Hands-Free Finishing of AM/3DP Metal Parts with High-Speed Centrifugal Iso-Finishing
- Dave Davidson
- Jan 4, 2018
- 3 min read
Updated: Jul 18, 2020
or further information or to make arrangements for sample part processing contact: Dave Davidson | Deburring/Finishing Technologist.
Email: ddavidson@deburring-tech.group.com | See also: dryfinish.wixsite.com/iso-finish


Above: How to Video featuring HZ-12 Centrifugal Finishing machine operation
Centrifugal Isotropic Finishing has been shown to be useful in reducing the rough surfaces common to 3D printed parts. Below is an example of surface finishes that can be achieved with the method. The slides provide profilometric and areal data tabulated by Jack Clark, President of Surface Analytics. This work was performed by Jack for a study being made by SME’s Machining/Material Removal Technical Community. The slides show surface readings from a part pictured above as printed and then following centrifugal isotropic finishing. The measurements were made in both 2D and 3D. To summarize, in this test, surface roughness was reduced from 356.24µin Ra. to 12.06µin Ra.












Centrifugal Iso-Finishing Technology. Centrifugal isotropic finishing (CIF) is a high-energy finishing method, which has come into widespread acceptance in recent years. Although not nearly as universal in application as vibratory finishing, a long list of important CIF applications for precision parts have been developed in the last few years.
Similar in some respects to barrel finishing, in that a drum-type container is partially filled with media and set in motion to create a sliding action of the contents, CBF is different from other finishing methods in some significant ways. Among these are the high pressures developed in terms of media contact with parts, the unique sliding action induced by rotational and centrifugal forces, and accelerated abrading or finishing action. As is true with other high energy processes, because time cycles are much abbreviated, surface finishes can be developed in minutes, which might tie up conventional equipment for many hours.

LEFT: Centrifugal Barrel Finishing principles – high-intensity finishing is performed with barrels mounted on the periphery of a turret. The turret rotates providing the bulk of the centrifugal action, the barrels counter-rotate to provide the sliding abrasive action on parts.
The principle behind CIF is relatively straightforward. Opposing barrels or drums are positioned circumferentially on a turret. (Most systems have either two or four barrels mounted on the turret; some manufacturers favor a vertical and others a horizontal orientation for the turret.) As the turret rotates at high speed, the barrels are counter-rotated, creating very high G-forces or pressures, as well as considerable media sliding action within the drums. Pressures as high as 50 Gs have been claimed for some equipment. The more standard equipment types range in size from 1 ft3 (30 L) to 10 ft3, although much larger equipment has been built for some applications.
Media used in these types of processes tend to be a great deal smaller than the common sizes chosen for barrel and vibratory processes. The smaller media, in such a high-pressure environment, are capable of performing much more work than would be the case in lower energy equipment. They also enhance access to all areas of the part and contribute to the ability of the equipment to develop very fine finishes. In addition to the ability to produce meaningful surface finish effects rapidly, and to produce fine finishes, CBF has the ability to impart compressive stress into critical parts that require extended metal fatigue resistance. Small and more delicate parts can also be processed with confidence, as the unique sliding action of the process seems to hold parts in position relative to each other, and there is generally little difficulty experienced with part impingement. Dry process media can be used in certain types of equipment and is useful for light deburring, polishing, and producing very refined isotropic super-finishes.
Below: Centrifugal Isotropic Finishing Operations Videos
Need more information? CONTACT Dave Davidson at ddavidson@deburring-tech-group.com

INDEX TERMS: #AbrasiveMedia #Burnishing #isotropicsurfaces #Polishing #smoothing #surfacefinishing #IsotropicFinishing #Finishing #aerospacefinishing #3DPrinting #aerospace #MetalFinishing #AMPartFinishing #microfinishing #dryprocessfinishing #Deburring #AdditiveManufacturing #Finising #partfinishing #tumbling #CentrifugalBarrelFinishing #finefinishing #massfinishing #abrasive #Precisionmachinedparts #Jewelry


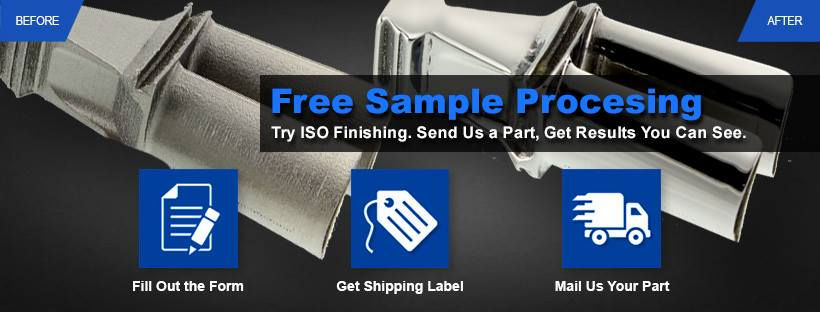
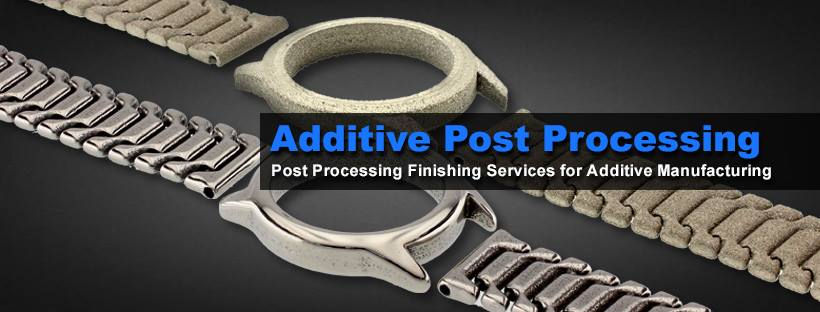

Comments