Part Stress Relief and High-Speed Centrifugal Barrel Tumbling
- Dave Davidson
- Dec 7, 2021
- 3 min read
Updated: Dec 25, 2021
Excerpted from SME Technical Paper MR79-569 by J. Bernard Hignett edited and updated
by Cole Mathisen
For additional technical assistance or to make arrangements for sample processing your parts contact:: Dave Davidson | Deburring/Surface Finishing Technologist at | ddavidson@deburring-tech-group.com
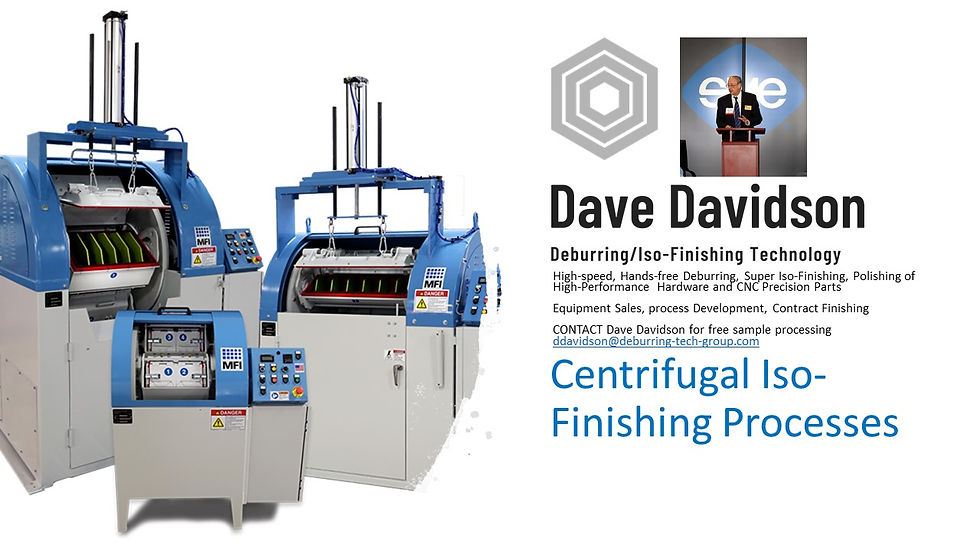
Shown above, (from smallest to largest), Model HZ-40, HZ-60 and HZ-160 Centrifugal iso-Finishing machines.
Metal fatigue is the most common cause of fracture in metal components. It is usually caused by numerous repeated applications of low stress—stress much lower than that needed for fracture in a single application. The higher the stress, however, the fewer applications are needed to cause failure. It follows that fatigue failure will be most common in components that are highly stressed and subject to repeated applications of stress in their functioning. A fatigue crack usually starts because of the tensile component of stress at the surface. of the material is too high. It is thus beneficial to impart compressive stress of components to oppose any tensile stress to which the component may be subjected in service.
High-Energy surface finishing methods can be used to change surface attributes such as compressive stress, develop isotropic surfaces and produce surface profiles that are neutral or negatively skewed. These attributes can contribute significantly to wear resistance, metal fatigue prevention and load-bearing improvement. Edge and surface finishing improvement can reduce the risk of fatigue failure. Surface imperfections can act as stress raisers and removal of these will invariably improve the performance of any highly stressed part. For critical components, it is desirable to achieve very high surface finishes to facilitate inspection for stress raises.

The chart above shows a comparison between compressive stresses generated by conventional shot peening and centrifugal iso-burnishing. The centrifugal iso-burnishing (unlike shot peening) can produce surfaces that resist fracture and metal fatigue cracking along with refined surface finish values simultaneously, obviating the need for a secondary surface finish operation to refine the surface rougness normally seen with peened surfaces. (Editor's note)
Removal of burrs and uniform radiusing of all sharp edges and corners will similarly improve performance. As has already been discussed, the CBF process can simultaneously deburr, edge radius and surface finish an immense range of components. It can also impart very high compressive stresses uniformly to the parts while edge radiusing and surface finishing so offering the unique capability of improving the resistance to fatigue failure of many highly stressed parts. The capability to improve resistance to fatigue failure is demonstrated by the results of some tests made by a manufacturer of stainless steel coil springs which were taken from a standard production run, Half of the components had the conventional finishing process of barreling, followed by shot peening, and the other half were processed in a centrifugal barrel machine for 20 minutes. The springs were tested to failure by compressing them from 1.104″ length to .730″, corresponding to a stress change from 9 to about 50,000 psi. The results were that all springs finished by the conventional method failed at between 160,000 and 360,000 cycles. The springs that had been tumbled in a CBF machine failed at between 360,000 and 520,000 cycles, an average performance improvement of 60%.
The tests indicated a benefit potentially greater than mere improvement of resistance to fatigue failure. It was noted that some of the parts that were processed in centrifugal barrel equipment had clearly visible surface defects or inclusions. Such defects were not visible in the parts that had been barreled and peened. It was the parts with the visible defects which were always those that failed below 400,000 cycles so that if an inspection department were instructed not to accept parts with such defects, then the performance of the springs put into service would be of consistently much higher quality. ________________________________________________________________________________________________
Shown below are some video examples of Centrifugal Iso-Finishing Equipment in operation...
Comments