Meeting the Deburring Challenge on Complex Aerospace Parts
- Dave Davidson
- May 3, 2017
- 2 min read
Contributing editor:Dave Davidson |
dryfinish@gmail.com | https://dryfinish.wordpress.com | 509.230.6821
For additional technical information Contact Dr. Michael Massarsky, Turbo-Finish Corporation | 917.518.8205 | michael@turbofinish.com
TURBO-FINISH TECHNOLOGY
The technology is currently used in the United States to deburr and contour the edges of complex parts, and to create isotropic surface finishes essential in finishing many complex parts. Unlike single-point-of-contact machining technologies the technology is relatively simple to control once process parameters for a given part have been developed, and thus enjoys the attributes of reliability and repeatability of simpler mechanical (vs. digital feedback) technologies. However, It accomplishes uniform results on very complex parts that often cannot be achieved reliably by other much more complex, processes.
The technology involves developing a fluidized bed of media in which the part to be processed is partially immersed while being rotated. A wide variety of differing results may be achieved by varying the process parameters (media, process time, rotational speed etc.). Process results can be closely controlled and are programmable, and are totally repeatable, providing unequaled process quality control. The process is dry and involves no chemicals or environmentally unfriendly materials.
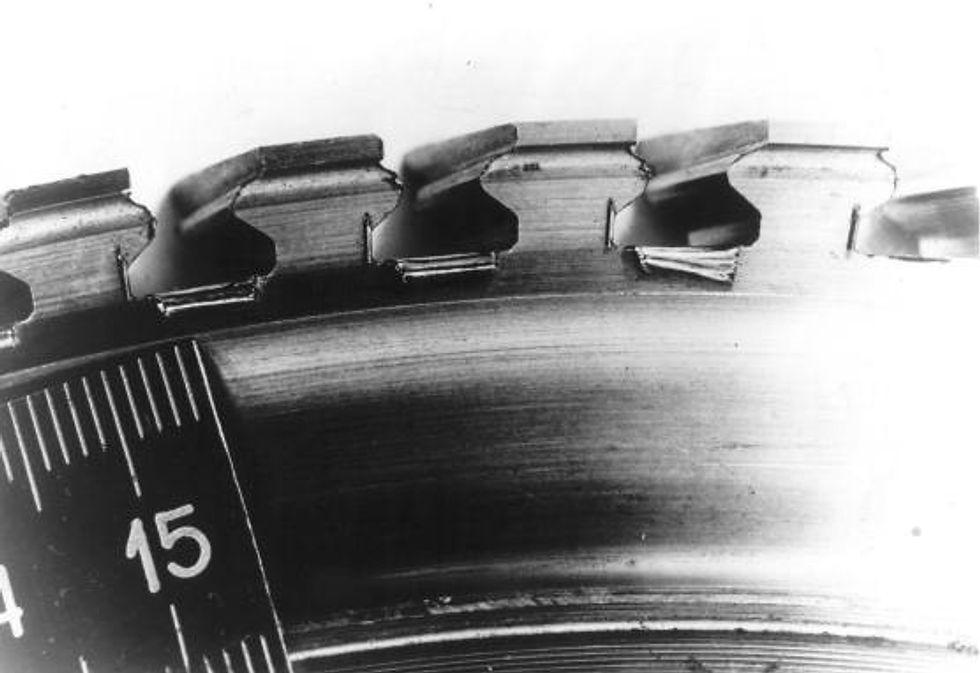
Before Processing with Turbo-Abrasive machining.
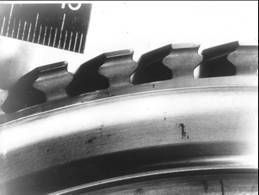
After Processing with Turbo-Abrasive Machining. A high-speed dry spindle finishing method with an abrasive fluidized-bed for deburring and isotropic finishing


Two step finishing procedure with Turbo-Finish. (1) Deburring, edge-contour and surface smoothing (2) Final finish and polish with Turbo-Finish fine polish media.
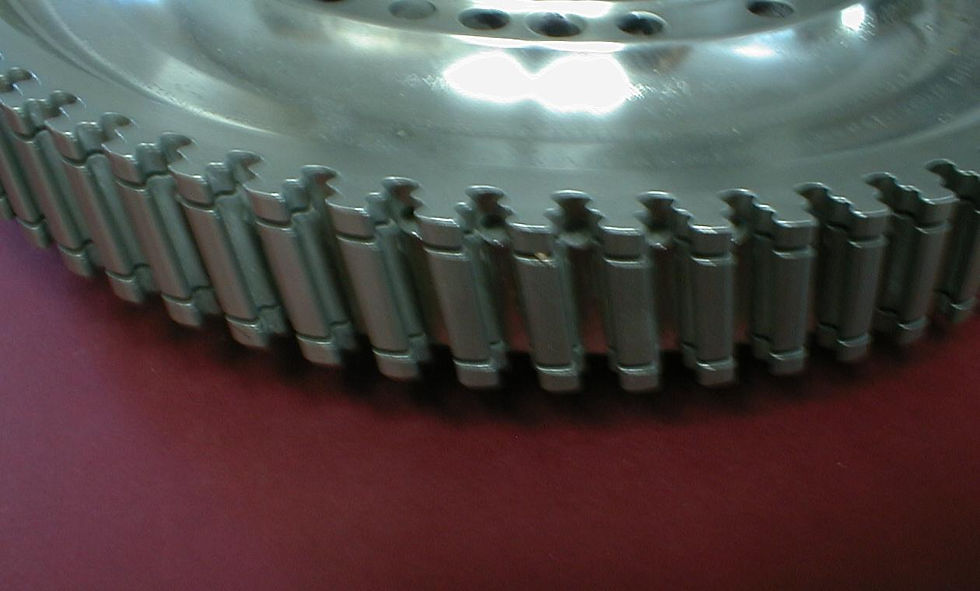
Edges and surfaces can be brought to below ten micro-inch Ra with secondary turbo-polishing operations. Fine finishes enhance visual inspection for quality assurance.

ABOVE: Heavily rooted burrs can be removed in a hands-free automated process.

ABOVE: Very rapid automated deburring and surface enhancement of rotor parts


Upper picture: Sharp edge condition and as ground surface condition prior to Turbo-Finish processing. Lower photo: Fir-tree geometries deburring and edge-contoured, Isotropic finish on disc surfaces.


Upper Photo: Disc prior to processing with Turbo-Finish, Lower Photo: Disc after processing

Processing of extreme burr and surface conditions

A Turbo-Finish Model 522-SS Turbo-Abrasive Machining Center
Comments