Vibratory Edge and Surface Finishing – Evolving Requirements and Processes (Part 2)
- Dave Davidson
- Nov 8, 2011
- 6 min read

The capacity of tub-style vibratory equipment makes it possible to develop uniform edge contour and surface finish on larger components in an overall sense. This was not possible with methods dependent on single point of contact which permitted substantial variation in edge and surface effects. Vibratory finishing makes it possible to support and process heavy and large components within the media mass encapsulated in the working chamber. Photo courtesy of Giant Finishing, Inc.
by Dave Davidson | SME MMR Tech Community dryfinish@gmail.com
Mass finishing processes often reduce or eliminate many procedures that are labor intensive and require extensive part handling. This is especially important in meeting increasingly stringent quality control standards, as most mass finishing processes generate surface effects with part-to-part and lot-to-lot uniformity that cannot be replicated with processes in which parts are individually handled. It has become a manufacturing engineering axiom that part reject and rework rates will plummet, if a mass finishing approach can be implemented to meet surface and edge finish requirements.
Although each of the mass finishing process types carries with it a unique set of process strengths and weaknesses, all of them are sufficiently versatile to be able to process a wide variety of part types successfully. A plethora of abrasive media types, sizes, and shapes makes it possible, in many cases, to achieve very different results within the same equipment, ranging from heavy grinding and radiusing to final finishing. Components from almost every conceivable type of material have been surface conditioned using mass finishing techniques including ferrous and nonferrous metals, plastics, composition materials, ceramics, and even wood. Vibratory finishing is still the most predominant method in the United States, and it falls into two broad categories in terms of the equipment being used: round bowl and tub designs.
Round-Bowl Vibratory Systems Round-bowl equipment normally has a processing chamber that resembles the bottom half of a doughnut. Although up to 20% slower than tub-style machines, and having occasionally more unwieldy media changeover routines, the advantages in automation and material handling for these machines have often given them an edge in any processing cost per part analysis. The vibratory motion generator on these machines is customarily a vertical shaft mounted in the center-post area of the bowl. Adjustments related to the eccentric weights on this shaft will affect the rolling motion of the media, as well as the forward spiral motion of the media in the bowl chamber. This spiral motion is one of the machine’s more salient advantages, as it promotes an even distribution and segregation of parts in the mass, thus lessening the chance of part-on-part contact.
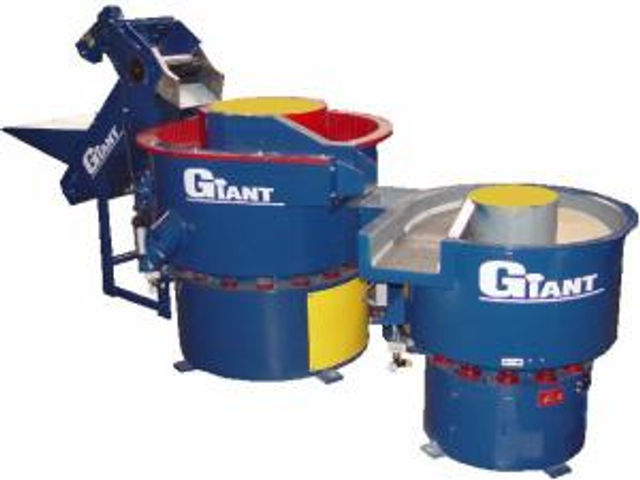
This photo show two round bowl vibratory systems being used in series. An automated part feeder meters in parts. After processing in an initial operation, parts can be separated and then transferred to either a secondary finishing operation or dried. Photo courtesy of Giant Finishing Inc.
Like tub machines, equipment size varies from small bench models, whose capacity are measured in quarts or gallons, to very large equipment in excess of 100 ft3 capacities. Successful processing requires appropriate media and compound selection, correct amplitude and frequency adjustments of the motion generator, and precisely determined water flow rate and compound metering rates. Unlike barrel systems, whose water levels are determined once at the beginning of the cycle, vibratory systems have a constant input and throughput of water into the system (both flow-through and recirculation systems are employed, although flow-through is generally much preferred). Water levels are critical to process success. Too much water will impede the vibratory motion of the mass. Too little will permit a soils/sludge buildup on the media, reducing its cutting efficiency. Flow-through functions can be automated with appropriate controls and metering devices. For parts requiring relatively short cycle times, round-bowl machines can be configured to perform in a continuous mode, the parts being metered in and then making one pass around the bowl, and exiting via the internal separation deck. Some designs include a spiral bottom to enhance loading from the machine onto the separation deck, lessening the likelihood of part-on-part contact at the entrance to the separation deck. Ease of use and economy are the hallmarks of vibratory finishing methods, and have contributed to making this perhaps the most accepted deburring and surface conditioning method for finishing parts in bulk. The equipment performs well in either batch or continuous applications. Standard applications usually can be run most economically in round-bowl-type equipment. Larger parts may require more specialized tub-type equipment, large volumes of parts, which can be processed in relatively short cycles, can make use of continuous tub or bowl equipment, or even multipath equipment. The latter can offer parts transfer from one operation to a secondary-type operation within the confines of the same machine, but different chambers. Vibratory action itself often will preclude the ability to develop superfinishes or microfinishes unless specialized chemically accelerated methods are adopted . (See photo gallery at end of article)

This type of “inline continuous” or “flow-through” unit is used to accommodate very high volumes of parts. Parts are introduced at the head of the machine, and are deburred and finished within the dwell time the parts remain in the media mass as they travel the length of the tube. Parts and media are then separated at the end of the tube, and media is conveyed back to the head of the machine where it is reintroduced to the media mass inside the processing chamber tube. Photo courtesy of Giant Finishing Inc.
Vibratory equipment ranges in size from 1 ft3 capacity up to 200 ft3. Tub vibrators are considered to have more aggressive media action than round-bowl machines, and they are capable of processing very large, bulky parts (as large as 6 ft by 6 ft) or potentially awkward part shapes (parts 40-ft long and longer). The vibratory motion generators consist of rotating shafts with sets of eccentric weights attached either at the bottom of the U-shaped tub or one of the sidewalls. This equipment is usually loaded from the top of the chamber, and usually unloaded through a discharge door located on a side panel. Parts and media can be screened on an external separation deck. This arrangement allows for relatively quick load/unload or media changeover cycles when compared with other equipment. Tub-shaped or tubular-shaped vibrators are commonly utilized for continuous high volume applications where the time cycle required to process the parts is relatively short. Media return conveyors and feed hoppers are used to meter the correct ratio of media and parts to the loading area of the machine, while media and parts are separated on a continuous basis by a screen deck located at the unload or discharge area of the machine. Tub-type machinery is also used extensively for batch applications and can be easily sub-compartmentalized for parts that require total segregation from each other.
Many manufacturers have discovered that as mass finishing processes have been

The ability to process larger and larger components is becoming an increasingly important characteristic of vibratory processing. The photo here shows aircraft frame processing. Even larger equipment has been developed to permit processing of aircraft engine casings and larger commercial aircraft frame and wing spar components. Photo courtesy of Samuel R. Thompson
adopted, put into service, and the parts involved have developed a working track record, an unanticipated development has taken place. Their parts are better—and not just in the sense that they no longer have burrs, sharp edges or that they have smoother surfaces. Depending on the application: they last longer in service, are less prone to metal fatigue failure, exhibit better tribological properties (translation: less friction and better wear resistance) and from a quality assurance perspective are much more predictably consistent and uniform. The question that comes up is why do commonly used mass media finishing techniques produce this effect? There are several reasons. These methods produce isotropic surfaces with negative or neutral surface profile skews. Additionally, they consistently develop beneficial compressive stress equilibriums. These alterations in surface characteristics often improve part performance, service life and functionality in ways not clearly understood when the processes were adopted. In many applications, the uniformity and equilibrium of the edge and surface effects obtained have produced quality and performance advantages for critical parts that can far outweigh the substantial cost-reduction benefits that were the driving force behind the initial process implementation.

Vibratory machinery designs can accommodate oversized and extremely heavy parts such as the 1200 lb. castings shown here. The advantages of this kind of processing is not just economic (reducing direct labor) but technical as well. Uniformity of edge and surface finish of parts can contribute to increased functionality. Photo courtesy of Samuel R. Thompson
______________________
1. Thompson, Samuel R., “Selection of Vibratory Equipment”, SME Technical Paper MR81-381, Dearborn, MI: Society of Manufacturing Engineers, 1981
2. Thompson, S. R., Comparison of Rectangular Tub and Inline Continuous Vibratory Equipment”, SME Technical Paper MR83-679, Dearborn, MI: Society of Manufacturing Engineers, 1983
3. Kittredge, John B., “Selection of Mass Finishing Equipment”, SME Technical Paper MR87-153, Dearborn, MI: Society of Manufacturing Engineers, 1987
4. Gillespie, LaRoux, Mass Finishing Handbook, pp. 237-247, New York, NY: Industrial Press, 2007
This slideshow requires JavaScript.
Comments