Stock and Material Removal with High Energy Centrifugal Isotropic Finishing
- Dave Davidson
- Dec 27, 2011
- 2 min read
Edited by Dave Davidson | Deburring/Finishing Specialist | dryfinish@gmail.com
Excerpted from SME Technical Paper MR79-569 by J. Bernard Hignett
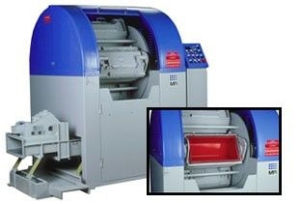
Centrifugal BarrelFinishing equipment such as this four barrel unit shown here can be utilized for stock removal in applications requiring removal of surface contaminants, and the blending in of machining and milling paths.
Like nearly all edge and surface finishing processes, centrifugal barrel equipment deburrs, radiuses edges and improves the surface of parts by removing stock from appropriate areas. Although this heading can encompass all applications it is worth considering stock removal in centrifugal barrel machines as an alternative to other grinding operations.The bearing industry makes extensive use of centrifugal barrel machines. One stock removal application is for grinding of bearing balls and this offers substantial economies compared with conventional grinding techniques. Centrifugal barrel finishing can be used for grinding of balls, both before and after hardening, And while it will not improve sphericity of the product substantially, it will precisely maintain tolerances and be absolutely consistent in result. Typical rates of stock removal are .006″ diameter reduction per hour on unhardened balls of 0.5″ diameter, and .004″ per hour on similar-sized balls after hardening. The machine shown in Figure 6 will handle 3,000 lbs. of balls each load, and with this equipment, total grinding costs in terms of labor, consumable materials, equipment amortization and maintenance can typically be not more than 75% of other grinding techniques. Even more dramatic results are achieved on bearing rollers. Generation of the correct crown and radius shape of needle rollers takes five percent of the time taken in conventional tumbling barrels, with very much improved consistency. Heavy grinding of cylindrical rollers in CBF machines achieve edge radii of as much as .060 inches, taper rollers are ground to remove parting line and

Magnified view of bearing surface after surface peaks have been removed (top series of diagrams). This method is an economical way of blending in machining or grinding lines to develop isotropic surfaces. Photo courtesy of Jack Clark, Surface Analytics LLC
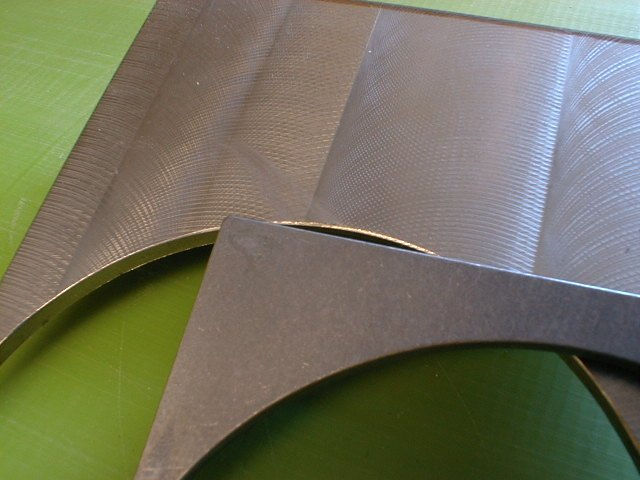
An example of milling and machining mark removal. The lower test bland has had machining marks removed by centrifugal barrel finshing.
blend radii and all types of rollers are processed for blending and finishing purposes. On more complex shaped parts, centrifugal barrel finishing can remove stock uniformly so that both descaling and surface finishing can be accomplished economically and simultaneously. This capability has real importance in the aerospace industry where many preforms of sophisticated alloys may have impurities in the surface that have to be removed. For example, the preforms for hot isostatic pressings require a .105″ envelope to be ground away to remove surface defects. It is also necessary to achieve a uniform and smooth surface finishing for sonic inspection. The centrifugal barrel process achieves these results much more economically than machining the components all over with a more suitable final surface.

Roller bearings such as these can be both abrasively processed in CBF processing for stock removal, but can also be polished in the same equipment and different materials to achieve very low micro-finished surface profiles.
This slideshow requires JavaScript.
Comments