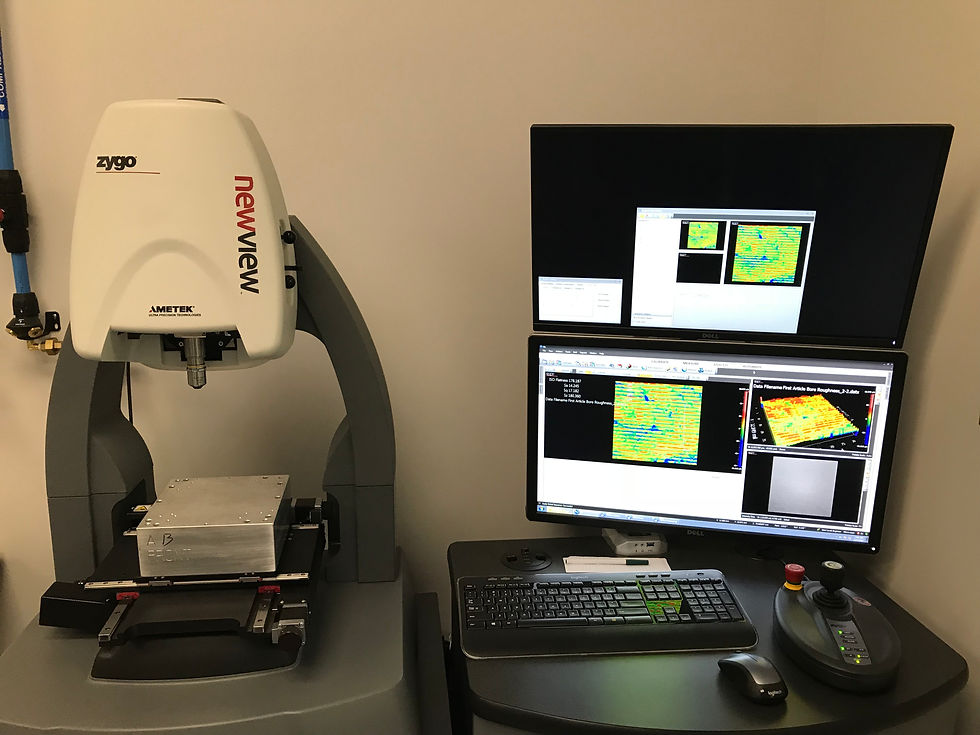
Above is shown a Zygo Model 8300 SWLI, used for surface mapping broader areas of surfaces into 3D graphics for a more detailed understanding of the surface texture of parts and components, especially after finishing processes have been completed.
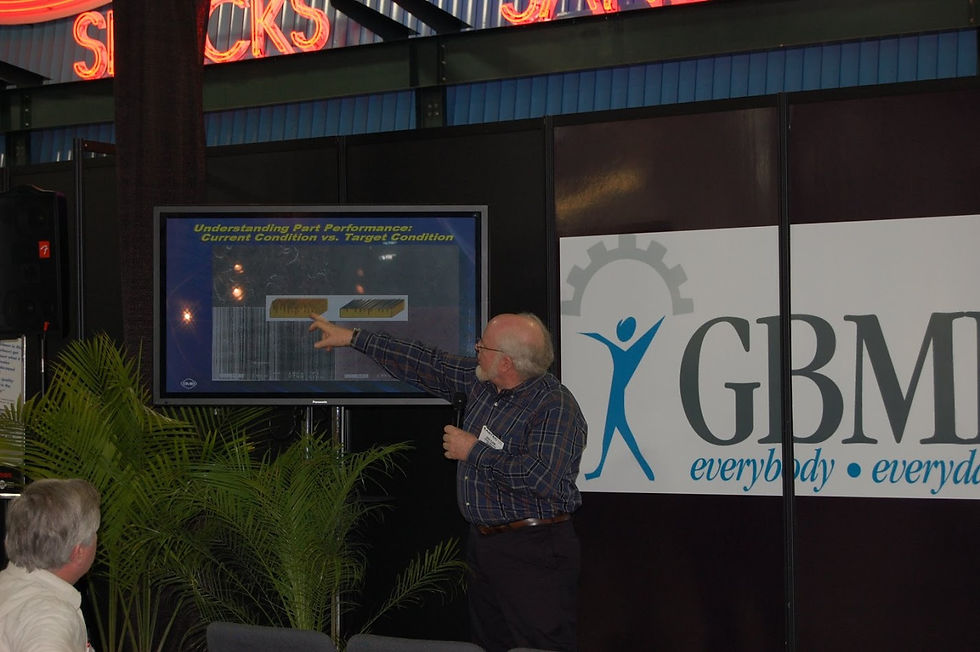
Jack Clark is a long time member of SME (formerly Society of Manufacturing Engineers) and ASME. He has written and lectured extensively on the subjects of surface finishing and surface metrology.
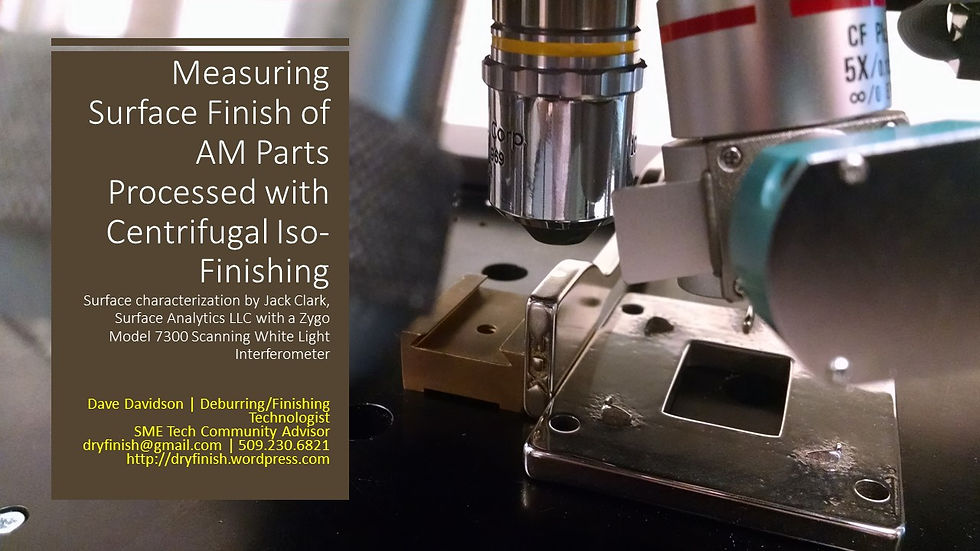
In this photo, AM (3DP) parts are being measured (mapped) following an operation with centrifugal iso-finishing to smooth and polish surfaces in a hands-free finishing operation

The above graphic shows a surface characterization of typical machined or ground surfaces with undesirable surface characteristics for parts with a need for wear resistance or fatigue failure resistance. These surface condition impairments can be remedied with post-process finishing methods such as centrifugal iso-finishing.
Understanding Centrifugal Iso-Finishing Technology
Centrifugal iso-finishing or barrel finishing (CBF) is a high-energy finishing method, which has come into widespread acceptance in the last few years. Although not nearly as universal in application as vibratory finishing, a long list of important CBF applications have been developed in the last few decades.
Similar in some respects to barrel finishing, in that, a drum-type container is partially filled with media and set in motion to create a sliding action of the contents, CBF is different from other finishing methods in some significant ways. Among these are the high pressures developed in terms of media contact with parts, the unique sliding action induced by rotational and centrifugal forces, and accelerated abrading or finishing action. With his high energy process, because time cycles are much abbreviated, surface finishes can be developed in minutes, which might tie up conventional equipment for many hours.
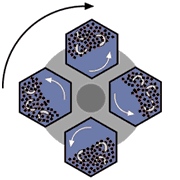
Centrifugal Barrel Finishing principles – high-intensity finishing is performed with barrels mounted on the periphery of a turret. The turret rotates providing the bulk of the centrifugal action, the barrels counter-rotate to provide the sliding abrasive action on parts.
The principle behind CBF is relatively straightforward. Opposing barrels or drums are positioned circumferentially on a turret. (Most systems have either two or four barrels mounted on the turret; some manufacturers favor a vertical and others a horizontal orientation for the turret.) As the turret rotates at high speed, the barrels are counter-rotated, creating very high G-forces or pressures, as well as considerable media sliding action within the drums. Pressures as high as 50 Gs have been claimed for some equipment. The more standard equipment types range in size from 1 ft3 (30 L) to 10 ft3, although much larger equipment has been built for some applications.
Media used in these types of processes tend to be a great deal smaller than the common sizes chosen for the barrel and vibratory processes. The smaller media, in such a high-pressure environment, are capable of performing much more work than would be the case in lower energy equipment. They also enhance access to all areas of the part and contribute to the ability of the equipment to develop very fine finishes. In addition to the ability to produce meaningful surface finish effects rapidly, and to produce fine finishes, CBF has the ability to impart compressive stress into critical parts that require extended metal fatigue resistance. Small and more delicate parts can also be processed with confidence, as the unique sliding action of the process seems to hold parts in position relative to each other, and there is generally little difficulty experienced with part impingement. Dry process media can be used in certain types of equipment and is useful for light deburring, polishing, and producing very refined isotropic super-finishes.
Below are some process video footage demonstrations of high-speed centrifugal isotropic finishing. These automated edge and surface finishing methods are capable of producing very refined low micro-inch surfaces that can improve functional part performance and service life.
AUTHOR BIOGRAPHY – David A. Davidson, [dryfinish@gmail.com] Mr. Davidson is a deburring/surface finishing specialist and consultant. He has contributed technical articles to Metal Finishing and other technical and trade publications and is the author of the Mass Finishing section in the Metal Finishing Guidebook and Directory. He has also written and lectured extensively for the Society of Manufacturing Engineers, Society of Plastics Engineers, American Electroplaters and Surface Finishers Association and the Mass Finishing Job Shops Association. Mr. Davidson’s specialty is finishing process and finishing product development.
For additional information about (free) sample part finishing contact Dave Davidson at ddavidson@deburring-tech-group.com


Comments