“Topical Case History – Converting from Standard Machined Surfaces to More Functional Plateaue
- Dave Davidson
- Nov 3, 2011
- 4 min read
Guest column by Jack Clark, President, Surface Analytics: jclark@surfaceanalytics.com and Colorado State University, Mechanical Engineering Dept. and SME’s Deburring and Surface Conditioning Technical Group
Contributing Editor: Dave Davidson | Deburring/Surface Finishing Technologist ddavidson@deburring-tech-group.com | dryfinish.wixsite.com/iso-finish
Edge and surface finish can be important factors in driving part performance of metal parts.

Top Figure 1 – Before finishing or honing. | Bottom Figure – Figure 2 Plateaued surface after surface finishing Diagrams Courtesy of Jack Clark, Surface Analytics., Optical Interferometry Graphics produced with Model 730 instrument
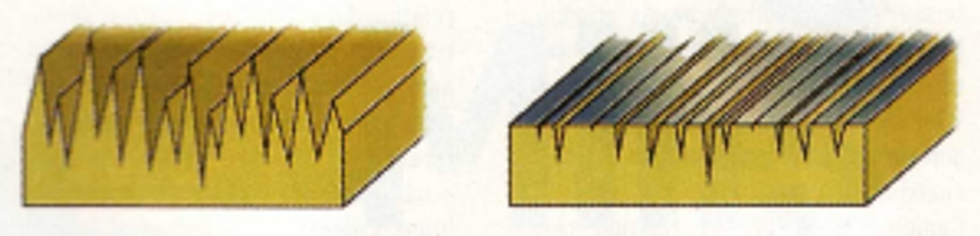
Typical Gaussian machined surface vs. Plateaued or planarized surface
Problem: Prior to the early 1970’s, there was little to no awareness of relating part function to the process that created a piece part. Many areas of automotive power train manufacturing was starting to realize that component failure was causing increases in scrap and warranty costs even though the specified metallurgy, fit and form was specified and controlled properly. There was no unified understanding of the root cause of premature wear, leakage, noise, unusually high operating temperatures and catastrophic failure, or, even if they were related. A conventionally produced surface (turned, milled, ground, EDM) is typically Gaussian in nature, that is, the peak and valley distribution is pretty much equal in height. This type of surface can be very unstable and unpredictable when wear and load bearing factors are considered.
Definitions:
A conventionally produced surface (turned, milled, ground, EDM) is typically Gaussian in nature, that is, the peak and valley distribution is pretty much equal in height. This type of surface can be very unstable and unpredictable when wear and load bearing is considered. The images in Figure 1. demonstrate this type of surface. There are many ways to produce plateaued surfaces. They are varied in approach but all have the ability to control the surfaces peak characteristics separately for the valley characteristics. This is summarized in Figure 2. showing that the peak and valley distributions can be controlled to allow substantial bearing load capabilities (broad, flat areas) with well-defined lubrication, debris collecting valleys.
This slideshow requires JavaScript.
The part slides shown above have isotropic and negatively skewed or neutral surfaces. Parts were processed with either Centrifugal Iso-Finishing which is a high speed, high G force and high-pressure mothod or chemically accelerated Isotropic micro-finishing.
The constant that must be maintained to ensure part function of the sealing system is the specification and consistency the surfaces involved. There are very specialized ISO Standard parameters that were designed to describe plateaued finished surfaces. These are the Bearing Ratio parameters (Rpk, Rk and Rvk) and, more recently, the Probability Parameters (Rpq, Rmq, Rvq). They monitor the peak and valley regimes of the surface independently allowing the production team to know that the process and therefore, the piece part, will function.
Gear Contact Surfaces:
Gears of all types must be designed to maintain their integrity under very high local surface loads. The industry has always battled what material, what form, what surface will survive the varying designs and environments. Again the surface must distribute the lube well and, at the same time, have the capability to withstand very high unit area load.
This slideshow requires JavaScript.
ABOVE: Gear performance and service life can be improved dramatically when isotropic finishing technologies are utilized are used as a post-machining method to improve surfaces.
The plateauing process generally will produce a surface free of local anomalies that can increase the local unit load and initiate a failure site. The mechanisms for surface failure are many and, sometimes difficult to identify. It has been found that when attention is paid to the integrity of the contacting gear surfaces by reporting the correct parameters during production, gear life is extended, noise and operating temperatures are reduced, and wear is minimized.
Conclusion:
The mechanism that allows for improved “functionality” for all surfaces is basic to surface performance – to accept the loads imposed and resist wear. Traditional processes that generate form and control fit do not necessarily dictate whether that part or assembly will function. Over the last three (3) decades, it has been realized that there is another contributor to part performance – Surface Finish. If a manufacturer does not account for surface finish characteristics like lube retention, micro burr removal, identification of torn and folded material, directionality, and load bearing capability, he then cannot predict the performance of components in the system.
Through progressive process development, evolving measurands (new ISO Standard Parameters), and a mature understanding of the “Function” of surfaces, manufacturers can design parts that become assemblies that are in systems performing over predictable, extended lives. This is the key to reduced warranty costs, reduced scrap, lower production costs, and satisfied customers. One popular method for producing these important functionaal surfaces is Centrifugal Iso-Finishing Technology. More details about this important deburring and surfacing technology is shown below. □
Centrifugal Iso-Finishing Technology

Contributing Editor: Dave Davidson, Deburring/Finishing Technologist 509.563.9859 ddavidson@deburring-tech-group.com | https://dryfinish.wixsite.com/iso-finish
If you have parts that need edge or surface finishing improvement and would like to have FREE sample part processing and a quotation developed for finishing the parts please contact Dave Davidson at dryfinish@gmail.com I can also be reached at 509.563.9859. Information about equipment for bringing Centrifugal Iso-Finishing capability to your facility is also available…
Below are some process video footage demonstrations of high-speed centrifugal isotropic finishing. These automated high-energy and hands-free edge and surface finishing methods are capable of producing very refined low micro-inch surfaces that can improve functional part performance and service life and minimize the need for hand-deburring or finishing methods. (1) The first video shows a process for smoothing and then polishing some aluminum parts. Other metal alloys can also be deburred, finished or polished with variations of this basic process. (2) The second video in the series was shot by SME (Society of Manufacturing Engineers) on the factory floor at MacKay Manufacturing in Spokane, Washington. Katie MacKay narrates how they utilize Centrifugal Iso-Finish processes to minimize hand-deburring and develop highly polished surfaces for their precision medical, aerospace and other components. The other videos offer additional Centrifugal Iso-Finishing information…
CONTRIBUTING EDITOR BIOGRAPHY – David A. Davidson, [dryfinish@gmail.com] Mr. Davidson is a deburring/surface finishing specialist and consultant. He has contributed technical articles to Metal Finishing and other technical and trade publications and is the author of the Mass Finishing section in the current Metal Finishing Guidebook and Directory. He has also written and lectured extensively for the Society of Manufacturing Engineers, Society of Plastics Engineers, American Electroplaters and Surface Finishers Association and the Mass Finishing Job Shops Association. Mr. Davidson’s specialty is finishing process and finishing product development.
For additional information on both sample processing and contract deburring and finishing services with the Centrifugal Iso-Finishing method visit our web-page on Contract Finishing (Free sample part processing):
SEE: https://dryfinish.wordpress.com/2016/08/05/contract-finishing-and-free-sample-part-processing-for-centrifugal-isotropic-finishing-and-polishing/
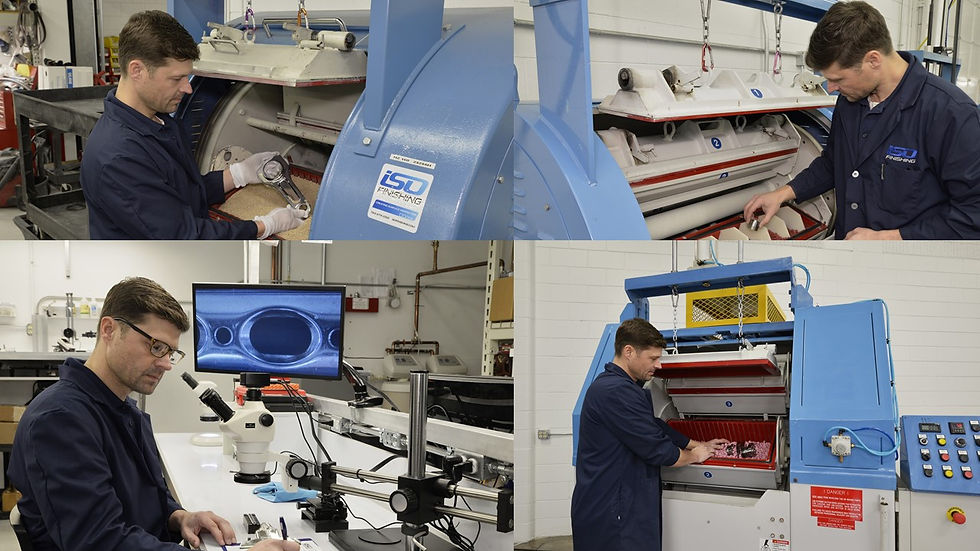
FREE SAMPLE PARTS PROCESSING AVAILABLE.
CONTACT DAVE DAVIDSON AT DRYFINISH@GMAIL.COM
Comentários