“Topical Case History – Converting from Standard Machined Surfaces to More Functional Surfaces
- Dave Davidson
- Jun 26, 2013
- 5 min read
Updated: Mar 18, 2021
For additional information contact: Dave Davidson, Deburring/Finishing Technologist | 509.563.9859 ddavidson@deburring-tech-group.com | dryfinish.wixsite.com/iso-finish
Technical Post : “Topical Case History – Converting from Standard Machined Surfaces to More Functional Plateaued Surfaces”. Contributed by: Jack Clark, Surface Analytics, Colorado State University and chair, SME Deburring, Edge Finishing and Surface Conditioning Technical Group,
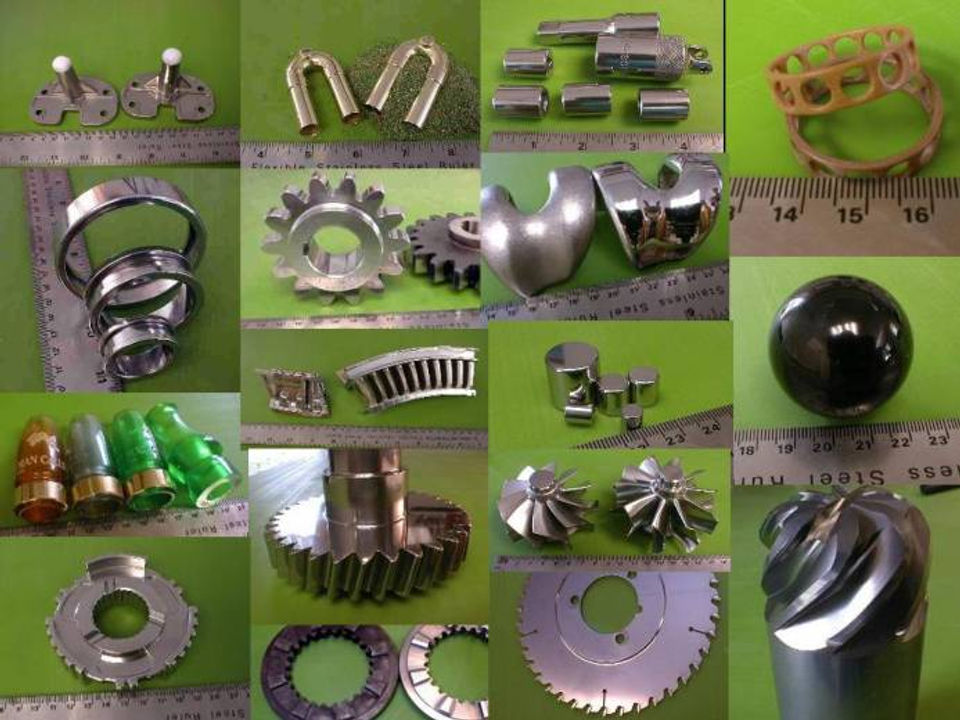
Parts of all sizes, shapes and compositions have been deburred, edge-finished, surface conditioned and even polished using mass finishing methods such as centrifugal barrel finishing. These parts exhibit isotropic surface conditions that can extend service life and improve function.
Problems: Prior to the early 1970s, there was little to no awareness of relating part function to the process that created a piece part. Many areas of automotive power-train manufacturing were starting to realize that component failure was causing increases in scrap and warranty costs even though the specified metallurgy, fit and form was specified and controlled properly. There was no unified understanding of the root cause of premature wear, leakage, noise, unusually high operating temperatures and catastrophic failure, or, even if they were related.
Definitions: A conventionally produced surface (turned, milled, ground, EDM) is typically Gaussian in nature, that is, the peak and valley distribution is pretty much equal in height. This type of surface can be very unstable and unpredictable when wear and load bearing is considered. The images in Figure 1. demonstrate this type of surface.
Figure 1.
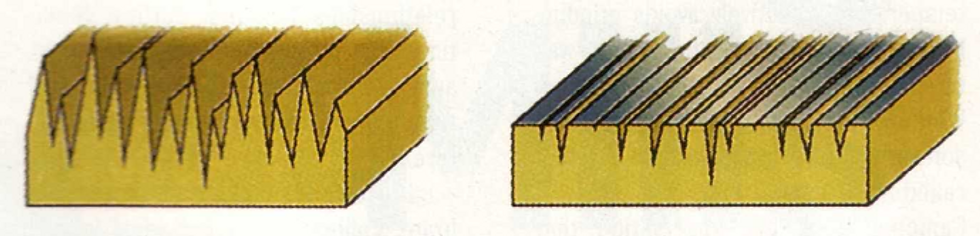
Typical machined surface vs. Plateaued surface after Isotropic Finishing
There are many ways to produce plateaued surfaces. They are varied in approach but all have the ability to control the surface’s peak characteristics separately for the valley characteristics. This is summarized in Figure 2. showing that the peak and valley distributions can be controlled to allow substantial bearing load capabilities (broad, flat are well-defined lubrication, debris collecting valleys.
Figure 2.

As machined surface to the right, isotropic and plateaued surface to the left was created with vibratory abrasive finishing method. Photo by Dave Davidson, SME MMR Tech Community
Examples - Engine Cylinder Bores: Honing cylinder bores produces an evenly distributed (gaussian) surface of peaks and valleys. Lubrication (lube) retention is dependent on the valley portion of the surface allowing even distribution over the entire swept area of the piston and rings. Contrary to that, the peak portion of the surface was not supporting the needs of other bore requirements such as, reducing friction, sealing to the piston ring, and reduction of wear. As extended warranty life (now over 100,000 miles in diesel applications), emission requirements, and higher combustion temperatures evolved, the need for more control of the surfaces became evident.
Plateau honing was first used as a final cylinder bore finishing technique in the 1970s. Later, 1980s, the diesel industry was instrumental in incorporating this technique to extend engine life and improve the sealing of the piston ring to the bore. Today, the gasoline engine manufacturers are finding that they must migrate to these bore conditioning practices to meet emission requirements and, again extend predictable engine life.
The solution has been in respecifying bore materials and implementing new honing techniques. The old standard of cast iron was a material that did not support finely controlled machining processes. Consistently there were issues with tears and folds in the surfaces, poor plateau and frictional characteristics. Manufacturers have migrated to various ferrous and non-ferrous materials that better support temperature variations, high unit surface loading, frictional requirements, and dimensional distortions typical of today’s advanced engine designs.
The constant that must be maintained to ensure part function of the sealing system is the specification and consistency of the surfaces involved. There are very specialized ISO Standard parameters that were designed to describe plateaued finished surfaces. These are the Bearing Ratio parameters (Rpk, Rk and Rvk) and, more recently, the Probability Parameters (Rpq, Rmq, Rvq). They monitor the peak and valley regimes of the surface independently allowing the production team to know that the process and therefore, the piece part, will function.
Gear Contact Surfaces:
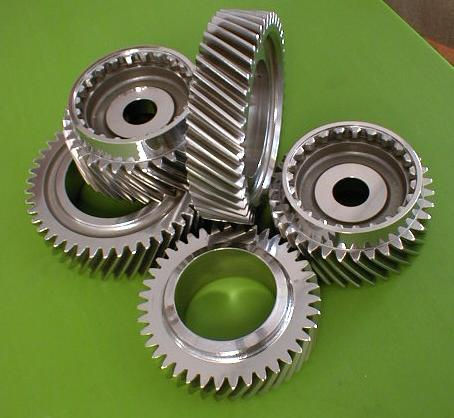
Drive train truck gears centrifugally finished for isotropic surface effect. Photo by Dave Davison, SME Tech Community
Gears of all types must be designed to maintain their integrity under very high local surface loads. The industry has always battled what material, what form, what surface will survive the varying designs and environments. Again the surface must distribute the lube well and, at the same time, have the capability to withstand very high unit area load.
As most of the economical process that generate the form of a gear are directional in nature, it is sometimes difficult to produce a surface that is capable of distributing the lube evenly. Manufactures have been quite creative in this arena by developing processes that can generate repeatable surfaces (much like the crosshatch of cylinder bores) or random lube retentive striations (mass finishing, liquid honing) that control lube very well.
These new process also produce the required plateau finish that allows for very high load bearing capability. Again, it is necessary to measure the appropriate surface parameters to know that the surface will function. In addition to the Standard Parameters listed previously, there are Bearing Ratio results that indicate the “true” load-bearing capability of a given surface. The Tp% and Htp of a surface will report load bearing and potential wear characteristics predicting component life and wear.

3D measuring technology such as optical interferometry can promote a deeper understanding of surface finish issues and help predict surface finish values effect on functionality and service life. The upper photographs show a Gaussian surface prior to mass media finishing operations. The lower set shows a negatively skewed plateaued or planarized surface that provides a much more functional surface for mating or cooperating parts. Images by Jack Clark, Surface Analytics LLC
The plateauing process generally will produce a surface free of local anomalies that can increase the local unit load and initiate a failure site. The mechanisms for surface failure are many and, sometimes difficult to identify. It has been found that when attention is paid to the integrity of the contacting gear surfaces by reporting the correct parameters during production, gear life is extended, noise and operating temperatures are reduced, and wear is minimized.
Conclusion: The mechanism that allows for improved “Functionality” for all surfaces is basic to surface performance – to accept the loads imposed and resist wear. The traditional processes that generate form and control fit do not necessarily dictate whether that part or assembly will function. Over the last three (3) decades, it has been realized that there is another contributor to part performance – Surface Finish. If a manufacturer does not account for surface finish characteristics like lube retention, micro burr removal, identification of torn and folded material, directionality, and load-bearing capability, he then cannot predict the performance of components in the system.
Through progressive process development, evolving measurands (new ISO Standard Parameters), and a mature understanding of the “Function” of surfaces, manufactures can design parts that become assemblies that are in systems performing over predictable, extended lives. This is the key to reduced warrantee costs, reduced scrap, lower production costs, and satisfied customers.
See Below: Case Study and operating videos of Centrifugal Isotropic Finishing
BELOW: Part examples of Centrifugal Isotropic Finishing
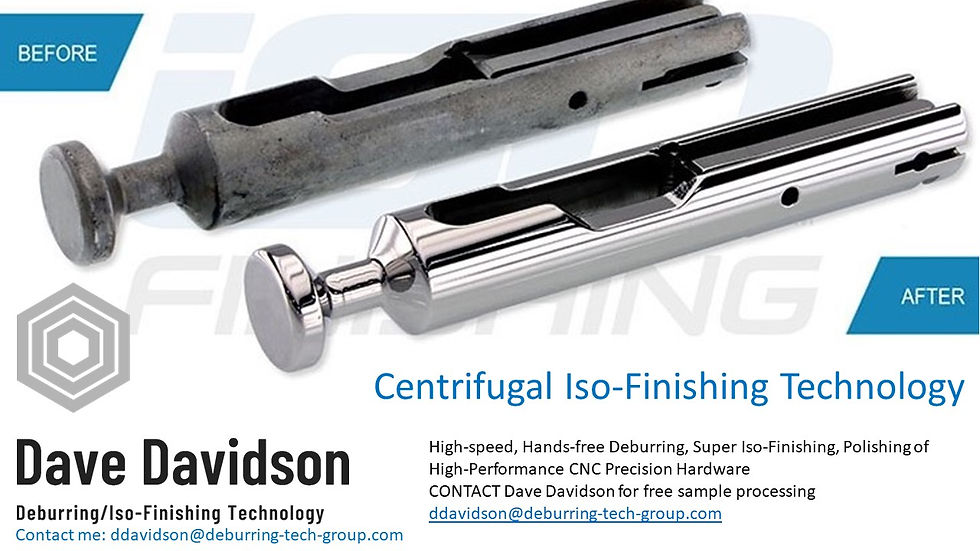
BIOGRAPHY – David A. Davidson, [dryfinish@gmail.com]
Mr. Davidson is a deburring/surface finishing specialist and consultant. He has contributed technical articles to Metal Finishing and other technical and trade publications and is the author of the Mass Finishing section in the current Metal Finishing Guidebook and Directory. He has also written and lectured extensively for the Society of Manufacturing Engineers, Society of Plastics Engineers, American Electroplaters and Surface Finishers Association and the Mass Finishing Job Shops Association. Mr. Davidson’s specialty is finishing process and finishing product development.

#SME #EdgeContourandFinish #3Dsurfacemeasurement #broachslotdeburringdeburring #TurboFinish #componentfailure #isotropicfinishing #centrifugalbarrelfinishing #machinedsurfaces #aircraftframedeburring #electronmicroscopy #abrasive #centrifugalbarrel #deburring #TumblingMassFinishing #compressivestress
Comments