Next Generation Finishing Technology for Gears and Other Cooperating Parts
- Dave Davidson
- Aug 24, 2017
- 6 min read
ABOVE: Isotropic Micro-Finishing Photography by Mark Riley, BV Products
Ray Chalmers Interview with Dave Davidson, Deburring/Finishing Technologist ddavidson@deburring-tech-group.com | https://dryfinish.wixsite.com/iso-finish

If you have parts that need edge or surface finishing improvement and would like to have FREE sample part processing and a quotation developed for finishing the parts please contact Dave Davidson at ddavidson@deburring-tech-group.com I can also be reached at 509.563.9859. Information about equipment for bringing Centrifugal Iso-Finishing capability to your facility is also available…

Vibratory finishing, Centrifugal Iso-finishing, and turbo-abrasive machining are the three top techniques for finishing gears, improving performance and extending service life.
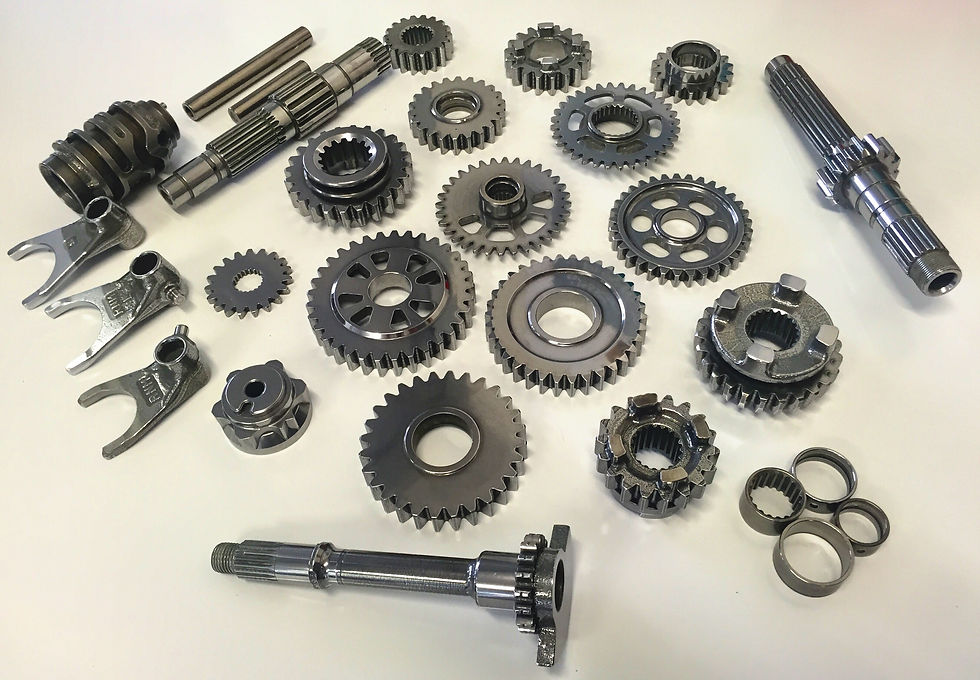
Isotropic finishing can have a dramatic impact on gear performance and service life, so much so that some racing teams disassemble stock gear sets and components and send them out to be isotropically finished for the performance and extended service life benefits. (Photo courtesy of Mark Riley, BV Products.)
Related Topics (Index Terms):
Deburring
Gear Production
Mass Finishing
Isotropic Finishing
Wear Resistance
Fatigue Failure Resistance
Lubricant Retention
Reduced Operating Temperature
Less Parasitic Friction
(Interview by Ray Chalmers) Dave Davidson has surface finishing in his DNA. His manufacturing beginnings trace to the 1970s working in a longstanding family business that manufactured wooden shoe pegs used for tumble-polishing small plastic items using steam-era machinery.
To get a leg up on the technology, Mr. Davidson, who remains active as a consultant in the industry, joined the Society of Manufacturing Engineers’ Burr, Edge and Surface Technology Division. With the help of SME mentors, he developed a line of abrasive and polishing products as well as new mass finishing processes for barrel, vibratory and centrifugal finishing systems. He is a master at problem-solving customer challenges.
That includes gear-making. Depending on the particular application, Mr. Davidson describes three mass-finishing methodologies for producing surface finishes on gears that contribute to improved performance and extended service life. They are:
Vibratory Finishing—Conventional and predominant, the familiar vibratory bowls or tubs come in small or large sizes and have been around for decades. There is a relatively recent wrinkle in vibratory finishing, chemically assisted vibratory finishing, which uses specially formulated chemical compounds along with non-abrasive media to produce a conversion coating on gears and similar components. This makes it possible to develop level surfaces with micro-finish surface attributes. This technology is especially applicable to automotive gear train systems and engine components such as camshafts and crankshafts and is widely seen among racing teams to acquire performance advantages.
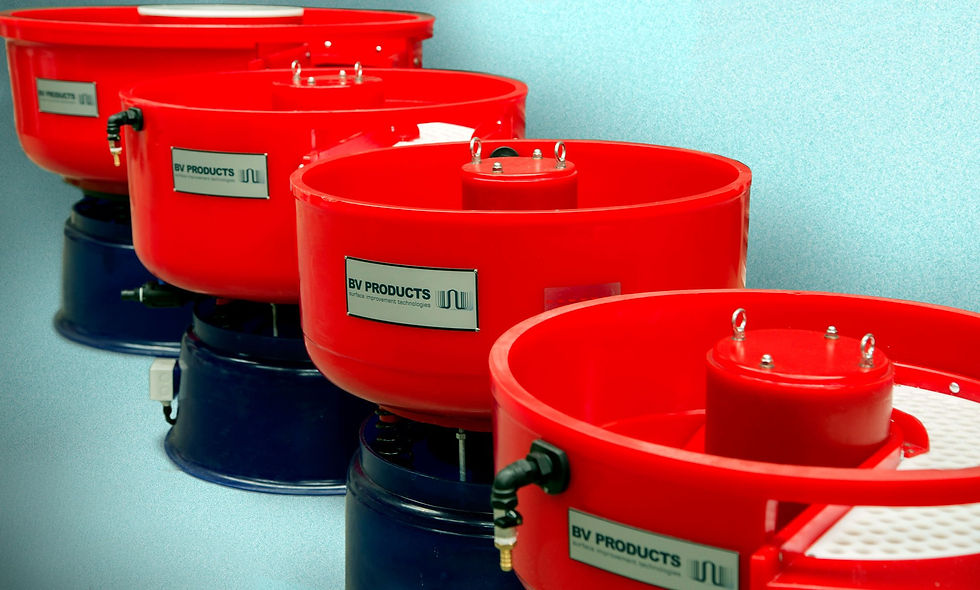
This slideshow requires JavaScript.
Above: Isotropic Micro-Finished Part photography by Mark Riley, BV Products
Centrifugal Barrel Finishing—This high-energy method is a mechanically accelerated means for producing edge contour and isotropic micro-finishes on gears. This method is used by a variety of gear manufacturers and high-performance racing teams to improve the surface finish and endurance of gear sets. It is also capable of producing low micro-inch finishes to improve load-bearing qualities of mating surfaces and to develop beneficial compressive stress and cold-hardening properties useful to highly stressed parts. A sequence of processes (analogous to roughing, finishing and polishing) is often used to develop highly finished surfaces. The high centrifugal forces and speed of this process achieve high-level surface finishes in short cycle times.
One user, Mr. Davidson recalls, pulled racing transmissions after each event for centrifugal finishing, only to find afterward that gear sets were lasting an entire season.
A note here about isotropic surface finishes for gears. Isotropic finishing, Mr. Davidson says, is a technical term used to distinguish surface finish patterns that are random and non-directional in nature. “This is in contrast to surfaces developed by all common machining and grinding methods, characterized by Gaussian peak-and-valley distributions parallel to each other that manifest a positive skewed surface with surface peaks and asperities predominating the surface profile,” he says.
By this definition, all mass finishing methods could be said to be isotropic in nature. The process outlined above, however, has been optimized to consistently produce gear surface finishes that will improve overall operational performance and extend service life.
This slideshow requires JavaScript.
Above: Centrifugal Iso-Finishing Part Applications
This slideshow requires JavaScript.
Turbo-Finish or Turbo-Abrasive Machining—This is the next-generation gear-finishing method, according to Mr. Davidson, who advises and assists Turbo Finish Corp. of Barre, Massachusetts, developer of turbo-abrasive machining (TAM). Not wholly machining and not wholly finishing, one of the properties separating TAM from vibratory or centrifugal gear finishing is that it is a dry method using no fluid media. Parts are fixtured on a spindle, similar to a horizontal machining center, and rotated at speeds ranging from 500 to 2,000 rpm, fully enveloped in an abrasive media cloud. Highly refined surfaces can be developed when a secondary operation utilizing dry polishing soft granulates, treated with fine polishing materials occurs as a follow-up to the abrasive deburring, contouring and smoothing operation. “Once you’ve got abrasive particles impinging the part at that level of force, you’re creating a shot-peening effect without creating shot-peening surfaces,” Mr. Davidson says.
From an environmental perspective, that TAM produces these effects in a waterless, dry operation is an added advantage. Unlike most of the other mass-finishing methods, TAM produces no wet-waste discharge effluent that requires treatment or remediation.
Admittedly, TAM investment is more on the capital equipment level, but users can create edge contours and other surface finishes very rapidly—with 60- to 120-second cycles in many cases—and machines can accommodate large gears in the 48-inch diameter range that would make vibratory or centrifugal finishing inefficient, if not impossible.
For additional technical information contact Dr. Michael Massrasky at Turbo-Finish Corporation at michael@turbofinish.com
This slideshow requires JavaScript.
Above: High speed deburring and isotropic finishing applications with Turbo-Finish Below: Video of Model TF-522 Turbo-Abrasive machining Center on compressor disk
Isotropic Finishing – Advantages and Benefits
According to Jim Riley of BV Products, a surface improvement technologies specialist based in Victoria, Australia, the advantage and benefit feature sets most commonly attributed to these types of isotropic finishing are:
Performance Benefits
Reduced friction
Increased part durability
Improved corrosion resistance
Reduced wear
Reduced lubrication requirements and cost
Improved oil retention
Reduced contact and bending fatigue
Improved pitting resistance
Reduced vibration and noise attenuation
Reduced applied torque requirements
Improved surface finish uniformity (part-to-part, feature-to-feature, and lot-to-lot)
High-quality, micro-finished surfaces
Reduced Friction Benefits
Increased fuel economy
Reduced contact fatigue
Increased power density
Lower operating temperature
Extended mean time between maintenance overhauls
Reduced maintenance costs
Eliminated break-in
Extended component life
Reduced metal debris
Reduced part failures
Minimized overheating
Many gears and gear sets in a variety of industries remain subject to fatigue, fracture and wear, Mr. Davidson says. “Such parts can gain substantial improvements in life and performance, from alterations to their overall surface texture. Improvements in overall smoothness, load-bearing ratio, surface profile skewness and isotropicity can, in many instances, improve life and performance and cut operational costs dramatically. Manufacturers that have not subjected their parts to an analysis to determine the potential benefits of this kind of processing may be making parts that are not all that they can be.”
ADDITIONAL VIDEO INFORMATION ON CENTRIFUGAL ISO-FINISHING:
Below are some process video footage demonstrations of high-speed centrifugal isotropic finishing. These automated edge and surface finishing methods are capable of producing very refined low micro-inch surfaces that can improve functional part performance and service life.
SEE video below showing the three-step Centrifugal Iso-finishing process for developing super-finished and polished surfaces.
CENTRIFUGAL ISO-FINISHING TECHNOLOGY
Centrifugal barrel finishing (CBF) is a high-energy finishing method, which has come into widespread acceptance in the last 25-30 years. Although not nearly as universal in application as vibratory finishing, a long list of important CBF applications have been developed in the last few decades.
Similar in some respects to barrel finishing, in that a drum-type container is partially filled with media and set in motion to create a sliding action of the contents, CBF is different from other finishing methods in some significant ways. Among these are the high pressures developed in terms of media contact with parts, the unique sliding action induced by rotational and centrifugal forces, and accelerated abrading or finishing action. As is true with other high energy processes, because time cycles are much abbreviated, surface finishes can be developed in minutes, which might tie up conventional equipment for many hours.
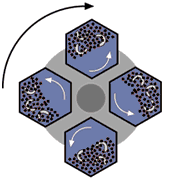
LEFT: Centrifugal Barrel Finishing principles – high-intensity finishing is performed with barrels mounted on the periphery of a turret. The turret rotates providing the bulk of the centrifugal action, the barrels counter-rotate to provide the sliding abrasive action on parts.
The principle behind CBF is relatively straightforward. Opposing barrels or drums are positioned circumferentially on a turret. (Most systems have either two or four barrels mounted on the turret; some manufacturers favor a vertical and others a horizontal orientation for the turret.) As the turret rotates at high speed, the barrels are counterrotated, creating very high G-forces or pressures, as well as considerable media sliding action within the drums. Pressures as high as 50 Gs have been claimed for some equipment. The more standard equipment types range in size from 1 ft3 (30 L) to 10 ft3, although much larger equipment has been built for some applications.
Media used in these types of processes tend to be a great deal smaller than the common sizes chosen for barrel and vibratory processes. The smaller media, in such a high-pressure environment, are capable of performing much more work than would be the case in lower energy equipment. They also enhance access to all areas of the part and contribute to the ability of the equipment to develop very fine finishes. In addition to the ability to produce meaningful surface finish effects rapidly, and to produce fine finishes, CBF has the ability to impart compressive stress into critical parts that require extended metal fatigue resistance. Small and more delicate parts can also be processed with confidence, as the unique sliding action of the process seems to hold parts in position relative to each other, and there is generally little difficulty experienced with part impingement. Dry process media can be used in certain types of equipment and is useful for light deburring, polishing, and producing very refined isotropic super-finishes.
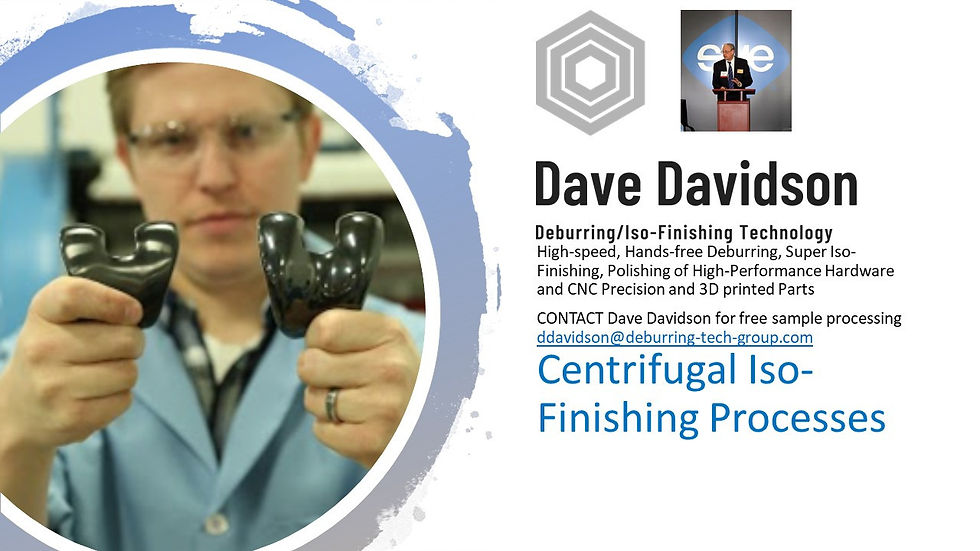
Mr. Davidson is a deburring/surface finishing specialist and consultant. He has contributed technical articles to Metal Finishing and other technical and trade publications and is the author of the Mass Finishing section in the current Metal Finishing Guidebook and Directory. He has also written and lectured extensively for the Society of Manufacturing Engineers, Society of Plastics Engineers, American Electroplaters and Surface Finishers Association and the Mass Finishing Job Shops Association. Mr. Davidson’s specialty is finishing process and finishing product development. Contact him for additional information or assistance with getting your parts sample finished for either having your parts contract finished or bringing the Centrifugal Iso-Finishing Technology to your facility.
CONTACT: ddavidson@deburring-tech-group.com | +1.509.563.9859

Comments