Technovation in Vibratory Deburring and Surface Finishing
- Dave Davidson
- May 18, 2019
- 3 min read
Updated: Jul 18, 2020
CONTACT: Dave Davidson, Deburring/Finishing Technologist | 509.563.9859 ddavidson@deburring-tech-group.com | https://dryfinish.wixsite.com/iso-finish
_______________________________________________________________________
BV Products Model BV5DR Vibratory Finishing Machine

Robust design with direct-drive motor and integrated parts/media separation for economical vibratory finishing of metal parts. BV Products has been perfecting its unique all cast polyurethane vibratory finishing machines with direct-drive motion generators for almost 40 years to make them the most innovative and most cost-effective surface finishing solution in the industry. Contact Dave Davidson: ddavidson@deburring-tech-group.com

ABOVE: BV Products machines have effective sound suppression with the BV designed hinged sound suppression cover.

BV Products also manufactures a full line of tub-shaped vibratory equipment which is widely used for the polishing of crankshafts and automotive components in super-finishing operations.
About Us
Our company was first incorporated over 37 years ago by people with a strong vision and a passion to turn their ideas into an innovative product. Their idea – that an accepted, traditionally manufactured piece of equipment should not only be more efficient and less costly to produce, it should also look good. This idea was predicated on keeping what is essentially a very basic piece of capital equipment simple to make, easy to operate, totally reliable and needing little maintenance. In almost 7 decades we are the ONLY company in the industry to re-consider the technology of manufacturing a vibratory bowl machine and radically change it to make it both perform and look better.
BV Products manufacture a wide variety of sizes and shapes of vibratory finishing equipment for both deburring applications as well as its proprietary super-finishing processes that can develop highly useful polished surfaces for performance and durability of cooperating parts.
To make this possible we had to start from the beginning by developing own materials, own molds and designing our purpose-built vibratory motors. We had to have in house polyurethane casting facilities – which we still have to this day to control the quality. This enabled us to establish molding techniques and casting methods specific to our requirements – to be able to invent and make what is known today as the most unique vibratory machine available.
Since those early days, our machines have gone through several re-development and improvement stages – and will continue to do so – as we learn and understand the possibilities that this unique concept is capable of and some of these are detailed in the next column. In the meantime, our company is continuing to enhance its reputation for producing truly innovative world-class products.
See a selection of Isotropic Micro-Finished components in the part montage shown below.
Introducing the world’s most innovative vibratory finishing machine
The work chamber of the machine or bowl is cast in one piece around a very heavy duty steel fabrication. It has extra thick walls compared to all other machines which provide superior rigidity and enable long life -allowing us to provide a 5-year warranty on premature wear.
The bowl never needs a costly re-line. At the end of its useful life it can be easily disposed of and simply replaced very quickly with a new one. A process that takes a few hours. Your downtime is therefore minimal compared with the more conventional, somewhat dated designs.
As it is a high-performance urethane structure, the bowl cannot crack or fatigue, resulting in performance at much higher speeds than traditionally built machines – enabling shorter process cycles.The bowl is lighter which means it requires less energy to operate without any sacrifice of performance.This enables us to generally use slightly more compact and more energy-efficient vibratory motors. The use of more compact motors means that the machines are much quieter in operation thus more environmentally acceptable than older designs of equipment that have remained the same for 70 years.
The design means fewer wearable parts and a more aesthetically pleasing appearance The machines mounting base is cast entirely from polyurethane. It cannot rust, needs no bolting down and eliminates ALL vibrations to the factory floor. The machine is corrosion-proof and resists all common acids and alkalis. It is, therefore, an ideal choice for “exotic” processes such as ISFP, CASF and other chemically accelerated finishing applications
The machines enable us to offer a number of unique optional features – some of which are detailed in the following pages.JIT ( Just in Time) delivery. From raw materials to finished product can take as little as 24 hours which enables us to deliver competitively priced machines without having to stock and because of the machines, inherent low weight air shipment to customers anywhere is an option at very economical rates.
For more information contact: Dave Davidson | Deburring/Finishing Technologist ddavidson@deburring-tech-group.com | https://dryfinish.wixsite.com/iso-finish
Equipment Sales | Sample Processing and Process Development | Contract Finishing
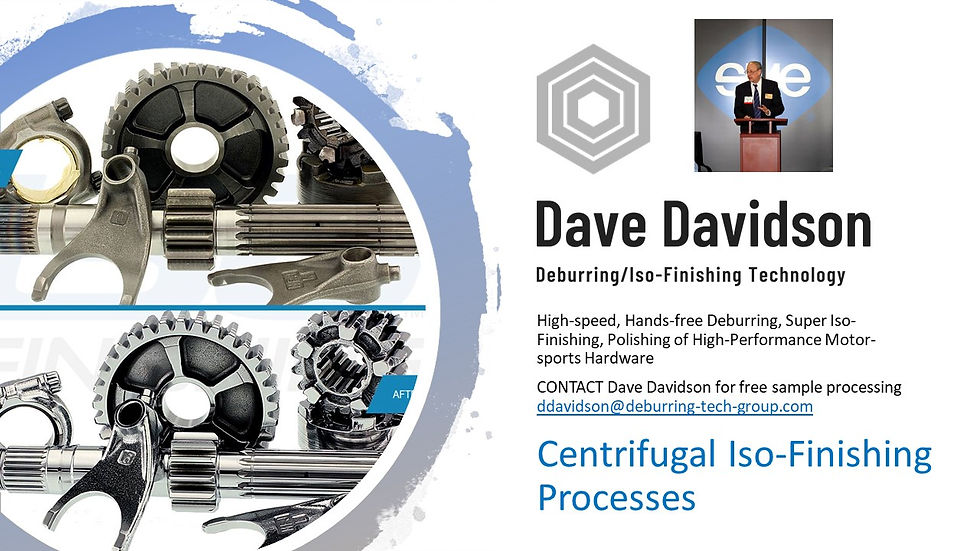
Comments