Vibratory Iso-Finishing Down-Under, World-Class Equipment with World-Class Finishing Processing
- Dave Davidson
- Sep 25, 2017
- 6 min read
Updated: Dec 3, 2020
Photo Credits: Mark Riley, BV Products, Australia
Contributing Editor: Dave Davidson, Deburring/Finishing Technologist | 509.563.9859 | dryfinish@gmail.com | dryfinish.wixsite.com/iso-finish
If you have parts that need edge or surface finishing improvement and would like to have FREE sample part processing and a quotation developed for finishing the parts please contact Dave Davidson at dryfinish@gmail.com I can also be reached at 509.563.9859 Information about equipment for bringing Centrifugal Iso-Finishing Equipment to your facility is also available…

BV Products All-Cast Polyurethane Vibratory Bowl Finishing Machines.
(Melbourne, Australia) Jim Riley, [ jim.riley@bvproducts.com.au ] owner of BV Products and the HPSF Contract Finishing Service Center has deburring and surface finishing in his DNA. His finishing process experience has included work in England, Canada, the United States and Australia. His company has been perfecting its unique all cast polyurethane vibratory finishing machines for almost 40 years. His unique equipment design makes his finishing equipment some of the most innovative and most cost-effective surface finishing process solutions available.
The company operating from a modern purpose built factory in the southeastern suburbs of Melbourne, stocks and produces to order a comprehensive range of equipment and materials for deburring and vibratory isotropic finishing of industrial components and parts. The company also maintains an extensive demonstration and job shop facility for many different types of applications. Not only does the company offer high-quality mass finishing products but also a fully documented process report sheet with each machine sold – established by the free sample processing and process development the company provides for each customer. Clients are thus assured of the best possible edge and surface finishing solution and result.
Jim Rilley Managing Director BV Products, HPSF & Massfinish Surface Finishing Centre 16 Access Way, Carrum Downs VIC 3201, Australia Bus: +61 (3) 9775 0898 Bus Fax: +61 (0) 3 9775 0897 Email: jim.riley@bvproducts.com.au Website <http://www.bvproducts.com.au/>
ABOVE: BV Products unique and innovative all-cast polyurethane direct-drive vibratory finishing machine with BV’s sound suppression cover.
Below: BV Products Bowl machine with integrated internal screen deck for easy parts and media separation
PROCESS DEVELOPMENTIn mass finishing, everything begins with selecting the correct process and in this regard the company develops processes by first providing a solution which then dictates the correct equipment and materials to be used. In an effort to select the correct type and size of machine and to establish the process parameters for achieving a particular finished result on the customer’s part the company operates a large demonstration facility with some eighteen machines of varying types and sizes. Customers simply submit parts to the company, with a control sample of what they wish to accomplish if possible, and the company will establish a process in the most suitable machine, media and compound that produces the optimum result for the customer application.

ISOTROPIC MICRO-FINISHING PROCESSES
The company has developed a range of finishing systems that produce extremely low surface roughness values and highly polished or reflective surfaces. The main benefits of this type of surface finish for industrial and automotive applications include:
Reduced Friction
Reduced Heat
Greatly increased service life
Improved efficiency which provides higher power outputs.T his technology is especially useful for automotive gear train systems and engine components (such as crankshafts and camshafts) and is used widely in the motorsports racing industry for improved engine performance. Other uses include components from the wind turbine industry, aircraft engine components and mining equipment where durability and long service life is a requirement.
Below: examples of BV Vibratory Iso-Finishing for gear train and engine component processed in the HPSF Finishing Service Center (Photos b Mark Riley, BV Products)
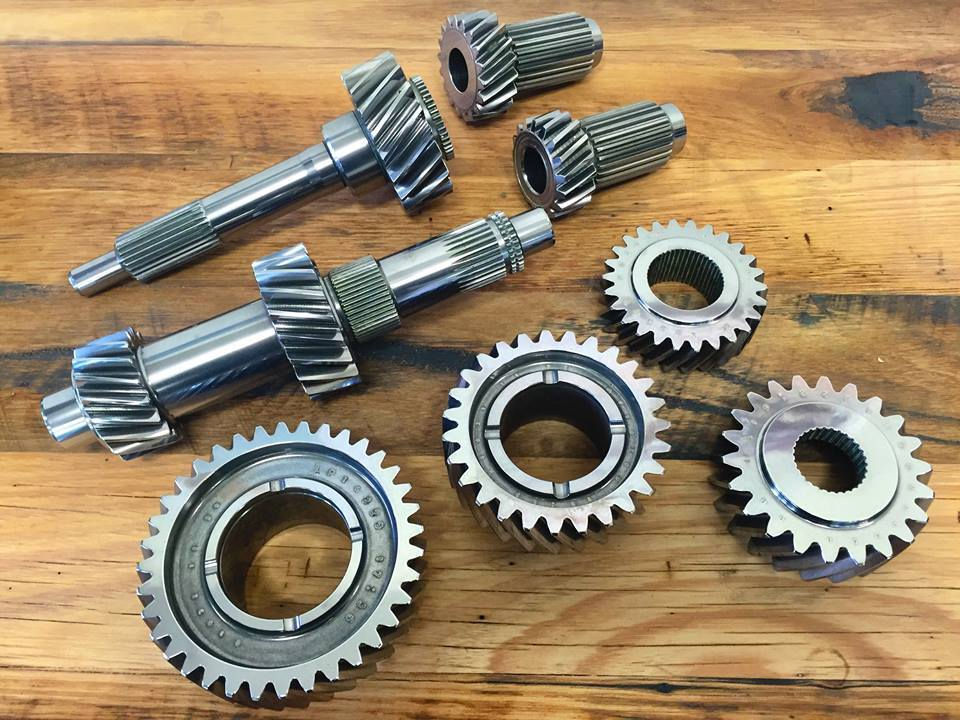

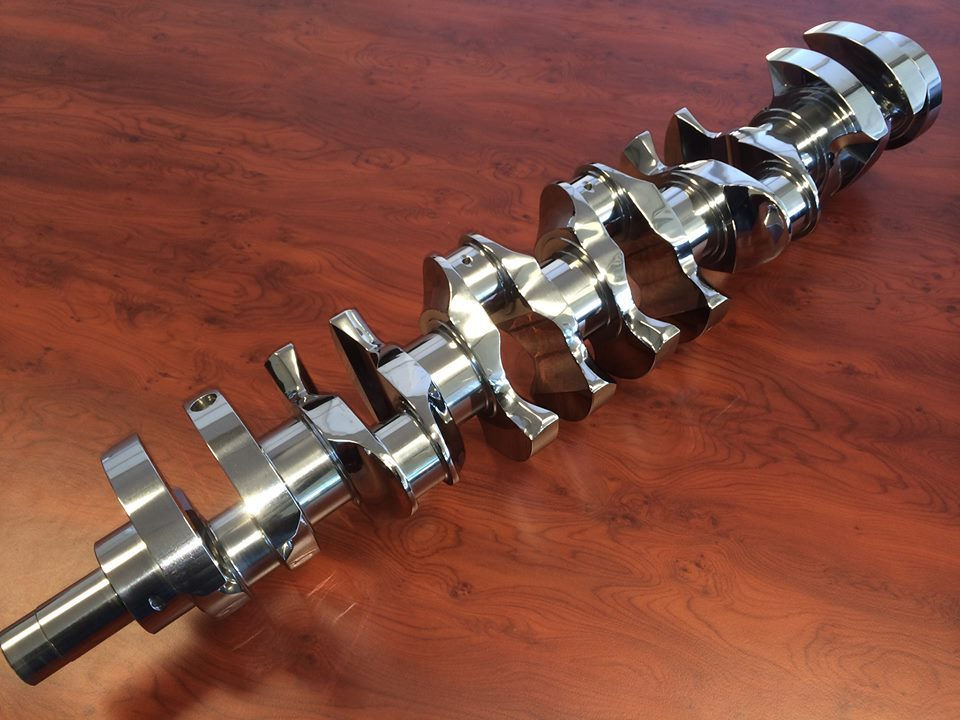




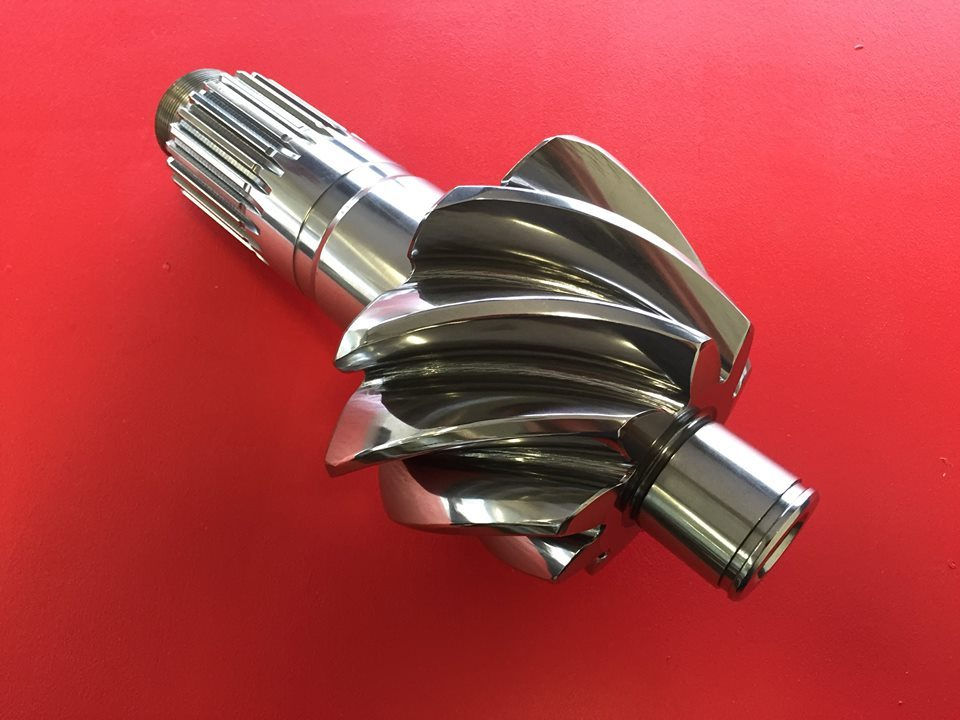

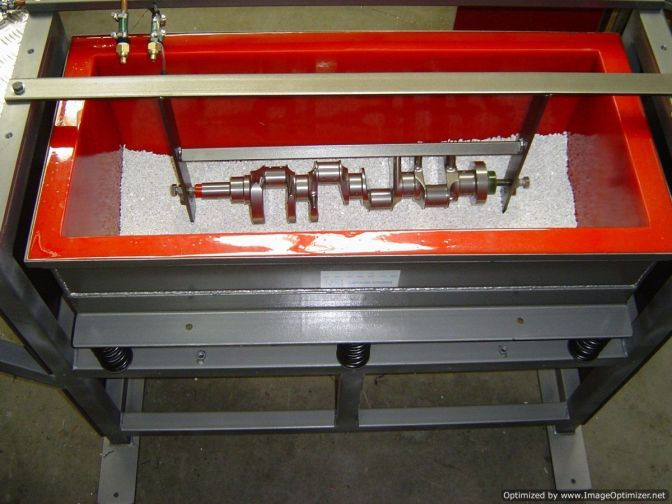
(Photo above) In some Isotropic Finishing applications, it can be useful to fixture parts in the media mass. this is a force multiplier and magnifies the force of the part is acted upon by the finishing media. The equipment shown is a tub-style vibratory machine and accommodate part lengths that would be impractical for round bowl-shaped vibratory finishing machines. Photo Credit: BV Products
Isotropic Micro-Finishing and Super-Finishing. The process of isotropic micro-finishing and superfinishing is used in applications such as Formula One, V8 Supercars, wind turbine transmissions, helicopter transmissions and other performance critical part applications. These processes are especially useful to improve surfaces in any area where it is desirable to reduce friction and heat and increase efficiency and service life. Specialized chemicals and processes have been developed over the past decade in order to produce these important surface effects economically.
Several high-performance component manufacturers are sending their products to specially equipped contract finishing service providers for final finish processing. Some of them offer it to their customers as an add-on, and others build the cost into the components’ selling price. Typical items processed include automotive gears, motorcycle gears, crown wheel and pinions, camshafts, oil pump internals, steering rack and pinion, and crankshafts. Not only does the Vibratory Isotropic Micro-Finishing [VIM] process significantly reduce wear in parts such as the ones listed above but it also enhances the durability and efficiency of metal components, resulting in cost savings and added value to parts and the manufacturer’s operational budget.
Vibratory Isotropic Micro-Finishing Isotropic Micro-Finishing is used to produce a high-quality surface finish to components, typically used on parts where high contact stresses are present. The improvements in surface finish gained by this superfinishing process can reduce wear and stress concentrations and improve overall finish while extending component life.
Wherever metals come into contact with each other contact stresses and friction occur. Both these conditions regulate and reduce the performance and compromise the design of the component. Micro-finishing is a means of regaining those losses by producing a superfine finish where it is most needed – at the point of contact. The benefits are greatest with high contact stress applications and high fatigue life requirements. It is particularly beneficial in mating gear applications where it is proven to reduce contact stresses but also to reduce individual tooth bending which is key to maintaining good fatigue life with a resultant reduced operating temperature. While it is known that reduced operating temperatures are an indication of increased performance the secondary benefit is that there is less heat to dissipate and as such the specific cooling cross-section or cooling flow rate can be reduced all of which complement efficiency and performance.
The Process. This process is radically different from conventional machining. The following is a brief overview of the chemically accelerated vibratory finishing process using high density, nonabrasive ceramic media.
Equipment: vibratory machines. The process is carried out in specially designed vibratory finishing bowls and or tub/trough machines. These durable machines have been around for more than 60 years. Vibratory machines are available in sizes from 15 L to 1000 L working capacity. This means gears and other components can be finished ranging in size from less than six mm in diameter to more than two meters in diameter and quantities from one to hundreds at a time.
Consumables: high density, non-abrasive ceramic media. The process utilizes high density, non-abrasive ceramic media in the vibratory finishing machine. It is considered non-abrasive since it does not contain discrete abrasive particles and alone is unable to abrade material from the hardened surface of the components being processed. The media is selected from a range of shapes and sizes best suited for maintaining the geometry of the parts. The selection of the correct media is a critical part of the process.
Process chemistry. The unique and significant feature of the process is the surface leveling/smoothing mechanism utilized to achieve the surface finish. Reactive chemistry is used in the vibratory machine in conjunction with the media. When introduced to the vibratory machine this chemistry produces a stable, soft conversion coating across the asperities (peaks and valleys) of the components. The rubbing motion across the components developed by the machine and media effectively wipes soft conversion coating off the ‘peaks’ of the parts surfaces, thereby removing a micro-layer of metal. After this continual process is complete, the conversion coating is wiped off one final time using a neutral soap to produce a mirror-like surface. This process does not affect the integrity of the parts either structurally or dimensionally and any very sensitive part areas can be effectively masked if required prior to processing with VIM.
Performance Benefits • Reduced friction • Increased part durability • Improved corrosion resistance • Reduced wear • Reduced lubrication requirements and cost • Improved oil retention • Reduced contact and bending fatigue • Improved pitting resistance • Reduced vibration and noise attenuation • Reduced applied torque requirements • Improved surface finish uniformity (part-to- part, feature-to-feature, and lot-to-lot) • High-quality, micro-finished surfaces
Reduced Friction Benefits • Increased fuel economy • Reduced contact fatigue • Increased power density • Lower operating temperature • Extended mean time between maintenance overhauls • Reduced maintenance costs • Eliminated break-in • Extended component life • Reduced metal debris • Reduced part failures • Minimized overheating
Many cooperating parts including gears and gear sets in a variety of industries remain subject to fatigue, fracture and wear. Such parts can gain substantial improvements in life and performance, from alterations to their overall surface texture. Improvements in overall smoothness, load-bearing ratio, surface profile skewness and isotropicity can, in many instances, improve life and performance and cut operational costs dramatically. Manufacturers that have not subjected their parts to an analysis to determine the potential benefits of this kind of isotropic processing may be making parts that are not all that they can be.
###

Comments